O amoníaco é utilizado no processo de recozimento principalmente porque pode ser dissociado numa mistura gasosa de 75% de hidrogénio e 25% de azoto, o que proporciona várias vantagens. O hidrogénio, um componente-chave desta mistura, tem um elevado coeficiente de transferência de calor, tornando o processo de recozimento mais eficiente e eficaz. Além disso, o hidrogénio no amoníaco dissociado evita a oxidação, assegurando a integridade dos materiais a tratar. A utilização de amoníaco dissociado é também rentável em comparação com o hidrogénio puro, tornando-o uma escolha prática para aplicações industriais. Esta combinação de eficiência, proteção e custo-benefício faz do amoníaco um recurso valioso nos processos de recozimento.
Pontos-chave explicados:
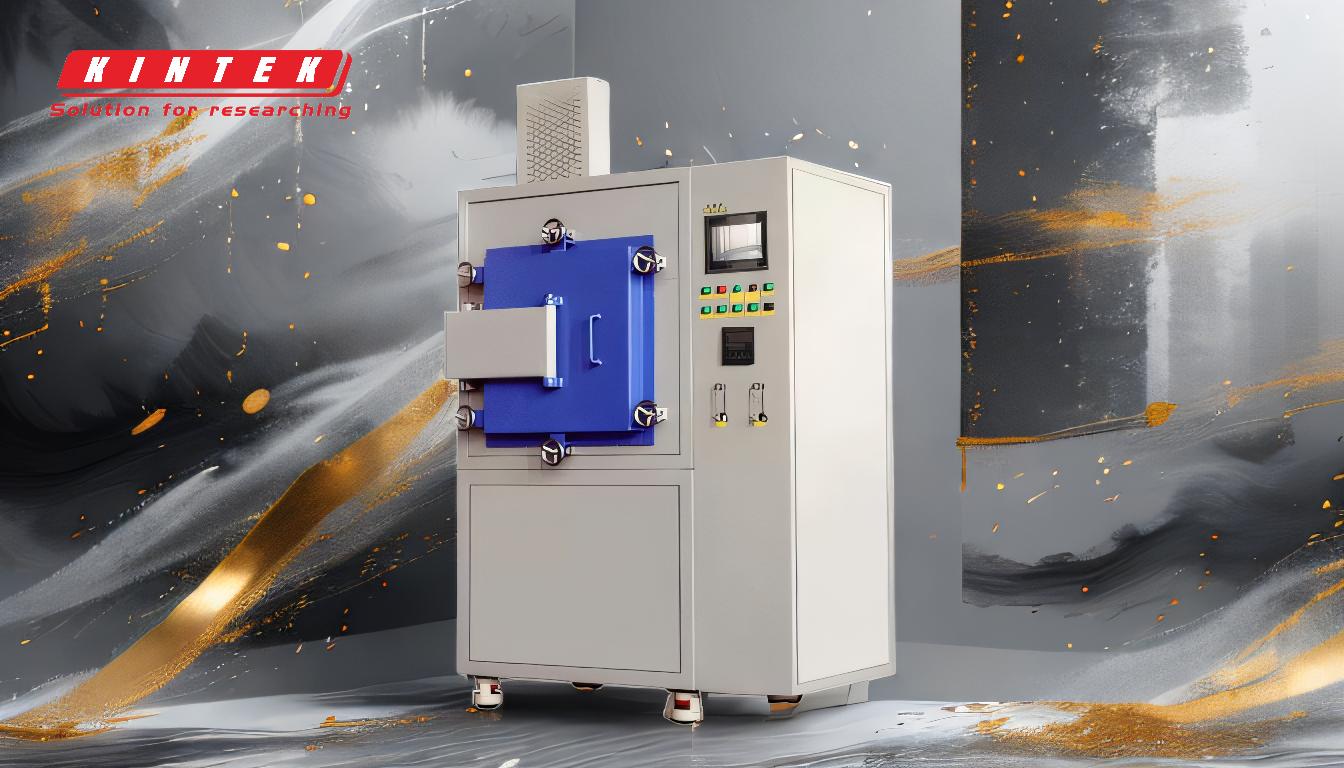
-
Dissociação do amoníaco:
- O amoníaco pode ser dissociado (crackeado) numa mistura gasosa contendo 75% de hidrogénio e 25% de azoto.
- Este processo de dissociação faz do amoníaco uma fonte versátil de hidrogénio e azoto, que são essenciais em vários processos de tratamento térmico, incluindo o recozimento.
-
Papel do hidrogénio no recozimento:
- O hidrogénio, um dos principais componentes do amoníaco dissociado, tem um elevado coeficiente de transferência de calor, o que aumenta a eficiência do processo de recozimento.
- Uma transferência de calor eficiente garante um aquecimento e arrefecimento uniformes dos materiais, o que é crucial para alcançar as propriedades mecânicas desejadas e reduzir as tensões internas.
-
Prevenção da oxidação:
- O hidrogénio presente no amoníaco dissociado actua como agente redutor, impedindo a oxidação dos materiais durante o processo de recozimento.
- A oxidação pode levar a defeitos na superfície e à degradação das propriedades do material, pelo que a atmosfera protetora fornecida pelo hidrogénio é fundamental para manter a integridade do material.
-
Custo-eficácia:
- O amoníaco dissociado oferece muitas das vantagens do hidrogénio puro, mas a um custo inferior.
- Esta vantagem de custo torna-o uma opção atractiva para aplicações industriais em que são necessários grandes volumes de gás.
-
Versatilidade e praticidade:
- O amoníaco pode ser produzido e armazenado sob várias formas (gás gerado, gás engarrafado ou gás armazenado a granel), o que o torna uma escolha flexível e prática para diferentes instalações industriais.
- A sua capacidade de servir dois objectivos (como fonte de azoto para a nitretação e de hidrogénio para a redução) aumenta a sua versatilidade nos processos de tratamento térmico.
-
Aplicação no tratamento térmico de componentes fundidos e soldados:
- A utilização de amoníaco dissociado é particularmente benéfica no tratamento térmico de componentes fundidos e soldados, onde a transferência de calor eficiente e a prevenção da oxidação são cruciais.
- Estes componentes requerem frequentemente um tratamento térmico preciso para obter as propriedades mecânicas e a integridade estrutural desejadas.
Ao aproveitar as propriedades do amoníaco dissociado, as indústrias podem obter processos de recozimento eficientes, eficazes e económicos, garantindo resultados de alta qualidade para os materiais tratados.
Quadro de resumo:
Benefício chave | Explicação |
---|---|
Dissociação do amoníaco | O amoníaco dissocia-se em 75% de hidrogénio e 25% de azoto, ideal para o tratamento térmico. |
Transferência de calor eficiente | O elevado coeficiente de transferência de calor do hidrogénio assegura um aquecimento e arrefecimento uniformes. |
Prevenção da oxidação | O hidrogénio actua como um agente redutor, protegendo os materiais da oxidação. |
Custo-eficácia | O amoníaco dissociado é mais económico do que o hidrogénio puro para utilização industrial. |
Versatilidade | O amoníaco tem uma dupla função: o hidrogénio para a redução e o azoto para a nitretação. |
Aplicações industriais | Ideal para o tratamento térmico de componentes fundidos e soldados, garantindo a integridade do material. |
Optimize o seu processo de recozimento com amoníaco dissociado contacte-nos hoje para saber mais!