Fornos e calcinadores são equipamentos de processamento térmico utilizados em diversas indústrias, mas atendem a finalidades diferentes e operam em condições distintas. Um forno é usado principalmente para queimar, secar ou endurecer materiais como cerâmica, cimento ou tijolos, geralmente em altas temperaturas. Ele é projetado para manter uma distribuição de calor consistente e é comumente usado na fabricação e construção. Por outro lado, um calcinador é projetado especificamente para calcinação, um processo que envolve o aquecimento de materiais a altas temperaturas para induzir decomposição térmica, transição de fase ou remoção de substâncias voláteis. Os calcinadores são amplamente utilizados em indústrias como produção de cimento, processamento químico e metalurgia. As principais diferenças residem nas aplicações pretendidas, nas faixas de temperatura e nos tipos de alterações químicas ou físicas que facilitam.
Pontos-chave explicados:
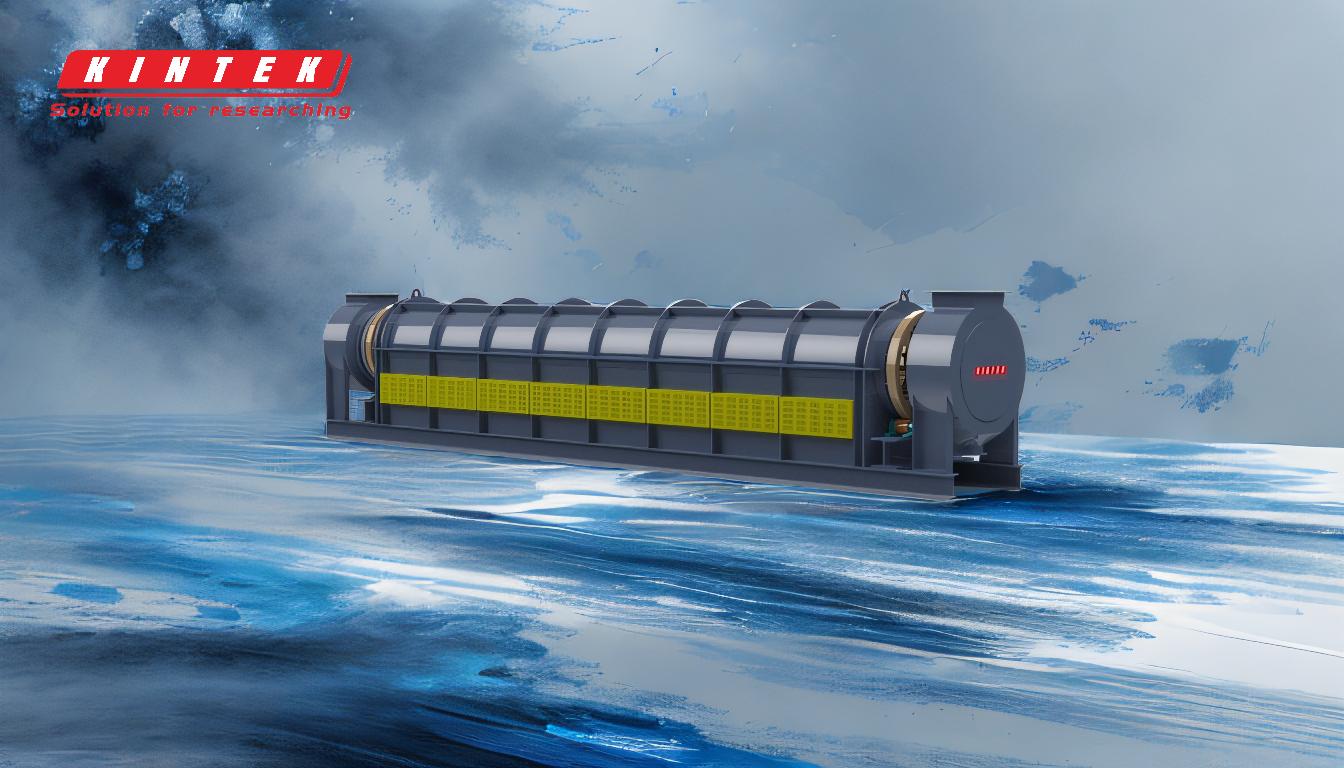
-
Função Primária e Propósito:
- Forno: Os fornos são usados principalmente para processos como queima de cerâmica, secagem de materiais ou endurecimento de substâncias como cimento ou tijolos. Eles são projetados para fornecer calor consistente por longos períodos, garantindo tratamento uniforme dos materiais.
- Calcinador: Os calcinadores são especializados no processo de calcinação, que envolve o aquecimento de materiais a altas temperaturas para eliminar componentes voláteis, induzir decomposição ou causar transições de fase. Isto é crítico em indústrias como a produção de cimento, onde o calcário é calcinado para produzir cal.
