Princípios básicos do processo de revestimento PVD
Evaporação
Num ambiente de vácuo, o material sólido, conhecido como o alvo, sofre uma transformação para o seu estado gasoso através de vários métodos, principalmente envolvendo aquecimento. Este processo, conhecido como evaporação, é fundamental para o processo de revestimento por Deposição Física de Vapor (PVD). São utilizadas várias técnicas para conseguir esta transformação:
-
Evaporação térmica: Este método envolve o aquecimento do material alvo até à sua temperatura de evaporação, utilizando uma resistência eléctrica ou outros elementos de aquecimento. Quando o material atinge o seu ponto de vaporização, transforma-se num gás, que depois se difunde e condensa no substrato para formar uma película fina.
-
Evaporação por feixe de electrões: Aqui, um feixe de electrões de alta energia é dirigido para o material alvo, provocando a sua evaporação. Esta técnica é particularmente útil para materiais com pontos de fusão elevados, uma vez que o efeito de aquecimento localizado permite um controlo preciso do processo de evaporação.
-
Evaporação a laser: Utilizando impulsos de laser de alta energia, este método vaporiza o material alvo. A evaporação a laser é vantajosa para a preparação de materiais complexos de película fina, uma vez que oferece uma elevada precisão e pode ser utilizada para evaporar materiais que são difíceis de manusear com os métodos tradicionais.
Cada um destes métodos tem as suas vantagens únicas e é escolhido com base nos requisitos específicos do processo de revestimento, tais como o tipo de material que está a ser utilizado e as propriedades desejadas da película resultante.
Transporte
O material gasoso, uma vez transformado num estado de vapor, sofre uma difusão dentro da câmara de vácuo. Esta difusão é uma fase crítica no processo PVD, uma vez que influencia diretamente a uniformidade e a qualidade da subsequente deposição da película. Vários factores-chave têm um impacto significativo nesta fase de transporte:
-
Pressão do gás: A pressão dentro da câmara de vácuo desempenha um papel fundamental. Normalmente, as pressões mais baixas aumentam a eficiência da difusão, assegurando que o material gasoso se espalha mais uniformemente pelo substrato. Por outro lado, pressões mais elevadas podem levar a colisões entre as moléculas de gás, reduzindo potencialmente a taxa de difusão global e afectando a uniformidade da película.
-
Temperatura: A temperatura no ambiente de vácuo é outra variável crucial. As temperaturas mais elevadas podem acelerar o processo de difusão, mas devem ser cuidadosamente controladas para evitar danos térmicos no substrato ou a formação de depósitos não uniformes. O equilíbrio da temperatura com outros parâmetros do processo é essencial para uma difusão óptima.
-
Posição do substrato: A disposição espacial do substrato em relação à fonte do material gasoso também é significativa. O alinhamento correto assegura que o material gasoso atinge todas as áreas do substrato de forma uniforme, evitando a sobre-deposição ou sub-deposição localizada. Técnicas como a rotação ou inclinação do substrato podem ajudar a obter uma cobertura mais uniforme.
Em suma, o transporte de material gasoso em vácuo é um processo complexo que requer um controlo meticuloso da pressão do gás, da temperatura e do posicionamento do substrato para garantir a deposição bem sucedida de uma película de alta qualidade.
Deposição
Durante a fase de deposição, o material gasoso, que foi transportado para o substrato, começa a arrefecer e a condensar. Este processo de arrefecimento é crucial, uma vez que transforma o gás numa película fina sólida, aderente à superfície do substrato. O processo de deposição não é apenas uma mudança física, mas também uma mudança transformadora, alterando significativamente as propriedades do substrato com base na aplicação específica.
O tipo de gás utilizado durante a deposição desempenha um papel fundamental na determinação da estrutura e das caraterísticas finais da película. Por exemplo, os gases inertes, como o árgon e o hélio, são frequentemente utilizados para manter a pureza da película, assegurando que não ocorrem reacções químicas indesejadas. Por outro lado, os gases reactivos, como o oxigénio, o azoto e o flúor, são introduzidos para criar compostos específicos, como óxidos, nitretos e fluoretos, melhorando a funcionalidade da película para aplicações específicas.
