A deposição física de vapor (PVD) é uma técnica de revestimento amplamente utilizada para criar películas de proteção com propriedades anticorrosivas e resistentes ao desgaste.No entanto, apresenta várias desvantagens que podem afetar a sua eficiência, custo e aplicabilidade.Estas incluem o elevado custo de capital do equipamento, taxas de deposição lentas, limitações no revestimento de geometrias complexas e a necessidade de operadores qualificados e sistemas de arrefecimento especializados.Além disso, a PVD é um processo de linha de visão, o que dificulta o revestimento de cortes inferiores e de superfícies com caraterísticas complexas.Estes factores, em conjunto, tornam o PVD um processo complexo e dispendioso, particularmente para aplicações de grande escala ou intrincadas.
Pontos-chave explicados:
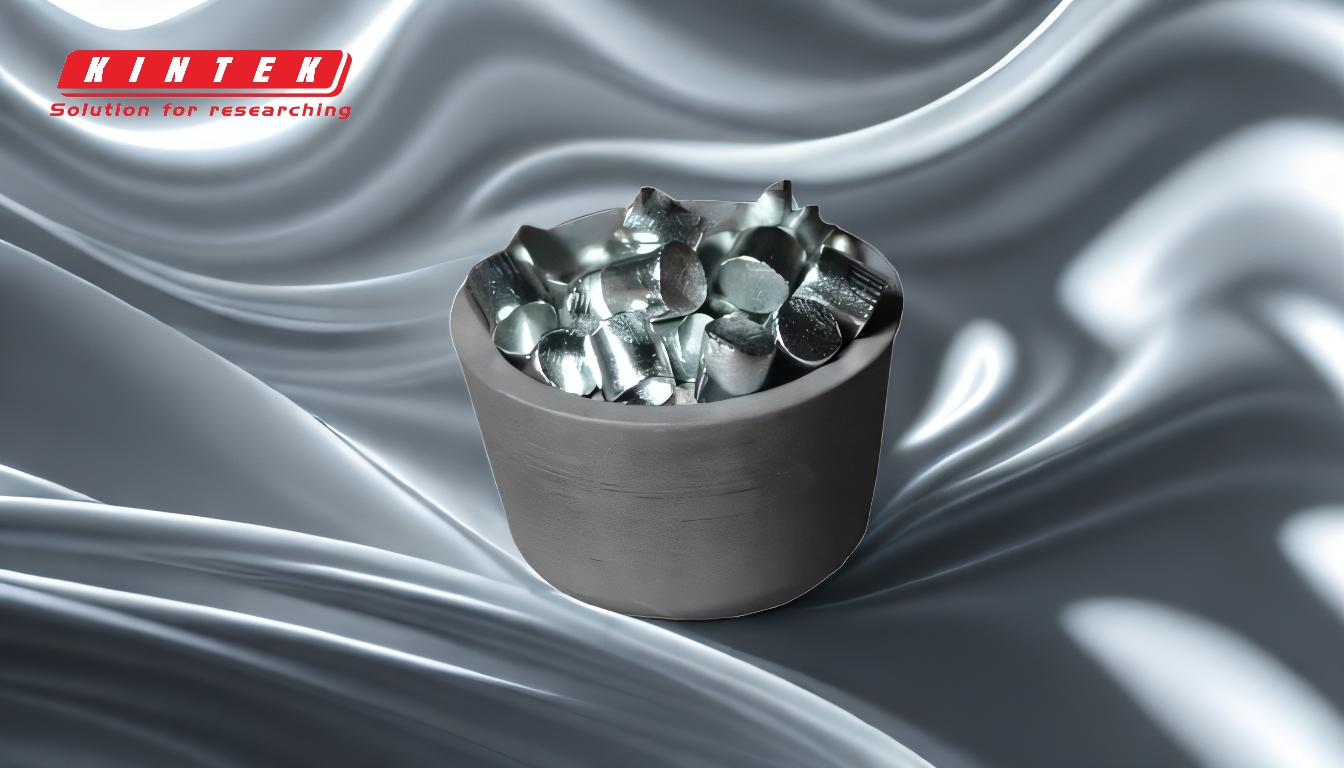
-
Custo de capital elevado:
- A PVD requer equipamento complexo e dispendioso, incluindo câmaras de vácuo e sistemas de alta temperatura.O investimento inicial para a criação de uma instalação de PVD é substancial, o que pode constituir um obstáculo para as empresas mais pequenas ou com orçamentos limitados.
