Introdução à deposição de vapor de silício-carbono (VPD-SiC)
Vantagens do VPD-SiC
O VPD-SiC demonstra melhorias substanciais em relação aos materiais convencionais em várias áreas críticas, tornando-o uma escolha superior para aplicações avançadas de baterias. Em primeiro lugar, aeficiência da primeira volta do VPD-SiC é notavelmente mais elevada, o que se traduz em ciclos iniciais de carga-descarga mais eficazes e numa perda de energia reduzida. Esta melhoria é fundamental para a rápida implementação de baterias de elevado desempenho em várias indústrias.
Além disso, o VPD-SiC aumenta significativamente adensidade energética. Ao integrar partículas de silício numa matriz de carbono poroso, o material pode armazenar mais energia por unidade de volume ou massa, oferecendo tempos de funcionamento mais longos e frequências de carregamento reduzidas. Isto é particularmente vantajoso para a eletrónica portátil, veículos eléctricos e sistemas de armazenamento de energia renovável.
Odesempenho de ciclismo do VPD-SiC é também superior, com maior estabilidade ao longo de repetidos ciclos de carga-descarga. Esta durabilidade é crucial para a longevidade e fiabilidade dos sistemas de baterias, garantindo um desempenho consistente durante longos períodos sem degradação.
Além disso, o VPD-SiC atenua eficazmente aexpansão celular comum aos ânodos tradicionais à base de silício. Esta redução da expansão do volume durante os processos de carga e descarga ajuda a manter a integridade estrutural da bateria, aumentando assim a sua vida útil e segurança.
Em termos deredução de custoso VPD-SiC oferece um potencial de industrialização prometedor. O processo de síntese simplificado, combinado com a utilização eficiente das matérias-primas, pode conduzir a métodos de produção mais económicos. Este benefício económico é essencial para aumentar a produção e tornar as baterias de alto desempenho mais acessíveis.
Globalmente, as vantagens abrangentes do VPD-SiC em termos de eficiência na primeira volta, densidade energética, desempenho em ciclos, expansão celular e redução de custos fazem dele um material transformador para a próxima geração de tecnologias de baterias.
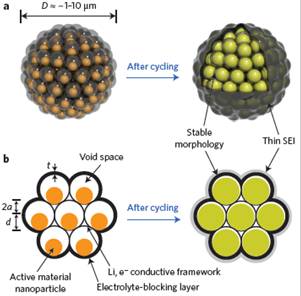
Principais etapas da tecnologia VPD-SiC
O processo de Deposição em Fase de Vapor (VPD) para a criação de materiais de ânodo de silício-carbono (SiC) é um procedimento em várias fases que integra vários passos críticos para obter soluções de armazenamento de energia de elevado desempenho. A tecnologia pode ser dividida em três fases principais: a preparação de um esqueleto de carbono poroso, a deposição de partículas de silício e a aplicação de um revestimento de camada de carbono.
-
Preparação do esqueleto de carbono poroso:
- A base do processo VPD-SiC, o esqueleto de carbono poroso, é meticulosamente trabalhado para fornecer uma estrutura robusta que melhora o desempenho geral do material. Esta etapa é essencial para criar uma estrutura com uma área de superfície específica elevada e uma excelente condutividade eléctrica, que são vitais para melhorar a capacidade do ânodo e a estabilidade do ciclo.
-
Deposição de partículas de silício:
- Uma vez estabelecido o esqueleto de carbono poroso, o próximo passo envolve a deposição de partículas de silício dentro dos poros. Isto é normalmente conseguido através da utilização de gás silano, que desempenha um papel fundamental na formação de silício dentro da matriz de carbono. O processo de deposição é altamente sensível a parâmetros como a temperatura e as taxas de fluxo de gás, que devem ser controlados com precisão para garantir uma distribuição uniforme das partículas e propriedades óptimas do material.
-
Revestimento da camada de carbono:
- A etapa final da tecnologia VPD-SiC é o revestimento do compósito silício-carbono com uma camada de carbono. Esta camada tem vários objectivos: protege as partículas de silício da degradação, melhora a condutividade eléctrica do material e proporciona estabilidade mecânica adicional. O revestimento de carbono é normalmente aplicado por deposição de vapor químico (CVD) ou outras técnicas semelhantes, assegurando uma camada uniforme e contínua que encapsula eficazmente as partículas de silício.