Além disso, a pressão do gás na câmara de deposição é um parâmetro crítico que influencia tanto a taxa de deposição como a qualidade da película. Normalmente, pressões de gás mais baixas resultam em películas mais densas e homogéneas, o que é desejável para muitas aplicações. Inversamente, pressões de gás mais elevadas podem conduzir a películas mais rugosas, o que pode ser benéfico em determinados contextos, como quando é necessária uma maior área de superfície para uma melhor adesão ou reatividade.
Em resumo, o processo de deposição é uma interação sofisticada de arrefecimento, tipo de gás e pressão, sendo cada fator meticulosamente controlado para obter as propriedades desejadas da película. Esta orquestração cuidadosa garante que a película fina resultante cumpre as normas exigentes requeridas por várias indústrias, desde a eletrónica à ótica e muito mais.
Principais tipos de processo PVD
Deposição por evaporação
A deposição por evaporação é uma técnica sofisticada utilizada para produzir películas finas através do aquecimento de materiais alvo até ao seu ponto de vaporização. Este processo é particularmente eficaz para metais e certas ligas, transformando-os do estado sólido para o estado gasoso através da energia térmica. Os átomos vaporizados condensam-se então no substrato, formando uma película fina uniforme e conformada. Este método é normalmente conduzido num ambiente de alto vácuo para minimizar as colisões e a contaminação, garantindo a pureza e a integridade da película depositada.
Uma das principais vantagens da deposição por evaporação é a sua capacidade de criar películas de alta qualidade com excelente uniformidade e conformação. Esta técnica é versátil, capaz de depositar uma vasta gama de materiais, incluindo metais, cerâmicas e semicondutores. No entanto, o processo exige uma configuração de alto vácuo e é altamente sensível a factores ambientais, o que pode restringir a sua aplicabilidade em determinados cenários.
Deposição por Sputtering
A deposição por pulverização catódica é uma técnica sofisticada de deposição física de vapor (PVD) que envolve o bombardeamento de um material alvo com partículas de alta energia, normalmente iões de um plasma. Este bombardeamento faz com que o material alvo ejecte átomos ou moléculas, que depois viajam através do vácuo e se condensam num substrato, formando uma película fina. O processo é versátil, aplicável a um amplo espetro de materiais, incluindo metais, óxidos e nitretos.
Na deposição por pulverização catódica, o material alvo é exposto a um plasma, frequentemente composto por iões de árgon e electrões. Estas partículas energéticas "derrubam" átomos do alvo, criando uma nuvem de átomos de origem. Esta nuvem condensa-se então no substrato, onde forma uma película fina. A escolha do material alvo e as condições do plasma influenciam significativamente as caraterísticas da película depositada.
Um aspeto notável da deposição por pulverização catódica é o fenómeno de resputtering, em que o material já depositado pode ser reemitido por um bombardeamento subsequente de iões ou átomos. Este fenómeno pode afetar a uniformidade e a espessura da película, exigindo um controlo cuidadoso dos parâmetros de deposição para obter os resultados desejados.
A deposição por pulverização catódica é amplamente utilizada em várias indústrias devido à sua capacidade de produzir filmes densos e de alta qualidade com excelente adesão ao substrato. É particularmente favorecida pela sua aplicabilidade a uma vasta gama de materiais, tornando-a uma ferramenta versátil no fabrico de películas finas avançadas para componentes electrónicos, ópticos e mecânicos.
Deposição por Laser Pulsado (PLD)
A deposição por laser pulsado (PLD) é um processo de evaporação sofisticado que emprega impulsos de laser de alta energia para vaporizar um material alvo dentro de uma câmara de vácuo. Este método é particularmente adequado para a preparação de materiais de película fina complexos, o que o torna uma escolha preferida em várias aplicações científicas e industriais.
O processo PLD começa com o feixe de laser a incidir sobre o material, provocando a sua vaporização e a formação de uma pluma de plasma. Este plasma deposita-se então num substrato, onde se condensa para formar uma película fina. A complexidade deste processo, que envolve a evaporação, a ablação, a formação de plasma e a esfoliação, exige uma otimização cuidadosa. Apesar do aumento do tempo e do esforço necessários para gerir as numerosas variáveis envolvidas, a PLD oferece várias vantagens.
