O processo de sinterização é um passo crítico no fabrico, particularmente na metalurgia do pó e na cerâmica, em que os materiais são transformados em estruturas densas e coesas sem atingirem os seus pontos de fusão.O processo é normalmente dividido em três fases principais: composição do pó de sinterização, compactação do pó na forma desejada e aquecimento do material compactado num forno de sinterização para facilitar a ligação e a densificação das partículas.Cada fase desempenha um papel vital na obtenção das propriedades mecânicas, integridade estrutural e precisão dimensional do produto final.A compreensão destas fases ajuda a otimizar o processo de sinterização para várias aplicações industriais.
Explicação dos pontos-chave:
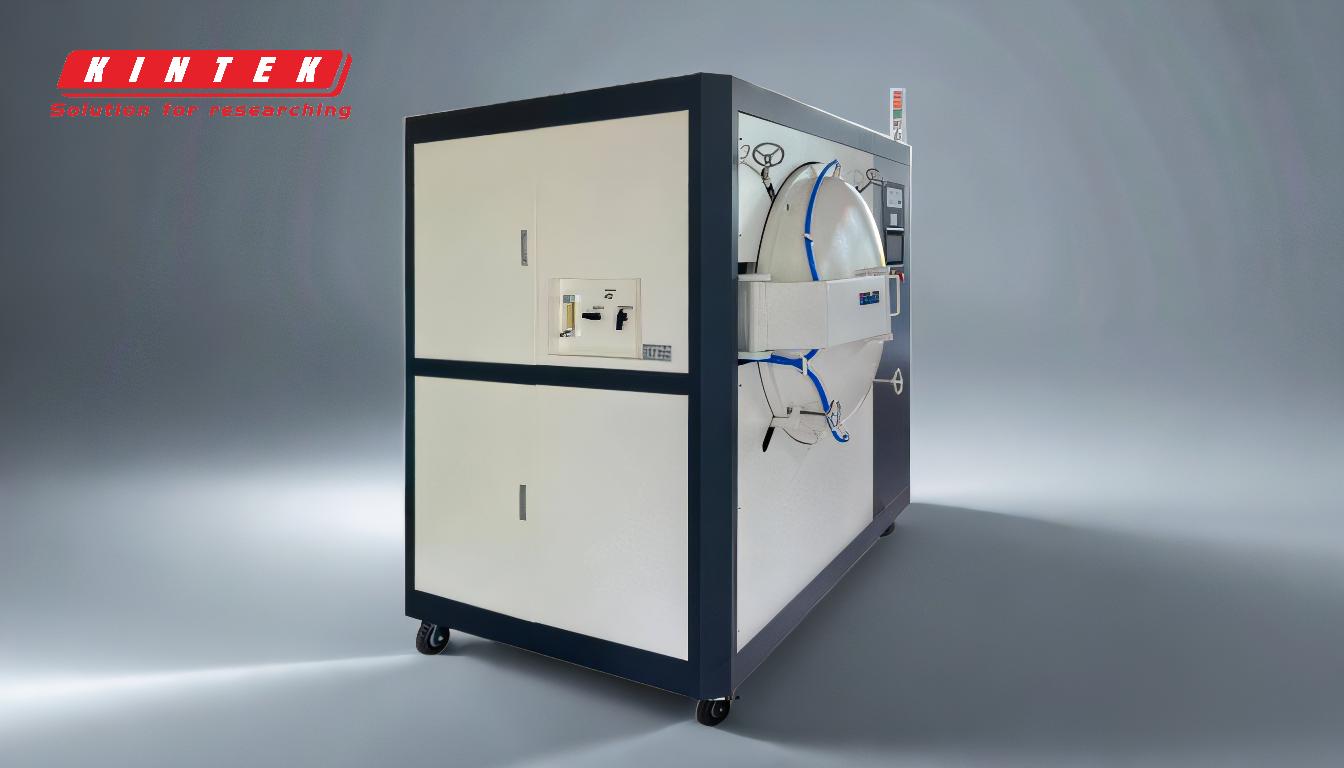
-
Composição do pó de sinterização:
- Esta fase inicial consiste em selecionar e misturar as matérias-primas, frequentemente sob a forma de pó, para criar uma mistura homogénea.A composição pode incluir materiais primários, elementos de liga e aditivos para obter propriedades específicas.
- O objetivo é assegurar a uniformidade da mistura de pós, que é crucial para obter resultados consistentes nas fases subsequentes.São utilizadas técnicas e equipamentos de mistura adequados para evitar a segregação ou a distribuição desigual dos componentes.
- Por exemplo, na sinterização de metais, os metais em pó são misturados com elementos de liga para aumentar a força, a resistência à corrosão ou outras caraterísticas desejadas.
-
Compactação do pó:
- Uma vez preparado o pó, este é compactado na forma desejada utilizando ferramentas ou moldes de alta pressão.Este passo é essencial para eliminar os vazios e assegurar que o material tem resistência verde suficiente para manter a sua forma durante o manuseamento e a sinterização.
- O processo de compactação pode ser efectuado à temperatura ambiente ou sob condições de aquecimento, dependendo do material e da aplicação.A pressão aplicada deve ser cuidadosamente controlada para obter uma densidade uniforme em toda a peça compactada.
- Esta fase envolve frequentemente a utilização de prensas hidráulicas ou mecânicas, e a conceção do molde ou matriz deve ter em conta qualquer contração que possa ocorrer durante a sinterização.
-
Aquecimento num forno de sinterização:
- O material compactado é depois submetido a um aquecimento controlado num forno de sinterização .A temperatura é cuidadosamente regulada para facilitar a ligação das partículas através da difusão sem causar a fusão completa.
- Durante esta fase, as partículas sofrem uma formação de pescoço, onde começam a unir-se nos pontos de contacto, levando à densificação e à redução da porosidade.A duração e a temperatura do aquecimento dependem do material e das propriedades desejadas.
- Após a sinterização, o produto é arrefecido gradualmente para solidificar numa estrutura rígida e coesa.Este processo de arrefecimento é fundamental para evitar tensões térmicas e garantir a estabilidade dimensional.
Ao compreender e otimizar estas três fases, os fabricantes podem produzir produtos sinterizados de alta qualidade com propriedades personalizadas para várias aplicações, desde componentes automóveis a cerâmicas avançadas.
Tabela de resumo:
Fase | Descrição | Considerações fundamentais |
---|---|---|
Composição do pó | Seleção e mistura de matérias-primas para criar uma mistura homogénea. | A uniformidade, as técnicas de mistura corretas e a prevenção da segregação são cruciais. |
Compactação do pó | Pressionar o pó numa forma desejada utilizando ferramentas ou moldes de alta pressão. | A pressão controlada, a densidade uniforme e o controlo da retração são essenciais. |
Aquecimento num forno | Aquecimento do material compactado num forno de sinterização para unir as partículas. | A temperatura controlada, a formação do pescoço e o arrefecimento gradual garantem a integridade estrutural. |
Optimize o seu processo de sinterização hoje- contacte os nossos especialistas para soluções à medida!