O processo de calcinação rotativa envolve a utilização de um forno rotativo para aquecer materiais a altas temperaturas, provocando a dissociação química ou alterações físicas, como a remoção de humidade.O processo baseia-se num tambor rotativo, ligeiramente inclinado para permitir o fluxo de material, e é aquecido interna ou externamente.O material tomba dentro do tambor, assegurando uma exposição uniforme ao calor, enquanto a temperatura controlada e o tempo de retenção garantem a reação desejada.Os calcinadores rotativos são normalmente utilizados para materiais inorgânicos como calcário, dolomite e magnesite, produzindo produtos uniformes de forma eficiente.
Pontos-chave explicados:
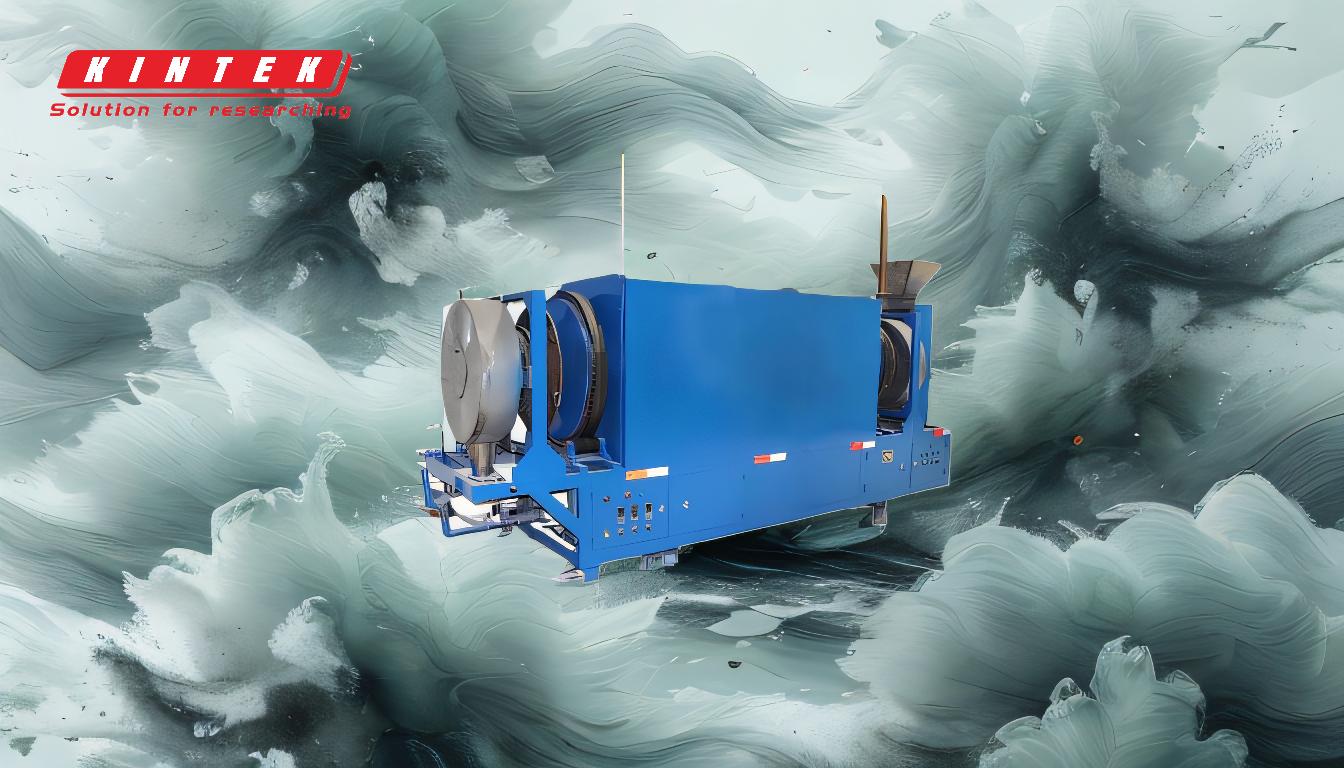
-
Função principal dos calcinadores rotativos:
- Os calcinadores rotativos são concebidos para aquecer materiais a altas temperaturas, permitindo a dissociação química ou alterações físicas, como a remoção de humidade.