Cada uma destas etapas é interdependente e a sua integração bem sucedida é crucial para a produção de materiais de ânodo de silício-carbono de alta qualidade que satisfaçam as exigências rigorosas das aplicações modernas de armazenamento de energia.
Síntese de materiais de carbono poroso
Importância do carbono poroso
Os materiais de carbono poroso desempenham um papel fundamental na otimização dos ânodos de silício-carbono, melhorando significativamente o seu desempenho global. Esta melhoria é atribuída principalmente a várias propriedades-chave inerentes ao carbono poroso.
Em primeiro lugar, a elevada área de superfície específica do carbono poroso proporciona uma plataforma alargada para a deposição de partículas de silício. Esta grande área de superfície garante que as partículas de silício sejam distribuídas uniformemente, o que é crucial para manter a integridade estrutural e o desempenho do ânodo.
Em segundo lugar, a excelente condutividade eléctrica do carbono poroso facilita a transferência eficiente de electrões no interior do material do ânodo. Esta propriedade é vital para manter uma elevada eficiência energética e reduzir a resistência interna, que são essenciais para o desempenho a longo prazo e a durabilidade do ânodo.
Por último, a boa estabilidade mecânica do carbono poroso contribui para a resiliência estrutural do ânodo. Esta estabilidade é particularmente importante durante os repetidos ciclos de carga e descarga, uma vez que ajuda a atenuar as alterações de volume que as partículas de silício sofrem, evitando assim a degradação e prolongando a vida útil do ânodo.
Em resumo, a combinação de uma elevada área de superfície específica, excelente condutividade eléctrica e boa estabilidade mecânica torna os materiais de carbono poroso indispensáveis para o avanço dos ânodos de silício-carbono na tecnologia de baterias.
Considerações sobre a síntese
Ao sintetizar materiais de carbono poroso para ânodos de silício-carbono, vários factores críticos devem ser meticulosamente considerados para garantir um desempenho e uma escalabilidade ideais. A conceção da estrutura dos poros é fundamental, uma vez que influencia diretamente a capacidade do material para acomodar alterações de volume durante os ciclos de litiação e deslitiação. Uma estrutura de poros bem concebida pode aumentar significativamente a estabilidade do ânodo durante os ciclos e a retenção da capacidade.
A seleção do precursor é outro aspeto fundamental. A escolha do material precursor afecta não só as propriedades finais do carbono poroso, mas também a facilidade de síntese e o custo do material. Os precursores com elevado rendimento em carbono e baixo teor de cinzas são normalmente preferidos, uma vez que facilitam a formação de uma matriz de carbono uniforme e condutora. Além disso, o precursor deve ser compatível com técnicas de produção escaláveis para garantir a viabilidade do fabrico em grande escala.
A escalabilidade para a produção em grande escala é uma consideração não negociável. O processo de síntese deve ser adaptável a reactores de escala industrial, garantindo uma qualidade e um rendimento consistentes. Isto implica a otimização das condições de reação, como a temperatura, a pressão e as concentrações de reagentes, para conseguir uma deposição uniforme de partículas de silício no interior do carbono poroso. Além disso, o processo deve minimizar o consumo de energia e a geração de resíduos, alinhando-se com práticas de fabrico sustentáveis.
Em resumo, a síntese de materiais de carbono poroso para ânodos de silício-carbono requer uma abordagem holística, equilibrando a conceção da estrutura de poros, a seleção de precursores e a escalabilidade para satisfazer as exigências de desempenho e de aplicação industrial.
Silano e processo de deposição
Papel do gás silano
O gás silano (SiH₄) desempenha um papel fundamental na deposição de partículas de silício dentro da estrutura de carbono poroso, uma etapa crítica na fabricação de materiais de ânodo de silício-carbono. A eficácia deste processo depende da gestão cuidadosa das propriedades do silano e do intrincado equilíbrio dos parâmetros de deposição.
