Os fornos de recozimento utilizam principalmente gases inertes como o azoto (N2), o árgon (Ar) e o hélio (He) para criar uma atmosfera protetora que evita a oxidação, a descarbonetação e outras reacções químicas indesejáveis durante o processo de recozimento. Os gases inertes de elevada pureza (pureza > 99,99%) são essenciais para manter a integridade do material que está a ser tratado. Adicionalmente, o hidrogénio (H2) é utilizado em aplicações específicas, tais como fornos de vácuo a hidrogénio, devido às suas propriedades redutoras. A escolha do gás depende do material, dos requisitos do processo e dos resultados desejados, sendo a pressão normalmente mantida entre 0,05 e 0,07 MPa para obter os melhores resultados.
Pontos-chave explicados:
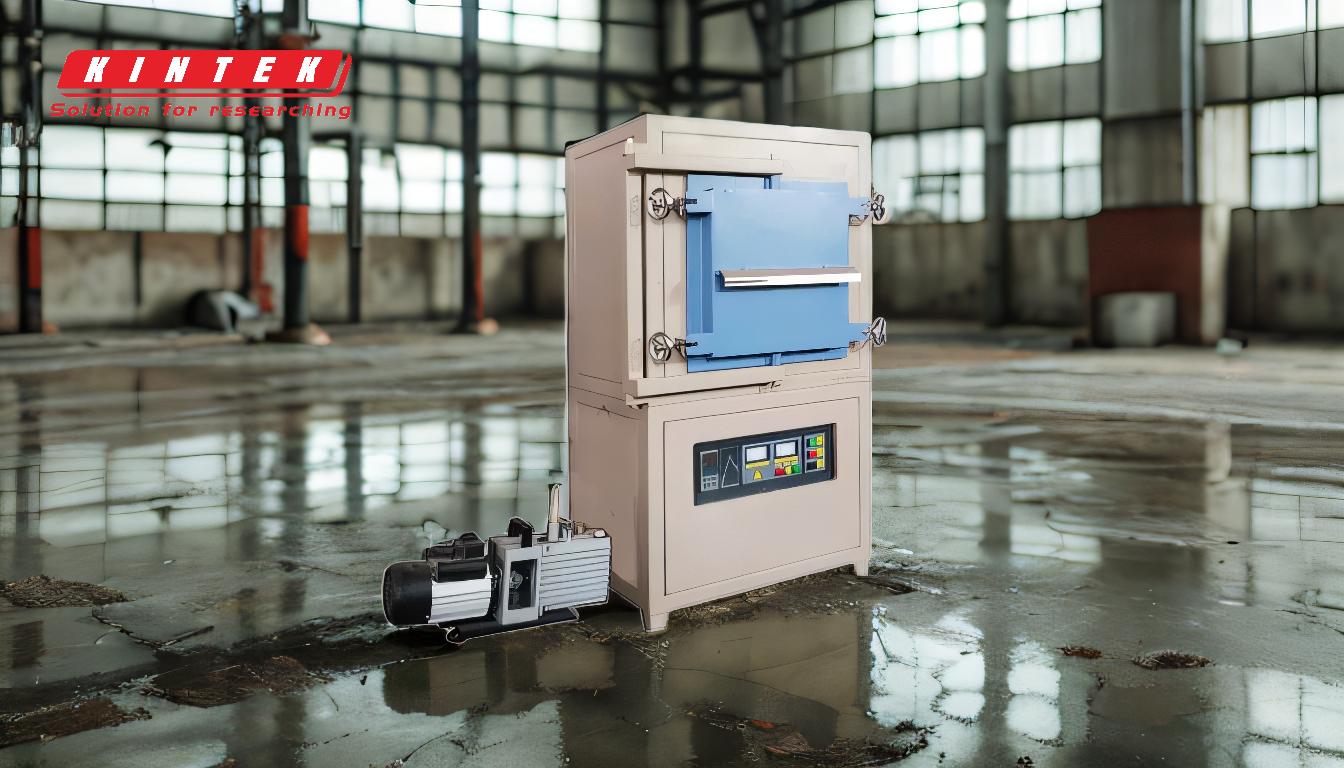
-
Gases primários utilizados nos fornos de recozimento:
- Azoto (N2): Um gás inerte económico e amplamente utilizado que evita a oxidação e a descarbonetação. É adequado para a maioria dos processos de recozimento, especialmente para metais não reactivos como o aço inoxidável.
