A sinterização na metalurgia do pó é um processo crítico de tratamento térmico que transforma pós metálicos comprimidos em componentes fortes e coesos. Envolve o aquecimento do pó compactado a uma temperatura imediatamente abaixo do seu ponto de fusão, permitindo que as partículas se unam através da difusão e do crescimento do grão. Este processo aumenta a resistência, a densidade e a integridade estrutural do material, mantendo a sua forma e propriedades. A sinterização é amplamente utilizada em indústrias como a automóvel e a do fabrico de ferramentas para produzir peças complexas e de elevado desempenho, como engrenagens, árvores de cames e ferramentas de corte.
Pontos-chave explicados:
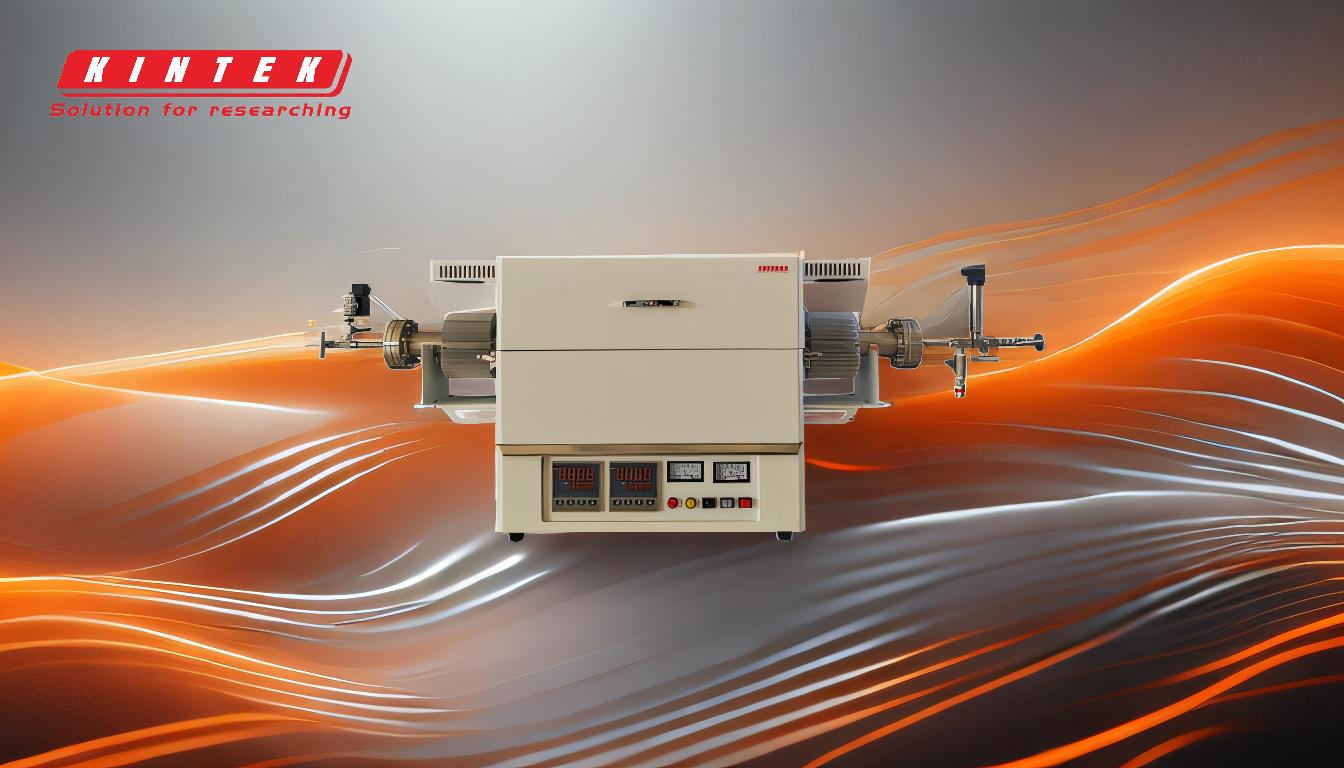
-
Definição e objetivo da sinterização:
- A sinterização é um processo de tratamento térmico na metalurgia dos pós em que os pós metálicos comprimidos são aquecidos a uma temperatura inferior ao seu ponto de fusão.
