Introdução às atmosferas dos fornos
As atmosferas dos fornos desempenham um papel essencial no processo de tratamento térmico dos materiais. A atmosfera no interior de um forno pode afetar significativamente as propriedades do produto final, tais como a resistência e a durabilidade. Uma atmosfera é um gás ou uma mistura de gases que envolve o material a ser tratado num forno. As atmosferas de forno mais utilizadas incluem o ar, o azoto, o hidrogénio e o árgon. Compreender as propriedades de cada atmosfera e os seus efeitos no material é crucial para produzir produtos de alta qualidade. A utilização de atmosferas inertes, como o azoto e o árgon, é importante para evitar reacções indesejadas e a oxidação durante o processo de tratamento térmico.
Índice
- Introdução às atmosferas dos fornos
- O que é uma atmosfera inerte?
- Por que é importante usar atmosferas inertes?
- Gases comuns em atmosferas de fornos
- Processos de tratamento térmico que requerem atmosferas inertes
- Como medir a atmosfera do forno
- Ferramentas para medição e amostragem
- Conclusão sobre a importância das atmosferas inertes
O que é uma Atmosfera Inerte?
No trabalho de laboratório, é essencial criar um ambiente controlado para determinadas reacções ou processos. Um desses ambientes é uma atmosfera inerte, que se caracteriza pela ausência de gases reactivos que possam interferir com o resultado desejado. Gases inertes como o azoto, o árgon e o hélio são normalmente utilizados para criar este ambiente, o que pode ser conseguido através de técnicas como a purga, a cobertura ou a utilização de caixas de luvas.
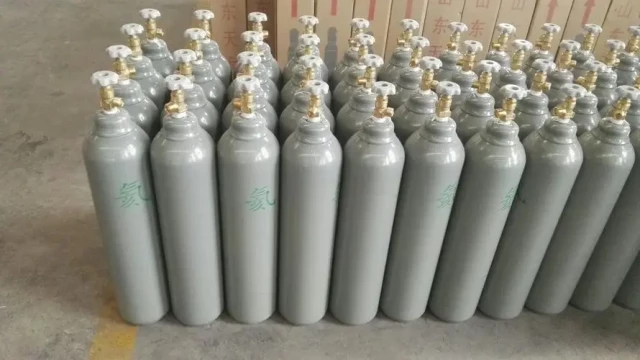
Definição de atmosfera inerte
Uma atmosfera inerte é um ambiente controlado utilizado para várias aplicações laboratoriais e industriais, em que a atmosfera está isenta de gases reactivos que podem causar reacções químicas indesejadas. Os gases inertes, como o azoto, o árgon e o hélio, são normalmente utilizados para criar um ambiente deste tipo. Estes gases são considerados inertes porque não reagem quimicamente com outras substâncias, o que os torna ideais para criar um ambiente controlado.
Criação de uma atmosfera inerte
Existem várias maneiras de criar uma atmosfera inerte, incluindo purga, cobertura e o uso de caixas de luvas. A purga envolve a remoção de todo o ar de um recipiente ou sistema e a sua substituição por um gás inerte. A cobertura envolve o enchimento de um recipiente com um gás inerte para criar uma camada de gás que impede a entrada de ar ou outros gases reactivos. As caixas de luvas são espaços de trabalho fechados que utilizam uma atmosfera de gás inerte para criar um ambiente controlado.
Usos de atmosferas inertes
As atmosferas inertes são utilizadas em várias aplicações laboratoriais e industriais, incluindo processos de tratamento térmico, como sinterização, recozimento brilhante e carbonitretação. Estes processos requerem atmosferas altamente controladas para produzir peças de qualidade para indústrias como a aeroespacial, automóvel e petroquímica. As atmosferas inertes são também utilizadas na produção de semicondutores, onde a pureza é crítica.
Gases inertes comuns
Os gases inertes mais utilizados para criar uma atmosfera inerte são o nitrogénio, o árgon e o hélio. O nitrogénio é o gás inerte mais acessível e amplamente utilizado e é frequentemente utilizado em aplicações em que é necessário remover a humidade e o oxigénio. O árgon é um gás mais denso e é normalmente utilizado em aplicações que requerem uma barreira de gás inerte mais substancial. O hélio é o gás inerte mais leve e é utilizado em aplicações em que é necessária uma baixa densidade e uma elevada condutividade térmica.
Em conclusão, uma atmosfera inerte é um ambiente controlado no qual a atmosfera está livre de gases reactivos que podem interferir com o resultado desejado. Este ambiente é crucial em aplicações laboratoriais e industriais em que a precisão e o controlo são essenciais. A utilização de gases de atmosfera inerte, como o azoto, o árgon e o hélio, é fundamental para criar este ambiente e garantir a qualidade, fiabilidade e reprodutibilidade das experiências laboratoriais e dos processos industriais.
