O endurecimento é um processo usado para aumentar a dureza e a resistência dos materiais, normalmente metais, através de tratamento térmico ou outros métodos. Embora ofereça vantagens significativas, como maior resistência ao desgaste e durabilidade, também apresenta várias desvantagens. Estes incluem aumento da fragilidade, redução da ductilidade, potencial de fissuração e limitações na seleção de materiais. Além disso, o processo pode ser caro, demorado e pode introduzir tensões residuais que afetam o desempenho do material. Compreender essas desvantagens é crucial para tomar decisões informadas na seleção e aplicação de materiais.
Pontos-chave explicados:
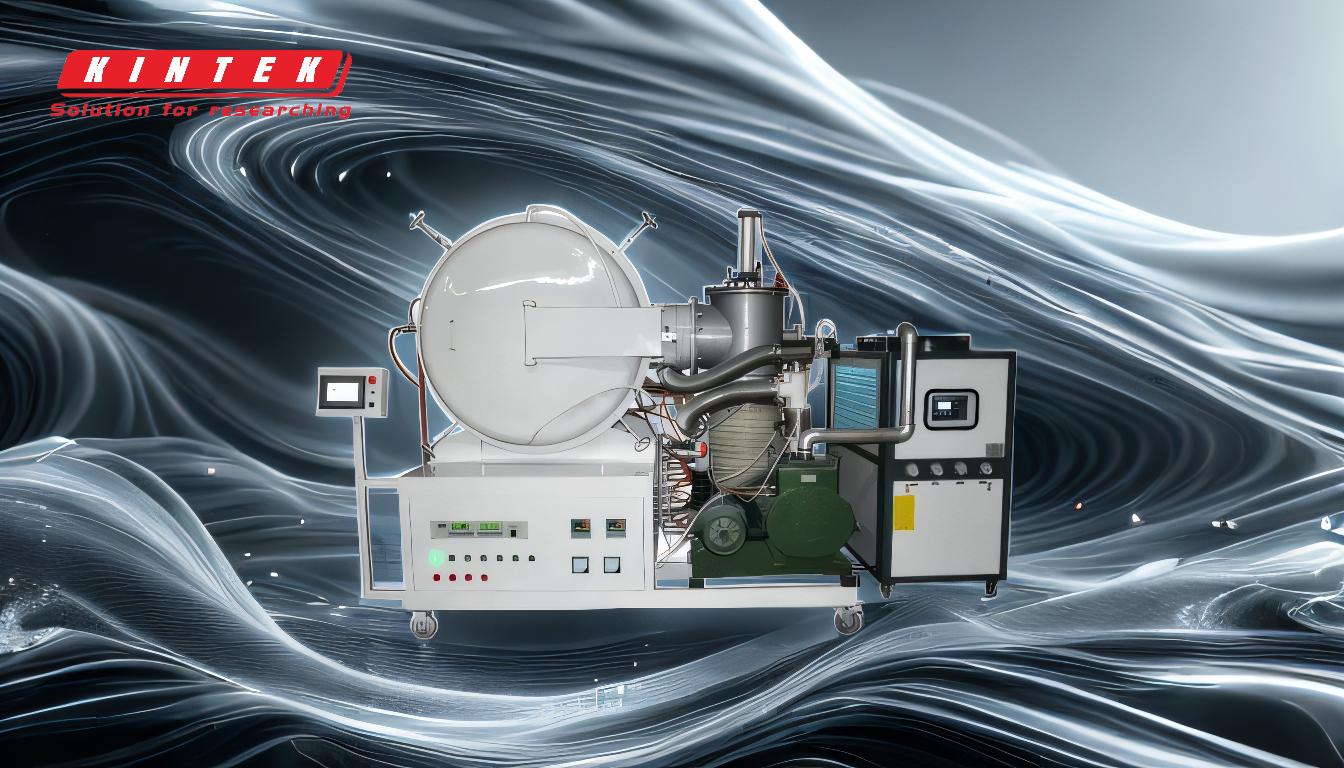
-
Maior fragilidade:
- O endurecimento muitas vezes leva a um aumento significativo na fragilidade, tornando o material mais propenso a falhas repentinas sob impacto ou tensão.
