A sinterização é um processo crítico na metalurgia do pó e na cerâmica, em que os materiais em pó são aquecidos para formar uma massa sólida sem derreter.Os dois principais tipos de sinterização são a sinterização em fase líquida e a sinterização em fase sólida.A sinterização em fase líquida envolve a adição de um material de baixo ponto de fusão que derrete durante o processo, auxiliando o rearranjo e a ligação das partículas e reduzindo a temperatura de sinterização necessária.Este método é particularmente útil para materiais que são difíceis de sinterizar.Em contrapartida, a sinterização em fase sólida ocorre inteiramente no estado sólido, onde as partículas se ligam por difusão sem qualquer fase líquida.A escolha entre estes métodos depende das propriedades do material e dos resultados desejados.
Pontos-chave explicados:
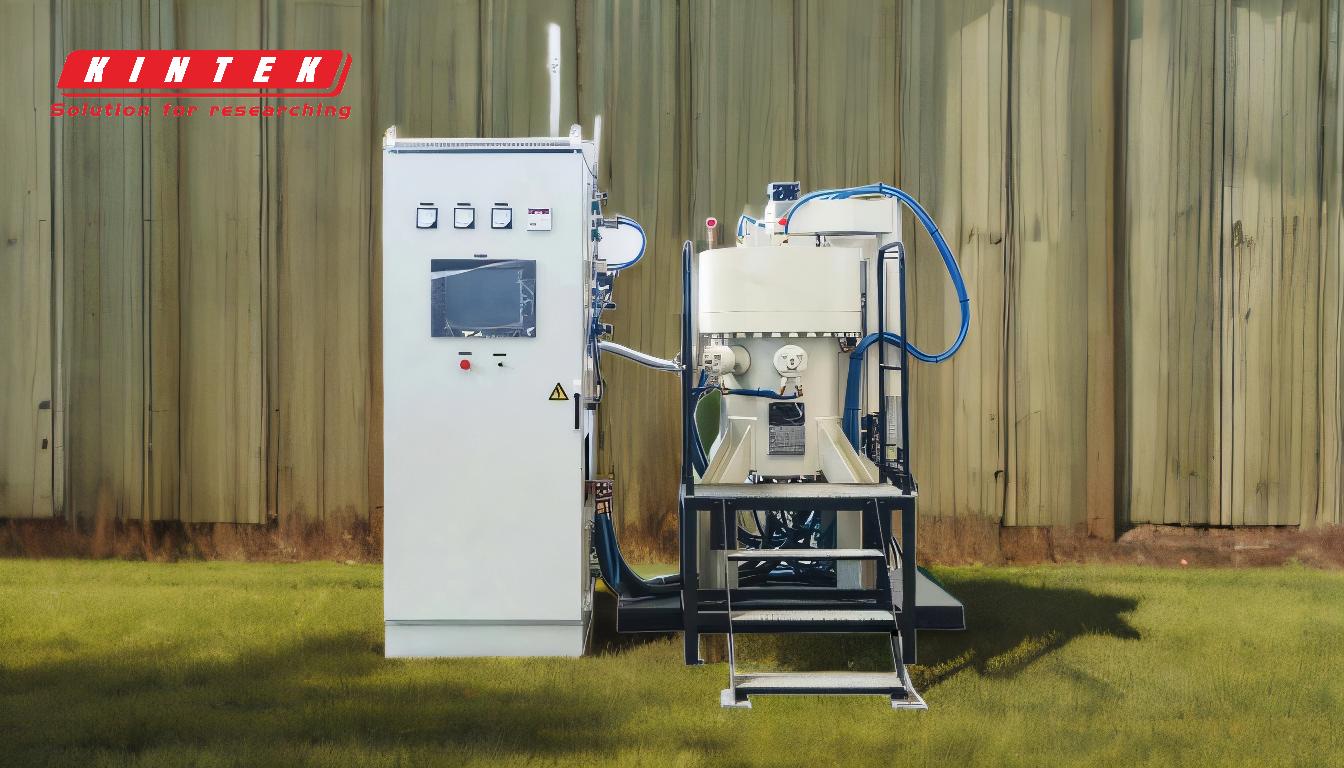
-
Definição e Mecanismo:
- Sinterização em fase líquida:Este processo envolve a adição de um material de baixo ponto de fusão ao pó.Durante o aquecimento, este aditivo derrete, formando uma fase líquida que ajuda no rearranjo e ligação das partículas.A fase líquida actua como um aglutinante ou fundente, reduzindo a temperatura de sinterização necessária e aumentando a densificação.Este método é particularmente útil para materiais que são difíceis de sinterizar.
