Para reduzir os problemas de sinterização, como fissuras e irregularidades, é essencial concentrar-se na seleção de materiais, na otimização do processo e nos ajustes do equipamento. Ao escolher materiais adequados, otimizar os parâmetros de sinterização e garantir um aquecimento uniforme, pode melhorar significativamente a qualidade e o rendimento do produto. As principais estratégias incluem a utilização de auxiliares de sinterização, o controlo das zonas de aquecimento e a correspondência com a curva de calor original para minimizar os defeitos. Além disso, a compreensão dos mecanismos de sinterização, como a sinterização em fase líquida, pode ajudar a baixar as temperaturas e melhorar o desenvolvimento microestrutural. A implementação sistemática destes passos conduzirá a um processo de sinterização mais eficiente e consistente.
Pontos-chave explicados:
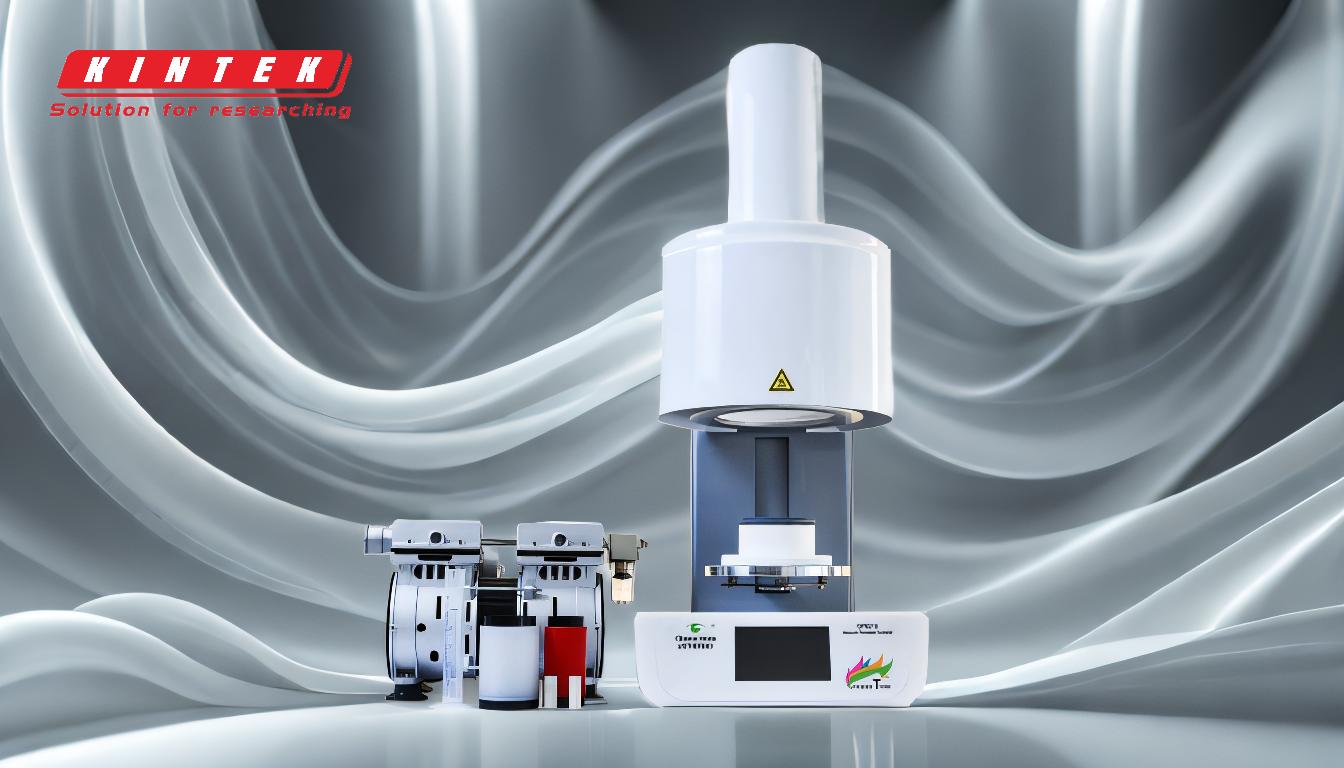
-
Seleção de materiais:
- Importância: A escolha dos materiais corretos é crucial para reduzir os defeitos de sinterização, como as fissuras. Os materiais com melhores propriedades térmicas e mecânicas podem suportar o processo de sinterização de forma mais eficaz.
