Introdução à tecnologia CVD
Definição e importância
A deposição química em fase vapor (CVD) é uma tecnologia fundamental de deposição de películas finas, desempenhando um papel crucial no fabrico de semicondutores e numa miríade de outras indústrias. Esta tecnologia permite a deposição precisa e controlada de películas finas em vários substratos, o que é essencial para o fabrico de componentes electrónicos, revestimentos ópticos e camadas protectoras.
No fabrico de semicondutores, a CVD é indispensável para criar películas uniformes e de alta qualidade que melhoram o desempenho e a fiabilidade dos circuitos integrados. A capacidade de depositar materiais com propriedades específicas, como a condutividade, o isolamento e a transparência ótica, faz da CVD uma ferramenta essencial na produção de dispositivos microelectrónicos avançados.
Para além dos semicondutores, a CVD encontra aplicações extensivas na tecnologia dos ecrãs, onde é utilizada para depositar películas de óxido de índio e estanho (ITO) e películas de cobre, melhorando a funcionalidade e a durabilidade dos dispositivos de visualização. Além disso, a CVD é utilizada na produção de revestimentos ópticos para lentes e espelhos, bem como em revestimentos anti-corrosão para superfícies metálicas, demonstrando a sua versatilidade em diversos domínios.
A importância da CVD reside não só nas suas vastas aplicações, mas também na sua capacidade de produzir películas com uma uniformidade, adesão e controlabilidade excepcionais. Estes atributos fazem da CVD uma tecnologia indispensável para o avanço de várias indústrias e para a inovação na ciência dos materiais.
Princípio de funcionamento da CVD
Processo de reação química
Durante o processo de Deposição Química em Vapor (CVD), a formação de películas finas depende de uma reação química controlada. Inicialmente, os precursores gasosos, que são as matérias-primas para a película desejada, são introduzidos na câmara de reação. Estes precursores são normalmente compostos voláteis que podem ser facilmente vaporizados. Uma vez dentro da câmara, estes gases são sujeitos a aquecimento, muitas vezes na ordem das várias centenas a milhares de graus Celsius, dependendo do precursor específico e das propriedades da película pretendida.
O processo de aquecimento é crucial, uma vez que fornece a energia necessária para que as moléculas de gás ultrapassem as suas barreiras de energia de ativação, permitindo-lhes reagir. À medida que a temperatura aumenta, os precursores gasosos decompõem-se e reagem entre si ou com a superfície do substrato. Esta reação ocorre tipicamente na superfície do substrato, onde os precursores se adsorvem e depois sofrem nova decomposição ou combinação. Os produtos resultantes destas reacções incluem o material de película desejado, que se deposita no substrato, e subprodutos, que são normalmente gasosos e são eliminados do sistema.
Por exemplo, na deposição de películas de silício, um precursor comum é o silano (SiH4). Quando aquecido, o silano decompõe-se em silício e hidrogénio gasoso. Os átomos de silício depositam-se então no substrato, formando uma película contínua, enquanto o gás hidrogénio é evacuado da câmara de reação. Este exemplo ilustra a natureza dinâmica do processo CVD, em que o controlo preciso da temperatura e dos caudais de precursores é essencial para obter a qualidade e uniformidade desejadas da película.
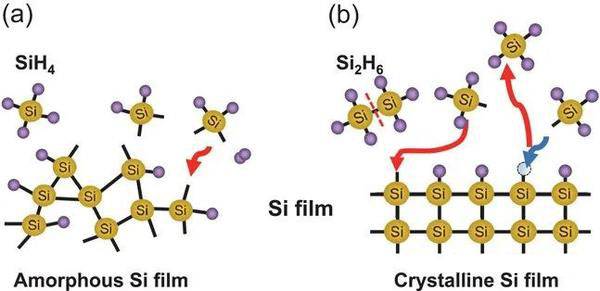
O processo de reação química em CVD não se limita a simples decomposições; pode também envolver reacções complexas como a oxidação, a nitridação ou a formação de materiais compostos. Estas reacções são frequentemente facilitadas pela presença de gases reagentes adicionais, como o oxigénio ou o azoto, que são introduzidos na câmara para modificar as propriedades da película. Por exemplo, ao depositar películas de dióxido de silício (SiO2), o silano reage com o oxigénio para formar a camada de óxido.
