O processo de Deposição Física em Vapor (PVD) é um método sofisticado utilizado para depositar películas finas de material num substrato.Envolve a transformação de um material sólido numa fase de vapor, que é depois depositado num substrato para formar um revestimento fino e uniforme.O processo é normalmente efectuado num ambiente de vácuo para garantir a pureza e o controlo da deposição.O PVD é amplamente utilizado em várias indústrias para aplicações como a melhoria da resistência ao desgaste, o aumento da resistência à corrosão e o fornecimento de acabamentos decorativos.O processo envolve várias etapas importantes, incluindo a vaporização do material de revestimento, a migração das partículas vaporizadas e a deposição no substrato.
Pontos-chave explicados:
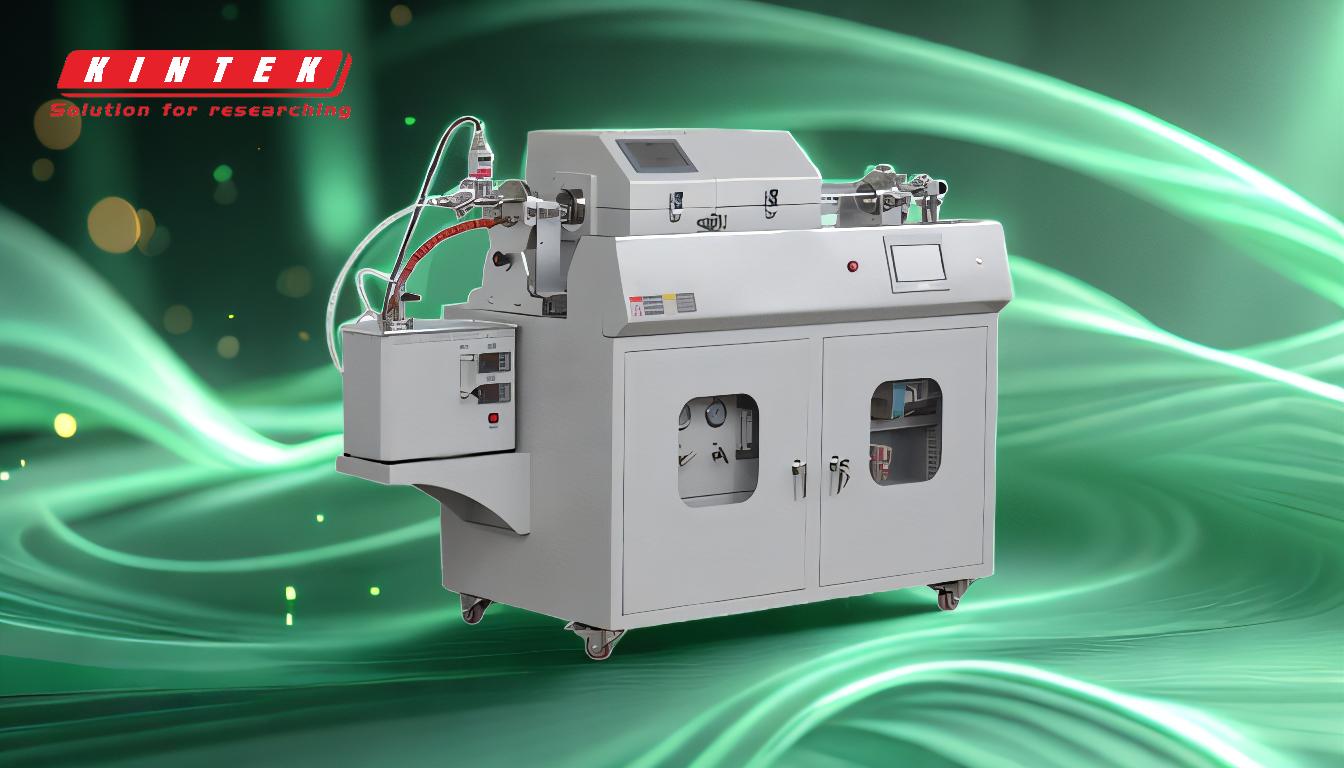
-
Vaporização do material de revestimento:
- O primeiro passo no processo PVD é a vaporização do material de revestimento.Isto pode ser conseguido através de vários métodos, incluindo evaporação, pulverização catódica ou ablação por laser.
- Evaporação:O material é aquecido a uma temperatura elevada até se vaporizar.Isto é frequentemente feito utilizando um feixe de electrões ou aquecimento resistivo.
- Sputtering:Os iões de alta energia são utilizados para bombardear o material alvo, fazendo com que os átomos sejam ejectados da superfície e entrem na fase de vapor.
- Ablação por laser:É utilizado um laser de alta potência para vaporizar diretamente o material.
