Sim, existem diferentes tipos de processos de recozimento, cada um deles adaptado para obter propriedades específicas dos materiais ou responder a necessidades industriais particulares. O recozimento é um processo de tratamento térmico que envolve o aquecimento do metal a uma temperatura específica, mantendo-o nessa temperatura e, em seguida, arrefecendo-o a uma velocidade controlada. Este processo ajuda a amolecer os materiais, a melhorar a maquinabilidade, a reduzir as tensões internas e a melhorar as propriedades mecânicas ou eléctricas. Os tipos específicos de recozimento incluem o recozimento preto, o recozimento azul, o recozimento em caixa, o recozimento brilhante, o recozimento cíclico, o recozimento por chama, o recozimento total, a grafitização, o recozimento intermédio, o recozimento isotérmico, o recozimento de processo, o recozimento de têmpera e a esferoidização. Cada tipo é concebido para aplicações e materiais específicos, garantindo a obtenção da microestrutura e das propriedades desejadas.
Pontos-chave explicados:
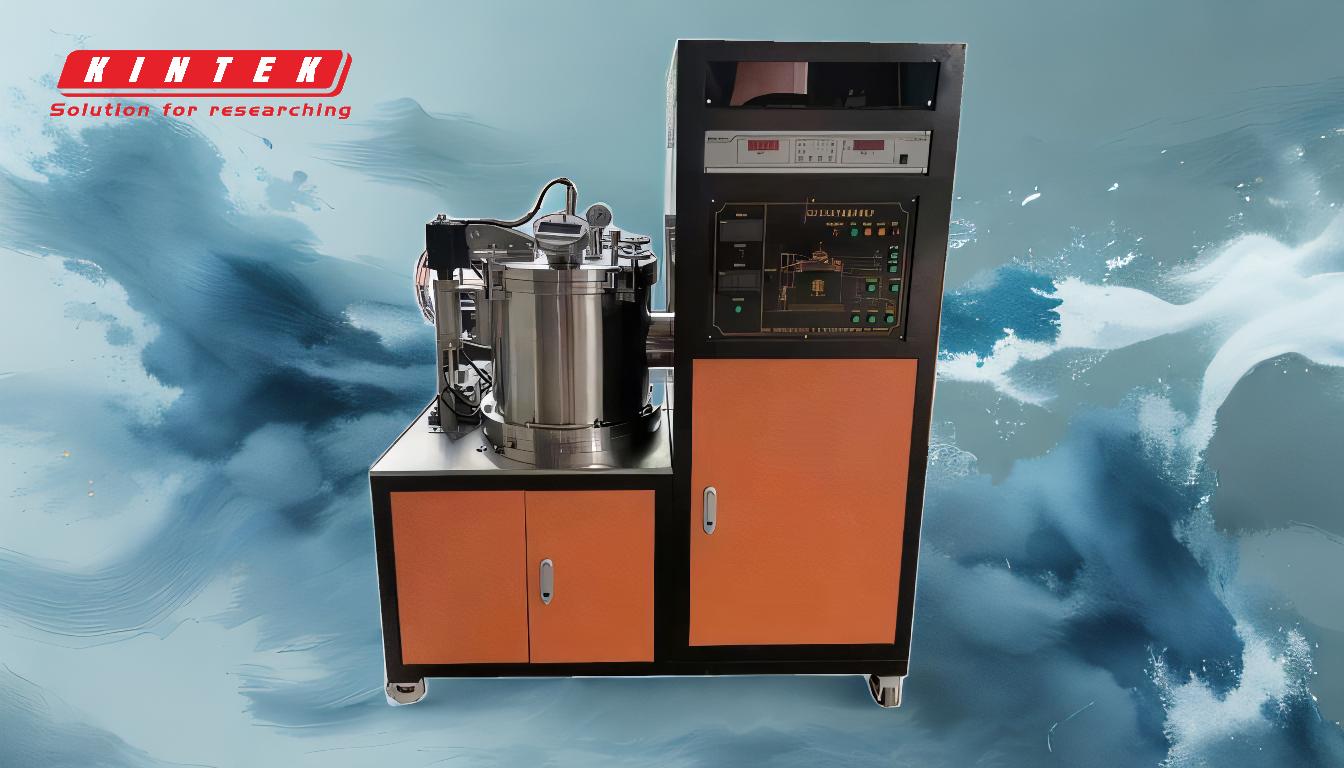
-
Definição de recozimento:
- O recozimento é um processo de tratamento térmico que envolve o aquecimento de um material a uma temperatura específica, mantendo-o a essa temperatura e, em seguida, arrefecendo-o a uma velocidade controlada. Este processo é utilizado para amolecer materiais, melhorar a maquinabilidade, reduzir tensões internas e melhorar as propriedades mecânicas ou eléctricas.
-
Fases do recozimento:
- Recuperação: Esta é a primeira fase em que o material é aquecido para aliviar as tensões internas sem alterar significativamente a sua microestrutura.
- Recristalização: Nesta fase, formam-se novos grãos no material, substituindo os grãos deformados. Isto ocorre a temperaturas mais elevadas e resulta num material mais macio e dúctil.
- Crescimento dos grãos: A fase final envolve o crescimento destes novos grãos, que podem afetar as propriedades mecânicas do material. O controlo desta fase é essencial para obter as caraterísticas desejadas do material.