Exemplo de reação
No contexto da Deposição Química em Vapor (CVD), uma das principais reacções envolve a decomposição do triclorossilano (SiHCl₃). Este processo é fundamental para a formação de películas finas, nomeadamente no fabrico de semicondutores. Quando o SiHCl₃ é aquecido, sofre uma transformação química complexa. O material de origem do silício, SiHCl₃, decompõe-se em silício elementar, que depois se deposita no substrato. Simultaneamente, os gases cloro (Cl₂) e ácido clorídrico (HCl) são libertados como subprodutos. Estes gases são normalmente exauridos da câmara de reação, assegurando que não interferem com o processo de deposição.
Esta reação exemplifica o princípio fundamental da CVD, em que os gases precursores são convertidos em películas sólidas através de reacções químicas controladas. A decomposição do SiHCl₃ não só fornece o silício necessário para a formação da película, como também ilustra a importância da gestão de gases na manutenção de um ambiente de deposição limpo e eficiente. Os gases subprodutos, Cl₂ e HCl, são cruciais para monitorizar e controlar, uma vez que a sua presença pode afetar a qualidade e a uniformidade da película depositada.
Classificação da CVD
CVD térmica
A Deposição Química em Vapor (CVD) térmica envolve o aquecimento de gases precursores a uma temperatura elevada, normalmente acima de 700°C, dentro de uma câmara de reação. Esta temperatura elevada é crucial para promover a decomposição dos gases precursores, que depois se depositam no substrato para formar uma película fina. O processo baseia-se na energia térmica para conduzir as reacções químicas necessárias à formação da película, assegurando que a película depositada apresenta propriedades melhoradas, tais como uma melhor cristalinidade, maior densidade e taxas de deposição mais rápidas.
Na CVD térmica, os reagentes gasosos são frequentemente transportados para a câmara do reator por um gás inerte como o azoto, o que ajuda a manter um ambiente controlado. As temperaturas elevadas não só facilitam a decomposição dos precursores, como também permitem reacções que, de outro modo, seriam impossíveis a temperaturas mais baixas. No entanto, estas temperaturas elevadas podem conduzir a inconvenientes como a formação de tensões na película, taxas de difusão mais elevadas de elementos do substrato para a película e potencial degradação do próprio substrato.
Vantagens | Desvantagens |
---|---|
Taxa de deposição melhorada | Formação de tensões |
Melhoria da cristalinidade | Taxas de difusão mais elevadas |
Maior densidade de película | Degradação do substrato |
A CVD térmica é particularmente vantajosa no fabrico de semicondutores, onde é utilizada para depositar películas finas como o dióxido de silício, o nitreto de silício e o polissilício em bolachas de silício. Estas películas são essenciais para o fabrico de circuitos integrados e outros dispositivos electrónicos. Apesar das suas vantagens, a CVD térmica exige uma gestão cuidadosa da temperatura e das taxas de fornecimento de precursores para otimizar o processo de deposição e atenuar os potenciais inconvenientes.
CVD melhorado por plasma (PECVD)
A Deposição de Vapor Químico com Plasma (PECVD) é uma variante especializada da Deposição de Vapor Químico (CVD) que utiliza o plasma para aumentar a taxa de reação e controlar meticulosamente o processo de deposição. Ao contrário dos métodos tradicionais de CVD, que dependem apenas da energia térmica para decompor os gases precursores, o PECVD utiliza o plasma para ativar os gases reactivos, facilitando assim a deposição a temperaturas significativamente mais baixas, normalmente entre 100 e 600 °C.
No PECVD, o plasma actua como um catalisador, decompondo os precursores reactivos nos seus átomos ou moléculas constituintes, que depois reagem e se depositam na superfície do substrato. Esta decomposição assistida por plasma permite a deposição de várias películas, incluindo silício (Si), dióxido de silício (SiO2), nitreto de silício, oxinitreto de silício e carboneto de silício, a temperaturas tão baixas como 200-350 °C. Esta gama de temperaturas mais baixas é particularmente vantajosa para aplicações que envolvam materiais sensíveis à temperatura, como o alumínio, em que temperaturas mais elevadas poderiam comprometer a integridade do substrato.
