Os fornos rotativos são equipamentos de processamento a alta temperatura utilizados em indústrias como a produção de cimento, redução de minério de ferro e processamento químico.O revestimento refratário é um componente crítico, uma vez que protege o revestimento do forno do calor extremo e das reacções químicas, assegurando simultaneamente uma transferência de calor eficiente para o material a ser processado.A escolha do material refratário depende do processo específico, da temperatura e do ambiente químico dentro do forno.Os materiais refractários mais comuns incluem a alumina com baixo teor de ferro, os tijolos de magnésio-spinel e os tijolos de magnesite, sendo a seleção influenciada por factores como a resistência ao desgaste, a condutividade térmica e a estabilidade química.Os refractários podem ser fundidos (vertidos no local) ou em tijolo (colocados manualmente), cada um oferecendo vantagens distintas em termos de facilidade de instalação e durabilidade.
Pontos-chave explicados:
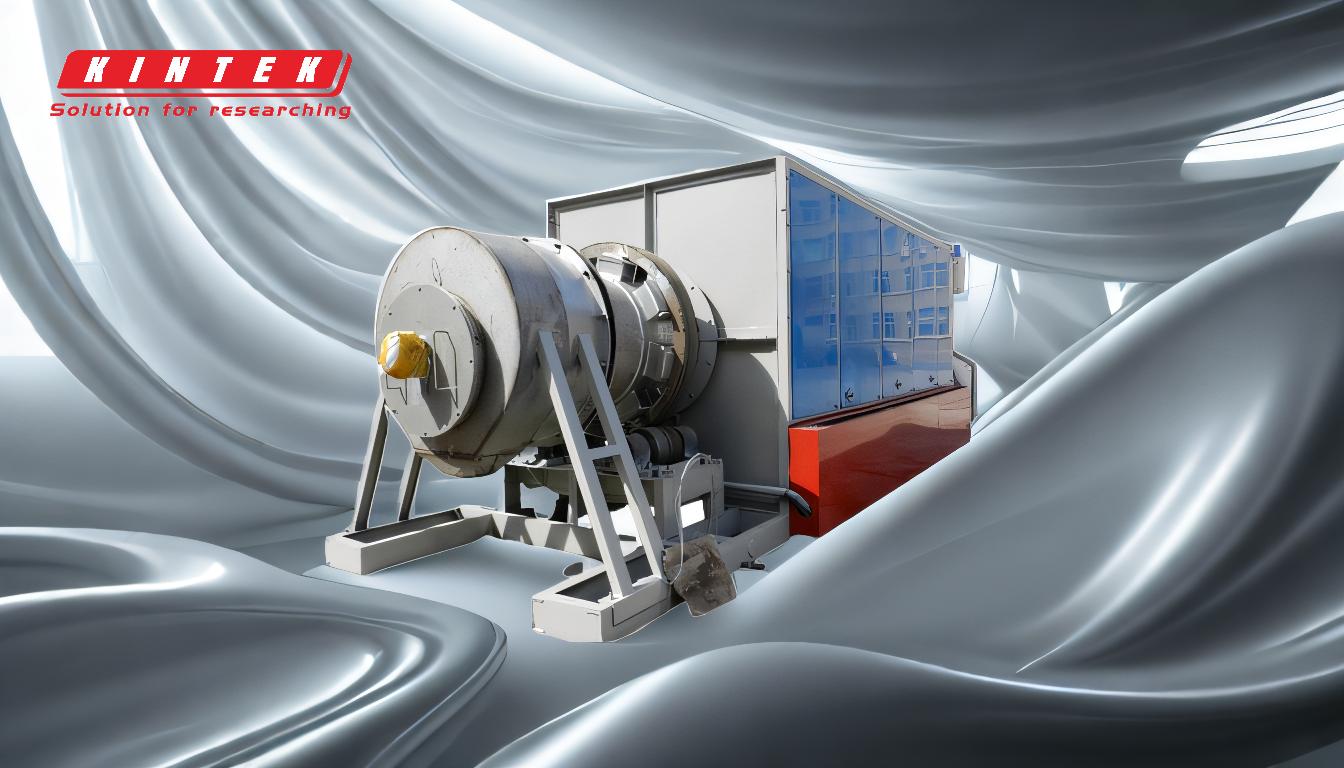
-
Objetivo do revestimento refratário em fornos rotativos:
- O revestimento refratário serve como uma barreira protetora entre a estrutura do forno e o ambiente de alta temperatura no interior do forno.
- Evita a perda de calor, protege o revestimento contra danos térmicos e químicos e assegura uma transferência de calor eficiente para o material a ser processado.
- O revestimento tem de suportar temperaturas extremas, tensões mecânicas e reacções químicas durante o funcionamento.
-
Factores que influenciam a seleção do material refratário:
-
Requisitos do processo:O tipo de material a ser processado (por exemplo, cimento, minério de ferro ou produtos químicos) determina a escolha do refratário.Por exemplo:
- Os tijolos de alumina com baixo teor de ferro ou de magnésio-espinélio são utilizados em fornos de redução de minério de ferro devido à sua resistência a atmosferas redutoras.
