Um forno de cerâmica é um dispositivo de aquecimento especializado, concebido para atingir e manter temperaturas extremamente elevadas, normalmente utilizado para processos como a cozedura, fusão ou sinterização de materiais cerâmicos. Estes fornos são construídos com componentes capazes de suportar calor intenso, garantindo um controlo preciso da temperatura e uma distribuição uniforme do calor. Os principais componentes incluem uma câmara de cozedura ou de aquecimento, elementos de aquecimento, isolamento e um sistema de controlo eletrónico. Os fornos de cerâmica são amplamente utilizados em indústrias como o fabrico de cerâmica, metalurgia e investigação laboratorial, onde o processamento a alta temperatura é essencial. Existem em vários modelos, incluindo fornos de mufla, fornos de tubo e fornos de cadinho, cada um adaptado a aplicações específicas.
Pontos-chave explicados:
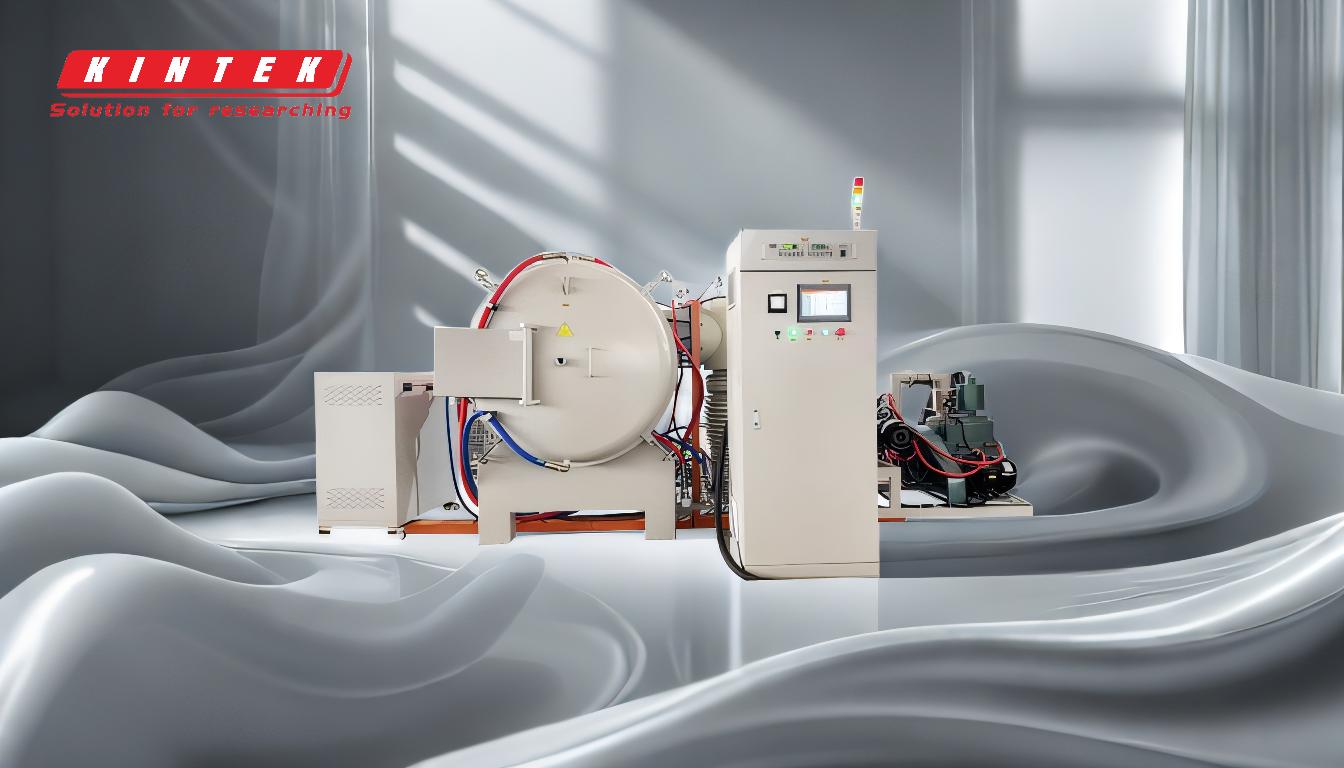
-
Definição e finalidade de um forno de cerâmica:
- Um forno de cerâmica é um dispositivo de aquecimento a alta temperatura utilizado para processos como a cozedura de cerâmica, a fusão de metais ou a sinterização de materiais.
- Foi concebido para atingir e manter temperaturas que variam entre 1200°C e mais de 1500°C, consoante a aplicação.
- Estes fornos são essenciais em indústrias como a cerâmica, a metalurgia e a investigação laboratorial, onde o aquecimento preciso e uniforme é fundamental.