O processo PECVD é frequentemente efectuado num sistema de plasma de placas paralelas, acoplado capacitivamente. Nesta configuração, o substrato é posicionado sobre um elétrodo ligado à terra, enquanto o plasma é gerado entre dois eléctrodos. Os gases utilizados no PECVD podem variar em função das propriedades desejadas para a película, sendo os gases mais comuns o silano (SiH4), o óxido nitroso (N2O), o amoníaco (NH3), o hélio (He), o árgon (Ar), o trifluoreto de azoto (NF3) e a fosfina (PH3). Cada gás desempenha um papel específico no processo de deposição, contribuindo para a formação da película desejada.
Uma das principais especificações técnicas do PECVD é a sua capacidade de funcionar a temperaturas inferiores a 540 °C, tornando-o adequado para uma vasta gama de substratos. A câmara de processo está normalmente equipada com várias câmaras de gás, tais como câmaras de silano (A + C) e uma câmara de TEOS (tetraetilortosilicato) (B), cada uma concebida para lidar com diferentes misturas de gás e requisitos de deposição. Esta conceção modular permite uma maior flexibilidade e controlo do processo de deposição, garantindo a produção de películas de alta qualidade com propriedades precisas.
CVD de metais orgânicos (MOCVD)
A Deposição de Vapor Químico Orgânico de Metal (MOCVD) é uma técnica avançada de crescimento epitaxial que utiliza compostos orgânicos de metal como gases precursores para a deposição de películas de metal e semicondutores. Este método é particularmente notável pela sua capacidade de fazer crescer uma vasta gama de semicondutores compostos, incluindo materiais Ⅲ-V e Ⅱ-VI, bem como as suas soluções sólidas multicamadas.
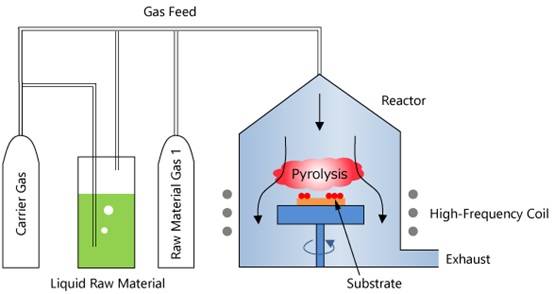
Principais caraterísticas do MOCVD
-
Materiais de origem: O MOCVD emprega compostos orgânicos de elementos dos grupos III e II, juntamente com hidretos de elementos dos grupos V e VI, como os principais materiais de origem para o crescimento de cristais. Estes materiais são introduzidos na câmara de reação sob a forma gasosa, onde sofrem decomposição térmica para formar camadas finas de cristal único no substrato.
-
Controlo de precisão: Uma das vantagens significativas do MOCVD é o controlo preciso da composição e da concentração de dopantes das películas depositadas. Esta precisão é conseguida através da regulação do caudal e do tempo de ativação/desativação dos precursores gasosos, permitindo o crescimento de materiais em camadas finas e ultra-finas com elevada precisão.
-
Comutação rápida: O caudal de gás relativamente rápido dentro da câmara de reação permite alterações rápidas na composição e na concentração de dopante dos múltiplos compostos. Esta capacidade de comutação rápida reduz a probabilidade de efeitos de memória, facilitando a criação de interfaces íngremes e tornando o MOCVD ideal para o crescimento de heteroestruturas, super-redes e materiais de poços quânticos.
Vantagens em relação a outras técnicas epitaxiais
Em comparação com outros métodos de crescimento epitaxial, o MOCVD oferece várias vantagens distintas:
Vantagem | Descrição |
---|---|
Controlo de componentes | O estado gasoso dos precursores permite um controlo preciso dos componentes, da concentração de dopantes e da espessura da camada epitaxial. |
Ajustes rápidos | Mudanças rápidas nas taxas de fluxo de gás permitem ajustes rápidos na composição do composto, reduzindo os efeitos de memória e melhorando a qualidade da interface. |
Versatilidade | Adequado para uma ampla gama de semicondutores compostos, incluindo materiais Ⅲ-V e Ⅱ-VI, tornando-o altamente versátil para várias aplicações. |
Aplicações de CVD
Fabrico de semicondutores
No fabrico de semicondutores, a Deposição Química de Vapor (CVD) desempenha um papel fundamental na criação de materiais avançados que melhoram o desempenho e a fiabilidade dos dispositivos. O processo envolve a deposição de várias películas, incluindo silicidas, películas de nitreto e películas metálicas, cada uma delas adaptada a aplicações específicas na indústria de semicondutores.