-
Migração de partículas vaporizadas:
- Quando o material se encontra na fase de vapor, as partículas (átomos, moléculas ou iões) migram através da câmara de vácuo.Esta migração é influenciada pelo ambiente de vácuo, que minimiza as colisões com outras partículas e assegura uma deposição limpa.
- Durante esta fase, as partículas vaporizadas podem sofrer reacções, especialmente se forem introduzidos gases reactivos (como o azoto ou o oxigénio) na câmara.Estas reacções podem formar compostos que são depois depositados no substrato.
-
Deposição no substrato:
- O passo final é a deposição do material vaporizado no substrato.Isto ocorre quando as partículas vaporizadas se condensam na superfície mais fria do substrato, formando uma película fina e uniforme.
- O substrato é normalmente mantido a uma temperatura mais baixa em comparação com o material vaporizado, o que promove a condensação e a adesão do revestimento.
- A espessura da película depositada pode ser controlada com precisão utilizando técnicas como a monitorização da taxa de cristais de quartzo, que mede a taxa de deposição e a ajusta conforme necessário.
-
Utilização de Plasma e Gases Reactivos:
- Em muitos processos de PVD, o plasma é utilizado para melhorar o processo de vaporização e deposição.O plasma é criado através da ionização de um gás, utilizando frequentemente uma fonte de plasma indutivamente acoplado (ICP).
- O plasma de alta energia pode ajudar a dissociar as moléculas de gás em espécies reactivas, que podem depois reagir com o material vaporizado para formar compostos.Isto é particularmente útil para criar revestimentos duros e resistentes ao desgaste, como o nitreto de titânio (TiN) ou o nitreto de crómio (CrN).
- A introdução de gases reactivos (por exemplo, azoto, oxigénio) permite a formação de revestimentos compostos, que podem ter propriedades superiores aos revestimentos de metal puro.
-
Ambiente de vácuo:
-
Todo o processo PVD é realizado num ambiente de alto vácuo.Isto é crucial por várias razões:
- Pureza:O vácuo minimiza a presença de contaminantes, garantindo uma deposição limpa.
- Controlo:A baixa pressão permite um controlo preciso do processo de deposição, incluindo a velocidade e a uniformidade do revestimento.
- Controlo da reação:O ambiente de vácuo ajuda a controlar as reacções entre o material vaporizado e quaisquer gases reactivos, assegurando propriedades de revestimento consistentes.
-
Todo o processo PVD é realizado num ambiente de alto vácuo.Isto é crucial por várias razões:
-
Aplicações dos revestimentos PVD:
-
Os revestimentos PVD são utilizados numa vasta gama de aplicações, incluindo:
- Resistência ao desgaste:Os revestimentos como TiN e CrN são utilizados para melhorar a resistência ao desgaste de ferramentas de corte, moldes e outros componentes.
- Resistência à corrosão:Os revestimentos PVD podem constituir uma barreira contra a corrosão, prolongando a vida útil dos componentes expostos a ambientes agressivos.
- Acabamentos decorativos:O PVD é utilizado para criar revestimentos decorativos com uma vasta gama de cores e acabamentos, frequentemente vistos em produtos electrónicos de consumo e jóias.
- Revestimentos ópticos:A PVD é utilizada para depositar películas finas com propriedades ópticas específicas, tais como revestimentos antirreflexo em lentes.
-
Os revestimentos PVD são utilizados numa vasta gama de aplicações, incluindo:
Em resumo, o processo PVD é um método altamente controlado e versátil para depositar películas finas de material num substrato.Envolve a vaporização do material de revestimento, a migração das partículas vaporizadas e a deposição no substrato, tudo isto realizado num ambiente de vácuo.A utilização de plasma e gases reactivos permite a criação de revestimentos compostos com propriedades melhoradas, tornando a PVD uma técnica valiosa em várias aplicações industriais.
Tabela de resumo:
Etapas principais | Descrição |
---|---|
Vaporização | O material de revestimento é vaporizado por evaporação, pulverização catódica ou ablação a laser. |
Migração | As partículas vaporizadas movem-se através de um vácuo, minimizando as colisões. |
Deposição | As partículas condensam-se no substrato, formando uma película fina e uniforme. |
Plasma e Gases Reactivos | Melhora as propriedades do revestimento, por exemplo, formando TiN ou CrN para resistência ao desgaste. |
Ambiente de vácuo | Garante a pureza, o controlo e a consistência da reação durante a deposição. |
Aplicações | Resistência ao desgaste, proteção contra a corrosão, acabamentos decorativos e revestimentos ópticos. |
Descubra como os revestimentos PVD podem melhorar os seus produtos- contacte os nossos especialistas hoje mesmo !