A sinterização em fase líquida, embora benéfica para aumentar a densificação e reduzir as temperaturas de sinterização, apresenta várias desvantagens. Estas incluem desafios no controlo da microestrutura, potencial para uma densificação irregular e limitações na seleção de materiais devido à necessidade de uma fase líquida compatível. Além disso, o processo pode levar a problemas como o crescimento do grão, tensões residuais e anisotropia nas propriedades. As altas temperaturas e o consumo de energia associados à sinterização em fase líquida também contribuem para aumentar os custos operacionais e as preocupações ambientais. Compreender estes inconvenientes é crucial para otimizar o processo e selecionar os materiais e parâmetros corretos para aplicações específicas.
Pontos-chave explicados:
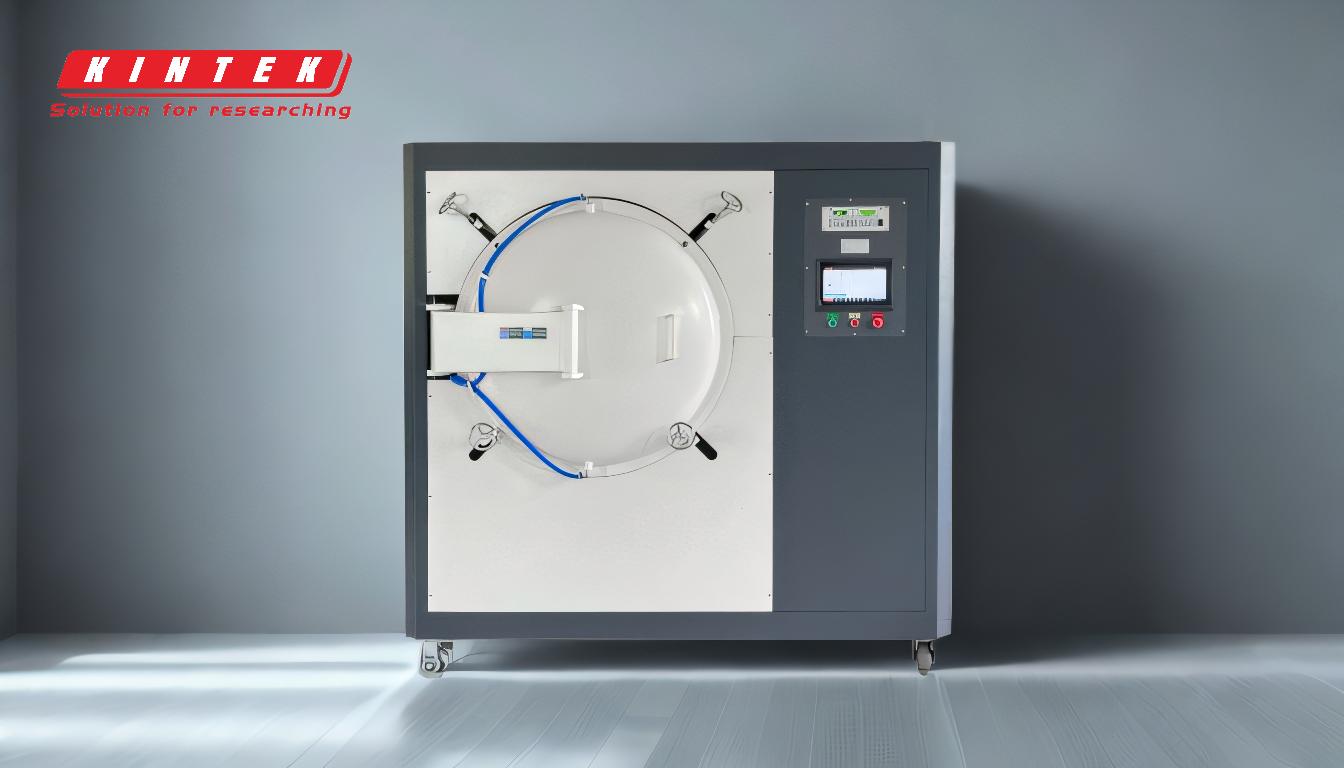
-
Desafios do controlo da microestrutura:
- A sinterização em fase líquida pode levar a um crescimento e engrossamento irregulares dos grãos, resultando numa microestrutura menos uniforme.