Silicetos
Os silicetos, formados pela reação do silício com metais, são cruciais para reduzir a resistência de contacto e melhorar a eficiência dos dispositivos semicondutores. São normalmente utilizados em eléctrodos de porta, interligações e almofadas de contacto. Por exemplo, o siliceto de tungsténio (WSi₂) é frequentemente utilizado na tecnologia CMOS devido à sua baixa resistividade e estabilidade térmica.
Películas de nitreto
As películas de nitreto, como o nitreto de silício (Si₃N₄), têm múltiplas finalidades no fabrico de semicondutores. Actuam como barreiras de difusão, impedindo a migração de dopantes e impurezas, e como camadas de passivação, protegendo o dispositivo de factores ambientais. Além disso, as películas de nitreto são parte integrante da formação de condensadores em dispositivos DRAM, assegurando uma elevada capacitância e baixas correntes de fuga.
Filmes metálicos
As películas de metal, incluindo alumínio (Al) e cobre (Cu), são essenciais para criar interligações que facilitam o fluxo de sinais eléctricos nos circuitos integrados. O cobre, em particular, é preferido pela sua baixa resistividade e capacidade de reduzir o consumo de energia e a geração de calor. A utilização de CVD na deposição destas películas metálicas assegura uma cobertura uniforme e uma excelente aderência, essenciais para manter a integridade e o desempenho dos dispositivos semicondutores.
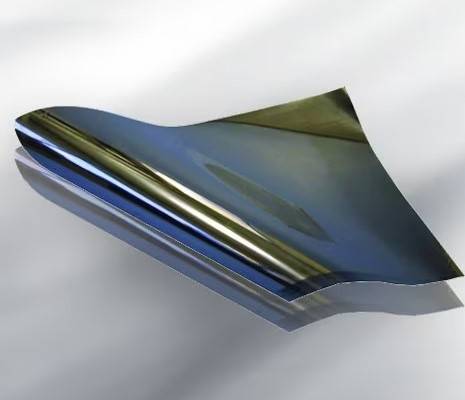
Ao utilizar a tecnologia CVD, os fabricantes de semicondutores podem obter um controlo preciso do processo de deposição, resultando em películas de alta qualidade que cumprem os requisitos rigorosos dos dispositivos electrónicos modernos.
Tecnologia de ecrãs
No domínio da tecnologia de ecrãs,películas de óxido de índio e estanho (ITO) epelículas de cobre desempenham um papel fundamental. Estes materiais são essenciais para o fabrico de vários dispositivos de visualização, melhorando o seu desempenho e funcionalidade.
Películas de óxido de índio e estanho (ITO)
As películas de ITO são conhecidas pela sua excecional condutividade eléctrica e transparência ótica. Esta combinação única torna-as ideais para aplicações como:
- Ecrãs tácteis: Fornecendo a camada condutora necessária para ecrãs sensíveis ao toque.
- Painéis electroluminescentes: Facilitam a emissão de luz nos ecrãs.
- Células solares: Melhorar a eficiência dos dispositivos fotovoltaicos, permitindo a passagem da luz enquanto conduzem eletricidade.
Películas de cobre
As películas de cobre, por outro lado, são famosas pela sua elevada condutividade eléctrica e resistência mecânica. Estas propriedades são aproveitadas em:
- Ecrãs flexíveis: Oferecem durabilidade e transmissão de sinal eficiente.
- Ecrãs de alta resolução: Garantem uma perda mínima de sinal e um processamento de dados a alta velocidade.
- Embalagem avançada: Apoiar a interconectividade em sistemas electrónicos complexos.
As películas de ITO e de cobre são normalmente depositadas utilizandotécnicas de deposição química de vapor (CVD) que permitem um controlo preciso da espessura e uniformidade da película, garantindo um desempenho ótimo em dispositivos de visualização.
Outros domínios
A tecnologia de deposição química em fase vapor (CVD) estende as suas aplicações para além do fabrico de semicondutores e da tecnologia de ecrãs, penetrando em diversas indústrias que exigem revestimentos precisos e duradouros. Uma aplicação proeminente é emrevestimentos ópticosonde a CVD é utilizada para depositar películas finas em lentes, espelhos e outros componentes ópticos. Estes revestimentos melhoram a transmissão da luz, reduzem a reflexão e melhoram o desempenho ótico global, tornando-os indispensáveis em domínios como as telecomunicações, a indústria aeroespacial e a imagiologia médica.