-
Passos a seguir:
- Avaliar as propriedades dos materiais, como a condutividade térmica, o ponto de fusão e a resistência mecânica.
- Considerar a utilização de auxiliares de sinterização ou aditivos que formem fases líquidas transitórias para melhorar a ligação das partículas.
-
Otimização dos parâmetros de sinterização:
- Importância: Parâmetros de sinterização corretamente ajustados garantem um aquecimento e arrefecimento uniformes, reduzindo o risco de fissuras e irregularidades.
-
Passos a seguir:
- Ajustar os perfis de temperatura de acordo com os requisitos do material.
- Controlar as taxas de aquecimento e arrefecimento para minimizar o stress térmico.
- Monitorizar e ajustar as definições de pressão para garantir uma densificação consistente.
-
Ajustamentos de equipamento:
- Importância: O equipamento avançado pode proporcionar um melhor controlo do processo de sinterização, conduzindo a resultados mais uniformes.
-
Passos a seguir:
- Utilizar um tambor rotativo com um dispositivo de acionamento para garantir uma distribuição uniforme do material.
- Controlo independente das zonas de aquecimento no forno elétrico para corresponder à curva de calor desejada.
- Implementar sistemas de monitorização em tempo real para medir e ajustar o processo de sinterização de forma dinâmica.
-
Compreender os mecanismos de sinterização:
- Importância: Uma compreensão profunda dos mecanismos de sinterização pode conduzir a soluções inovadoras para reduzir os defeitos e melhorar as propriedades dos materiais.
-
Passos a seguir:
- Estudar a sinterização em fase líquida para baixar a temperatura de sinterização e melhorar a ligação das partículas.
- Explorar a utilização de auxiliares de sinterização que formam fases líquidas transitórias nas superfícies de contacto das partículas.
- Investigar o impacto de diferentes atmosferas de sinterização nas propriedades dos materiais.
-
Correspondência com a curva de calor original:
- Importância: Garantir que o processo de sinterização corresponde à curva de calor original é fundamental para manter a consistência e a qualidade do produto.
-
Passos a seguir:
- Utilizar ferramentas de medição precisas para reproduzir a curva de calor original.
- Ajustar os parâmetros do processo de sinterização para os alinhar com os dados históricos.
- Monitorizar e aperfeiçoar continuamente o processo para manter o alinhamento com a curva de calor desejada.
Ao abordar sistematicamente cada um destes pontos-chave, é possível reduzir eficazmente os problemas de sinterização e obter um processo de sinterização mais fiável e de alta qualidade.
Quadro de resumo:
Área-chave | Importância | Passos a seguir |
---|---|---|
Seleção de materiais | A escolha dos materiais corretos reduz os defeitos como as fissuras. | - Avaliar a condutividade térmica, o ponto de fusão e a resistência mecânica. Utilizar auxiliares de sinterização para uma melhor ligação das partículas. |
Otimização de parâmetros | Parâmetros adequados garantem um aquecimento e arrefecimento uniformes, reduzindo os defeitos. | - Ajuste os perfis de temperatura, controle as taxas de aquecimento/arrefecimento e monitorize as definições de pressão para uma densificação consistente. |
Ajustamentos de equipamento | O equipamento avançado melhora o controlo e a uniformidade do processo de sinterização. | - Utilizar tambores rotativos, controlar de forma independente as zonas de aquecimento e implementar sistemas de monitorização em tempo real. |
Mecanismos de sinterização | A compreensão de mecanismos como a sinterização em fase líquida faz baixar as temperaturas. | - Estudar a sinterização em fase líquida, explorar os auxiliares de sinterização e investigar as atmosferas de sinterização. |
Curva de calor correspondente | O alinhamento com a curva de calor original garante a consistência e a qualidade do produto. | - Utilizar ferramentas precisas para reproduzir curvas de calor, ajustar parâmetros e monitorizar continuamente o processo. |
Pronto para otimizar o seu processo de sinterização? Contacte os nossos especialistas hoje mesmo para soluções à medida!