O recozimento é um processo de tratamento térmico utilizado para alterar as propriedades físicas e, por vezes, químicas de um material, normalmente metais, para aumentar a sua ductilidade e reduzir a sua dureza, tornando-o mais trabalhável.O processo envolve três fases principais:Recuperação, Recristalização e Crescimento de Grãos.Cada fase é crucial para alcançar as propriedades desejadas do material, e o processo requer um controlo preciso da temperatura e das taxas de arrefecimento para garantir que o material alcança as alterações estruturais pretendidas.
Pontos-chave explicados:
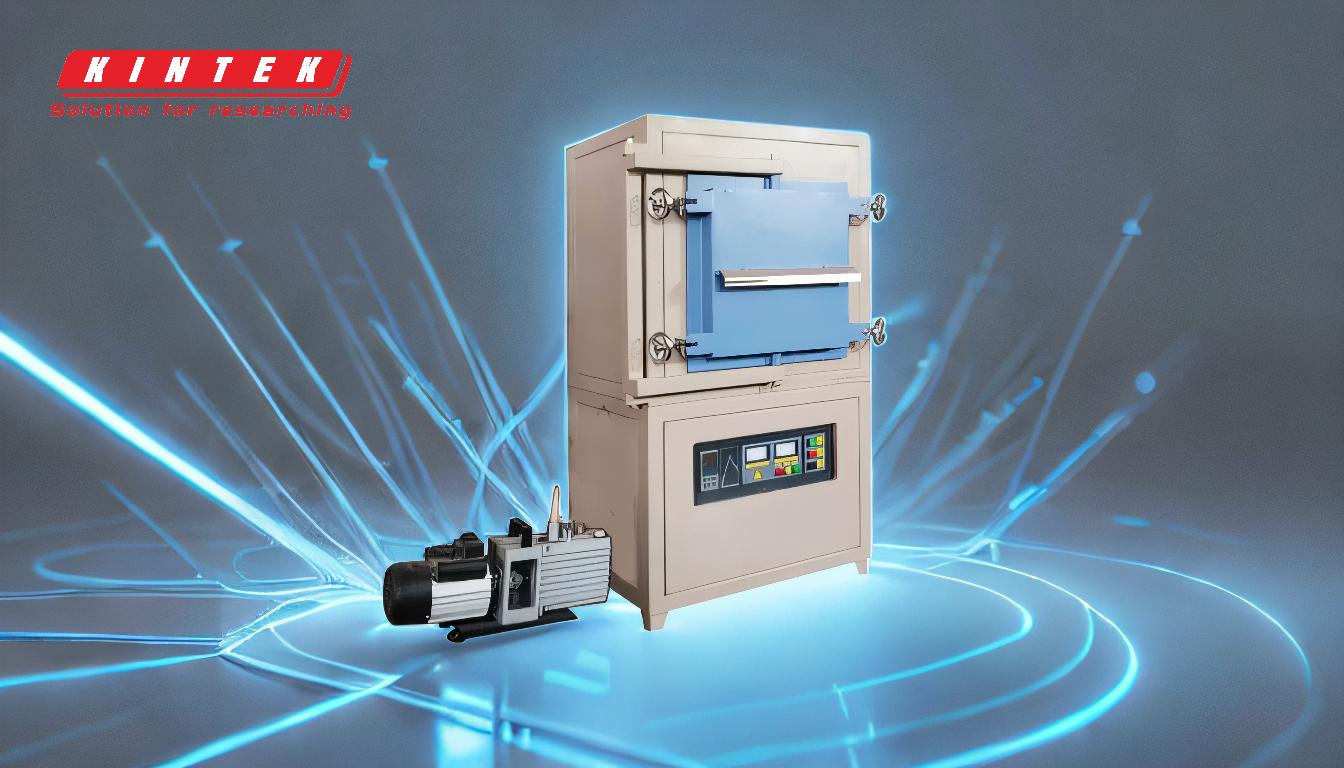
-
Aquecimento a uma temperatura específica:
- Objetivo:O principal requisito para o recozimento é o aquecimento do metal a uma temperatura específica em que a sua estrutura cristalina se torna fluida, mas permanece no estado sólido.Esta temperatura varia consoante o tipo de metal e a composição específica da liga.
- Importância:O aquecimento à temperatura correta é crucial porque permite aliviar as tensões internas e os defeitos do metal.Esta fase estabelece a base para as fases subsequentes do recozimento.
