O aumento da pressão durante a sinterização tem vários efeitos significativos no material que está a ser processado.Em primeiro lugar, melhora o processo de densificação ao fornecer uma força motriz adicional para a fusão de partículas, o que é particularmente benéfico para materiais difíceis de sinterizar.Isto resulta numa redução da porosidade e em propriedades mecânicas melhoradas, como a força, a dureza e a resistência ao desgaste.Além disso, a aplicação de pressão pode diminuir o tempo de sinterização, tornando o processo mais eficiente.A microestrutura do material, incluindo o tamanho do grão e a distribuição dos limites do grão, também é influenciada positivamente, levando a um melhor desempenho geral do material.
Pontos-chave explicados:
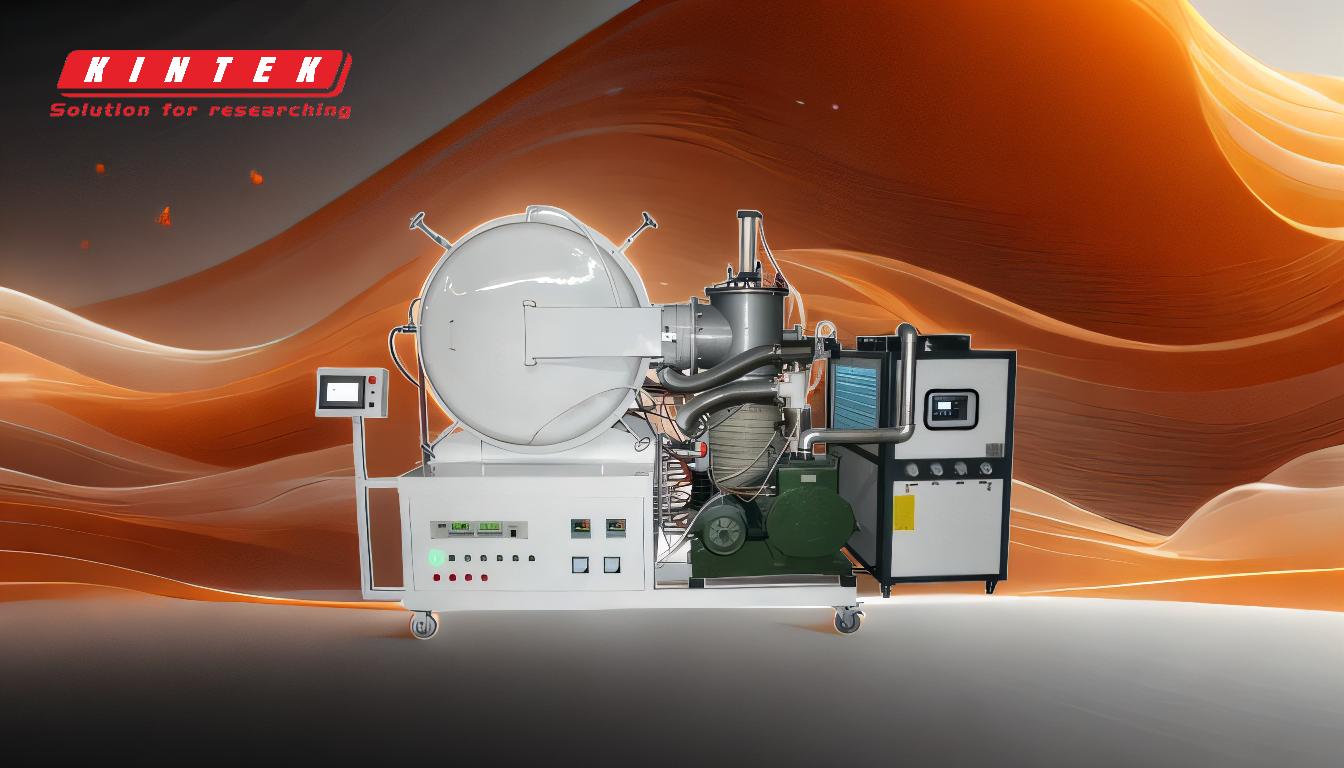
-
Densificação melhorada:
- Força motriz para a fusão: A aplicação de pressão durante a sinterização introduz uma força motriz adicional que ajuda as partículas a fundirem-se mais eficazmente.Isto é especialmente útil para materiais que, de outra forma, seriam difíceis de sinterizar.
- Porosidade reduzida: O aumento da pressão ajuda a minimizar a porosidade do material sinterizado, levando a uma estrutura mais densa e coesa.
-
Propriedades mecânicas melhoradas:
- Resistência e Dureza: O processo de densificação resulta em materiais com propriedades mecânicas superiores.As ligações entre as partículas tornam-se mais fortes, aumentando a resistência geral e a dureza do material.
- Resistência ao desgaste: Uma estrutura mais densa com menos poros também melhora a resistência ao desgaste do material, tornando-o mais durável sob tensão mecânica.
-
Redução do tempo de sinterização:
- Eficiência: A aplicação de pressão pode reduzir significativamente o tempo necessário para a sinterização.Isto torna o processo mais eficiente e pode levar a poupanças de custos em aplicações industriais.
- Consistência: Tempos de sinterização mais curtos também podem contribuir para propriedades de material mais consistentes, uma vez que o risco de sinterização excessiva ou irregular é reduzido.
-
Benefícios microestruturais:
- Tamanho e distribuição do grão: A pressão durante a sinterização afecta o tamanho do grão e a distribuição dos limites de grão no material.Isto pode levar a uma microestrutura mais uniforme, o que é benéfico para as propriedades mecânicas do material.
- Forma dos contornos de grão: A forma e a distribuição dos limites do grão também são influenciadas, o que pode aumentar ainda mais a resistência e a durabilidade do material.
-
Aplicação em prensagem a quente:
- Técnica: A prensagem a quente é uma técnica de sinterização específica em que a pressão e o calor são aplicados simultaneamente.Este método é particularmente eficaz para materiais que são difíceis de sinterizar utilizando métodos convencionais.
- Adequação do material: A prensagem a quente é adequada para uma vasta gama de materiais, incluindo cerâmicas e metais, e pode produzir componentes com propriedades mecânicas excepcionais.
Em resumo, o aumento da pressão durante a sinterização oferece múltiplos benefícios, incluindo uma densificação acrescida, propriedades mecânicas melhoradas, tempo de sinterização reduzido e alterações microestruturais favoráveis.Estes efeitos tornam a sinterização assistida por pressão uma técnica valiosa na produção de materiais de alto desempenho.
Tabela de resumo:
Efeito | Descrição |
---|---|
Densificação melhorada | A pressão melhora a fusão das partículas, reduzindo a porosidade e criando materiais mais densos. |
Propriedades mecânicas melhoradas | Aumenta a força, a dureza e a resistência ao desgaste devido a ligações de partículas mais fortes. |
Redução do tempo de sinterização | Reduz o tempo de sinterização, melhorando a eficiência e a consistência das propriedades do material. |
Benefícios microestruturais | Optimiza o tamanho do grão, a distribuição e a forma dos limites para um melhor desempenho. |
Aplicação de prensagem a quente | Combina calor e pressão para materiais difíceis, produzindo componentes de elevado desempenho. |
Desbloqueie o potencial da sinterização assistida por pressão para os seus materiais- contacte-nos hoje para saber mais!