- Este processo é particularmente útil para materiais inorgânicos como o carbonato de cálcio, que se dissocia em óxido de cálcio e dióxido de carbono.
-
Estrutura e funcionamento do forno rotativo:
- O forno rotativo é um grande tambor cilíndrico, oco, que gira lentamente em torno do seu eixo longitudinal.
- É ligeiramente inclinado para permitir que a gravidade ajude a mover o material da extremidade superior (entrada de matéria-prima) para a extremidade inferior (porta de saída).
- A rotação garante o tombamento e a mistura do material, promovendo uma exposição uniforme ao calor.
-
Mecanismos de aquecimento:
-
O aquecimento pode ser conseguido através de métodos diretos ou indirectos:
- Aquecimento direto:Os gases quentes são gerados no interior do forno ou introduzidos a partir de um forno externo.
- Aquecimento indireto:O calor é aplicado externamente ao tambor, evitando o contacto direto entre o material e a fonte de calor.
- A direção dos gases quentes pode ser em co-corrente (mesma direção do fluxo de material) ou em contra-corrente (direção oposta), dependendo da eficiência térmica desejada e do controlo da reação.
-
O aquecimento pode ser conseguido através de métodos diretos ou indirectos:
-
Temperatura e tempo de retenção:
- A temperatura e o tempo de retenção são pré-determinados com base em análises químicas e térmicas do material.
- Estes parâmetros asseguram que o material atinge o estado necessário, seja para dissociação química ou remoção de humidade.
- A conceção selada do forno ajuda a manter uma atmosfera controlada, optimizando as condições de reação.
-
Aplicações dos calcinadores rotativos:
-
Os calcinadores rotativos são amplamente utilizados em indústrias que requerem processamento a alta temperatura, tais como:
- Produção de cimento:Calcinação de calcário para produzir cal.
- Processamento de minerais:Transformação de dolomite, magnesite e outros minerais.
- Fabrico de produtos químicos:Produção de compostos inorgânicos e remoção de humidade de materiais como o bórax.
-
Os calcinadores rotativos são amplamente utilizados em indústrias que requerem processamento a alta temperatura, tais como:
-
Vantagens dos calcinadores rotativos:
- Qualidade uniforme do produto:A ação de tombamento assegura uma distribuição consistente do calor, resultando num produto uniforme.
- Elevadas taxas de processamento:Os calcinadores rotativos podem lidar com grandes volumes de material de forma eficiente, tornando-os adequados para operações em escala industrial.
- Versatilidade:Podem processar uma vasta gama de materiais e tamanhos de partículas, normalmente até 60 mm.
-
Considerações operacionais:
- Taxa de alimentação do material:O ritmo a que o material é introduzido no forno deve ser controlado para corresponder aos requisitos de tempo de retenção e temperatura.
- Velocidade de rotação do forno:A velocidade de rotação afecta a ação de tombamento e o fluxo de material, influenciando a exposição ao calor e a eficiência da reação.
- Gestão da fonte de calor:A escolha da fonte de calor (direta ou indireta) e da direção do fluxo de gás (em co-corrente ou em contra-corrente) tem impacto na eficiência energética e no controlo do processo.
Ao compreender estes pontos-chave, o comprador pode avaliar a adequação dos calcinadores rotativos às suas necessidades específicas, considerando factores como o tipo de material, a produção desejada e a eficiência operacional.
Tabela de resumo:
Aspeto | Detalhes |
---|---|
Função principal | Aquece materiais para dissociação química ou alterações físicas como a remoção de humidade. |
Estrutura | Tambor rotativo, ligeiramente inclinado para o fluxo de material e exposição uniforme ao calor. |
Mecanismos de aquecimento | Métodos de aquecimento direto (interno) ou indireto (externo). |
Aplicações | Produção de cimento, processamento de minerais e fabrico de produtos químicos. |
Vantagens | Qualidade uniforme do produto, altas taxas de processamento e versatilidade. |
Factores operacionais | Taxa de alimentação do material, velocidade de rotação do forno e gestão da fonte de calor. |
Pronto para otimizar o seu processamento de materiais? Contacte-nos hoje para saber mais sobre os calcinadores rotativos!