Um dos principais desafios na utilização do silano é a sua sensibilidade às condições ambientais. Por exemplo, a introdução de oxigénio na câmara de deposição pode levar à formação de SiOH, o que prejudica a qualidade da película de silício. Por outro lado, na ausência de oxigénio, é possível obter películas de silício amorfo, que são puras e adequadas para a deposição. Isto realça a necessidade de um controlo preciso do ambiente de deposição para evitar reacções químicas indesejadas.
Além disso, o custo e a disponibilidade do silano são factores significativos que influenciam a viabilidade da produção em grande escala. O material deve ser manuseado com cuidado devido à sua natureza reactiva, o que exige equipamento especializado e protocolos de segurança para mitigar os riscos. Além disso, o processo de deposição requer um equilíbrio delicado entre o silano e outros gases, como o oxigénio e o xénon, para obter o compósito silício-carbono desejado.
Para otimizar o processo de deposição, é essencial manter taxas médias de introdução de silano. O excesso de silano pode resultar na formação de SIH, enquanto que um excesso de oxigénio pode levar à formação de SiOH, sendo que ambos degradam a qualidade do produto final. Alcançar o equilíbrio correto é crucial para obter películas de silício amorfas e duras, o que melhora as caraterísticas de desempenho do ânodo.
Em resumo, o papel do gás silano no processo de deposição é multifacetado, exigindo uma compreensão profunda das suas propriedades químicas e uma gestão cuidadosa dos parâmetros de deposição para garantir a produção de materiais de ânodo de silício-carbono de alta qualidade.
Parâmetros do processo de deposição
Os parâmetros do processo de deposição desempenham um papel fundamental na determinação da qualidade e do desempenho dos materiais de ânodo de silício-carbono (Si-C). Os parâmetros-chave incluem a temperatura de deposição, as condições de reação e medidas de segurança rigorosas, cada uma das quais influencia significativamente as caraterísticas do produto final.
Influência da temperatura
A temperatura de deposição é um fator crítico que afecta diretamente a uniformidade e a densidade das partículas de silício na matriz de carbono poroso. Temperaturas mais altas podem aumentar a difusão do gás silano nos poros de carbono, levando a uma deposição mais uniforme. No entanto, temperaturas demasiado elevadas podem também causar a degradação térmica da estrutura de carbono, reduzindo a sua estabilidade mecânica e área de superfície específica. Por conseguinte, a otimização da temperatura de deposição é essencial para equilibrar estes efeitos concorrentes.
Condições de reação
As condições de reação, como os caudais de gás e a pressão, são igualmente importantes. Estas condições determinam o tempo de permanência dos reagentes na câmara de deposição e a taxa de formação de partículas de silício. Por exemplo, um caudal de gás mais elevado pode levar a tempos de permanência mais curtos, reduzindo potencialmente a uniformidade da deposição de silício. Inversamente, caudais mais baixos podem melhorar o processo de deposição, mas podem também aumentar o risco de entupimento ou outros problemas operacionais. Assim, é necessário um controlo preciso destas condições para obter propriedades ideais do material silício-carbono.
Medidas de segurança
Dada a natureza perigosa do gás silano, são indispensáveis medidas de segurança rigorosas durante o processo de deposição. Estas medidas incluem a utilização de sistemas avançados de deteção de gás, protocolos de paragem de emergência e sistemas de ventilação robustos para mitigar o risco de fugas ou explosões. A garantia de um ambiente de trabalho seguro não só protege o pessoal, como também assegura a fiabilidade e a consistência do processo de deposição, o que é crucial para a produção à escala industrial.
Em resumo, os parâmetros do processo de deposição - temperatura, condições de reação e medidas de segurança - estão intrinsecamente ligados ao desempenho e à qualidade dos materiais de ânodo silício-carbono. A otimização destes parâmetros é essencial para melhorar as propriedades electroquímicas do material e garantir a sua viabilidade para aplicações em grande escala.
