Para obter componentes sinterizados consistentes e satisfatórios, devem ser cumpridas várias condições críticas.Estas incluem o controlo preciso da temperatura de sinterização, o tamanho e a distribuição adequados das partículas do pó, uma pressão de compactação uniforme e uma atmosfera adequada durante a sinterização.Cada um destes factores desempenha um papel vital na garantia da densidade, resistência e precisão dimensional do produto final.Para além disso, a escolha do método de sinterização, quer se trate de sinterização em estado sólido, sinterização em fase líquida ou sinterização assistida por pressão, deve estar alinhada com as propriedades do material e os resultados desejados.Compreender e otimizar estas condições é essencial para obter componentes sinterizados de alta qualidade em aplicações industriais.
Pontos-chave explicados:
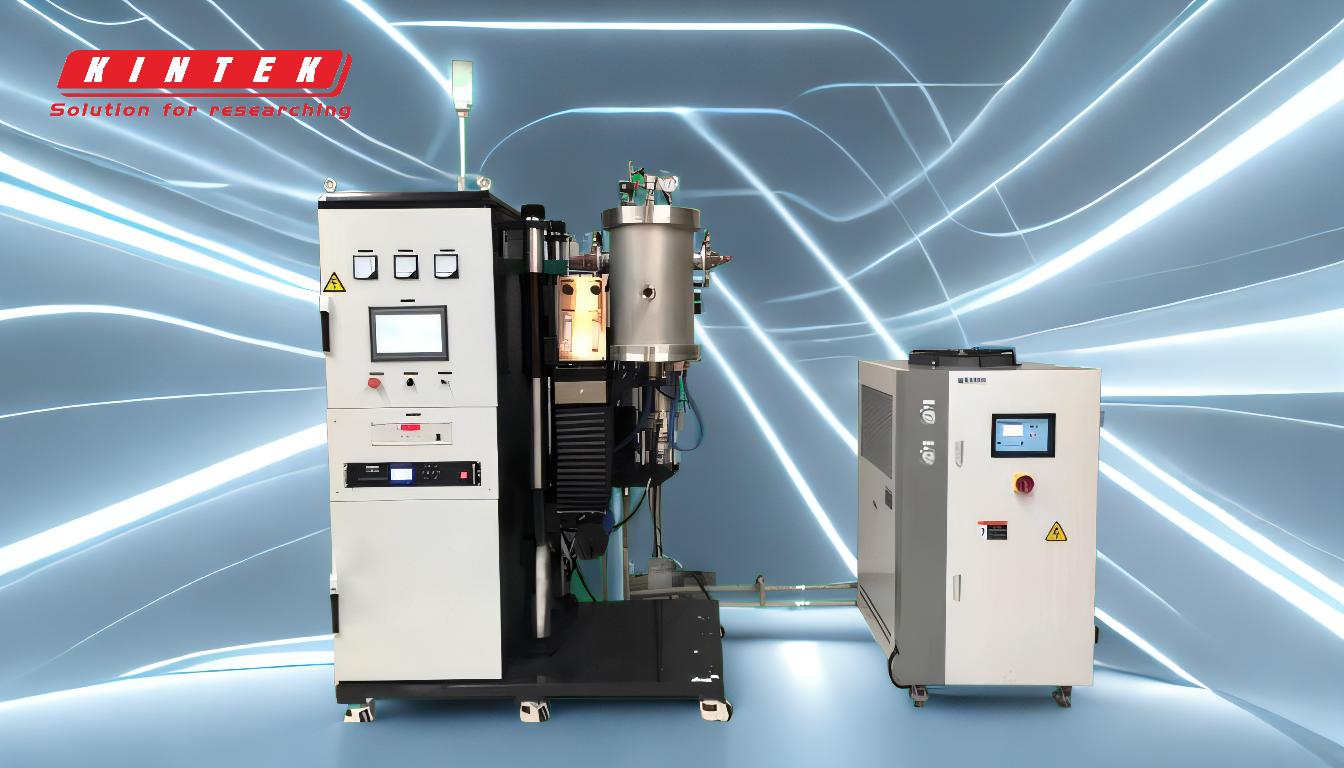
-
Controlo da temperatura de sinterização:
- A temperatura de sinterização é um parâmetro crítico que afecta diretamente a densificação e a microestrutura do produto final.