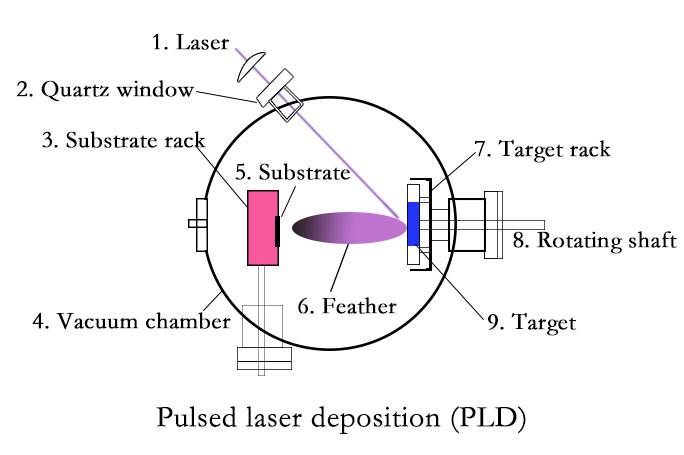
Uma das principais vantagens do PLD são as suas elevadas taxas de deposição, que simplificam significativamente o processo em comparação com outros métodos. Além disso, a PLD elimina a necessidade de filamentos, simplificando a manutenção e reduzindo potenciais fontes de contaminação. Isto torna a PLD particularmente adequada para aplicações que exigem elevada precisão e pureza, tais como nas indústrias eletrónica e ótica.
Em resumo, embora a complexidade do PLD exija um controlo meticuloso, a sua capacidade de produzir películas finas complexas e de alta qualidade de forma eficiente e com uma manutenção mínima torna-o uma ferramenta valiosa no domínio dos processos de revestimento PVD.
Deposição química de vapor (CVD)
Embora a deposição química de vapor (CVD) seja fundamentalmente diferente da deposição física de vapor (PVD), há casos em que estas duas técnicas são combinadas para obter propriedades de película superiores. O CVD, um método de deposição em vácuo, é conhecido por produzir materiais sólidos de alta qualidade e elevado desempenho, particularmente películas finas utilizadas na indústria de semicondutores. O processo envolve a exposição de uma bolacha (substrato) a um ou mais precursores voláteis, que reagem e/ou se decompõem na superfície do substrato para formar o depósito desejado. Este método é versátil, capaz de depositar materiais em várias formas, incluindo estruturas monocristalinas, policristalinas, amorfas e epitaxiais.
Em contraste com a PVD, que se baseia em processos físicos como a evaporação ou a pulverização catódica, a CVD utiliza reacções químicas para depositar materiais. Esta abordagem química permite um maior controlo sobre a composição e as propriedades da película depositada. No entanto, em determinadas aplicações, a utilização complementar de CVD e PVD pode produzir películas com caraterísticas melhoradas, tais como uma melhor aderência, melhores propriedades mecânicas ou revestimentos mais uniformes. Por exemplo, as camadas preliminares de PVD podem ser utilizadas para criar uma superfície mais recetiva para as camadas subsequentes de CVD, optimizando assim a qualidade global da película.
A integração da CVD com a PVD é particularmente benéfica em processos complexos de microfabricação, em que a combinação de técnicas de deposição química e física pode resolver desafios específicos que nenhum dos métodos poderia resolver isoladamente. Esta abordagem híbrida não só alarga a gama de materiais que podem ser depositados, como também melhora a funcionalidade e o desempenho do produto final.
Aplicação de gases no processo PVD
Gases inertes
Os gases inertes, como o árgon (Ar) e o hélio (He), desempenham um papel crucial nos processos de deposição por pulverização catódica, actuando como gases de transporte. Estes gases são preferidos pela sua capacidade de aumentar a eficiência de pulverização do material alvo sem causar quaisquer reacções químicas. Esta natureza não reactiva garante a manutenção da pureza da película depositada, o que é essencial para obter revestimentos de alta qualidade.
A utilização de gases inertes não se limita à deposição por pulverização catódica; são também utilizados para evitar reacções químicas indesejadas que podem degradar uma amostra. Geralmente, estas reacções indesejáveis incluem a oxidação e a hidrólise, que são normalmente iniciadas pela presença de oxigénio e humidade no ar. Ao substituir estes elementos reactivos por gases inertes, a integridade da amostra é preservada.
O árgon, em particular, é o gás inerte mais utilizado em várias aplicações devido à sua elevada abundância natural e custo relativamente baixo. Representa cerca de 1% da atmosfera da Terra, o que o torna facilmente disponível para utilização industrial. Embora o árgon seja o mais popular, outros gases nobres como o hélio e o néon também podem ser utilizados, dependendo dos requisitos específicos do processo.
