A sinterização por plasma de faísca (SPS) é uma técnica de sinterização avançada que utiliza corrente contínua pulsada (CC) e pressão uniaxial para obter uma rápida densificação de materiais em pó.O processo envolve normalmente três ou quatro fases, consoante a classificação.As fases primárias incluem a remoção do gás e a criação de vácuo, a aplicação de pressão, o aquecimento por resistência (plasma e aquecimento por efeito de joule) e o arrefecimento.Estas fases funcionam em conjunto para facilitar o aquecimento rápido, a ligação das partículas e a densificação a temperaturas mais baixas em comparação com os métodos de sinterização convencionais.O processo é altamente eficiente, permitindo a produção de materiais a granel densos e homogéneos com um crescimento mínimo de grãos.
Pontos-chave explicados:
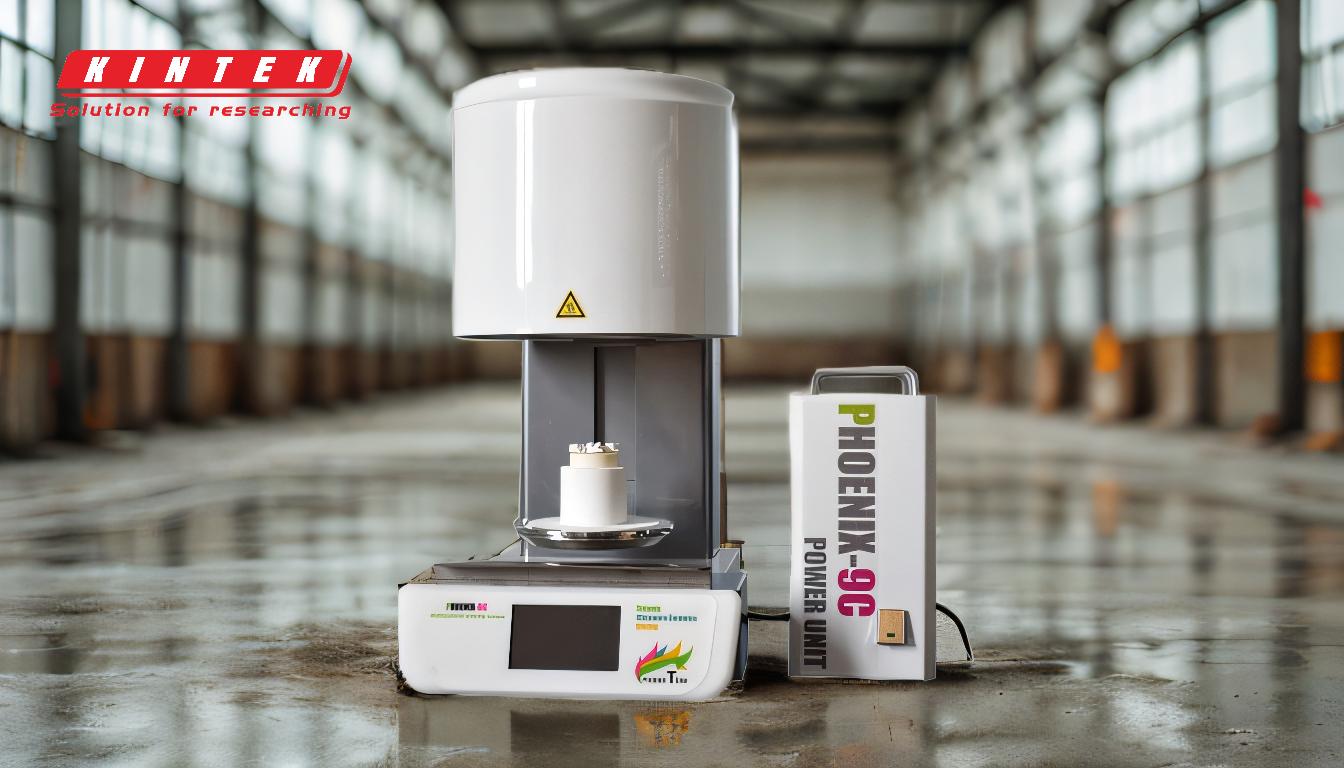
-
Remoção de gases e criação de vácuo
- Esta fase inicial envolve a remoção de gases e a criação de vácuo dentro da câmara de sinterização.
- Objetivo:Elimina o oxigénio e outros gases que poderiam oxidar o pó ou interferir com o processo de sinterização.
- Processo de sinterização:A câmara é evacuada a uma baixa pressão atmosférica, assegurando um ambiente controlado para a sinterização.
- Importância:Evita a contaminação e assegura a pureza do produto final.
-
Aplicação de pressão
- A pressão uniaxial é aplicada ao pó dentro da matriz.