Porque é que é importante utilizar atmosferas inertes?
Os gases de atmosfera inerte são essenciais para muitos processos de tratamento térmico devido à sua capacidade de criar um ambiente controlado que evita reacções químicas indesejáveis, oxidação e contaminação do produto. Nesta secção, discutiremos as razões pelas quais é importante utilizar atmosferas inertes em atmosferas de fornos.
Prevenção de reacções químicas indesejáveis
Quando se trabalha com tratamento térmico, sinterização ou brasagem, a presença de determinados gases, como o oxigénio ou o vapor de água, pode causar oxidação ou outras reacções químicas indesejadas. Os gases inertes, como o azoto, o árgon e o hélio, são utilizados para deslocar o oxigénio e o vapor de água da câmara do forno, criando uma atmosfera desprovida de gases reactivos. Isto assegura que o processo é controlado e que o resultado desejado é alcançado.
Melhorar a qualidade do produto
A utilização de gases inertes pode aumentar a eficiência do processo, reduzindo a quantidade de energia necessária para atingir a temperatura desejada e acelerando o processo de arrefecimento. Além disso, a atmosfera inerte ajuda a evitar a oxidação e a contaminação do produto, resultando num resultado final de maior qualidade. Isto é especialmente importante para indústrias como a aeroespacial, automóvel ou petroquímica, onde são fabricadas peças de missão crítica.
Obtenção de precisão e repetibilidade
Para os processos de tratamento térmico que requerem uma atmosfera altamente controlada, como o recozimento brilhante, a sinterização e a carbonitretação, é essencial obter precisão e repetibilidade. Os fornos utilizados nestes processos devem suportar uma atmosfera controlada de modo a obter resultados bem sucedidos, de alta precisão e repetíveis para estas peças. São utilizadas atmosferas inertes para garantir que o processo é controlado e que o resultado desejado é alcançado.
Reduzir os danos no forno e as lesões dos trabalhadores
Uma atmosfera incorretamente controlada pode conduzir a um forno danificado ou, pior ainda, a ferimentos nos empregados. Os gases inertes são utilizados para evitar reacções químicas na superfície de uma peça que comprometam a sua qualidade e desempenho, levando à rejeição de peças. Isto, por sua vez, leva a perdas financeiras, perda de tempo e repercussões potencialmente perigosas para aqueles que utilizam a peça se os problemas não forem detectados.
Em conclusão, a utilização de gases de atmosfera inerte em atmosferas de fornos é essencial para garantir um processo controlado e eficiente, evitar reacções químicas indesejáveis e produzir produtos de alta qualidade. É importante compreender porque é que os utilizamos e qual é a melhor atmosfera para uma aplicação específica, de modo a obter resultados bem sucedidos, de alta precisão e repetíveis.
Gases comuns em atmosferas de fornos
Os gases de atmosfera inerte desempenham um papel crucial nas atmosferas dos fornos para evitar reacções químicas indesejadas ou a oxidação de materiais durante o processamento a alta temperatura. Os gases mais comuns utilizados em aplicações de atmosfera inerte incluem o azoto, o árgon e o hélio.
Azoto
O azoto é o gás mais utilizado devido à sua disponibilidade e acessibilidade. É um gás não reativo que proporciona uma atmosfera protetora. O seu conteúdo de carbono, oxigénio e azoto não reage com o aço, tornando-o um gás ideal para atmosferas de fornos. O nitrogénio é utilizado para evitar a oxidação em aplicações de tratamento térmico e é eficaz na deslocação do oxigénio da atmosfera.
Árgon
O árgon é frequentemente utilizado em processos que requerem um nível de pureza mais elevado ou um período prolongado de processamento a alta temperatura. O árgon é um gás "nobre" completamente inerte e não reage com nenhum material com o qual entra em contacto. Desloca o oxigénio, o que o torna um gás ideal para aplicações em que a oxidação é indesejável. O árgon é mais caro do que o azoto, mas tem a vantagem de poder ser utilizado a temperaturas superiores a 1800°C sem qualquer risco de reação.
Hélio
O hélio é utilizado quando é necessária uma baixa solubilidade, uma vez que é o gás menos reativo. A sua baixa densidade e elevada condutividade térmica fazem dele um gás ideal para determinadas aplicações. O hélio é frequentemente utilizado em cromatografia gasosa, deteção de fugas e aplicações de refrigeração.