Vale a pena notar que o termo "gás inerte" depende do contexto. Embora os gases nobres sejam frequentemente considerados inertes, podem reagir em determinadas condições, embora com uma baixa probabilidade. Esta caraterística deve-se em grande parte às camadas de valência completas destes gases, que geralmente os tornam não reactivos. No entanto, esta não é uma regra absoluta, uma vez que mesmo os gases nobres podem formar compostos em condições específicas.
Ao especificar a pureza dos gases inertes, é comum indicar o nível de contaminação em partes por milhão (ppm). Por exemplo, um nível de contaminação de 100 ppm significa que, em cada milhão de moléculas do gás inerte, 100 são moléculas estranhas. Esta medida é crucial para garantir a eficácia do gás inerte na manutenção da pureza da película depositada.
Em resumo, os gases inertes, como o árgon e o hélio, são indispensáveis na deposição por pulverização catódica e noutros processos em que a manutenção da pureza e da integridade dos materiais é fundamental. A sua natureza não reactiva e disponibilidade tornam-nos ideais para uma vasta gama de aplicações industriais.
Gases reactivos
Os gases reactivos desempenham um papel crucial na preparação de várias películas finas em processos PVD. Estes gases, que incluem oxigénio (O₂), azoto (N₂) e flúor (F₂), são essenciais para a criação de películas de óxido, nitreto e fluoreto, respetivamente. A introdução destes gases reactivos é muitas vezes necessária para atingir a composição química e as propriedades desejadas nas películas depositadas.
Por exemplo, ao preparar películas finas de óxido de alumínio (Al₂O₃), o oxigénio é normalmente introduzido como gás de reação. Isto assegura que os átomos de alumínio na fase de vapor reagem com o oxigénio para formar uma película de Al₂O₃ estável e uniforme. A utilização de gases reactivos não se limita ao óxido de alumínio; estende-se também a outros materiais, como o nitreto de silício (Si₃N₄) e o dióxido de titânio (TiO₂), em que são utilizados, respetivamente, azoto e oxigénio.
A escolha do gás reativo e a sua concentração podem influenciar significativamente as propriedades da película, incluindo a sua densidade, dureza e estabilidade química. Por exemplo, concentrações mais elevadas de oxigénio podem conduzir a películas mais porosas e menos densas, enquanto concentrações mais baixas podem resultar numa oxidação incompleta, afectando a qualidade geral da película.
Em resumo, a utilização criteriosa de gases reactivos é um aspeto crítico dos processos de PVD, permitindo a criação de películas finas de elevado desempenho com propriedades personalizadas para várias aplicações.
Gases orgânicos
Em determinadas aplicações especializadas, os gases orgânicos, como o etileno e o propileno, desempenham um papel crucial na preparação de películas de polímeros e compósitos. Estes gases são frequentemente introduzidos no processo de PVD para facilitar a formação de estruturas de película específicas que não podem ser obtidas apenas com gases inertes ou reactivos.
A utilização de gases orgânicos nos processos de PVD é particularmente benéfica para a criação de películas de polímeros que requerem funcionalidades químicas específicas. Por exemplo, o etileno pode ser utilizado para formar películas de polietileno, que são conhecidas pelas suas excelentes propriedades mecânicas e resistência química. Do mesmo modo, o propileno pode ser utilizado para criar películas de polipropileno, que são altamente resistentes ao calor e aos produtos químicos.
Além disso, os gases orgânicos podem ser combinados com outros gases para criar películas compostas que exibem uma mistura de propriedades de componentes orgânicos e inorgânicos. Esta abordagem híbrida permite a personalização das propriedades da película, possibilitando a adaptação das películas a aplicações específicas em indústrias como a eletrónica, a ótica e a engenharia mecânica.
Em resumo, a incorporação de gases orgânicos nos processos de PVD abre novas possibilidades para a criação de películas e compósitos de polímeros avançados, permitindo o desenvolvimento de materiais com propriedades únicas e melhoradas.
Ajuste da pressão do gás
A pressão do gás no processo PVD desempenha um papel fundamental na determinação da taxa de deposição e da qualidade da película. Este parâmetro influencia diretamente o comportamento do material gasoso à medida que este se desloca do alvo para o substrato.
Com pressões de gás mais baixas, o material gasoso tende a difundir-se mais uniformemente, levando a uma melhor densificação e homogeneidade da película. Isto deve-se ao facto de a pressão reduzida minimizar as colisões entre as moléculas de gás, permitindo um processo de deposição mais ordenado. Consequentemente, a película resultante apresenta menos defeitos e uma estrutura mais consistente.