- O objetivo principal é unir as partículas de metal, criando uma estrutura forte e coesa, mantendo a forma e as propriedades desejadas do material.
-
Controlo da temperatura:
- A temperatura de sinterização é cuidadosamente controlada para se manter abaixo do ponto de fusão do metal primário ou da liga.
- Isto evita a fusão, assegurando que as partículas se ligam através da difusão em estado sólido e não através da fusão em fase líquida.
-
Mecanismo de ligação:
- Durante a sinterização, as partículas metálicas sofrem difusão, onde os átomos migram através das fronteiras das partículas.
- O crescimento dos grãos ocorre quando as partículas mais pequenas se fundem com as maiores, reduzindo a porosidade e aumentando a densidade.
- Este mecanismo de ligação reforça o material e melhora as suas propriedades mecânicas.
-
Fases da sinterização:
- Fase inicial: As partículas começam a unir-se nos pontos de contacto, formando pescoços entre elas.
- Fase intermédia: A porosidade diminui à medida que os pescoços crescem e o material se densifica.
- Fase final: O crescimento do grão domina, e o material atinge a sua densidade e resistência finais.
-
Benefícios da Sinterização:
- Resistência e dureza melhoradas: A ligação das partículas melhora significativamente as propriedades mecânicas do material.
- Formas complexas: A sinterização permite a produção de componentes intrincados e precisos que são difíceis de obter com outros métodos.
- Eficiência dos materiais: Minimiza os resíduos através da utilização eficiente dos pós metálicos.
-
Aplicações na indústria:
- Automóvel: Utilizado para o fabrico de engrenagens, árvores de cames, sedes de válvulas e outros componentes críticos.
- Fabrico de ferramentas: Produz ferramentas de corte, brocas e outras peças resistentes ao desgaste.
- Filtros e rolamentos: Cria estruturas porosas para filtros e rolamentos auto-lubrificantes.
-
Comparação com outros processos:
- Ao contrário da fusão, a sinterização preserva as propriedades originais do material, como a estrutura do grão e a composição da liga.
- É mais económico e eficiente em termos energéticos do que a fundição ou maquinagem tradicionais para a produção de peças complexas.
-
Factores que influenciam a sinterização:
- Temperatura e tempo: Temperaturas mais elevadas e tempos de sinterização mais longos melhoram geralmente a ligação, mas devem ser equilibrados para evitar um crescimento excessivo do grão.
- Caraterísticas do pó: O tamanho, a forma e a distribuição das partículas afectam o processo de sinterização e as propriedades finais.
- Atmosfera: As atmosferas controladas (por exemplo, hidrogénio, azoto ou vácuo) evitam a oxidação e asseguram resultados consistentes.
-
Processos de pós-sinterização:
- Após a sinterização, as peças podem ser submetidas a tratamentos adicionais, como o tratamento térmico, a maquinagem ou o acabamento superficial, para obter as propriedades e tolerâncias desejadas.
-
Vantagens para os fabricantes:
- Rentável: Reduz o desperdício de material e o consumo de energia em comparação com os métodos de fabrico tradicionais.
- Versatilidade: Compatível com uma vasta gama de metais e ligas, incluindo ferro, cobre, titânio e ligas à base de níquel.
- Escalabilidade: Adequado tanto para a criação de protótipos em pequena escala como para a produção em grande escala.
Ao compreender o processo de sinterização, os fabricantes podem otimizar os seus métodos de produção para criar componentes duradouros e de elevada qualidade, adaptados a aplicações específicas. Este processo é a pedra angular da metalurgia do pó moderna, permitindo a produção de peças complexas com desempenho e eficiência superiores.
Quadro de resumo:
Aspeto | Detalhes |
---|---|
Definição | Processo de tratamento térmico que liga pós metálicos abaixo do ponto de fusão. |
Mecanismo-chave | Difusão em estado sólido e crescimento de grãos. |
Fases | Inicial (formação do colo), Intermédio (densificação), Final (crescimento do grão). |
Benefícios | Maior resistência, formas complexas, eficiência dos materiais. |
Aplicações | Peças para automóveis, ferramentas de corte, filtros, rolamentos. |
Factores que influenciam | Temperatura, tempo, caraterísticas do pó, atmosfera controlada. |
Vantagens | Económica, versátil e escalável. |
Optimize a sua produção com a sinterização- contacte os nossos especialistas hoje mesmo para saber mais!