Uma atmosfera inerte é utilizada no fabrico de ligas para evitar reacções químicas indesejadas, como a oxidação ou a contaminação, durante processos como o tratamento térmico, a sinterização ou a prensagem isostática a quente. Ao criar um ambiente controlado com gases como o árgon ou o azoto, os fabricantes podem garantir que a liga mantém as propriedades desejadas, como a resistência, a durabilidade e a qualidade da superfície. Isto é especialmente crítico em indústrias como a aeroespacial, automóvel e petroquímica, onde a integridade do material é fundamental. A atmosfera inerte também reduz riscos como incêndios, explosões e contaminação, garantindo processos de produção mais seguros e eficientes.
Pontos-chave explicados:
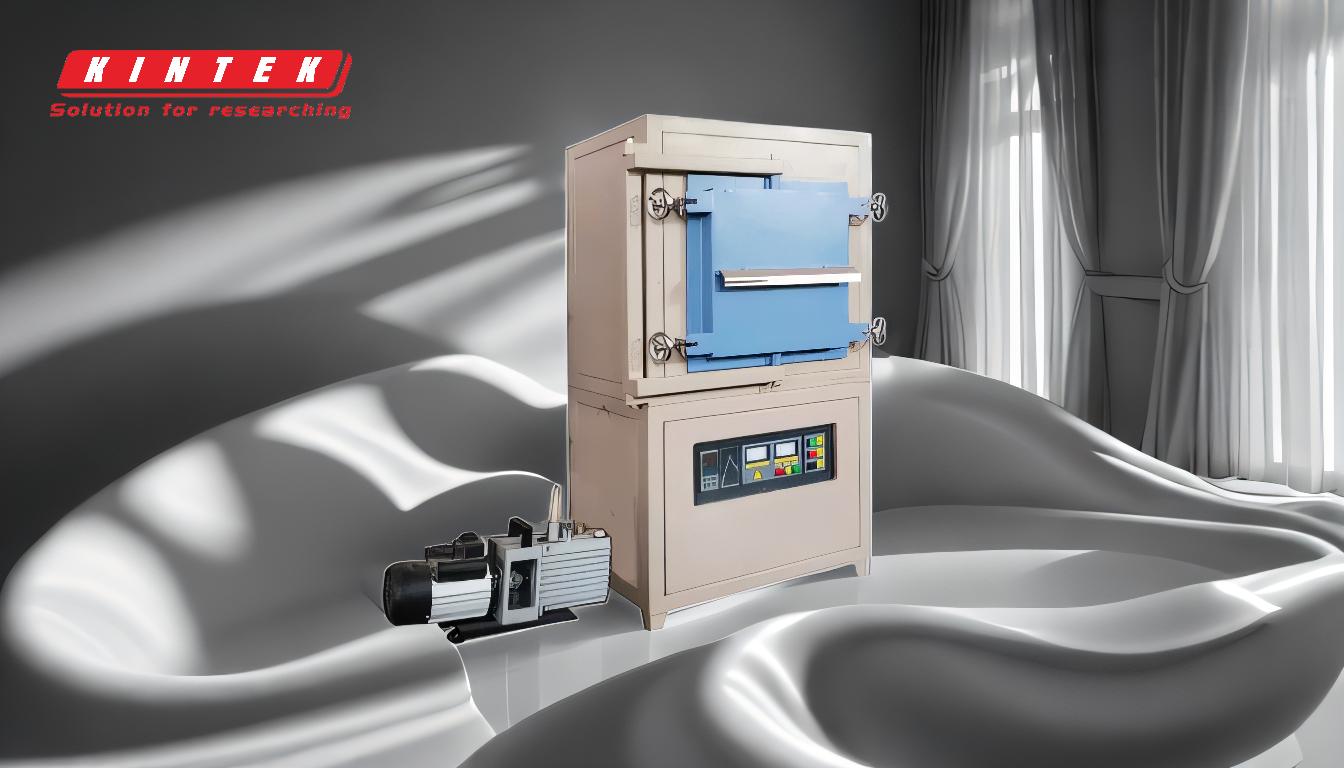
-
Prevenção da oxidação e da contaminação
- A oxidação ocorre quando os metais reagem com o oxigénio do ar, formando óxidos que podem degradar a superfície e as propriedades mecânicas da liga.