- Sinterização em fase sólida:Neste processo, o pó compacto é densificado inteiramente no estado sólido à temperatura de sinterização.Não está presente qualquer fase líquida; em vez disso, as partículas ligam-se através de mecanismos de difusão no estado sólido.Este método é normalmente utilizado para materiais que podem atingir uma densificação suficiente sem a necessidade de uma fase líquida.
-
Requisitos de temperatura:
- Sinterização em fase líquida:A presença de uma fase líquida reduz significativamente a temperatura de sinterização, tornando o processo mais eficiente em termos energéticos.A fase líquida facilita o rearranjo e a ligação mais rápidos das partículas, o que pode ser benéfico para materiais que requerem temperaturas de processamento mais baixas.
- Sinterização em fase sólida:Este método requer geralmente temperaturas mais elevadas em comparação com a sinterização em fase líquida, porque as partículas têm de se ligar através da difusão no estado sólido, que é um processo mais lento e requer frequentemente mais energia térmica.
-
Adequação do material:
- Sinterização em fase líquida:Ideal para materiais que são difíceis de sinterizar ou que requerem uma densificação melhorada.A fase líquida ajuda a preencher os poros e a reorganizar os grãos, levando a um arranjo de empacotamento mais favorável.
- Sinterização em fase sólida:Adequado para materiais que podem atingir uma densificação suficiente apenas através da difusão em estado sólido.Este método é frequentemente utilizado para materiais que não requerem os benefícios adicionais fornecidos por uma fase líquida.
-
Eficiência do processo:
- Sinterização em fase líquida:O processo é geralmente mais eficiente devido às temperaturas de sinterização mais baixas e às taxas de densificação mais rápidas.A fase líquida ajuda a um rearranjo e ligação mais rápidos das partículas, levando a tempos de processamento mais rápidos.
- Sinterização em fase sólida:Embora possa exigir temperaturas mais elevadas e tempos de processamento mais longos, este método pode ser mais simples e menos complexo, uma vez que não envolve a gestão de uma fase líquida.
-
Aplicações:
- Sinterização em fase líquida:Normalmente utilizado na produção de cerâmicas, carbonetos cimentados e certas ligas metálicas em que uma maior densificação e temperaturas de processamento mais baixas são benéficas.
- Sinterização em fase sólida:Normalmente utilizado para metais e cerâmicas que podem atingir a densidade e as propriedades desejadas apenas através da difusão em estado sólido.
-
Considerações sobre o equipamento:
- Sinterização em fase líquida:O processo pode exigir fornos de sinterização fornos de sinterização capazes de um controlo preciso da temperatura para gerir eficazmente a fase líquida.
- Sinterização em fase sólida:Os fornos de sinterização normais são normalmente suficientes, uma vez que o processo não envolve uma fase líquida e pode ser conduzido a temperaturas mais elevadas sem necessidade de uma gestão precisa da fase líquida.
Em resumo, a escolha entre sinterização em fase líquida e em fase sólida depende das propriedades do material, dos resultados desejados e das restrições de processamento.A sinterização em fase líquida oferece vantagens em termos de temperaturas mais baixas e densificação mais rápida, enquanto a sinterização em fase sólida é mais simples e adequada para materiais que podem atingir uma densificação suficiente através da difusão no estado sólido.
Tabela de resumo:
Aspeto | Sinterização em fase líquida | Sinterização em fase sólida |
---|---|---|
Definição | Envolve um material de baixo ponto de fusão que funde, facilitando o rearranjo e a ligação das partículas. | Ocorre inteiramente no estado sólido; as partículas ligam-se através da difusão no estado sólido. |
Temperatura de sinterização | Temperatura de sinterização mais baixa devido à fase líquida. | Temperaturas mais elevadas necessárias para a difusão no estado sólido. |
Adequação do material | Ideal para materiais difíceis de sinterizar ou que requerem uma densificação melhorada. | Adequado para materiais que atingem a densificação através da difusão em estado sólido. |
Eficiência do processo | Mais eficiente devido à densificação mais rápida e temperaturas mais baixas. | Mais lento mas simples, sem a complexidade da gestão de uma fase líquida. |
Aplicações | Utilizado em cerâmicas, carbonetos cimentados e certas ligas metálicas. | Normalmente utilizado para metais e cerâmicas que atingem propriedades através da difusão em estado sólido. |
Equipamento | Requer fornos de sinterização especializados com controlo preciso da temperatura. | Os fornos de sinterização normais são suficientes. |
Precisa de ajuda para escolher o método de sinterização correto para os seus materiais? Contacte os nossos especialistas hoje para um aconselhamento personalizado!