Outra aplicação significativa é emrevestimentos anti-corrosão. As técnicas CVD são utilizadas para criar camadas protectoras em metais e ligas, protegendo-os de condições ambientais adversas e prolongando a sua vida útil. Isto é particularmente crucial em indústrias como a automóvel, a aeroespacial e a engenharia naval, onde os materiais estão expostos a elementos corrosivos.
Aplicações | Impacto na indústria |
---|---|
Revestimentos ópticos | Melhoram os dispositivos ópticos, cruciais para as telecomunicações e a imagiologia médica. |
Revestimentos anti-corrosão | Protege metais nos sectores automóvel, aeroespacial e marítimo, prolongando a sua vida útil. |
Estas aplicações sublinham a versatilidade e a robustez da tecnologia CVD, tornando-a numa pedra angular dos processos industriais modernos.
Caraterísticas do processo CVD
Exigência de alta temperatura
O requisito de alta temperatura no processo de Deposição Química de Vapor (CVD) é fundamental por várias razões. Em primeiro lugar, as temperaturas elevadas são essenciais parapromover a velocidade de reação dos gases precursores. Quando aquecidos, estes gases sofrem decomposição e subsequentes reacções químicas na superfície do substrato, levando à formação da película fina desejada. A energia cinética fornecida pelo calor assegura que as moléculas têm energia suficiente para reagir e formar ligações estáveis.
Além disso, as temperaturas elevadas ajudam aa aumentar a taxa de difusão dos reagentes no substrato. Esta difusão é crucial para conseguir uma deposição uniforme da película em toda a superfície. Sem calor adequado, o processo de difusão seria lento, resultando em películas não uniformes e potencialmente defeituosas.
Além disso, as altas temperaturas desempenham um papel importante naremoção de impurezas do ambiente de reação. As impurezas, como a humidade ou os gases residuais, podem ser eliminadas a temperaturas elevadas, garantindo um processo de deposição mais limpo. Este aspeto de purificação é particularmente importante no fabrico de materiais de elevada pureza utilizados em dispositivos semicondutores.
Gama de temperaturas | Efeito |
---|---|
Baixa (<400°C) | Taxas de reação lentas, difusão limitada, potencial para filmes não uniformes. |
Média (400-800°C) | Optimizado para muitos processos CVD, taxas de reação e de difusão equilibradas. |
Alta (>800°C) | Reacções rápidas, elevadas taxas de difusão, mas podem exceder os limites térmicos do substrato. |
Ambiente de vácuo
O processo CVD é normalmente conduzido num ambiente de vácuo. Esta atmosfera controlada é crucial por várias razões. Em primeiro lugar, o vácuo minimiza a presença de contaminantes, como o oxigénio e o vapor de água, que poderiam interferir com as reacções químicas e degradar a qualidade da película depositada. Em segundo lugar, a manutenção do vácuo ajuda a gerir a pressão dentro da câmara de deposição, assegurando que os precursores gasosos fluem a taxas óptimas e reagem eficazmente na superfície do substrato.
No vácuo, o caminho livre médio das moléculas de gás é aumentado, reduzindo as colisões entre as moléculas. Esta redução das colisões permite um movimento mais direcionado dos precursores gasosos em direção ao substrato, melhorando o processo de deposição. Além disso, o ambiente de vácuo facilita um melhor controlo das condições de temperatura e pressão, que são parâmetros críticos no processo CVD.
Benefício | Descrição |
---|---|
Redução de contaminantes | Minimiza a interferência do oxigénio e do vapor de água. |
Gestão da pressão | Assegura um fluxo e uma reação ideais dos precursores de gás. |
Aumento do caminho livre médio | Reduz as colisões moleculares, melhorando a deposição. |
Controlo da temperatura | Facilita um melhor controlo dos parâmetros críticos. |
O ambiente de vácuo não é apenas um requisito técnico, mas um aspeto fundamental que sustenta a eficiência e a precisão do processo CVD. Ao manter o vácuo, os fabricantes podem obter películas uniformes e de alta qualidade com as propriedades desejadas, tornando-o uma parte indispensável da tecnologia CVD.
Preparação da superfície
Antes de qualquer processo de revestimento, particularmente na Deposição Química em Vapor (CVD), a superfície do substrato deve ser submetida a uma preparação rigorosa para garantir uma adesão e uma qualidade de película óptimas. Este passo é crucial, uma vez que tem um impacto direto no desempenho e na longevidade das películas finas depositadas.
