O revestimento por sinterização é um processo especializado utilizado para criar revestimentos densos, duradouros e funcionais em substratos através da fusão de partículas sem derreter o material de base.Este processo envolve a preparação de uma mistura de pó, a sua compactação na forma desejada e a aplicação de calor e pressão para unir as partículas.O resultado é um revestimento coeso e de baixa porosidade com propriedades mecânicas melhoradas.A sinterização é amplamente utilizada em indústrias como a metalurgia do pó, cerâmica e fabrico de aditivos para produzir revestimentos com elevada resistência, resistência ao desgaste e estabilidade térmica.Abaixo, os principais passos e princípios do processo de revestimento por sinterização são explicados em pormenor.
Explicação dos pontos-chave:
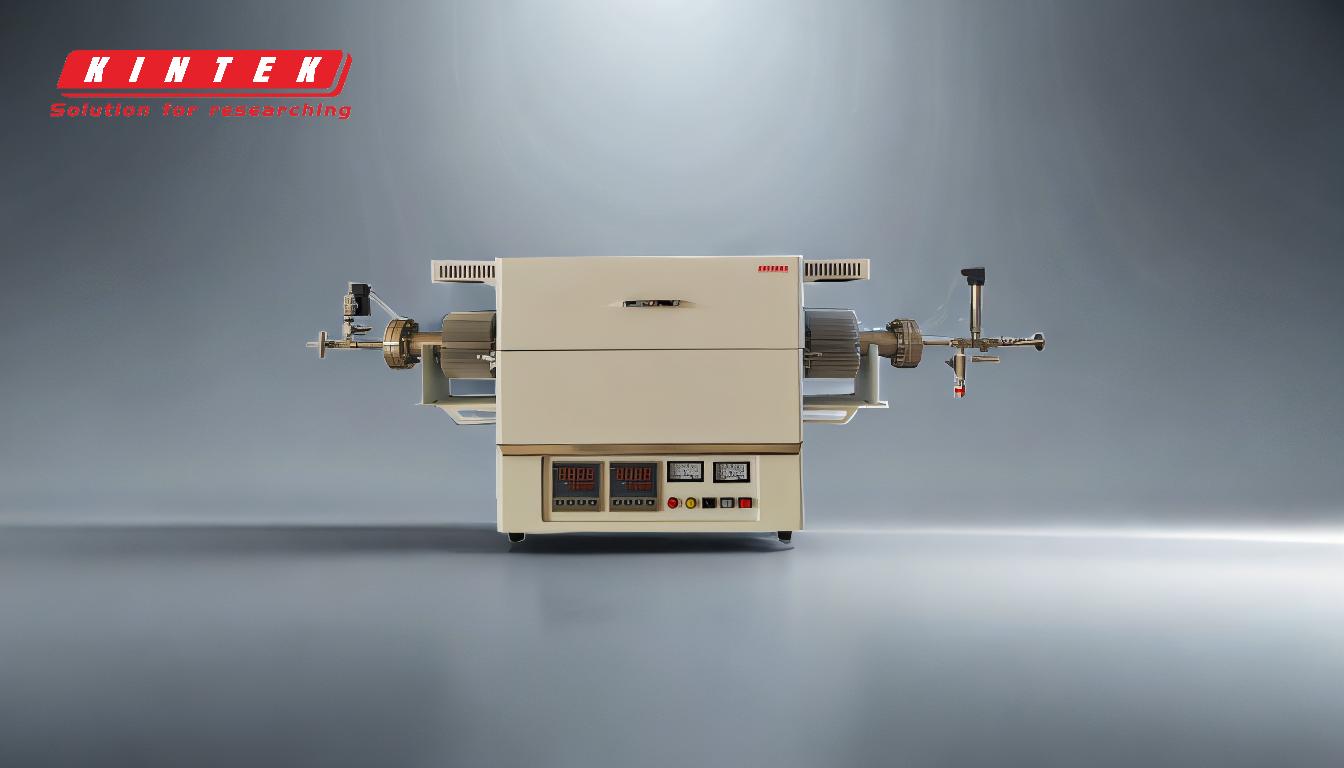
-
Preparação da mistura de pó
- O processo começa com a preparação de uma mistura de pó, que normalmente inclui o material primário (por exemplo, metal, cerâmica ou plástico) e um agente de ligação (por exemplo, cera ou polímero).
- O agente de ligação ajuda as partículas de pó a aderirem umas às outras durante a fase inicial de moldagem.