- Árgon (Ar): Um gás inerte mais pesado que proporciona uma excelente proteção contra a oxidação e é frequentemente utilizado para recozer materiais reactivos ou de elevado valor como o titânio e ligas especiais.
- Hélio (He): Um gás inerte mais leve com elevada condutividade térmica, tornando-o adequado para processos que requerem uma rápida transferência de calor. É menos utilizado devido ao seu custo mais elevado.
- Hidrogénio (H2): Utilizado nos fornos de vácuo a hidrogénio pelas suas propriedades redutoras, que ajudam a remover os óxidos das superfícies metálicas. É particularmente útil para o recozimento de materiais como o aço silício.
-
Importância da pureza do gás:
- Os gases inertes de elevada pureza (pureza > 99,99%) são essenciais nos fornos de recozimento para evitar a contaminação e garantir resultados consistentes. As impurezas no gás podem levar à oxidação, descarbonetação ou outros defeitos no material tratado.
- O grau de pureza garante que a atmosfera protetora permanece estável e eficaz durante todo o processo de recozimento.
-
Requisitos de pressão:
- A pressão do gás inerte no forno de recozimento é normalmente mantida entre 0,05 e 0,07 MPa. Esta gama assegura uma atmosfera protetora estável, minimizando o risco de fugas de gás ou de consumo excessivo.
- O controlo adequado da pressão é essencial para obter um tratamento térmico uniforme e evitar defeitos no material.
-
Papel dos gases inertes no recozimento:
- Os gases inertes criam um ambiente não reativo que impede a oxidação, a descarbonetação e outras reacções químicas durante o processo de recozimento.
- Ajudam a manter a qualidade da superfície, as propriedades mecânicas e a estabilidade dimensional do material.
-
Aplicações de gases específicos:
- Nitrogénio: Normalmente utilizado para recozer aço inoxidável, cobre e outros metais não reactivos.
- Árgon: Preferido para recozer metais reactivos como o titânio, o zircónio e ligas especiais.
- Hidrogénio: Utilizado em fornos de vácuo a hidrogénio para o recozimento de materiais que requerem a remoção de óxidos, como o aço silício.
-
Vantagens da utilização de gases inertes:
- Precisão: Os gases inertes permitem um controlo preciso do processo de recozimento, garantindo resultados consistentes.
- Integridade do material: Protegem o material de defeitos superficiais e mantêm as suas propriedades mecânicas.
- Versatilidade: Podem ser selecionados diferentes gases com base nos requisitos do material e do processo.
-
Considerações sobre a seleção do gás:
- Compatibilidade de materiais: A escolha do gás depende do material a ser recozido. Por exemplo, o árgon é preferido para os metais reactivos, enquanto o azoto é adequado para os metais não reactivos.
- Custo: O nitrogénio é mais económico do que o árgon ou o hélio, o que o torna uma escolha popular para operações em grande escala.
- Requisitos do processo: O hidrogénio é utilizado quando é necessária a remoção de óxidos, enquanto o hélio é escolhido para processos que requerem uma rápida transferência de calor.
Ao compreender estes pontos-chave, os compradores de equipamento e de consumíveis podem tomar decisões informadas sobre o tipo de gás a utilizar nos fornos de recozimento, garantindo resultados óptimos e uma boa relação custo-eficácia.
Quadro de resumo:
Gás | Propriedades principais | Aplicações |
---|---|---|
Azoto (N2) | Económica, evita a oxidação e a descarbonetação | Aço inoxidável, cobre, metais não reactivos |
Árgon (Ar) | Gás inerte pesado, excelente proteção contra a oxidação | Titânio, zircónio, ligas especiais |
Hélio (He) | Gás inerte leve, alta condutividade térmica | Processos que requerem uma rápida transferência de calor |
Hidrogénio (H2) | Propriedades redutoras, eliminação de óxidos | Aço silício, fornos de vácuo a hidrogénio |
Precisa de ajuda para selecionar o gás certo para o seu forno de recozimento? Contacte os nossos especialistas hoje mesmo para uma orientação personalizada!