-
Manutenção da temperatura:
- Objetivo:Depois de atingir a temperatura desejada, o metal deve ser mantido a essa temperatura durante um período específico.Este tempo de permanência permite que os defeitos do material se reparem através de um processo conhecido como recuperação.
- Importância:O tempo de espera é crítico porque garante que o metal sofra uma recuperação suficiente, que é a primeira fase do recozimento.Durante a recuperação, as deslocações na estrutura do metal são reduzidas, levando a uma diminuição das tensões internas.
-
Arrefecimento controlado:
- Objetivo:Após o período de espera, o metal é deixado arrefecer lentamente até à temperatura ambiente.Esta taxa de arrefecimento lento é essencial para produzir uma estrutura cristalina mais dúctil.
- Importância:O arrefecimento controlado é vital porque evita a formação de novas tensões e permite que o metal atinja uma estrutura de grão mais uniforme e refinada.O arrefecimento rápido, por outro lado, pode levar à formação de uma estrutura frágil, o que é indesejável para a maioria das aplicações.
-
Fases do recozimento:
- Recuperação:Esta é a primeira fase em que o metal é aquecido a uma temperatura abaixo do seu ponto de recristalização.Durante esta fase, as tensões internas são aliviadas e as deslocações na estrutura do metal são reduzidas.
- Recristalização:Nesta fase, o metal é aquecido a uma temperatura acima do seu ponto de recristalização.Novos grãos, livres de tensão, começam a formar-se, substituindo os grãos deformados da fase anterior.
- Crescimento dos grãos:A fase final consiste em manter o metal a uma temperatura que permita o crescimento dos grãos recém-formados.Esta fase é controlada para garantir que os grãos não cresçam demasiado, o que poderia afetar negativamente as propriedades mecânicas do metal.
-
Requisitos específicos do material:
- Importância:Diferentes metais e ligas têm requisitos específicos de recozimento, incluindo gamas de temperatura e taxas de arrefecimento.Por exemplo, a temperatura de recozimento do aço é diferente da do alumínio ou do cobre.
- Considerações:Os requisitos específicos para o recozimento devem ser cuidadosamente considerados com base nas propriedades do material e no resultado desejado.Isto inclui a compreensão do diagrama de fases do material e os efeitos de diferentes temperaturas na sua microestrutura.
-
Equipamento e ambiente:
- Importância:O equipamento utilizado para o recozimento, como os fornos, deve ser capaz de manter um controlo preciso da temperatura e um aquecimento uniforme.O ambiente no interior do forno também deve ser controlado para evitar a oxidação ou outras reacções superficiais que possam afetar as propriedades do metal.
- Considerações:A escolha do equipamento e o ambiente em que o recozimento é efectuado podem ter um impacto significativo na qualidade do material recozido.O isolamento adequado, a monitorização da temperatura e o controlo da atmosfera são essenciais para obter resultados consistentes.
Em resumo, os requisitos para o recozimento envolvem um controlo preciso dos processos de aquecimento, retenção e arrefecimento, bem como a compreensão das necessidades específicas do material a ser tratado.Cada etapa do processo de recozimento desempenha um papel crítico na obtenção das propriedades desejadas do material, e deve ser dada uma atenção cuidadosa ao equipamento e ao ambiente para garantir resultados bem-sucedidos.
Tabela de resumo:
Fase | Objetivo | Importância |
---|---|---|
Aquecimento | Aquecer o metal a uma temperatura específica para fluidez da estrutura cristalina. | Alivia as tensões internas e os defeitos, estabelecendo as bases para o recozimento. |
Manutenção | Manter a temperatura para permitir a recuperação de defeitos. | Assegura uma recuperação suficiente, reduzindo as deslocações e as tensões internas. |
Arrefecimento | Arrefecer lentamente o metal até à temperatura ambiente. | Evita novas tensões, obtendo uma estrutura de grão uniforme e refinada. |
Recuperação | Aliviar as tensões internas e reduzir as deslocações. | Prepara o metal para a recristalização. |
Recristalização | Forma grãos novos e livres de tensão. | Substitui os grãos deformados, melhorando as propriedades do material. |
Crescimento de grãos | Permite que os grãos recém-formados cresçam em condições controladas. | Assegura que os grãos não crescem demasiado, mantendo as propriedades mecânicas. |
Optimize o seu processo de recozimento com orientação especializada- contacte-nos hoje para soluções à medida!