Por outro lado, pressões de gás mais elevadas podem levar a um aumento da rugosidade da película. Nestas condições, o material gasoso sofre colisões mais frequentes, o que pode perturbar o processo de deposição ordenado. Isto resulta numa película menos uniforme com uma rugosidade superficial potencialmente mais elevada. No entanto, é importante notar que as pressões mais elevadas também podem aumentar a taxa de deposição, embora à custa da qualidade da película.
Pressão do gás | Qualidade da película | Taxa de deposição |
---|---|---|
Menor | Melhor densificação e homogeneidade | Mais lenta |
Mais alta | Aumento da rugosidade | Mais rápida |
A pressão de gás ideal é frequentemente determinada pelos requisitos específicos da aplicação, equilibrando a necessidade de películas de alta qualidade com o desejo de taxas de deposição eficientes. Este equilíbrio delicado é crucial para alcançar as propriedades desejadas no produto final.
Áreas de aplicação do processo de revestimento PVD
Indústria eletrónica
No domínio dos dispositivos semicondutores, circuitos integrados e ecrãs, o processo de Deposição Física de Vapor (PVD) desempenha um papel fundamental no fabrico de várias películas. Especificamente, a PVD é utilizada para preparar três tipos principais de películas: películas condutoras, películas isolantes e películas ópticas.
Películas condutoras
As películas condutoras são essenciais para assegurar o fluxo de corrente eléctrica nos dispositivos electrónicos. Estas películas são normalmente feitas de metais como o alumínio, o cobre e o ouro, que são depositados utilizando técnicas como a evaporação térmica ou a pulverização catódica. A escolha do metal e do método de deposição pode afetar significativamente a condutividade, a aderência e o desempenho geral da película.
Películas isolantes
As películas isolantes, por outro lado, são cruciais para evitar curto-circuitos eléctricos e proteger componentes sensíveis. Materiais como o dióxido de silício (SiO₂) e o nitreto de silício (Si₃N₄) são normalmente utilizados para criar estas películas. O processo PVD permite um controlo preciso da espessura e uniformidade da película, o que é vital para manter a integridade e fiabilidade do dispositivo.
Películas ópticas
As películas ópticas são concebidas para gerir a interação da luz com a superfície do dispositivo, melhorando a nitidez do ecrã e reduzindo o brilho. Estas películas incluem frequentemente revestimentos antirreflexo e camadas de melhoria da transmitância. O processo PVD permite a criação destas películas com propriedades ópticas específicas, como o índice de refração e a transmitância, adaptadas para satisfazer os requisitos do dispositivo.
Em resumo, o processo PVD é indispensável na indústria eletrónica, oferecendo um método versátil e preciso para a produção de películas condutoras, isolantes e ópticas que são fundamentais para os dispositivos electrónicos modernos.
Dispositivos ópticos
O processo PVD (Deposição Física de Vapor) desempenha um papel crucial no fabrico de revestimentos ópticos, que são essenciais para melhorar o desempenho de vários dispositivos ópticos. Estes revestimentos incluem revestimentos antirreflexo, películas de melhoria da transmitância e camadas de proteção, todas elas concebidas para otimizar a interação da luz com a superfície do dispositivo.
Tipos de revestimentos ópticos
-
Revestimentos antirreflexo: Estes revestimentos são concebidos para minimizar a reflexão da luz, aumentando assim a quantidade de luz que passa através da superfície ótica. Isto é particularmente importante em aplicações como lentes de câmaras, óculos e painéis solares.
-
Películas de aumento da transmitância: Estas películas são concebidas para aumentar a transmissão de comprimentos de onda específicos da luz, o que é crucial em dispositivos como filtros e sensores ópticos.
-
Camadas de proteção: Estes revestimentos protegem o material subjacente de factores ambientais como a humidade, o pó e os danos mecânicos, garantindo a longevidade e o desempenho do dispositivo ótico.
Vantagens da PVD no revestimento ótico
- Precisão: O processo PVD permite o controlo preciso da espessura da película, o que é fundamental para obter as propriedades ópticas desejadas.
- Durabilidade: Os dispositivos ópticos revestidos por PVD apresentam uma durabilidade superior em comparação com os revestidos por outros métodos, o que os torna ideais para uma utilização a longo prazo em vários ambientes.