-
Componentes principais de um forno de cerâmica:
-
Câmara de fiação/aquecimento:
- A câmara é o componente central onde os materiais são colocados para aquecimento.
- É normalmente feito de materiais resistentes a altas temperaturas, como a cerâmica (por exemplo, sílica, alumina), para suportar o calor extremo.
- Em alguns modelos, a câmara é cilíndrica (forno tubular) ou retangular (forno de mufla).
-
Elementos de aquecimento:
- Os elementos de aquecimento, muitas vezes feitos de materiais refractários como o carboneto de silício ou o dissiliceto de molibdénio, geram calor.
- Estes elementos estão embutidos nas paredes do forno ou em redor da câmara para garantir uma distribuição uniforme do calor.
-
Isolamento:
- Os materiais de isolamento, como a fibra cerâmica ou os tijolos refractários, são utilizados para reter o calor e melhorar a eficiência energética.
- Também protegem o invólucro externo do calor excessivo.
-
Sistema de controlo eletrónico:
- Um controlador PID (Proporcional-Integral-Derivativo) baseado em microprocessador regula a temperatura com elevada precisão.
- O sistema inclui sensores (por exemplo, termopares) para monitorização e feedback da temperatura em tempo real.
- Caraterísticas como temporizadores, interruptores de segurança e ecrãs LED aumentam a facilidade de utilização e a segurança.
-
Câmara de fiação/aquecimento:
-
Tipos de fornos de cerâmica:
-
Forno de mufla:
- Possui uma câmara interna isolada do ambiente externo, evitando a contaminação.
- Normalmente utilizado para aplicações que requerem um aquecimento limpo, como a cozedura de cerâmica ou o ensaio de cinzas.
-
Forno de tubos:
- Consiste numa câmara de aquecimento cilíndrica rodeada por bobinas de aquecimento embebidas numa matriz cerâmica.
- Ideal para processos que requerem um aquecimento uniforme, como a síntese de materiais ou o tratamento térmico.
-
Forno de cadinho:
- Inclui um cadinho (feito de grafite, argila ou carboneto de silício) colocado dentro de uma câmara de aquecimento.
- Utilizado para fundir metais ou outros materiais a altas temperaturas.
-
Forno de porcelana:
- Especificamente concebido para a cozedura de porcelana dentária ou industrial.
- Equipado com uma bomba de vácuo para evitar a opacidade e garantir resultados de alta qualidade.
-
Forno de mufla:
-
Aplicações dos fornos de cerâmica:
-
Fabrico de cerâmica:
- Utilizado para cozer cerâmica, azulejos e outros produtos cerâmicos para obter a dureza e a durabilidade desejadas.
-
Metalurgia:
- Utilizado para a fusão de metais, tratamento térmico e sinterização de metais em pó.
-
Investigação laboratorial:
- Utilizado na ciência dos materiais para experiências que requerem ambientes controlados a alta temperatura.
-
Indústria dentária:
- Os fornos de porcelana são utilizados para criar próteses dentárias como coroas e pontes.
-
Fabrico de cerâmica:
-
Principais caraterísticas e vantagens:
-
Capacidade para altas temperaturas:
- Pode atingir temperaturas até 1530°C ou superiores, adequadas a uma vasta gama de materiais.
-
Controlo de precisão:
- Os controladores PID avançados garantem uma regulação e uniformidade precisas da temperatura.
-
Durabilidade:
- Construído com materiais refractários que suportam calor extremo e ciclos térmicos.
-
Caraterísticas de segurança:
- Inclui interruptores de segurança, orifícios de libertação de gás e isolamento para evitar acidentes e garantir a segurança do operador.
-
Versatilidade:
- Disponível em vários modelos para satisfazer os requisitos de aplicações específicas.
-
Capacidade para altas temperaturas:
Em resumo, um forno de cerâmica é uma ferramenta altamente especializada e versátil, concebida para o processamento a alta temperatura. A sua construção robusta, o controlo preciso da temperatura e a sua adaptabilidade tornam-no indispensável em indústrias que vão desde a cerâmica e a metalurgia à investigação laboratorial e às aplicações dentárias.
Quadro de resumo:
Aspeto | Detalhes |
---|---|
Definição | Dispositivo de alta temperatura para queima, fusão ou sinterização de materiais. |
Gama de temperaturas | 1200°C a 1530°C ou superior. |
Componentes principais | Câmara de combustão, elementos de aquecimento, isolamento, sistema de controlo eletrónico. |
Tipos | Fornos de mufla, de tubos, de cadinho e de porcelana. |
Aplicações | Fabrico de cerâmica, metalurgia, investigação laboratorial, próteses dentárias. |
Caraterísticas principais | Capacidade para altas temperaturas, controlo de precisão, durabilidade, segurança e versatilidade. |
Descubra como um forno de cerâmica pode elevar os seus processos de alta temperatura- contacte-nos hoje para uma orientação especializada!