-
Tipos de recozimento:
- Recozimento preto: Normalmente utilizado para o aço, este processo envolve o aquecimento do material num forno aberto, resultando numa camada de óxido preto na superfície.
- Recozimento azul: Semelhante ao Recozimento Negro, mas efectuado a uma temperatura mais baixa, resultando numa camada de óxido azul. É frequentemente utilizado para o aço inoxidável.
- Recozimento em caixa: O material é aquecido num recipiente selado para o proteger da oxidação. Este método é utilizado para materiais que requerem uma atmosfera controlada.
- Recozimento brilhante: Conduzido numa atmosfera controlada ou vácuo para evitar a oxidação, resultando numa superfície limpa e brilhante. Normalmente utilizado para aço inoxidável e outros metais não ferrosos.
- Ciclo de recozimento: Envolve ciclos repetidos de aquecimento e arrefecimento para obter propriedades específicas do material.
- Recozimento por chama: Utiliza uma chama direta para aquecer o material, frequentemente utilizada para recozimento localizado.
- Recozimento total: Aquece o material a uma temperatura superior à sua temperatura crítica superior, seguida de um arrefecimento lento. Este processo é utilizado para obter a máxima suavidade e ductilidade.
- Grafitização: Processo de recozimento especializado utilizado no ferro fundido para converter a cementita em grafite, melhorando a maquinabilidade e reduzindo a fragilidade.
- Recozimento intermédio: Realizado entre as fases de trabalho a frio para restaurar a ductilidade e reduzir a dureza.
- Recozimento isotérmico: O material é aquecido a uma temperatura específica e depois mantido a essa temperatura até se obter a microestrutura desejada, seguida de arrefecimento.
- Processo de recozimento: Processo de recozimento a baixa temperatura utilizado para aliviar tensões em materiais trabalhados a frio sem alterar significativamente a sua microestrutura.
- Recozimento de têmpera: Envolve um arrefecimento rápido após o aquecimento, frequentemente utilizado para aços inoxidáveis para obter uma microestrutura específica.
- Esferoidização: Processo utilizado para produzir uma microestrutura esferoidal em aços com elevado teor de carbono, melhorando a maquinabilidade e reduzindo a fragilidade.
-
Aplicações do recozimento:
- Melhorar a maquinabilidade: O recozimento amolece os materiais, tornando-os mais fáceis de maquinar.
- Facilitar o trabalho a frio: Ao reduzir a dureza, o recozimento torna os materiais mais susceptíveis de serem trabalhados a frio, como a laminagem ou a trefilagem.
- Melhoria das propriedades mecânicas: O recozimento pode melhorar a tenacidade, a ductilidade e outras propriedades mecânicas.
- Aumento da estabilidade dimensional: Ao aliviar as tensões internas, o recozimento ajuda a manter a estabilidade dimensional dos componentes.
-
Importância do arrefecimento controlado:
- A taxa de arrefecimento após o recozimento é fundamental, uma vez que determina a microestrutura final e as propriedades do material. As taxas de arrefecimento lentas são geralmente utilizadas para obter um material macio e dúctil, enquanto as taxas de arrefecimento mais rápidas podem resultar em materiais mais duros e resistentes.
Ao compreender os diferentes tipos de recozimento e as suas aplicações específicas, os fabricantes podem selecionar o processo mais adequado para obter as propriedades desejadas dos materiais para os seus produtos.
Quadro de resumo:
Tipo de recozimento | Caraterísticas principais | Aplicações |
---|---|---|
Recozimento preto | O aquecimento num forno aberto forma uma camada de óxido negro | Normalmente utilizado para o aço |
Recozimento azul | Semelhante ao recozimento negro, mas a temperaturas mais baixas, forma uma camada de óxido azul | Frequentemente utilizado para aço inoxidável |
Recozimento em caixa | Aquecimento num recipiente fechado para evitar a oxidação | Adequado para materiais que requerem uma atmosfera controlada |
Recozimento brilhante | Realizado em atmosfera controlada ou vácuo para evitar a oxidação | Utilizado para aço inoxidável e metais não ferrosos |
Ciclo de recozimento | Ciclos repetidos de aquecimento e arrefecimento | Obtém propriedades específicas do material |
Recozimento por chama | Aquecimento por chama direta para recozimento localizado | Ideal para tratamento térmico localizado |
Recozimento total | Aquecimento acima da temperatura crítica superior, seguido de arrefecimento lento | Maximiza a suavidade e a ductilidade |
Grafitização | Converte a cementite em grafite no ferro fundido | Melhora a maquinabilidade e reduz a fragilidade do ferro fundido |
Recozimento intermédio | Efectuado entre as fases de trabalho a frio | Restaura a ductilidade e reduz a dureza |
Recozimento isotérmico | Mantida a uma temperatura específica até se obter a microestrutura desejada | Assegura uma microestrutura uniforme |
Processo de recozimento | Recozimento a baixa temperatura para aliviar tensões em materiais trabalhados a frio | Reduz as tensões internas sem alterar a microestrutura |
Recozimento de têmpera | Arrefecimento rápido após aquecimento | Utilizado em aços inoxidáveis para obter microestruturas específicas |
Esferoidização | Produz uma microestrutura esferoidal em aços com elevado teor de carbono | Melhora a maquinabilidade e reduz a fragilidade |
Precisa de ajuda para selecionar o processo de recozimento adequado para os seus materiais? Contacte os nossos especialistas hoje mesmo para soluções à medida!