- Uma temperatura demasiado baixa pode resultar numa ligação insuficiente entre as partículas, dando origem a componentes fracos e porosos.
- Uma temperatura demasiado elevada pode provocar um crescimento excessivo do grão ou a fusão, comprometendo as propriedades mecânicas do material.
- O controlo preciso da temperatura assegura uma difusão e ligação óptimas entre as partículas, resultando em componentes sinterizados consistentes e satisfatórios.
-
Tamanho e distribuição das partículas:
- O tamanho e a distribuição das partículas de pó influenciam significativamente o processo de sinterização.
- As partículas finas com uma distribuição de tamanho estreita promovem um melhor empacotamento e densificação durante a sinterização.
- Partículas irregulares ou grossas podem levar a uma densificação desigual e a defeitos no produto final.
- A preparação adequada do pó, incluindo a moagem e a peneiração, garante um tamanho e uma distribuição uniformes das partículas, o que é essencial para obter componentes sinterizados de alta qualidade.
-
Pressão de compactação uniforme:
- A pressão de compactação aplicada durante a formação do corpo verde afecta a densidade e a uniformidade da peça sinterizada.
- Uma pressão inconsistente pode levar a variações na densidade, causando deformações ou fissuras durante a sinterização.
- A compactação uniforme assegura um empacotamento homogéneo das partículas, reduzindo o risco de defeitos e melhorando as propriedades mecânicas do componente sinterizado.
-
Atmosfera de sinterização adequada:
- A atmosfera durante a sinterização desempenha um papel crucial na prevenção da oxidação, na redução das impurezas e no controlo das reacções químicas.
- As atmosferas de sinterização comuns incluem gases inertes (por exemplo, árgon ou azoto), gases redutores (por exemplo, hidrogénio) ou ambientes de vácuo.
- A escolha da atmosfera depende do material que está a ser sinterizado e das propriedades desejadas do produto final.
- Uma atmosfera adequada assegura a integridade e a qualidade do componente sinterizado, minimizando a contaminação e as reacções indesejadas.
-
Escolha do método de sinterização:
- Diferentes métodos de sinterização são adequados para vários materiais e aplicações.
- Sinterização em estado sólido baseia-se na difusão atómica para unir as partículas sem derreter, ideal para cerâmicas e alguns metais.
- Sinterização em fase líquida envolve uma fase líquida que ajuda na densificação, normalmente utilizada para materiais com baixos pontos de fusão.
- Sinterização assistida por pressão (por exemplo, prensagem a quente ou sinterização por plasma de faísca) aplica pressão externa para aumentar a densificação, adequada para materiais de elevado desempenho.
- A seleção do método de sinterização adequado com base nas propriedades do material e nos requisitos da aplicação é essencial para obter resultados consistentes e satisfatórios.
-
Tratamentos pós-sinterização:
- Os tratamentos pós-sinterização, como o recozimento ou o acabamento da superfície, podem melhorar ainda mais as propriedades do componente sinterizado.
- O recozimento alivia as tensões internas e melhora a ductilidade, enquanto os tratamentos de superfície (por exemplo, polimento ou revestimento) melhoram a resistência ao desgaste e a estética.
- Estes tratamentos garantem que o produto final cumpre as especificações e os critérios de desempenho desejados.
Ao controlar cuidadosamente estas condições e otimizar o processo de sinterização, os fabricantes podem produzir componentes sinterizados consistentes e de alta qualidade que satisfazem os requisitos rigorosos de várias indústrias.
Tabela de resumo:
Condição | Importância |
---|---|
Temperatura de sinterização | Assegura uma difusão e ligação óptimas; evita componentes fracos ou porosos. |
Tamanho e distribuição das partículas | Promove uma densificação uniforme; reduz os defeitos no produto final. |
Pressão de compactação uniforme | Assegura um empacotamento uniforme das partículas; minimiza a deformação ou fissuração. |
Atmosfera de sinterização | Evita a oxidação, reduz as impurezas e controla as reacções químicas. |
Método de sinterização | Alinha-se com as propriedades do material e os resultados desejados para obter resultados consistentes. |
Tratamentos pós-sinterização | Melhora propriedades como ductilidade, resistência ao desgaste e estética. |
Obtenha componentes sinterizados consistentes e de alta qualidade- contacte hoje os nossos especialistas para obter soluções à medida!