Equipamento de deposição
Tipos de equipamento de deposição
Os fornos rotativos e os leitos fluidizados são os principais tipos de equipamento utilizados no processo de deposição de materiais de ânodo de silício-carbono. Cada tipo de equipamento oferece vantagens e desafios distintos, que são considerações cruciais para alcançar as propriedades ideais do material e a escalabilidade.
Fornos rotativos
- Simplicidade operacional: Os fornos rotativos são relativamente simples em termos de funcionamento, o que os torna a escolha preferida para experiências iniciais e produção em pequena escala.
- Custo-efetivo: São geralmente mais económicos em termos de investimento de capital e de custos operacionais, o que pode ser vantajoso para projectos à escala piloto.
- Flexibilidade: Os fornos rotativos oferecem flexibilidade no manuseamento de vários materiais precursores e podem ser adaptados a diferentes condições de deposição.
Leitos Fluidizados
- Uniformidade e eficiência: Os leitos fluidizados são conhecidos pela sua uniformidade superior na distribuição de partículas e taxas de utilização de gás silano mais elevadas. Isto resulta em propriedades de material mais consistentes e num melhor desempenho global.
- Medidas de segurança melhoradas: A utilização de leitos fluidizados requer protocolos de segurança rigorosos devido à elevada reatividade do gás silano. Os sistemas de segurança avançados e a monitorização contínua são essenciais para mitigar os riscos associados a fugas de gás e outros perigos.
- Complexidade e fiabilidade: Apesar das suas vantagens, os leitos fluidizados são mais complexos e requerem uma elevada fiabilidade para garantir um funcionamento contínuo e estável. Esta complexidade pode colocar desafios ao aumento da produção à escala industrial.
Em resumo, enquanto os fornos rotativos oferecem uma solução mais simples e mais económica, os leitos fluidizados oferecem uma maior uniformidade e eficiência, embora com maior complexidade e requisitos de segurança. A escolha do equipamento depende das necessidades específicas e da escala do processo de produção.
Desafios na industrialização
A produção em larga escala de materiais de ânodo de silício-carbono usando leitos fluidizados apresenta vários desafios significativos. Esses desafios giram principalmente em torno da garantia de operação contínua, da manutenção da uniformidade no processo de deposição e da obtenção de uma alta utilização de gás silano.
Um dos principais obstáculos é a necessidade deotimização do equipamento e do processo. Os leitos fluidizados, embora ofereçam uma uniformidade e uma utilização de silano superiores, requerem um controlo meticuloso de vários parâmetros, como a temperatura, os caudais de gás e a distribuição do tamanho das partículas. Qualquer desvio destas condições ideais pode levar a propriedades inconsistentes do material, que são prejudiciais para o desempenho geral do ânodo.
Além disso, afiabilidade e segurança do sistema de leito fluidizado são fundamentais. A utilização de gás silano, que é altamente reativo e potencialmente explosivo, necessita de medidas de segurança robustas e de monitorização contínua. Isto acrescenta uma camada de complexidade ao processo de industrialização, exigindo sistemas avançados de automação e controlo para garantir um funcionamento seguro e eficiente.
Além disso, aescalabilidade do processo de leito fluidizado é uma preocupação significativa. A transição de experiências à escala laboratorial para a produção industrial à escala real exige uma análise cuidadosa da forma de manter o mesmo nível de controlo e uniformidade em volumes maiores. Isso geralmente envolve um investimento de capital significativo em atualizações de equipamentos e melhorias no processo.
Em resumo, embora os leitos fluidizados ofereçam vantagens promissoras para a produção de ânodos de silício-carbono, a sua industrialização requer a superação de desafios técnicos e operacionais substanciais. Estes incluem a otimização do equipamento e do processo, garantindo a fiabilidade e a segurança, e a resolução de problemas de escalabilidade para alcançar uma produção contínua e em grande escala.
CONTACTE-NOS PARA UMA CONSULTA GRATUITA
Os produtos e serviços da KINTEK LAB SOLUTION foram reconhecidos por clientes de todo o mundo. A nossa equipa terá todo o prazer em ajudar com qualquer questão que possa ter. Contacte-nos para uma consulta gratuita e fale com um especialista de produto para encontrar a solução mais adequada para as suas necessidades de aplicação!