O endurecimento por recozimento, um processo crítico na metalurgia, envolve o aquecimento de materiais a temperaturas específicas para alterar as suas propriedades físicas e, por vezes, químicas, seguido de um arrefecimento controlado.A gama de temperaturas para o endurecimento por recozimento varia significativamente consoante o material que está a ser tratado, normalmente entre 500°C e 1200°C.Por exemplo, o aço é frequentemente recozido a temperaturas entre 700°C e 900°C, enquanto as ligas de alumínio podem necessitar de temperaturas mais baixas, à volta de 300°C a 500°C.O processo tem como objetivo reduzir a dureza, aumentar a ductilidade e eliminar as tensões internas, tornando o material mais trabalhável e menos propenso a fissuras.Compreender a gama de temperaturas exacta para um material específico é crucial para alcançar as propriedades mecânicas desejadas e garantir o desempenho do material na aplicação pretendida.
Pontos-chave explicados:
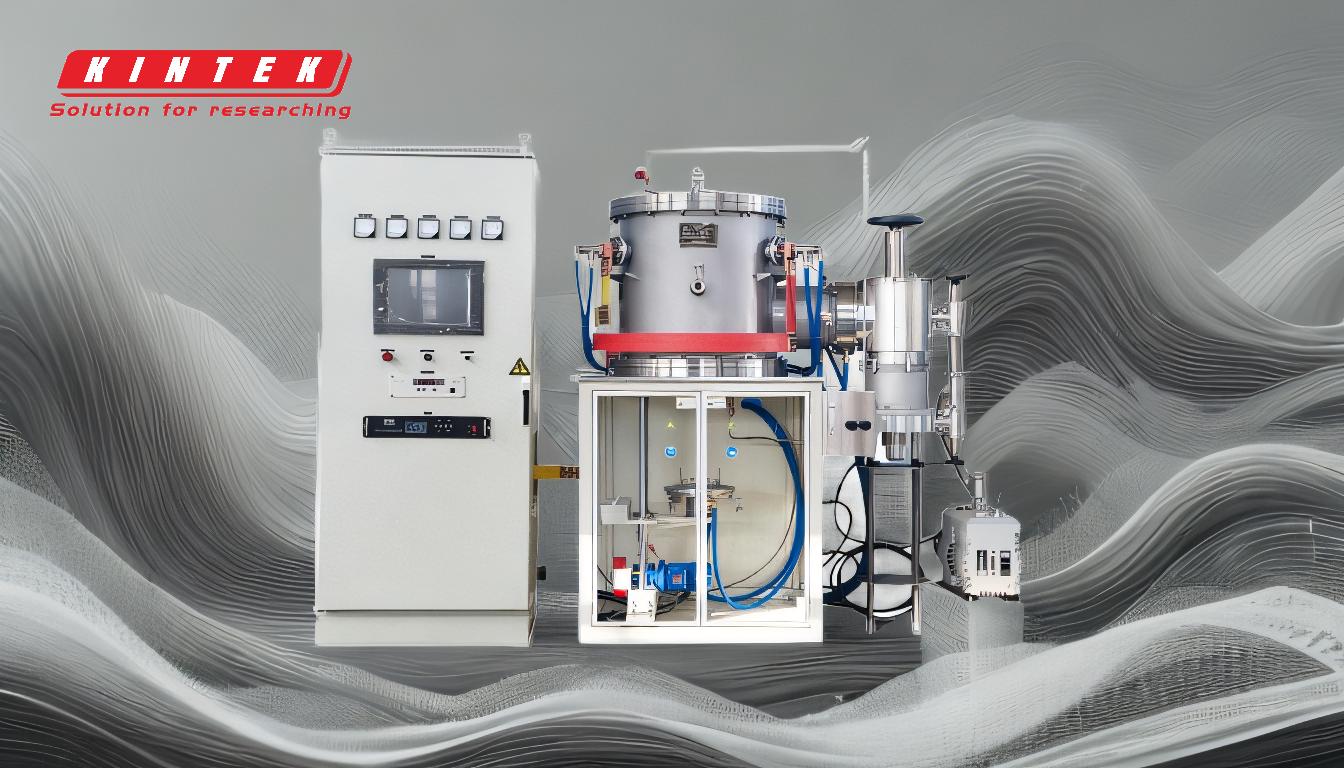
-
Definição e objetivo do recozimento Endurecimento:
- Definição: O endurecimento por recozimento é um processo de tratamento térmico em que um material é aquecido a uma temperatura específica, mantido a essa temperatura durante um período de tempo e, em seguida, arrefecido a uma velocidade controlada.