Em resumo, estes gases criam um ambiente sem oxigénio que protege os materiais a serem processados e garante resultados consistentes e precisos. Sem a utilização de gases de atmosfera inerte, podem ocorrer reacções indesejadas, conduzindo a defeitos do produto, diminuição da qualidade do produto e até danos no equipamento. A escolha do gás depende dos requisitos específicos do processo de tratamento térmico, e o tipo de atmosfera necessária determinará o tipo de forno necessário para o efetuar.
Processos de tratamento térmico que requerem atmosferas inertes
Os processos de tratamento térmico que requerem temperaturas elevadas e atmosferas controladas dependem frequentemente de gases de atmosfera inerte, como o azoto, o árgon e o hélio. Estes gases desempenham um papel crucial na criação de um ambiente isento de oxigénio e de outros gases reactivos que poderiam causar reacções químicas ou oxidação dos materiais a tratar.
Porque é que as atmosferas inertes são essenciais
A ausência de oxigénio e de outros gases reactivos na atmosfera do forno ajuda a manter a pureza dos materiais e a evitar contaminações ou reacções indesejadas. As atmosferas inertes são essenciais para uma vasta gama de aplicações, incluindo o tratamento térmico de metais, o recozimento de vidro e a sinterização de cerâmica. A utilização de gases de atmosfera inerte em atmosferas de fornos é fundamental para garantir a qualidade e a consistência dos produtos finais. Quaisquer desvios na atmosfera do forno podem ter um impacto significativo nas propriedades do produto final, tornando essencial manter um controlo rigoroso sobre o ambiente do forno.
Gases inertes utilizados nos processos de tratamento térmico
O árgon, o hélio e o azoto são os gases inertes mais utilizados nos processos de tratamento térmico. A escolha do gás inerte depende do tipo de material que está a ser tratado e dos requisitos específicos do processo de tratamento térmico. Em geral, o árgon e o hélio são mais inertes do que o hidrogénio. Uma atmosfera de azoto puro proporciona uma cobertura da peça a ser tratada termicamente e pode ser utilizada para purgar a atmosfera existente ou ser utilizada como gás de transporte para atmosferas controladas por carbono.
Processos de Tratamento Térmico que Utilizam Atmosferas Inertes
As atmosferas inertes são utilizadas numa vasta gama de processos de tratamento térmico, incluindo:
- Recozimento (metais não ferrosos, ligas de aço e descarbonetação)
- Endurecimento neutro
- Têmpera
- Nitretação (ligas de aço, aços inoxidáveis e aços de nitretação)
- Sinterização
- Brasagem (o azoto actua como gás de arrastamento)
- Processos de vácuo
Combinações de gases inertes
Em alguns casos, pode ser utilizada uma combinação de gases inertes nos processos de tratamento térmico. Por exemplo, uma atmosfera de hidrogénio + azoto funciona bem para recozimento brilhante; recozimento de aço inoxidável, ligas de aço e não ferro; endurecimento neutro; e sinterização. A utilização de uma atmosfera de hidrogénio + árgon funciona com recozimento brilhante; recozimento de aço inoxidável, aço ligado e não-ferro; e sinterização.
Conclusão
Em resumo, os gases de atmosfera inerte desempenham um papel crítico nos processos de tratamento térmico que requerem temperaturas elevadas e atmosferas controladas. A utilização destes gases ajuda a manter a pureza dos materiais e a evitar contaminações ou reacções indesejadas. A escolha do gás inerte depende do processo específico de tratamento térmico e do tipo de material que está a ser tratado. As atmosferas inertes são essenciais para garantir produtos finais de alta qualidade na indústria de tratamento térmico.
Como medir a atmosfera do forno
A medição da atmosfera do forno é um passo crucial para garantir que os gases da atmosfera inerte estão a funcionar corretamente e que o processo está a decorrer sem problemas. A seguir estão os passos para medir a atmosfera do forno.
Passo 1: Determinar o tipo de analisador
Existem várias formas de medir a atmosfera do forno, incluindo analisadores de condutividade térmica, de infravermelhos e de zircónio. Cada método tem os seus pontos fortes e fracos, e a escolha do analisador adequado depende da aplicação específica e do tipo de gases utilizados.
Passo 2: Calibrar o analisador
Antes de utilizar o analisador, é importante calibrá-lo para garantir que está a efetuar uma leitura precisa. A calibração implica expor o analisador a uma mistura de gases conhecida e ajustá-lo até ler os valores correctos.
Passo 3: Instalar o analisador
Instalar o analisador no forno ou no ponto de amostragem no fluxo de gases de combustão, consoante o tipo de analisador.
Passo 4: Efetuar a medição
Uma vez instalado o analisador, efectue a medição. A frequência das medições dependerá da aplicação específica, mas é importante monitorizar regularmente a atmosfera do forno para manter a sua integridade e garantir uma qualidade consistente do produto.