- Os tijolos de magnesite são preferidos nos fornos de cimento devido à sua elevada estabilidade térmica e resistência a ambientes alcalinos.
- Temperatura:Os refractários devem suportar a temperatura de funcionamento do forno, que pode ultrapassar os 1.400°C nos fornos de cimento.
- Ambiente Químico:O refratário deve resistir às reacções químicas com o material processado, os gases e as escórias.
- Tensões mecânicas:O revestimento deve resistir à abrasão, ao impacto e ao ciclo térmico.
-
Requisitos do processo:O tipo de material a ser processado (por exemplo, cimento, minério de ferro ou produtos químicos) determina a escolha do refratário.Por exemplo:
-
Tipos de materiais refractários:
-
Refractários de tijolo:
- Fabricados a partir de tijolos pré-formados, normalmente compostos por materiais como a magnesite, a alumina ou o espinélio.
- Altamente resistentes ao desgaste, o que os torna adequados para materiais abrasivos.
- A sua instalação é trabalhosa, mas oferecem uma vida útil mais longa em condições adversas.
-
Refractários Fundíveis:
- Composto por agregados refractários e aglutinantes, vazados no local para formar um revestimento monolítico.
- Mais fácil e rápido de instalar em comparação com os tijolos.
- Menos resistente ao desgaste, mas adequado para ambientes menos abrasivos ou áreas com geometrias complexas.
-
Refractários de tijolo:
-
Materiais refractários comuns utilizados em fornos rotativos:
- Alumina com baixo teor de ferro:Utilizado em fornos de redução de minério de ferro devido à sua resistência a atmosferas redutoras e à sua elevada estabilidade térmica.
- Tijolos de magnésio-espinafre:Oferecem uma excelente resistência ao choque térmico e são utilizados em aplicações de alta temperatura.
- Tijolos de magnesite:Preferidos nos fornos de cimento pela sua resistência aos meios alcalinos e pela sua elevada condutividade térmica.
-
Métodos de instalação:
-
Revestimento de tijolos:
- Os tijolos são colocados manualmente, muitas vezes com argamassa ou adesivos especializados.
- Proporciona um revestimento durável e resistente ao desgaste, mas requer mão de obra especializada e um tempo de instalação mais longo.
-
Revestimento fundido:
- Vazado no local e curado para formar uma estrutura monolítica.
- Instalação mais rápida e melhor adaptabilidade a formas complexas, mas pode exigir um tempo de cura adicional.
-
Revestimento de tijolos:
-
Considerações sobre o desempenho:
- Condutividade térmica:Os refractários devem equilibrar a retenção e a transferência de calor para garantir um processamento eficiente.
- Resistência ao desgaste:O revestimento deve resistir à abrasão do material a ser processado.
- Estabilidade química:A resistência a reacções com materiais processados, gases e escórias é fundamental.
- Resistência ao choque térmico:A capacidade de resistir a mudanças rápidas de temperatura sem fissurar.
-
Manutenção e duração de vida:
- É necessária uma inspeção e manutenção regulares para controlar o desgaste do refratário e evitar falhas.
- A vida útil do revestimento refratário depende do material, das condições de funcionamento e das práticas de manutenção.
- As secções refractárias danificadas ou gastas podem ser substituídas individualmente, minimizando o tempo de paragem.
Em resumo, o material refratário de um forno rotativo é um componente vital que assegura um funcionamento eficiente e seguro.A escolha do material depende do processo específico, da temperatura e do ambiente químico, com opções como a alumina com baixo teor de ferro, o magnésio-spinel e os tijolos de magnesite a serem normalmente utilizados.Tanto os refractários de tijolo como os refractários moldáveis têm as suas vantagens, com os tijolos a oferecerem uma resistência superior ao desgaste e os moldáveis a facilitarem a instalação.A seleção, instalação e manutenção adequadas do revestimento refratário são essenciais para maximizar o desempenho e a vida útil do forno.
Tabela de resumo:
Aspeto-chave | Detalhes |
---|---|
Objetivo | Protege o corpo do forno, assegura a transferência de calor e resiste a condições extremas. |
Factores de seleção do material | Tipo de processo, temperatura, ambiente químico e tensão mecânica. |
Materiais comuns | Alumina com baixo teor de ferro, tijolos de magnésio-espinélio, tijolos de magnesite. |
Métodos de instalação | Tijolo (manual, durável) ou betão vazado (vazado, instalação mais rápida). |
Considerações sobre o desempenho | Condutividade térmica, resistência ao desgaste, estabilidade química, choque térmico. |
Manutenção | Inspecções e substituições regulares para maximizar a vida útil. |
Optimize o desempenho do seu forno rotativo com o revestimento refratário adequado. contacte hoje os nossos especialistas !