- Objetivo:Compacta as partículas de pó, reduzindo os espaços entre elas e promovendo o contacto partícula a partícula.
- Processo:Um sistema hidráulico ou mecânico aplica pressão através de punções, assegurando uma compactação uniforme.
- Importância:Aumenta a densificação facilitando o rearranjo das partículas e a deformação plástica.
-
Aquecimento por resistência (aquecimento por plasma e por efeito de Joule)
- Esta fase envolve a aplicação de corrente contínua pulsada, que gera calor através de mecanismos de aquecimento por plasma e por efeito de joule.
-
Aquecimento por plasma:
- A corrente contínua pulsada cria altas temperaturas localizadas e descargas de plasma entre as partículas.
- Efeito:Derrete as superfícies das partículas, promovendo a difusão e a ligação da superfície.
-
Aquecimento por Joule:
- A corrente eléctrica atravessa a matriz condutora e, se for caso disso, a própria amostra.
- Efeito:Gera calor interno, permitindo um aquecimento rápido e uniforme do material.
- Importância:Permite uma sinterização rápida a temperaturas mais baixas, minimizando o crescimento do grão e preservando as propriedades do material.
-
Fase de arrefecimento
- Após a sinterização, o material é arrefecido em condições controladas.
- Objetivo:Solidifica o material sinterizado e estabiliza a sua microestrutura.
- Processo:As taxas de arrefecimento podem ser ajustadas para atingir as propriedades desejadas do material.
- Importância:Evita o stress térmico e assegura que o produto final tem a densidade e as propriedades mecânicas desejadas.
-
Principais vantagens do SPS
- Aquecimento e arrefecimento rápidos:Permite tempos de processamento mais curtos em comparação com a sinterização convencional.
- Temperaturas de sinterização mais baixas:Reduz o consumo de energia e minimiza os danos térmicos no material.
- Densificação melhorada:Produz materiais com alta densidade e porosidade mínima.
- Controlo do tamanho do grão:Evita o crescimento excessivo do grão, preservando as microestruturas de grão fino.
-
Aplicações do SPS
- Cerâmica avançada:Utilizado para a sinterização de cerâmicas com elevada resistência e estabilidade térmica.
- Metais e ligas:Produz componentes metálicos densos com propriedades personalizadas.
- Compósitos:Permite o fabrico de materiais compósitos com dispersão uniforme de fases.
- Nanomateriais:Preserva as nanoestruturas devido às baixas temperaturas de sinterização e aos curtos tempos de processamento.
Ao compreender estas fases, os compradores de equipamento e consumíveis podem avaliar melhor os requisitos dos sistemas SPS, incluindo materiais de matriz (por exemplo, grafite), elementos de aquecimento e sistemas de vácuo.Este conhecimento também ajuda a selecionar os pós adequados e a otimizar os parâmetros do processo para aplicações específicas.
Tabela de resumo:
Fase | Objetivo | Processo | Importância |
---|---|---|---|
Remoção de gases e criação de vácuo | Elimina os gases para evitar a oxidação e a contaminação. | Câmara evacuada a baixa pressão atmosférica. | Assegura um ambiente controlado e a pureza do produto final. |
Aplicação de pressão | Compacta as partículas de pó para um melhor contacto e densificação. | O sistema hidráulico ou mecânico aplica uma pressão uniforme através de punções. | Aumenta o rearranjo das partículas e a deformação plástica. |
Aquecimento por resistência | Gera calor através de plasma e aquecimento joule para uma sinterização rápida. | A corrente contínua pulsada cria altas temperaturas localizadas e calor interno através da matriz condutora. | Permite a sinterização rápida a temperaturas mais baixas, preservando as propriedades do material. |
Fase de arrefecimento | Solidifica o material e estabiliza a sua microestrutura. | Controlar as taxas de arrefecimento para obter as propriedades desejadas. | Evita o stress térmico e assegura uma densidade e propriedades mecânicas óptimas. |
Principais vantagens | Aquecimento/arrefecimento rápido, temperaturas de sinterização mais baixas, densificação melhorada. | Tempos de processamento mais curtos, eficiência energética e crescimento mínimo de grãos. | Produz materiais densos e homogéneos com microestruturas de grão fino. |
Aplicações | Cerâmicas avançadas, metais/ligas, compósitos, nanomateriais. | Fabrica cerâmicas de alta resistência, metais densos, compósitos uniformes e nanoestruturas preservadas. | Propriedades de material personalizadas para diversas aplicações industriais e de investigação. |
Pronto para explorar como a sinterização por plasma de faísca pode revolucionar o seu processamento de materiais? Contacte os nossos especialistas hoje para soluções à medida!