- Uma atmosfera inerte, normalmente criada com gases como o árgon ou o azoto, desloca o oxigénio e outros gases reactivos, evitando a oxidação e a contaminação.
- Isto assegura que a liga mantém a composição química e a qualidade da superfície pretendidas, o que é fundamental para aplicações que exigem elevada precisão e durabilidade.
-
Manutenção das propriedades dos materiais
- Durante os processos de tratamento térmico, como a sinterização, o recozimento brilhante ou a carbonitretação, a microestrutura da liga e as propriedades mecânicas são cuidadosamente controladas.
- Uma atmosfera inerte assegura que estes processos ocorrem sem interferência de factores externos, preservando a resistência, a dureza e outras propriedades críticas da liga.
- Por exemplo, na indústria aeroespacial ou automóvel, mesmo pequenos desvios nas propriedades dos materiais podem conduzir a falhas catastróficas.
-
Controlo de processos melhorado
- Uma atmosfera inerte proporciona um ambiente altamente controlado, reduzindo a variabilidade no processo de fabrico.
- Isto é particularmente importante em processos como a prensagem isostática a quente (HIP) ou operações de vácuo, em que é necessário um controlo preciso da temperatura, pressão e composição do gás.
- Ao minimizar as reacções indesejadas, os fabricantes podem obter resultados consistentes e reduzir o desperdício.
-
Segurança e redução de riscos
- As atmosferas inertes reduzem o risco de incêndios e explosões, especialmente quando se trabalha com metais reactivos ou processos de alta temperatura.
- Ao deslocar o oxigénio, a probabilidade de combustão é significativamente reduzida, criando um ambiente de trabalho mais seguro.
- Isto é particularmente importante em indústrias como a petroquímica, onde a segurança é uma prioridade máxima.
-
Aplicações em sectores críticos
- Indústrias como a aeroespacial, a automóvel e a petroquímica dependem de atmosferas inertes para produzir ligas de alta qualidade com especificações precisas.
- Por exemplo, no sector aeroespacial, as ligas têm de suportar condições extremas e qualquer contaminação ou oxidação pode comprometer o seu desempenho.
- Do mesmo modo, no fabrico de automóveis, componentes como peças de motor ou sistemas de transmissão requerem materiais com propriedades consistentes para garantir fiabilidade e longevidade.
-
Benefícios em termos de custos e eficiência
- Embora a criação de uma atmosfera inerte possa implicar custos adicionais, os benefícios a longo prazo ultrapassam frequentemente o investimento inicial.
- Ao reduzir a oxidação e a contaminação, os fabricantes podem minimizar o desperdício de material e o retrabalho, o que conduz a poupanças de custos.
- Além disso, a consistência e a qualidade melhoradas das ligas podem aumentar a eficiência global do processo de fabrico.
Em resumo, uma atmosfera inerte é essencial no fabrico de ligas para evitar a oxidação, manter as propriedades do material, assegurar o controlo do processo, aumentar a segurança e cumprir os requisitos rigorosos das indústrias críticas. Ao utilizar gases inertes, como o árgon ou o azoto, os fabricantes podem produzir ligas de alta qualidade com um desempenho consistente, o que o torna um componente vital dos processos industriais modernos.
Quadro de resumo:
Principais benefícios da atmosfera inerte | Detalhes |
---|---|
Evita a oxidação e a contaminação | Utiliza gases como o árgon ou o azoto para deslocar o oxigénio, assegurando a integridade da liga. |
Mantém as propriedades do material | Preserva a resistência, a dureza e a durabilidade durante os processos de tratamento térmico. |
Melhora o controlo do processo | Reduz a variabilidade, garantindo resultados consistentes em processos como HIP ou sinterização. |
Melhora a segurança | Reduz o risco de incêndios e explosões ao deslocar o oxigénio em processos a altas temperaturas. |
Aplicações industriais críticas | Essencial para o fabrico aeroespacial, automóvel e petroquímico. |
Benefícios em termos de custos e eficiência | Reduz o desperdício e o retrabalho, melhorando a eficiência do fabrico a longo prazo. |
Saiba como uma atmosfera inerte pode otimizar o seu processo de fabrico de ligas contacte os nossos especialistas hoje mesmo !