Passo 5: Interpretar os resultados
Interpretar os resultados obtidos com o analisador e tomar medidas correctivas, se necessário. Se os resultados indicarem que a atmosfera do forno não está a funcionar corretamente, ajuste os gases da atmosfera inerte para manter o equilíbrio correto.
Ao seguir estes passos, os fabricantes podem otimizar os seus processos e produzir produtos de alta qualidade com precisão e eficiência.
Ferramentas para medição e amostragem
Os gases de atmosfera inerte são componentes cruciais nas atmosferas dos fornos, sendo essencial garantir a sua segurança e eficácia durante operações a alta temperatura. A medição e amostragem destes gases é, portanto, uma tarefa crítica em ambientes laboratoriais.
Analisadores de gases
Os analisadores de gás são ferramentas sofisticadas que efectuam análises precisas de amostras de gás, detectando impurezas e alterações na concentração. São utilizados para medir uma vasta gama de parâmetros, incluindo oxigénio, dióxido de carbono e vapor de água. Os analisadores de gás são altamente sensíveis e podem detetar até as mais pequenas alterações na composição do gás, tornando-os ideais para monitorizar gases de atmosfera inerte.
Cromatógrafos de gás
Os cromatógrafos de gás são ferramentas poderosas que podem separar e analisar componentes individuais de uma amostra de gás. São capazes de detetar quantidades vestigiais de impurezas e podem medir com precisão as concentrações de vários gases. Os cromatógrafos de gás são amplamente utilizados em laboratórios e podem ser utilizados para analisar gases de atmosfera inerte para fins de segurança e controlo de qualidade.
Equipamento de amostragem
O equipamento de amostragem adequado é essencial para medir e monitorizar gases de atmosfera inerte. Os sacos de amostragem de gás, por exemplo, são utilizados para recolher amostras de gás para análise, enquanto as seringas de gás são utilizadas para extrair amostras diretamente de um fluxo de gás. Outros tipos de equipamento de amostragem incluem detectores de gás, que podem detetar a presença de gases específicos, e sensores de gás, que podem medir concentrações de gás em tempo real.
Equipamento de calibração
O equipamento de calibração é essencial para garantir a exatidão dos analisadores de gases e de outras ferramentas de medição de gases. Os gases de calibração, como o azoto e o oxigénio, são utilizados para calibrar os analisadores de gases e garantir leituras precisas. O equipamento de calibração também é usado para verificar a precisão de sensores de gás e outras ferramentas de medição de gás.
Benefícios da medição e amostragem de gases de atmosfera inerte
A medição e amostragem de gases de atmosfera inerte é importante para manter a segurança e a qualidade dos processos de tratamento térmico. A amostragem e análise regulares de gases de atmosfera inerte podem ajudar a identificar potenciais problemas nas operações do forno e evitar danos dispendiosos no equipamento. Pode também ajudar os profissionais e engenheiros de laboratório a otimizar os seus processos de tratamento térmico, resultando numa melhoria da qualidade do produto e na redução dos custos de produção.
Em conclusão, a medição e amostragem de gases de atmosfera inerte é uma tarefa crítica em ambientes laboratoriais. Analisadores de gás, cromatógrafos de gás, equipamento de amostragem, equipamento de calibração e outras ferramentas são todos componentes essenciais deste processo. Medindo e monitorizando regularmente os gases da atmosfera inerte, os profissionais de laboratório podem garantir a segurança e a eficácia dos processos de tratamento térmico e manter a qualidade dos seus produtos.
Conclusão sobre a Importância das Atmosferas Inertes
As atmosferas inertes desempenham um papel crucial no processo de tratamento térmico de materiais. Ajudam a evitar a oxidação, a descarbonetação ou outras reacções indesejáveis que podem ocorrer na presença de oxigénio ou de outros gases reactivos. Ao utilizar gases inertes, como o azoto ou o árgon, nas atmosferas dos fornos, os materiais podem ser aquecidos e arrefecidos num ambiente controlado, garantindo resultados consistentes e fiáveis. É importante medir e monitorizar a atmosfera no forno para garantir que as condições desejadas são mantidas. A utilização correcta de atmosferas inertes pode levar a uma melhor qualidade do produto, a taxas de refugo reduzidas e a uma maior produtividade na indústria de tratamento térmico.
CONTACTE-NOS PARA UMA CONSULTA GRATUITA
Os produtos e serviços da KINTEK LAB SOLUTION foram reconhecidos por clientes de todo o mundo. A nossa equipa terá todo o prazer em ajudar com qualquer questão que possa ter. Contacte-nos para uma consulta gratuita e fale com um especialista de produto para encontrar a solução mais adequada para as suas necessidades de aplicação!