Os contaminantes, tais como resíduos orgânicos, óxidos e humidade, devem ser meticulosamente removidos. Estas impurezas podem dificultar as reacções químicas necessárias para a formação da película e conduzir a defeitos como pinholes ou revestimentos não uniformes. As técnicas de preparação da superfície variam, mas os métodos comuns incluemlimpeza química,gravaçãoetratamento por plasma.
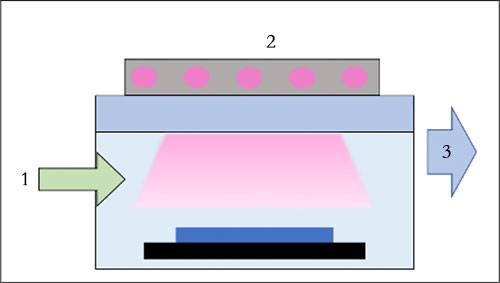
-
Limpeza química: Trata-se da utilização de solventes ou ácidos para dissolver e remover contaminantes orgânicos e inorgânicos. Por exemplo, a limpeza RCA é um método padrão que utiliza uma mistura de peróxido de hidrogénio e ácido sulfúrico para limpar bolachas de silício.
-
Gravura: Este método remove seletivamente as camadas superficiais utilizando reacções químicas. Por exemplo, o ácido fluorídrico é frequentemente utilizado para remover o dióxido de silício nativo dos substratos de silício.
-
Tratamento por plasma: Esta técnica utiliza plasma para ativar a superfície, aumentando a sua reatividade e limpando-a de quaisquer contaminantes residuais. É particularmente eficaz para remover resíduos orgânicos e melhorar a energia da superfície.
Cada um destes métodos desempenha um papel vital na garantia de que o substrato está livre de contaminantes, facilitando assim a deposição bem sucedida de películas finas de alta qualidade. A preparação adequada da superfície não só melhora a adesão da película depositada, como também garante que as propriedades da película, como a uniformidade e a densidade, cumprem as especificações exigidas.
Limitações do substrato
As limitações de temperatura e reatividade são factores críticos que podem restringir significativamente a gama de substratos aplicáveis nos processos de deposição química em fase vapor (CVD). As elevadas temperaturas necessárias para que as reacções químicas ocorram podem impor restrições térmicas ao material do substrato, limitando a escolha àqueles que podem suportar tais condições extremas sem degradação ou deformação. Por exemplo, certos materiais orgânicos ou metais de baixo ponto de fusão podem não ser adequados devido à sua incapacidade de manter a integridade estrutural a temperaturas elevadas.
Além disso, a reatividade dos gases precursores e as interações químicas resultantes com a superfície do substrato podem limitar ainda mais a seleção de materiais adequados. Alguns substratos podem reagir desfavoravelmente com os gases de deposição, conduzindo a reacções secundárias indesejáveis ou à formação de películas não uniformes. Esta limitação da reatividade exige uma seleção cuidadosa e um pré-tratamento dos substratos para garantir a compatibilidade com o processo CVD.
Cobertura e mascaramento
No contexto da deposição em fase vapor por processo químico (CVD), o processo de cobertura e mascaramento desempenha um papel crucial na determinação da qualidade final e da funcionalidade das películas finas depositadas. Enquanto a CVD assegura que todas as áreas do substrato são uniformemente cobertas com o material desejado, a capacidade de mascarar seletivamente áreas específicas torna-se um fator crítico na obtenção de padrões e estruturas precisos.
O aspeto de cobertura da CVD é altamente eficaz, uma vez que normalmente resulta numa deposição uniforme de material em toda a superfície do substrato. Esta uniformidade é essencial para aplicações em que é necessária uma espessura de película uniforme, como no fabrico de semicondutores e na tecnologia de ecrãs. No entanto, o desafio surge quando áreas específicas do substrato precisam de ser protegidas do processo de deposição. É aqui que as técnicas de mascaramento entram em ação.
O mascaramento em CVD envolve a utilização de barreiras físicas ou camadas fotorresistentes para impedir a deposição de material em determinadas regiões. Embora esta técnica seja geralmente eficaz, tem as suas limitações. Por exemplo, a precisão do processo de mascaramento pode ser afetada por factores como o tipo de substrato, a complexidade do padrão e os parâmetros CVD específicos utilizados. Além disso, os próprios materiais de mascaramento devem ser escolhidos cuidadosamente para garantir que não reagem com os gases de deposição ou se degradam sob as altas temperaturas normalmente envolvidas nos processos CVD.