- Objetivo: Os principais objectivos são reduzir a dureza, aumentar a ductilidade e aliviar as tensões internas do material.Isto torna o material mais fácil de maquinar, formar ou soldar.
-
Variabilidade da gama de temperaturas:
- Dependência do material: A gama de temperaturas para o endurecimento por recozimento depende muito do tipo de material que está a ser tratado.Diferentes materiais têm diferentes temperaturas críticas nas quais a sua microestrutura se altera.
- Aço: Para o aço, a temperatura de recozimento varia normalmente entre 700°C e 900°C.Esta gama permite a transformação da microestrutura, o que pode alterar significativamente as propriedades do material.
- Ligas de alumínio: O alumínio e as suas ligas requerem geralmente temperaturas de recozimento mais baixas, normalmente entre 300°C e 500°C.Isto deve-se ao facto de o alumínio ter um ponto de fusão mais baixo do que o aço.
- Outros metais: Outros metais, como o cobre, o latão e o titânio, têm os seus próprios intervalos de temperatura de recozimento específicos, que devem ser respeitados para obter resultados óptimos.
-
Importância do arrefecimento controlado:
- Taxa de arrefecimento: Depois de atingir a temperatura de recozimento, o material deve ser arrefecido a uma velocidade controlada.O arrefecimento rápido pode levar à formação de microestruturas indesejáveis, enquanto o arrefecimento lento ajuda a obter as propriedades desejadas.
- Métodos de arrefecimento: Os métodos de arrefecimento comuns incluem o arrefecimento em forno, o arrefecimento a ar e o arrefecimento em atmosfera controlada, cada um escolhido com base no material e no resultado pretendido.
-
Impacto nas propriedades do material:
- Dureza e ductilidade: O recozimento adequado reduz a dureza do material, tornando-o mais dúctil e mais fácil de trabalhar.Isto é particularmente importante nos processos de fabrico em que o material tem de ser moldado ou formado.
- Alívio de tensões: O recozimento ajuda a aliviar as tensões internas que podem ter sido introduzidas durante processos de fabrico anteriores, como a maquinagem ou a soldadura.Isto reduz o risco de falha do material sob tensão.
- Estrutura do grão: O processo também afecta a estrutura do grão do material, conduzindo a uma microestrutura mais uniforme e refinada, o que melhora o desempenho geral do material.
-
Considerações práticas para os compradores de equipamentos e consumíveis:
- Seleção do equipamento de recozimento: Os compradores devem considerar os requisitos específicos de temperatura dos materiais que irão processar.Isto inclui a seleção de fornos que possam atingir e manter as temperaturas necessárias com precisão.
- Eficiência energética: Dadas as elevadas temperaturas envolvidas, os fornos energeticamente eficientes podem conduzir a poupanças de custos significativas ao longo do tempo.
- Segurança e conformidade: Assegurar que o equipamento cumpre as normas de segurança e os requisitos regulamentares é crucial, especialmente quando se trata de processos a altas temperaturas.
- Manutenção e durabilidade: A durabilidade do equipamento e a facilidade de manutenção são factores importantes, uma vez que as reparações ou substituições frequentes podem ser dispendiosas e perturbar a produção.
-
Conclusão:
- Precisão e Controlo: O sucesso do processo de endurecimento por recozimento depende em grande medida do controlo preciso da temperatura e das taxas de arrefecimento adequadas.Compreender as necessidades específicas do material a ser tratado é essencial para alcançar as propriedades desejadas.
- Eficiência económica e operacional: Para os compradores de equipamento e consumíveis, investir no equipamento de recozimento correto e compreender as nuances do processo pode levar a um melhor desempenho do material, a custos reduzidos e a uma maior eficiência operacional.
Em resumo, a gama de temperaturas para o endurecimento por recozimento é um parâmetro crítico que varia muito consoante o material.O controlo adequado desta gama, juntamente com o arrefecimento controlado, é essencial para alcançar as propriedades desejadas do material.Para os compradores, a seleção do equipamento correto e a compreensão das complexidades do processo são fundamentais para garantir resultados bem sucedidos no tratamento de materiais.
Tabela de resumo:
Material | Gama de temperaturas de recozimento | Objetivo principal |
---|---|---|
Aço | 700°C - 900°C | Reduzir a dureza, aumentar a ductilidade |
Ligas de alumínio | 300°C - 500°C | Ponto de fusão mais baixo, alívio de tensões |
Cobre | 400°C - 700°C | Melhorar a trabalhabilidade, afinar a estrutura do grão |
Titânio | 700°C - 900°C | Aumentar a resistência, aliviar as tensões internas |
Assegurar um desempenho ótimo do material com um endurecimento por recozimento preciso contacte hoje os nossos especialistas para obter soluções à medida!