Os gases de proteção desempenham um papel fundamental nos processos de brasagem, evitando a oxidação e assegurando um acabamento limpo e de alta qualidade. A escolha do gás de proteção depende do método de brasagem e dos materiais envolvidos. Os gases de proteção comuns incluem o hidrogénio, o amoníaco dissociado e o azoto. Na brasagem a vácuo, o oxigénio é totalmente removido, enquanto a brasagem com proteção gasosa depende do azoto e do fluxo para obter resultados semelhantes. A seleção de materiais, como as ligas que contêm magnésio para a brasagem em vácuo ou as ligas dependentes de fluxo para a brasagem com proteção gasosa, influencia ainda mais a eficácia do gás de proteção. A compreensão destes factores é essencial para otimizar os resultados da brasagem.
Pontos-chave explicados:
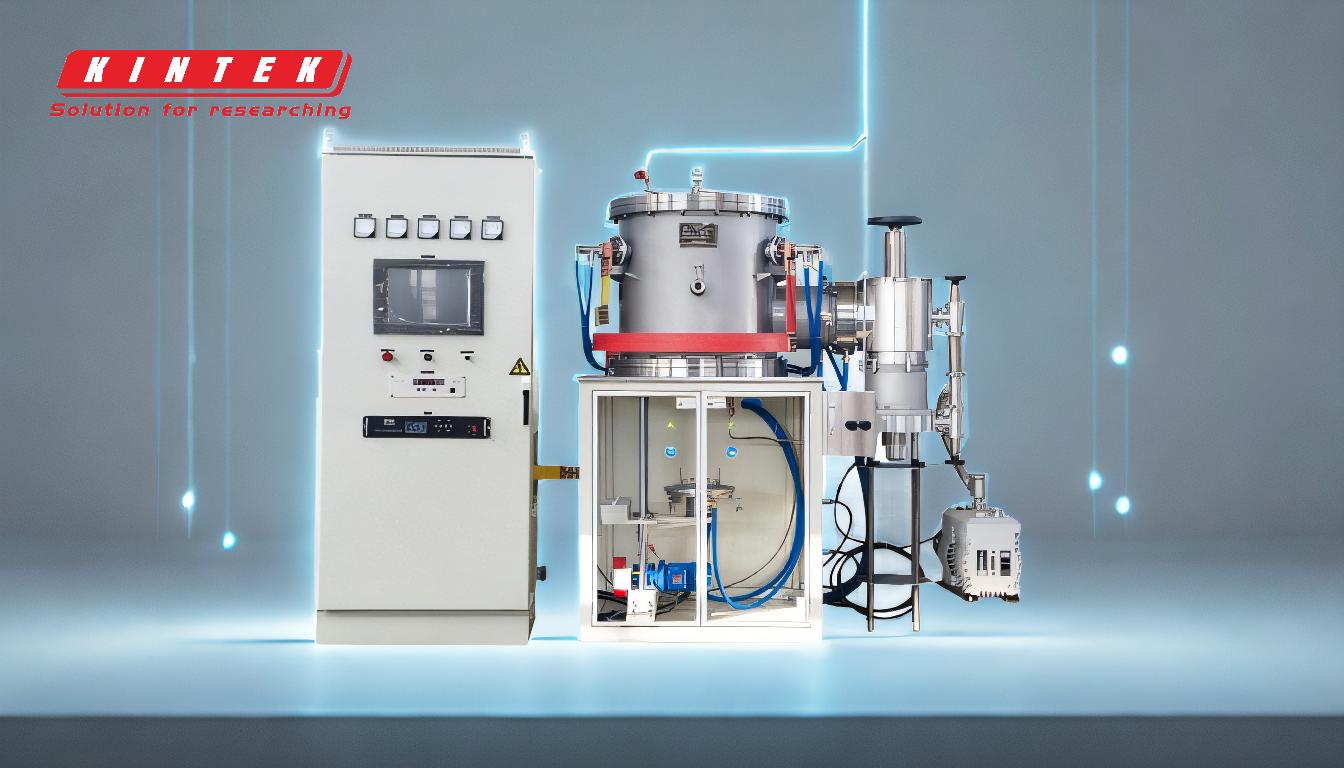
-
Finalidade dos gases de proteção na brasagem
- Os gases de proteção são utilizados para criar uma atmosfera inerte que evita a oxidação, a incrustação e a acumulação de carbono (fuligem) durante a brasagem.
- Asseguram um acabamento limpo e brilhante na peça de trabalho, o que é fundamental para obter juntas soldadas de alta qualidade.