Limitação da espessura da película
A espessura das películas finas depositadas por deposição química em fase vapor (CVD) é inerentemente limitada por vários factores, principalmente os parâmetros do processo e o estado físico dos materiais envolvidos. Estas limitações são fundamentais para compreender as aplicações práticas e os limites da tecnologia CVD.
Parâmetros do processo
O próprio processo de deposição impõe várias restrições à espessura da película. Os principais factores incluem:
- Temperatura e pressão: As altas temperaturas necessárias para as reacções CVD podem limitar a espessura da película depositada. As temperaturas extremas podem provocar a degradação térmica ou a não uniformidade da película. Do mesmo modo, a pressão sob a qual o processo é conduzido pode afetar a taxa de crescimento e a uniformidade da película.
- Cinética da reação: A velocidade a que os gases precursores reagem e formam a película desejada é outro fator limitante. Reacções mais rápidas podem levar a películas mais finas se o processo não for cuidadosamente controlado.
Estado do material
As propriedades físicas e químicas dos materiais precursores também desempenham um papel importante:
- Estabilidade do Precursor: A estabilidade dos gases precursores a altas temperaturas pode limitar a espessura da película. Os precursores instáveis podem decompor-se prematuramente, dando origem a películas incompletas ou não uniformes.
- Compatibilidade do substrato: A capacidade do material do substrato para suportar as condições de deposição é crucial. Certos substratos podem não ser capazes de suportar as altas temperaturas ou a reatividade necessárias para a deposição de películas mais espessas.
Estas restrições não são meras limitações, mas fazem parte integrante do processo, garantindo que as películas depositadas são de alta qualidade e adequadas para as aplicações pretendidas.
Adesão
As excelentes propriedades de adesão são uma caraterística da tecnologia de deposição química em fase vapor (CVD), que é crucial para a durabilidade e funcionalidade das películas finas que produz. A adesão destas películas é influenciada por vários factores, incluindo a preparação da superfície do substrato, a reatividade química dos gases precursores e as condições do processo, como a temperatura e a pressão.
Por exemplo, a preparação adequada da superfície assegura a remoção de contaminantes, criando uma superfície limpa e reactiva que melhora a ligação entre a película e o substrato. Este passo é particularmente importante no fabrico de semicondutores, onde mesmo pequenas impurezas podem levar a problemas de desempenho significativos.
A natureza química dos gases precursores também desempenha um papel fundamental. A reação entre os precursores gasosos e a superfície do substrato forma uma forte ligação química, que é a base da excelente adesão observada nas películas CVD. Este mecanismo de ligação química assegura que as películas depositadas permanecem firmemente ligadas ao substrato, mesmo em condições de funcionamento difíceis.
As condições do processo, tais como as elevadas temperaturas necessárias para a CVD, contribuem ainda mais para a forte adesão. Estas temperaturas elevadas não só promovem as reacções químicas necessárias para a formação da película, como também permitem uma melhor difusão dos materiais da película no substrato, criando uma interface mais robusta.
Vantagens da tecnologia CVD
Uniformidade
A uniformidade na Deposição Química de Vapor (CVD) é um atributo crítico que garante uma qualidade de película consistente em substratos de grandes áreas. Esta uniformidade é conseguida através de um controlo meticuloso dos parâmetros do processo, incluindo a temperatura, a pressão e os caudais dos precursores. A capacidade de manter a uniformidade é particularmente crucial no fabrico de semicondutores, onde mesmo pequenas variações podem levar a problemas de desempenho significativos no produto final.
Para ilustrar, considere uma configuração típica de CVD em que o substrato é exposto a um fluxo uniforme de gases precursores. As moléculas de gás difundem-se e reagem na superfície do substrato, formando uma película fina. Ao gerir com precisão a distribuição destes gases, os fabricantes podem garantir que a deposição ocorre uniformemente em todo o substrato, independentemente do seu tamanho. Isto é frequentemente facilitado por designs avançados de reactores que promovem uma distribuição uniforme do gás e minimizam as variações localizadas.