- A mistura de pó é frequentemente adaptada para obter propriedades específicas no revestimento final, tais como dureza, condutividade térmica ou resistência à corrosão.
-
Compactação e moldagem
- A mistura de pó é compactada na forma desejada utilizando métodos como ferramentas de prensagem, soldaduras a frio ou lasers impressos em 3D.
- Este passo assegura que as partículas de pó estão densamente compactadas e uniformemente distribuídas, o que é fundamental para obter um revestimento homogéneo.
- A compactação é normalmente efectuada numa atmosfera controlada para evitar a contaminação e a oxidação.
-
Aquecimento e consolidação
- O pó compactado é aquecido a uma temperatura imediatamente abaixo do ponto de fusão do material primário.
- Este aquecimento ativa a difusão de átomos através dos limites das partículas, fazendo com que estas se fundam e densifiquem.
- Em alguns casos, é utilizada a sinterização em fase líquida (LPS), em que um material secundário com um ponto de fusão mais baixo funde e preenche os espaços entre as partículas, acelerando o processo de ligação.
-
Remoção do agente de ligação
- À medida que a temperatura aumenta, o agente de ligação evapora-se ou queima, deixando para trás uma estrutura porosa do material primário.
- Este passo é crucial para garantir que o revestimento final está livre de impurezas e tem uma composição uniforme.
-
Fusão e densificação das partículas
- A temperaturas mais elevadas, as partículas primárias começam a fundir-se nas suas superfícies, formando uma massa sólida com porosidade reduzida.
- O processo de fusão é impulsionado pela difusão atómica, que reforça as ligações entre as partículas e melhora as propriedades mecânicas do revestimento.
- O resultado é um revestimento denso e coeso que adere firmemente ao substrato.
-
Arrefecimento e solidificação
- Após a conclusão do processo de fusão, o material é deixado arrefecer e solidificar numa massa unificada.
- O arrefecimento controlado é essencial para evitar tensões térmicas e garantir que o revestimento mantém as propriedades desejadas.
- O produto final é um revestimento duro e duradouro com maior resistência, resistência ao desgaste e estabilidade térmica.
-
Aplicações dos revestimentos de sinterização
- Os revestimentos de sinterização são amplamente utilizados em indústrias como a aeroespacial, automóvel e eletrónica para aplicações que requerem materiais de elevado desempenho.
- Os exemplos incluem revestimentos resistentes ao desgaste para ferramentas de corte, revestimentos de barreira térmica para componentes de motores e revestimentos resistentes à corrosão para equipamento industrial.
- O processo é também utilizado no fabrico de aditivos para criar peças complexas e de elevada resistência com geometrias precisas.
-
Vantagens dos revestimentos por sinterização
- O processo de sinterização permite a criação de revestimentos com propriedades personalizadas, como a dureza, a porosidade e a condutividade térmica.
- É rentável para produzir grandes quantidades de revestimentos de alta qualidade.
- O processo pode ser utilizado com uma vasta gama de materiais, incluindo metais, cerâmicas e compósitos.
Seguindo estes passos, os revestimentos por sinterização atingem um equilíbrio entre resistência, durabilidade e funcionalidade, tornando-os numa solução valiosa para uma variedade de aplicações industriais.
Quadro de resumo:
Passo | Descrição |
---|---|
1.Preparação do pó | Misturar o material primário (por exemplo, metal, cerâmica) com um agente de ligação (por exemplo, cera). |
2.Compactação e modelação | Compactar o pó na forma desejada utilizando ferramentas de prensagem ou lasers impressos em 3D. |
3.Aquecimento e consolidação | Aquecer até abaixo do ponto de fusão, permitindo a ligação e densificação das partículas. |
4.Remoção do agente de ligação | O agente de ligação evapora-se, deixando uma estrutura porosa do material primário. |
5.Fusão de partículas | As partículas fundem-se nas superfícies, formando um revestimento denso e coeso. |
6.Arrefecimento e solidificação | O arrefecimento controlado assegura que o revestimento mantém a resistência e a durabilidade. |
7.Aplicações | Utilizado na indústria aeroespacial, automóvel e eletrónica para revestimentos resistentes ao desgaste. |
8.Vantagens | Propriedades personalizadas, económicas e compatíveis com metais, cerâmicas, etc. |
Descubra como os revestimentos de sinterização podem melhorar as suas aplicações industriais... contacte-nos hoje !