-
Faixa de temperatura:
- Forno: Os fornos normalmente operam em altas temperaturas, geralmente variando de 600°C a 1.400°C, dependendo do material que está sendo processado. Por exemplo, fornos cerâmicos podem operar em torno de 1.200°C a 1.400°C.
- Calcinador: Os calcinadores geralmente operam em temperaturas ainda mais altas, muitas vezes excedendo 900°C e às vezes chegando até 1.600°C, para alcançar as alterações químicas necessárias durante a calcinação.
-
Mudanças Químicas e Físicas:
- Forno: Os processos em um forno são frequentemente físicos, como secagem ou sinterização, onde os materiais são fundidos sem alteração química significativa. Por exemplo, na produção de cimento, o forno é usado para sinterizar matérias-primas em clínquer.
- Calcinador: Os calcinadores são projetados para induzir alterações químicas, como decomposição térmica. Por exemplo, na produção de cimento, o calcinador é usado para decompor o carbonato de cálcio (CaCO₃) em óxido de cálcio (CaO) e dióxido de carbono (CO₂).
-
Design e Estrutura:
- Forno: Os fornos são normalmente projetados como cilindros longos e rotativos (fornos rotativos) ou câmaras estacionárias (por exemplo, fornos de túnel). Eles são construídos para garantir uma distribuição uniforme de calor e geralmente são revestidos com materiais refratários para suportar altas temperaturas.
- Calcinador: Os calcinadores também podem ser rotativos ou estacionários, mas são projetados especificamente para lidar com altas temperaturas e reações químicas envolvidas na calcinação. Muitas vezes incluem recursos como pré-aquecedores ou câmaras de combustão secundária para otimizar a eficiência.
-
Aplicativos:
- Forno: Os fornos são amplamente utilizados em indústrias como cerâmica, produção de cimento e metalurgia. Eles são essenciais para processos como queima de cerâmica, produção de clínquer em fábricas de cimento e tratamento térmico de metais.
- Calcinador: Os calcinadores são essenciais em indústrias como produção de cimento, processamento químico e metalurgia. Eles são usados para processos como calcinação de calcário, decomposição de gesso e produção de alumina a partir de bauxita.
-
Diferenças Operacionais:
- Forno: Os fornos são frequentemente operados continuamente ou em lotes, dependendo da aplicação. Requerem controle preciso de temperatura para garantir a qualidade do produto final.
- Calcinador: Os calcinadores normalmente são operados continuamente, especialmente em aplicações industriais de grande escala. Eles exigem um gerenciamento cuidadoso da temperatura e do fluxo de gás para alcançar as reações químicas desejadas.
-
Eficiência Energética:
- Forno: Os fornos são projetados para maximizar a retenção de calor e minimizar a perda de energia, muitas vezes usando revestimentos refratários e materiais de isolamento.
- Calcinador: Os calcinadores são otimizados para eficiência energética incorporando pré-aquecedores e sistemas de recuperação de calor, que reduzem o consumo geral de energia necessário para a calcinação.
Em resumo, embora tanto os fornos como os calcinadores sejam essenciais para o processamento a altas temperaturas, eles diferem significativamente nas suas funções primárias, condições operacionais e aplicações. Os fornos estão mais focados em mudanças físicas como secagem e sinterização, enquanto os calcinadores são especializados em processos químicos como decomposição e transições de fase. Compreender essas diferenças é crucial para selecionar o equipamento certo para necessidades industriais específicas.
Tabela Resumo:
Aspecto | Forno | Calcinador |
---|---|---|
Função Primária | Queima, secagem ou endurecimento de materiais (por exemplo, cerâmica, cimento, tijolos). | Induzindo decomposição térmica, transição de fase ou remoção volátil. |
Faixa de temperatura | 600°C a 1.400°C | 900°C a 1.600°C |
Químico/Físico | Mudanças físicas (por exemplo, secagem, sinterização). | Mudanças químicas (por exemplo, decomposição, transições de fase). |
Projeto | Câmaras rotativas ou estacionárias com revestimentos refratários. | Rotativo ou estacionário com pré-aquecedores/câmaras de combustão para maior eficiência. |
Aplicativos | Cerâmica, produção de cimento, metalurgia. | Produção de cimento, processamento químico, metalurgia. |
Modo Operacional | Processamento contínuo ou em lote. | Normalmente operação contínua. |
Eficiência Energética | Maximiza a retenção de calor com isolamento. | Otimizado com pré-aquecedores e sistemas de recuperação de calor. |
Precisa de ajuda para escolher o equipamento de processamento térmico certo? Contate nossos especialistas hoje para aconselhamento personalizado!