-
Gases de proteção comuns
- Hidrogénio: Frequentemente utilizado na brasagem devido à sua capacidade de reduzir os óxidos e criar uma superfície limpa.
- Amoníaco desassociado: Mistura de hidrogénio e azoto, normalmente utilizada pela sua relação custo-eficácia e capacidade de evitar a oxidação.
- Nitrogénio: Frequentemente utilizado na brasagem com proteção gasosa para proteger a peça de trabalho da oxidação.
-
Brasagem a vácuo vs. brasagem com proteção gasosa
-
Brasagem a vácuo:
- Envolve a evacuação do forno para remover o oxigénio e outros gases reactivos.
- Não necessita de fluxo, uma vez que o ambiente de vácuo elimina o risco de oxidação.
- Utiliza materiais como o composto duplo 4104/****/4104, que contém 1,5% de magnésio para romper a camada de AL203 na superfície da peça de trabalho.
-
Brasagem com proteção gasosa:
- Baseia-se no azoto como gás de proteção para proteger a peça de trabalho.
- Requer a aplicação de fluxo para quebrar a camada de AL203, uma vez que os materiais utilizados (por exemplo, composto duplo 4343/****/4343) não contêm magnésio.
-
Brasagem a vácuo:
-
Considerações sobre o material
- Ligas que contêm magnésio (por exemplo, 4104/****/4104): Utilizado na brasagem a vácuo, o magnésio ajuda a romper a camada de AL203, assegurando uma ligação correta.
- Ligas que não sejam de magnésio (por exemplo, 4343/****/4343): Utilizados na brasagem com proteção gasosa, estes materiais dependem do fluxo para obter o mesmo efeito.
-
Diferenças de processo
-
Brasagem a vácuo:
- Implica uma fase de isolamento mais longa (cerca de 4 horas por forno) para garantir uma distribuição uniforme da temperatura.
- Não é necessário qualquer processo de arrefecimento após a brasagem.
-
Brasagem com proteção gasosa:
- Funciona continuamente a uma velocidade de 350 mm/min.
- Não requer um processo de vácuo ou de arrefecimento, tornando-o mais rápido e eficiente para determinadas aplicações.
-
Brasagem a vácuo:
-
Vantagens dos gases de proteção
- Melhoria da qualidade das articulações: Os gases de proteção evitam a oxidação, conduzindo a juntas soldadas mais fortes e mais fiáveis.
- Estética melhorada: A utilização de gases inertes permite obter um acabamento limpo e brilhante da peça a trabalhar.
- Versatilidade: Diferentes gases e métodos (vácuo vs. gás blindado) permitem flexibilidade na abordagem de vários desafios de brasagem.
-
Factores que influenciam a seleção do gás
- Tipo de material: A escolha do gás de proteção depende da liga a ser soldada e dos seus requisitos específicos (por exemplo, teor de magnésio).
- Método de brasagem: A brasagem a vácuo e a brasagem com proteção de gás têm requisitos de gás distintos.
- Custo e eficiência: O amoníaco desassociado é frequentemente escolhido pela sua relação custo-eficácia, enquanto o azoto é preferido pela sua disponibilidade e facilidade de utilização na brasagem com proteção gasosa.
Ao compreender o papel dos gases de proteção e a sua aplicação em diferentes processos de brasagem, os fabricantes podem otimizar as suas operações para obter resultados superiores. A escolha do gás, do material e do método deve estar alinhada com os requisitos específicos da peça de trabalho e com o resultado desejado.
Quadro de resumo:
Aspeto | Brasagem a vácuo | Brasagem com proteção gasosa |
---|---|---|
Gás de proteção | O oxigénio é totalmente removido; não é necessário gás de proteção | Nitrogénio utilizado como gás de proteção |
Necessidade de fluxo | Não é necessário fluxo | Fluxo necessário para quebrar a camada de AL203 |
Material utilizado | Ligas que contenham magnésio (por exemplo, 4104/****/4104) | Ligas que não sejam de magnésio (por exemplo, 4343/****/4343) |
Duração do processo | Fase de isolamento mais longa (~4 horas por forno) | Funcionamento contínuo a 350 mm/min |
Processo de arrefecimento | Não é necessário arrefecimento | Não é necessário arrefecimento |
Vantagens | Juntas limpas e sem oxidação; sem resíduos de fluxo | Mais rápido e mais eficiente para determinadas aplicações |
Pronto para otimizar o seu processo de brasagem? Contacte os nossos especialistas hoje mesmo para soluções à medida!