- A presença de uma fase líquida pode causar densificação localizada, levando a variações na densidade e nas propriedades mecânicas da peça sinterizada.
-
Anisotropia nas propriedades:
- O fluxo da fase líquida durante a sinterização pode causar o alinhamento direcional dos grãos, levando à anisotropia nas propriedades mecânicas, térmicas e eléctricas.
- Esta anisotropia pode ser problemática para aplicações que requerem um comportamento isotrópico.
-
Limitações da seleção de materiais:
- A sinterização em fase líquida requer a formação de uma fase líquida compatível, o que limita a gama de materiais que podem ser efetivamente sinterizados utilizando este método.
- A necessidade de aditivos específicos para formar a fase líquida pode complicar a formulação do material e aumentar os custos.
-
Tensões residuais e defeitos:
- O processo de arrefecimento após a sinterização em fase líquida pode induzir tensões residuais devido à contração diferencial entre as fases sólida e líquida.
- Estas tensões podem provocar fissuras, deformações ou outros defeitos no produto final.
-
Elevado consumo de energia:
- A sinterização em fase líquida requer frequentemente temperaturas elevadas para atingir a formação da fase líquida necessária, o que leva a um maior consumo de energia.
- Este facto contribui para aumentar os custos operacionais e o impacto ambiental.
-
Crescimento e engrossamento dos grãos:
- A fase líquida pode acelerar o crescimento do grão, o que pode degradar as propriedades mecânicas do material sinterizado.
- O controlo do tamanho do grão torna-se mais difícil, exigindo um controlo preciso dos parâmetros de sinterização.
-
Custo e complexidade:
- O equipamento e o controlo do processo necessários para a sinterização em fase líquida são mais complexos e dispendiosos em comparação com a sinterização em estado sólido.
- A necessidade de moldes especializados, aditivos e fornos de alta temperatura aumenta o custo total.
-
Encolhimento e controlo dimensional:
- As peças sinterizadas com uma fase líquida sofrem frequentemente uma maior contração, que deve ser tida em conta durante o processo de conceção e produção.
- Isto pode complicar o fabrico de peças com tolerâncias dimensionais apertadas.
-
Preocupações ambientais e de segurança:
- As altas temperaturas e a potencial utilização de materiais perigosos na sinterização em fase líquida podem representar riscos de segurança e desafios ambientais.
- O manuseamento e a eliminação adequados dos materiais e subprodutos são necessários para mitigar estas preocupações.
Ao compreender estas desvantagens, os fabricantes podem avaliar melhor a adequação da sinterização em fase líquida para as suas aplicações específicas e tomar medidas para mitigar potenciais problemas através de uma conceção cuidadosa do processo e da seleção de materiais.
Quadro de resumo:
Desvantagem | Principais pormenores |
---|---|
Controlo da microestrutura | Crescimento irregular do grão, densificação localizada e propriedades não uniformes. |
Anisotropia nas propriedades | Alinhamento direcional do grão que conduz a um comportamento mecânico/térmico inconsistente. |
Limitações da seleção de materiais | Requer uma fase líquida compatível, o que limita as opções de materiais e aumenta os custos. |
Tensões residuais e defeitos | A contração diferencial provoca fissuras, deformações ou outros defeitos. |
Elevado consumo de energia | As temperaturas elevadas aumentam o consumo de energia e os custos operacionais. |
Crescimento e engrossamento dos grãos | O crescimento acelerado do grão degrada as propriedades mecânicas. |
Custo e complexidade | O equipamento especializado e os aditivos aumentam os custos e a complexidade do processo. |
Retração e controlo dimensional | Uma maior contração complica o fabrico de tolerâncias apertadas. |
Preocupações ambientais e de segurança | As temperaturas elevadas e os materiais perigosos representam riscos e problemas ambientais. |
Precisa de ajuda para otimizar o seu processo de sinterização? Contacte os nossos especialistas hoje mesmo para soluções à medida!