A sinterização de metais a laser (MLS) é um processo sofisticado de fabrico aditivo que utiliza um laser de alta potência para fundir partículas de pó metálico, camada a camada, para criar um objeto sólido e tridimensional.Este processo é amplamente utilizado em indústrias como a aeroespacial, automóvel e de dispositivos médicos, devido à sua capacidade de produzir geometrias complexas com elevada precisão e eficiência material.O processo envolve várias etapas fundamentais, incluindo a preparação do pó, a sinterização a laser e o pós-processamento, cada uma das quais desempenha um papel crítico na obtenção das propriedades desejadas do produto final.
Pontos-chave explicados:
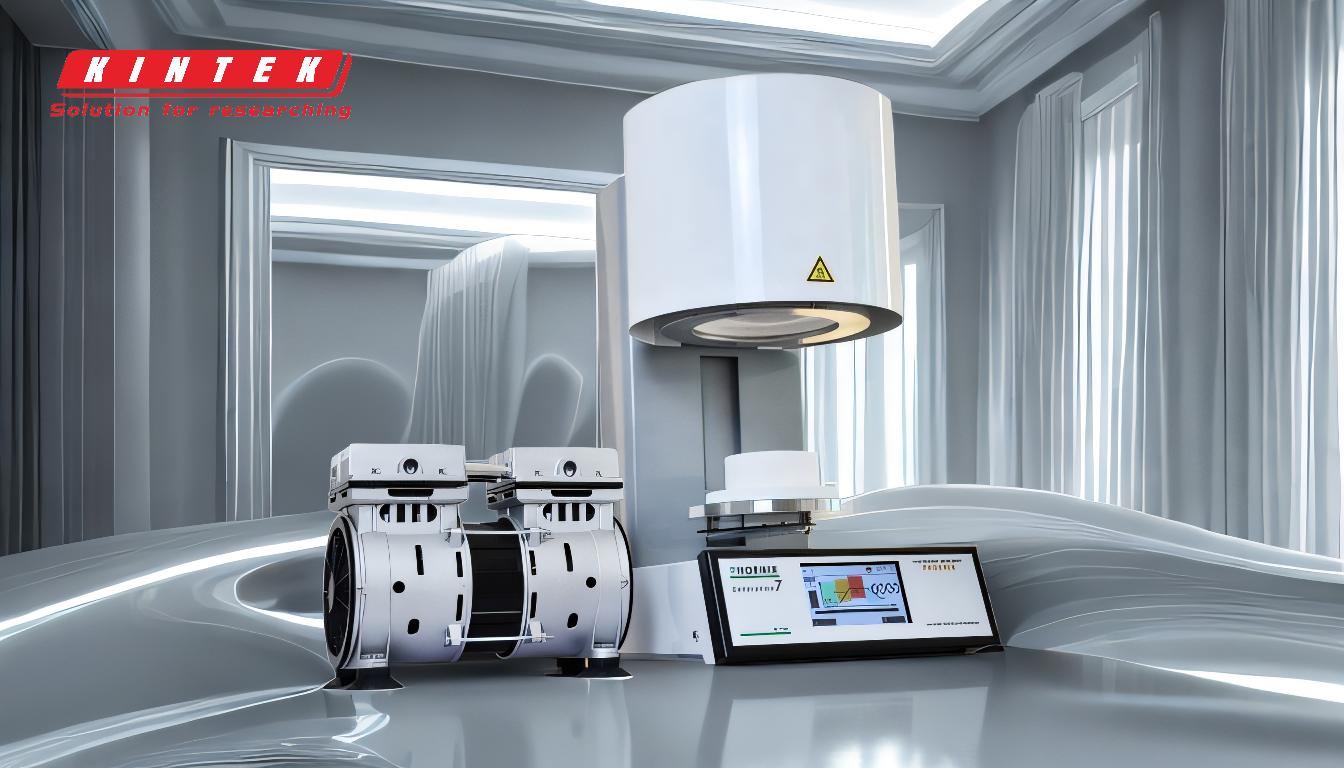
-
Preparação do pó:
- Seleção de materiais:O processo começa com a seleção dos pós metálicos adequados.Os materiais mais comuns incluem o titânio, o alumínio, o aço inoxidável e as ligas à base de níquel.A escolha do material depende das propriedades desejadas para o produto final, como a força, a durabilidade e a resistência térmica.