- A necessidade de sistemas de arrefecimento especializados para gerir o calor gerado durante o processo aumenta ainda mais o custo.
-
Taxas de deposição lentas:
- Em comparação com outros processos de deposição de revestimentos, a PVD é relativamente lenta.Este facto pode ser uma desvantagem significativa em indústrias onde é essencial um elevado rendimento.
- A taxa lenta de deposição também pode levar a tempos de produção mais longos, o que pode não ser viável para o fabrico em grande escala ou projectos sensíveis ao tempo.
-
Limitação da linha de visão:
- A PVD é uma técnica de linha de visão, o que significa que só pode revestir superfícies que estejam diretamente expostas à fonte de vapor.Este facto dificulta o revestimento de cortes inferiores, reentrâncias e outras geometrias complexas.
- Como resultado, o PVD é menos adequado para aplicações em que é necessário um revestimento uniforme de superfícies complexas ou ocultas.
-
Requisitos de alta temperatura e vácuo:
- Os processos PVD requerem frequentemente temperaturas extremamente elevadas e condições de vácuo, o que exige operadores qualificados e equipamento especializado.
- As temperaturas elevadas podem também levar à degradação do material ou a alterações nas propriedades do substrato, o que pode não ser desejável em todas as aplicações.
-
Necessidade de operadores qualificados:
- O funcionamento do equipamento PVD requer um elevado nível de especialização devido à natureza complexa do processo e à necessidade de manter condições precisas (por exemplo, níveis de vácuo, controlo da temperatura).
- A necessidade de pessoal qualificado pode aumentar os custos de mão de obra e tornar o processo menos acessível a empresas sem pessoal experiente.
-
Requisitos do sistema de arrefecimento:
- Os processos de PVD geram um calor significativo, sendo necessária a utilização de sistemas de arrefecimento para dissipar este calor e manter a estabilidade do processo.
- Os sistemas de arrefecimento aumentam a complexidade geral e o custo da instalação de PVD, bem como as despesas operacionais.
-
Desperdício de material e destruição da cor:
- A PVD pode destruir agressivamente as cores, levando ao desperdício de material e afectando potencialmente as propriedades estéticas do produto revestido.
- Isto pode ser uma desvantagem significativa em indústrias onde a consistência da cor e a eficiência do material são críticas.
-
Aplicabilidade limitada a geometrias complexas:
- Devido à sua natureza de linha de visão, a PVD não é adequada para o revestimento de substratos com geometrias complexas ou caraterísticas ocultas.
- Esta limitação pode restringir a utilização da PVD em determinadas aplicações, como as que requerem o revestimento uniforme de peças complexas ou componentes com cavidades internas.
Em resumo, embora o PVD ofereça várias vantagens em termos de produção de revestimentos duráveis e de alta qualidade, as suas desvantagens - tais como custos elevados, taxas de deposição lentas e limitações no revestimento de geometrias complexas - podem torná-lo menos adequado para determinadas aplicações.Estes factores devem ser cuidadosamente considerados ao decidir se o PVD é o método de revestimento adequado para um determinado projeto.
Tabela de resumo:
Desvantagem | Descrição |
---|---|
Custo de capital elevado | Requer equipamento e sistemas de arrefecimento dispendiosos, tornando a instalação inicial dispendiosa. |
Taxas de deposição lentas | Mais lentas em comparação com outros métodos de revestimento, afectando a eficiência da produção. |
Limitação da linha de visão | Não pode revestir eficazmente cortes inferiores ou geometrias complexas. |
Necessidades de alta temperatura e vácuo | Exige operadores qualificados e equipamento especializado para condições precisas. |
Necessidade de operadores qualificados | Aumenta os custos de mão de obra e limita a acessibilidade das pequenas empresas. |
Requisitos do sistema de arrefecimento | Acrescenta complexidade e despesas operacionais ao processo. |
Desperdício de material e perda de cor | Pode destruir cores e levar à ineficiência do material. |
Aplicabilidade limitada a peças complexas | Inadequado para revestimento uniforme de caraterísticas complexas ou ocultas. |
Está a considerar a PVD para o seu projeto? Contacte os nossos especialistas para determinar se é a solução certa para as suas necessidades!