- Versatilidade: O processo PVD pode ser adaptado para criar uma vasta gama de revestimentos, satisfazendo as necessidades específicas de diferentes aplicações ópticas.
Aplicações em dispositivos ópticos
Tipo de dispositivo | Objetivo do revestimento |
---|---|
Lentes de câmaras | Revestimentos antirreflexo para uma melhor imagem |
Óculos | Camadas antirreflexo e resistentes a riscos |
Painéis solares | Revestimentos antirreflexo para maximizar a captação de energia |
Filtros ópticos | Melhoria da transmitância para comprimentos de onda específicos |
Sensores | Camadas de proteção para garantir um desempenho consistente |
O processo PVD não só melhora a funcionalidade destes dispositivos, como também prolonga a sua vida útil, tornando-o uma tecnologia indispensável na indústria ótica.
Componentes mecânicos
No domínio do tratamento de superfícies de componentes mecânicos, os processos de deposição física de vapor (PVD) desempenham um papel fundamental na melhoria da sua longevidade e desempenho operacionais. As técnicas de PVD são meticulosamente empregues para aumentar a resistência ao desgaste, a resistência à corrosão e a resistência à oxidação destes componentes. Isto resulta numa extensão significativa da sua vida útil, tornando-os mais fiáveis e duradouros em ambientes industriais exigentes.
A aplicação de PVD em componentes mecânicos não se limita a adicionar uma camada protetora; trata-se de integrar a ciência avançada dos materiais para criar superfícies capazes de resistir a condições extremas. Por exemplo, os componentes de motores automóveis, turbinas aeroespaciais e maquinaria industrial são frequentemente submetidos a condições rigorosas que podem levar a uma rápida degradação. Com a aplicação de revestimentos PVD, estes componentes são reforçados contra o desgaste causado pela fricção, reacções químicas e exposição a altas temperaturas.
Além disso, os revestimentos PVD podem ser adaptados para satisfazer os requisitos específicos de diferentes componentes mecânicos. Quer se trate de uma ferramenta de alta precisão no sector da indústria transformadora ou de uma peça crítica num dispositivo médico, a capacidade de personalizar o revestimento garante que cada componente tem um desempenho ótimo sob o seu conjunto único de condições. Este nível de personalização é conseguido através da variação dos parâmetros de deposição, tais como o tipo de material alvo, a pressão do gás e a temperatura, para afinar as propriedades da película resultante.
Em suma, a utilização de processos PVD no tratamento de superfícies de componentes mecânicos é um investimento estratégico para aumentar a sua durabilidade e desempenho, contribuindo, em última análise, para a eficiência e fiabilidade de várias aplicações industriais.
Revestimentos decorativos
O processo PVD é fundamental para a criação de películas decorativas que melhoram o aspeto estético de vários produtos. Estas películas, caracterizadas pelo seu brilho metálico e cores vibrantes, são amplamente utilizadas em sectores como a joalharia, os relógios e os artigos domésticos. O processo permite o controlo preciso da espessura e uniformidade da película, garantindo que o produto final cumpre os elevados padrões de apelo visual e durabilidade exigidos nestas indústrias.
No domínio da joalharia, os revestimentos PVD proporcionam um acabamento sofisticado que pode imitar o aspeto dos metais preciosos por uma fração do custo. Isto é particularmente vantajoso para a produção de grandes volumes, onde a manutenção de um aspeto luxuoso é crucial. Os relógios, por outro lado, beneficiam de revestimentos PVD que não só melhoram o seu aspeto visual como também oferecem resistência a riscos e à corrosão, prolongando a vida útil destes relógios.
Os produtos para o lar, como utensílios de cozinha e artigos decorativos, também utilizam revestimentos PVD para obter um aspeto moderno e elegante. A capacidade de incorporar várias cores e padrões nos revestimentos abre um vasto leque de possibilidades de design, tornando o PVD uma ferramenta versátil no fabrico de bens de consumo.
Além disso, o processo PVD é amigo do ambiente, uma vez que funciona em condições de vácuo, minimizando os resíduos e reduzindo o impacto ambiental associado aos métodos de revestimento tradicionais. Este aspeto de sustentabilidade reforça ainda mais o seu apelo nas indústrias em que a estética e a responsabilidade ambiental são fundamentais.
