A sinterização é um processo crítico na ciência e fabrico de materiais, em que os materiais em pó ou granulados são transformados em corpos sólidos e densos através da aplicação de calor e pressão sem atingir o ponto de fusão do material. Este processo é amplamente utilizado em indústrias como a cerâmica, a metalurgia do pó e o fabrico avançado. Envolve etapas como a preparação do pó, a compressão, o aquecimento e a solidificação, que resultam na fusão de partículas numa massa unificada de baixa porosidade. O processo de sinterização melhora as propriedades do material, como a resistência, a durabilidade e a densidade, tornando-o essencial para a criação de componentes com elevado desempenho e precisão.
Pontos-chave explicados:
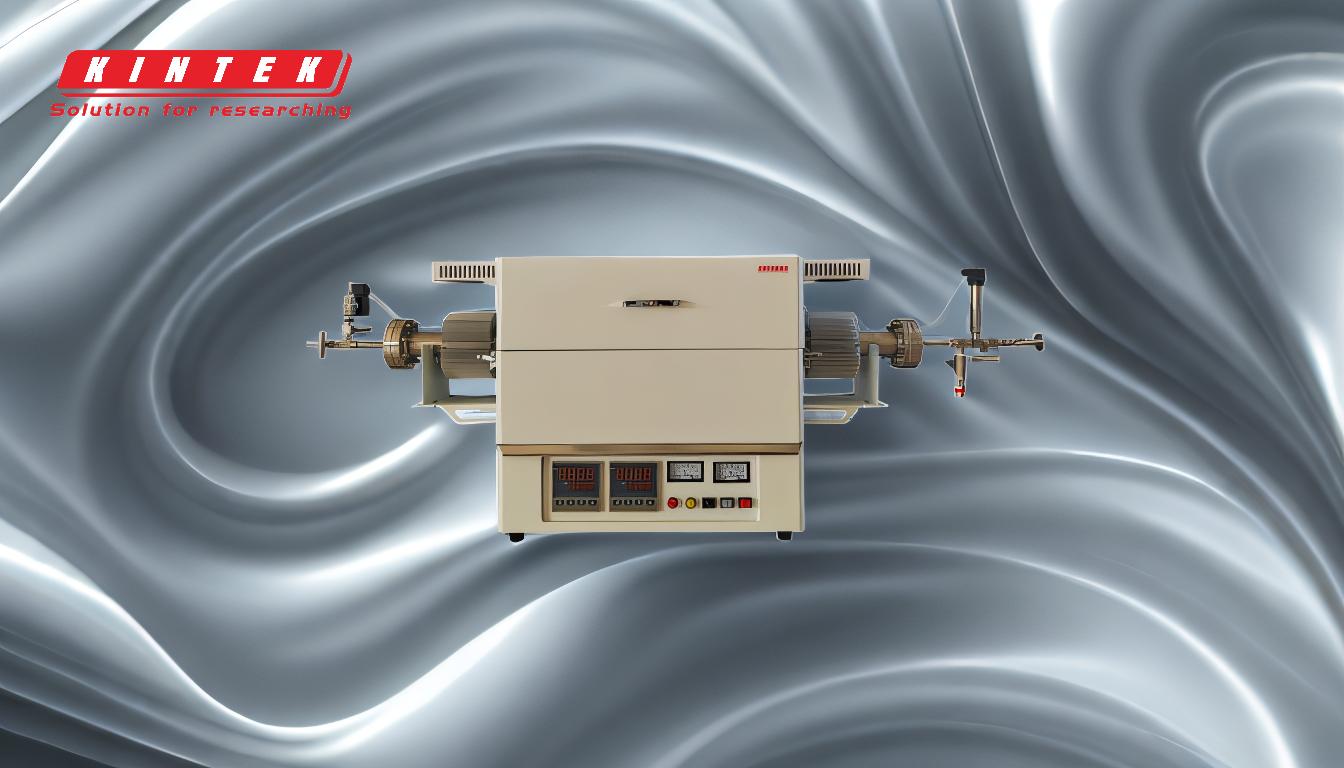
-
Definição e objetivo da sinterização:
- A sinterização é o processo de ligação de partículas de pó adjacentes numa massa sólida e densa, utilizando calor e pressão sem derreter o material.