- Isto é particularmente problemático em aplicações onde o material está sujeito a cargas dinâmicas ou choques.
-
Ductilidade reduzida:
- O processo de endurecimento normalmente reduz a ductilidade do material, o que significa que ele se torna menos capaz de sofrer deformação plástica sem quebrar.
- Esta redução na ductilidade pode limitar a capacidade do material de absorver energia, tornando-o inadequado para aplicações que exigem flexibilidade.
-
Potencial para rachaduras:
- Durante o processo de endurecimento, especialmente em métodos de resfriamento rápido como a têmpera, existe um alto risco de trincas devido a tensões térmicas.
- As fissuras podem comprometer a integridade estrutural do material, levando à falha prematura.
-
Tensões residuais:
- O endurecimento pode introduzir tensões residuais no material, o que pode levar à distorção ou empenamento.
- Estas tensões também podem reduzir a vida à fadiga do material, tornando-o mais suscetível a falhas sob carregamento cíclico.
-
Limitações materiais:
- Nem todos os materiais são adequados para endurecimento. Algumas ligas e metais podem não responder bem ao processo, limitando a gama de materiais que podem ser efetivamente endurecidos.
- Isto pode restringir as opções de design e exigir o uso de materiais ou tratamentos alternativos.
-
Considerações sobre custo e tempo:
- O processo de endurecimento pode ser caro, exigindo equipamentos especializados e ambientes controlados.
- Também é demorado, o que pode aumentar os prazos de produção e os custos gerais.
-
Dureza da superfície versus propriedades do núcleo:
- O endurecimento geralmente resulta em uma superfície muito mais dura que o núcleo do material. Essa discrepância pode levar a problemas como delaminação ou fragmentação sob certas condições.
- Equilibrar a dureza superficial com as propriedades do núcleo é uma consideração crítica no projeto e aplicação de materiais endurecidos.
-
Preocupações ambientais e de segurança:
- O processo de endurecimento, principalmente aqueles que envolvem altas temperaturas e tratamentos químicos, pode representar riscos ambientais e de segurança.
- O manuseio e descarte adequados de produtos químicos, bem como o cumprimento dos protocolos de segurança, são essenciais para mitigar esses riscos.
Em resumo, embora o endurecimento ofereça benefícios significativos em termos de resistência do material e resistência ao desgaste, é essencial considerar cuidadosamente as suas desvantagens. Estes incluem aumento da fragilidade, redução da ductilidade, potencial de fissuração, tensões residuais, limitações de material, considerações de custo e tempo, discrepâncias de propriedades do núcleo superficial e preocupações ambientais e de segurança. A compreensão destas desvantagens permite uma melhor tomada de decisão na seleção e aplicação de materiais, garantindo que os benefícios do endurecimento sejam maximizados e minimizando os seus impactos negativos.
Tabela Resumo:
Desvantagem | Descrição |
---|---|
Maior fragilidade | Maior risco de falha repentina sob estresse ou impacto. |
Ductilidade reduzida | Diminuição da capacidade de deformar sem quebrar, limitando a flexibilidade. |
Potencial para rachaduras | Alto risco de fissuras devido a tensões térmicas durante o resfriamento rápido. |
Tensões residuais | Introduz tensões internas, levando à distorção ou à redução da vida útil em fadiga. |
Limitações materiais | Nem todos os materiais podem ser endurecidos, restringindo as opções de design. |
Considerações sobre custo e tempo | Processo caro e demorado que requer equipamento especializado. |
Discrepância Superfície-Núcleo | Superfície mais dura em comparação com o núcleo, arriscando delaminação ou lascamento. |
Riscos Ambientais e de Segurança | Altas temperaturas e produtos químicos representam preocupações ambientais e de segurança. |
Precisa de ajuda para selecionar o material ou processo certo? Contate nossos especialistas hoje para soluções personalizadas!