Vantagens e desafios do processo PVD
Vantagens
Os processos de revestimento PVD oferecem várias vantagens atraentes que os tornam uma escolha preferida em vários sectores. Uma das vantagens mais significativas é a produção depelículas de alta qualidade. Estas películas apresentam uma excecionaladerência,uniformidadeeintegridade estruturalque são cruciais para melhorar o desempenho dos materiais revestidos. Por exemplo, na indústria eletrónica, as películas condutoras revestidas por PVD asseguram uma condutividade eléctrica superior e uma perda mínima de sinal, enquanto que nos dispositivos ópticos, os revestimentos proporcionam propriedades ópticas precisas que melhoram o desempenho do dispositivo.
Outra vantagem notável é arespeito pelo ambiente dos processos PVD. Ao contrário de alguns outros métodos de revestimento, a PVD funciona em condições de vácuo, minimizando a libertação de substâncias nocivas para o ambiente. Isto faz da PVD uma opção sustentável, particularmente em indústrias onde os regulamentos ambientais são rigorosos. Além disso, a utilização de gases inertes, como o árgon e o hélio, garante que a pureza das películas é mantida sem a introdução de quaisquer subprodutos reactivos que possam prejudicar o ambiente.
Aversatilidade dos processos de PVD é também um ponto forte. A PVD pode ser aplicada a uma vasta gama de materiais, incluindo metais, cerâmicas e polímeros, tornando-a adequada para diversas aplicações. Quer se trate da preparação de películas finas para semicondutores, do aumento da durabilidade de componentes mecânicos ou da criação de revestimentos decorativos para produtos de consumo, a PVD oferece uma solução flexível que pode ser adaptada para satisfazer necessidades específicas. Por exemplo, a utilização de gases reactivos como o oxigénio e o azoto permite a criação de películas complexas de óxido e nitreto, expandindo ainda mais a gama de aplicações possíveis.
Em resumo, a combinação de produção de películas de alta qualidade, sustentabilidade ambiental e ampla aplicabilidade faz dos processos de revestimento PVD uma tecnologia altamente vantajosa em vários sectores.
Desafios
Um dos principais desafios associados aos processos de Deposição Física de Vapor (PVD) é o significativocusto do equipamento. Os sistemas avançados de PVD, como os que utilizam a evaporação por feixe de electrões ou a deposição por laser pulsado, requerem maquinaria sofisticada e sistemas de controlo precisos, que podem ser proibitivamente dispendiosos para as operações mais pequenas. Além disso, a manutenção e a calibração destes sistemas exigem conhecimentos especializados, contribuindo ainda mais para o custo global.
Outro desafio crítico são astaxas de deposição. A obtenção de taxas de deposição óptimas é crucial para uma produção eficiente, mas pode ser influenciada por uma miríade de factores, incluindo a pressão do gás, a temperatura do substrato e o tipo de material alvo utilizado. Taxas de deposição mais lentas podem levar a tempos de processamento mais longos, aumentando os custos operacionais e afectando potencialmente a qualidade da película depositada. Por outro lado, taxas de deposição mais elevadas podem resultar em películas com propriedades inferiores às ideais, como densidade reduzida ou rugosidade aumentada.
O controlo da espessura da película é também um obstáculo significativo nos processos de PVD. Garantir uma espessura uniforme da película em todo o substrato é essencial para o desempenho e fiabilidade do produto final. No entanto, manter um controlo preciso da espessura da película pode ser um desafio, especialmente quando se trata de geometrias complexas ou de substratos de grandes dimensões. As variações de espessura podem levar a inconsistências nas propriedades da película, como as suas caraterísticas ópticas, mecânicas ou eléctricas, o que pode ser prejudicial para a aplicação pretendida.
Para enfrentar estes desafios, a investigação em curso e os avanços tecnológicos centram-se no desenvolvimento de equipamento mais rentável, na otimização dos parâmetros de deposição e na melhoria dos mecanismos de controlo da espessura da película. Estes esforços visam aumentar a eficiência e a fiabilidade dos processos de PVD, tornando-os mais acessíveis e eficazes em várias indústrias.
CONTACTE-NOS PARA UMA CONSULTA GRATUITA
Os produtos e serviços da KINTEK LAB SOLUTION foram reconhecidos por clientes de todo o mundo. A nossa equipa terá todo o prazer em ajudar com qualquer questão que possa ter. Contacte-nos para uma consulta gratuita e fale com um especialista de produto para encontrar a solução mais adequada para as suas necessidades de aplicação!