- Mistura de pós:Os pós metálicos são frequentemente misturados com elementos de liga e aditivos para melhorar propriedades específicas.Esta mistura assegura uma mistura homogénea que resultará num produto final uniforme.
-
Processo de sinterização a laser:
- Deposição de camadas:Uma fina camada de pó metálico é espalhada uniformemente pela plataforma de construção.A espessura desta camada é normalmente da ordem dos 20-100 microns, dependendo da resolução pretendida e da aplicação específica.
- Fusão a laser:Um feixe de laser de alta potência é dirigido para o leito de pó, fundindo seletivamente as partículas de pó de acordo com o modelo digital 3D da peça.A energia do laser é controlada com precisão para garantir que as partículas de metal se fundem sem causar distorção térmica excessiva.
- Colagem de camadas:À medida que cada camada é sinterizada, liga-se às camadas previamente sinterizadas que se encontram por baixo.Esta abordagem camada a camada permite a criação de geometrias complexas e estruturas internas que seriam difíceis ou impossíveis de alcançar com os métodos de fabrico tradicionais.
-
Atmosfera controlada:
- Ambiente de gás inerte:O processo de sinterização ocorre normalmente numa atmosfera controlada, muitas vezes cheia de gases inertes como o árgon ou o azoto.Este ambiente evita a oxidação e a contaminação do metal, garantindo a integridade e a qualidade do produto final.
- Controlo da temperatura:O forno de sinterização mantém uma temperatura precisa, geralmente um pouco abaixo do ponto de fusão do metal, para facilitar a difusão atómica e a ligação entre as partículas, sem provocar a sua fusão total.
-
Pós-Processamento:
- Remoção do excesso de pó:Após a conclusão do processo de sinterização, o excesso de pó que não foi fundido pelo laser é removido.Este pó pode frequentemente ser reciclado e reutilizado em construções subsequentes.
- Tratamento térmico:Dependendo do material e das propriedades desejadas, a peça sinterizada pode ser submetida a processos adicionais de tratamento térmico, como o recozimento ou o alívio de tensões, para melhorar as suas propriedades mecânicas.
- Acabamento da superfície:A etapa final envolve frequentemente processos de acabamento de superfície, como maquinagem, polimento ou revestimento, para obter a qualidade de superfície e a precisão dimensional desejadas.
-
Vantagens e aplicações:
- Geometrias complexas:A MLS permite a criação de peças com estruturas internas complexas e detalhes intrincados que não são viáveis com os métodos de fabrico tradicionais.
- Eficiência do material:O processo é altamente eficiente em termos de material, uma vez que utiliza apenas a quantidade de pó necessária para construir a peça, minimizando o desperdício.
- Personalização e prototipagem:A MLS é particularmente valiosa para a prototipagem rápida e o fabrico personalizado, permitindo uma rápida iteração e personalização dos desenhos.
- Aplicações do sector:A tecnologia é amplamente utilizada em indústrias que exigem componentes de alto desempenho, como a aeroespacial para estruturas leves, a automóvel para peças personalizadas e a de dispositivos médicos para implantes específicos para cada paciente.
Em resumo, a sinterização de metais a laser é um processo de fabrico versátil e preciso que aproveita o poder dos lasers para fundir pós metálicos em peças complexas e de elevado desempenho.O processo envolve uma preparação cuidadosa dos materiais, um controlo preciso do ambiente de sinterização e um pós-processamento minucioso para obter as propriedades e o acabamento desejados.Esta tecnologia continua a revolucionar o fabrico, permitindo a produção de peças que anteriormente eram impossíveis de criar com os métodos tradicionais.
Tabela de resumo:
Etapas principais | Detalhes |
---|---|
Preparação do pó | - Seleção de material (por exemplo, titânio, alumínio, aço inoxidável). |
- Mistura de pós para obter propriedades uniformes. | |
Sinterização a laser | - Deposição de camadas (20-100 microns). |
- Fusão a laser para uma fusão precisa.
- Colagem de camadas para geometrias complexas.| | Atmosfera Controlada
- | Ambiente de gás inerte (árgon ou azoto). Controlo preciso da temperatura.| |
- Pós-processamento
- | Remoção do excesso de pó. Tratamento térmico (recozimento, alívio de tensões). Acabamento de superfícies (maquinagem, polimento).|
- |
- Vantagens | Geometrias complexas. Eficiência dos materiais.
Prototipagem rápida e personalização.| | Aplicações