- É utilizado para criar materiais com propriedades mecânicas melhoradas, tais como maior resistência, durabilidade e densidade.
- As aplicações comuns incluem a produção de cerâmica, metais, plásticos e materiais avançados como o tungsténio e o molibdénio.
-
Etapas do processo de sinterização:
-
Preparação do pó:
- A matéria-prima é preparada na forma de pó, frequentemente misturada com agentes de acoplamento ou aglutinantes para melhorar a ligação.
- Métodos como a soldadura a frio, a impressão 3D ou a prensagem mecânica são utilizados para moldar o pó num compacto.
-
Compressão:
- O pó é prensado na forma desejada utilizando ferramentas ou moldes em condições controladas.
- Este passo assegura que as partículas estão em contacto estreito, o que é essencial para uma sinterização eficaz.
-
Aquecimento:
- O material compactado é aquecido a uma temperatura ligeiramente inferior ao seu ponto de fusão.
- O calor ativa os mecanismos de difusão, permitindo que os átomos migrem através das fronteiras das partículas e as fundam.
-
Solidificação:
- Após o aquecimento, o material é arrefecido, resultando numa massa sólida e unificada com porosidade reduzida e integridade estrutural melhorada.
-
Preparação do pó:
-
Mecanismos de Sinterização:
-
Sinterização em estado sólido:
- As partículas ligam-se por difusão atómica sem a presença de uma fase líquida.
- Isto é comum em materiais com pontos de fusão elevados, como a cerâmica e os metais refractários.
-
Sinterização em fase líquida (LPS):
- É introduzida uma pequena quantidade de fase líquida para acelerar a fusão e a densificação das partículas.
- Este método é frequentemente utilizado para materiais que beneficiam de uma ligação melhorada, como certos metais e ligas.
-
Sinterização em estado sólido:
-
Aplicações de Sinterização:
-
Cerâmica:
- A sinterização é utilizada para produzir cerâmica, azulejos e componentes de cerâmica avançada com elevada estabilidade térmica e mecânica.
-
Metalurgia do pó:
- Os pós metálicos são sinterizados para criar componentes como engrenagens, rolamentos e filtros com dimensões e propriedades precisas.
-
Materiais avançados:
- Materiais como o tungsténio, o molibdénio e os materiais compósitos são sinterizados para utilização em aplicações de alta temperatura e alta resistência.
-
Cerâmica:
-
Vantagens da Sinterização:
-
Propriedades melhoradas do material:
- A sinterização melhora a densidade, a resistência e a durabilidade, eliminando os espaços vazios e criando fortes ligações atómicas.
-
Custo-eficácia:
- O processo permite a produção de formas complexas com um mínimo de desperdício de material.
-
Versatilidade:
- A sinterização pode ser aplicada a uma vasta gama de materiais, incluindo metais, cerâmicas e polímeros.
-
Propriedades melhoradas do material:
-
Desafios e considerações:
-
Controlo da temperatura:
- A regulação exacta da temperatura é crucial para evitar a fusão ou a ligação incompleta.
-
Qualidade do pó:
- O tamanho, a forma e a pureza do pó afectam significativamente o resultado da sinterização.
-
Pós-processamento:
- Podem ser necessárias etapas adicionais, como maquinagem ou tratamento de superfície, para atingir as especificações do produto final.
-
Controlo da temperatura:
Ao compreender o processo de sinterização e as suas etapas principais, os fabricantes podem otimizar a produção de materiais com propriedades superiores, garantindo a sua adequação a aplicações exigentes em várias indústrias.
Quadro de resumo:
Aspeto | Detalhes |
---|---|
Definição | Ligação de partículas de pó numa massa densa utilizando calor e pressão. |
Principais etapas | Preparação de pós, compressão, aquecimento e solidificação. |
Mecanismos | Sinterização em estado sólido e sinterização em fase líquida (LPS). |
Aplicações | Cerâmica, metalurgia do pó, materiais avançados como o tungsténio e o molibdénio. |
Vantagens | Densidade, resistência, durabilidade e rentabilidade melhoradas. |
Desafios | Controlo da temperatura, qualidade do pó e requisitos de pós-processamento. |
Descubra como a sinterização pode otimizar a sua produção de materiais- contacte os nossos especialistas hoje mesmo !