O consumo de energia de um forno de indução, como um Forno de indução IGBT , é um fator crítico tanto para a eficiência operacional como para a gestão de custos. Em média, um forno de indução de aço consome aproximadamente 625 kWh por tonelada de material processado. No entanto, este valor pode variar dependendo de fatores como projeto do forno, tipo de material, temperatura operacional e eficiência do processo. Compreender essas variáveis é essencial para otimizar o uso de energia e minimizar custos.
Pontos-chave explicados:
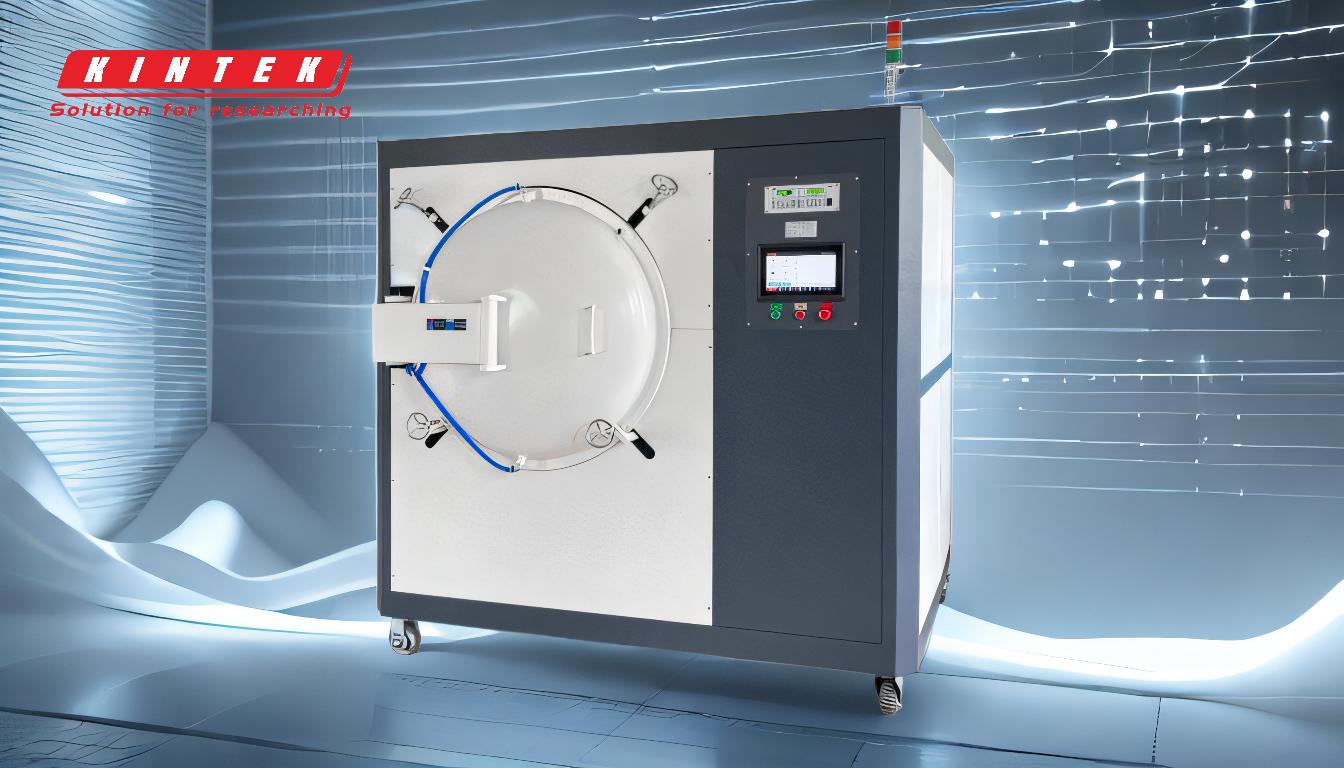
-
Consumo de energia padrão:
- O consumo médio de energia para um forno de indução de aço é 625 kWh/ton . Este é um valor de referência que fornece uma ideia geral dos requisitos de energia para a fusão do aço.
- Este valor é baseado na energia necessária para aquecer e derreter o material, contabilizando as perdas de calor e as ineficiências do forno.
-
Fatores que influenciam o consumo de energia:
- Projeto do Forno: Moderno Fornos de indução IGBT são mais eficientes em termos energéticos em comparação com modelos mais antigos. Eles usam eletrônica de potência avançada para reduzir o desperdício de energia.
- Tipo de material: Diferentes materiais têm diferentes pontos de fusão e capacidades térmicas específicas. Por exemplo, a fusão do alumínio requer menos energia do que o aço devido ao seu ponto de fusão mais baixo.
- Temperatura operacional: Temperaturas mais altas aumentam o consumo de energia. Manter um controle preciso da temperatura pode ajudar a otimizar o uso de energia.
- Eficiência de Processo: Fatores como qualidade do isolamento, design da bobina e estabilidade da fonte de alimentação afetam a eficiência geral. Isolamento deficiente ou bobinas ineficientes podem levar a maiores perdas de energia.
-
Melhorias na eficiência energética:
- Atualizando para um Forno de indução IGBT pode reduzir significativamente o consumo de energia. A tecnologia IGBT oferece melhor controle sobre a saída de energia e reduz a distorção harmônica, levando a menores perdas de energia.
- A implementação de sistemas de recuperação de energia, como a captura de calor residual, pode melhorar ainda mais a eficiência.
- A manutenção regular do forno, incluindo limpeza da bobina e verificações de isolamento, garante desempenho ideal e minimiza o desperdício de energia.
-
Implicações de custos:
- O consumo de energia impacta diretamente nos custos operacionais. A 625 kWh/ton, o custo da eletricidade torna-se uma parte significativa das despesas globais de produção.
- Ao melhorar a eficiência e reduzir o consumo de energia, as empresas podem obter poupanças substanciais de custos ao longo do tempo.
-
Considerações Ambientais:
- O menor consumo de energia não só reduz os custos, mas também minimiza a pegada ambiental da operação do forno. Isto é cada vez mais importante para as empresas que pretendem cumprir as metas de sustentabilidade.
Ao compreender estes pontos-chave, os compradores e operadores de fornos de indução podem tomar decisões informadas para otimizar o uso de energia, reduzir custos e melhorar a eficiência geral.
Tabela Resumo:
Aspecto | Detalhes |
---|---|
Consumo Padrão | 625 kWh/ton para fusão de aço |
Fatores-chave | Projeto do forno, tipo de material, temperatura operacional, eficiência do processo |
Dicas de eficiência | Atualize para fornos IGBT, implemente recuperação de energia, manutenção regular |
Impacto nos custos | Elevados custos de eletricidade de 625 kWh/ton; melhorias de eficiência economizam dinheiro |
Benefício Ambiental | O menor uso de energia reduz a pegada de carbono e apoia as metas de sustentabilidade |
Pronto para otimizar o uso de energia do seu forno de indução? Contate-nos hoje para aconselhamento especializado!