Parâmetro | Impacto na uniformidade |
---|---|
Temperatura | Garante a decomposição uniforme e a deposição de precursores. |
Pressão | Ajuda a manter um fluxo de gás e uma taxa de reação consistentes. |
Fluxo de precursores | Controla a concentração e a distribuição das espécies reactivas. |
Em resumo, a uniformidade nos processos CVD não é apenas uma caraterística desejável, mas um requisito fundamental para a produção de películas finas de alta qualidade. Sublinha a importância do controlo preciso do processo e da tecnologia avançada de reactores para a obtenção de resultados consistentes em grandes substratos.
Controlabilidade
Uma das caraterísticas de destaque da tecnologia de Deposição Química em Vapor (CVD) é o seu elevado grau de controlo sobre o processo de deposição. Esta capacidade de controlo é essencial para obter propriedades de película e taxas de deposição precisas, que são críticas para várias aplicações no fabrico de semicondutores, tecnologia de ecrãs e muito mais.
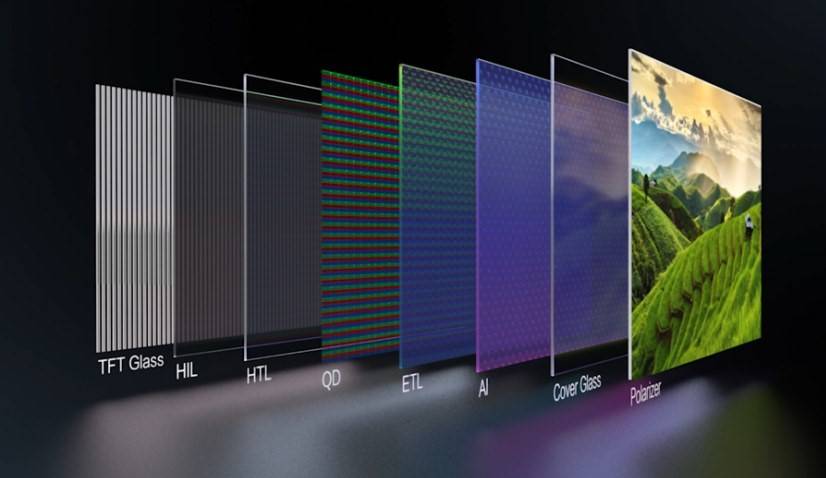
Controlo da taxa de deposição
A taxa de deposição em CVD pode ser meticulosamente controlada através do ajuste de vários parâmetros. Estes incluem:
- Temperatura: Ao variar a temperatura do substrato e dos gases precursores, a taxa a que as reacções químicas ocorrem pode ser ajustada. As temperaturas mais elevadas aceleram geralmente a taxa de reação, conduzindo a uma deposição mais rápida.
- Pressão (pressão): O funcionamento sob diferentes pressões pode influenciar a dinâmica do fluxo dos gases precursores e a taxa a que estes atingem a superfície do substrato.
- Caudais de gás: O controlo das taxas de fluxo dos gases precursores permite ajustes precisos na concentração de reagentes no substrato, afectando assim a taxa de deposição.
Personalização das propriedades da película
Para além da taxa de deposição, a CVD oferece um controlo extensivo sobre as propriedades da película resultante. As principais propriedades que podem ser personalizadas incluem:
- Espessura da película: Ao gerir cuidadosamente os parâmetros do processo, a espessura da película depositada pode ser controlada dentro de um intervalo estreito, garantindo a uniformidade em grandes substratos.
- Composição química: A utilização de diferentes gases precursores ou misturas permite a deposição de películas com composições químicas variáveis, adaptadas aos requisitos de aplicações específicas.
- Estrutura cristalina: As condições de temperatura e pressão podem influenciar a cristalinidade da película depositada, permitindo a criação de estruturas amorfas ou cristalinas, conforme necessário.
- Stress: A tensão interna da película pode ser controlada para evitar defeitos e garantir a integridade e a adesão da película ao substrato.
Flexibilidade do processo
A capacidade de controlo da CVD estende-se à flexibilidade do próprio processo. Os diferentes tipos de CVD, como o CVD térmico, o CVD reforçado com plasma (PECVD) e o CVD orgânico metálico (MOCVD), oferecem vantagens e mecanismos de controlo únicos. Por exemplo, o PECVD utiliza plasma para aumentar a taxa de reação e proporcionar um controlo adicional sobre o processo de deposição, enquanto o MOCVD permite a utilização de compostos orgânicos metálicos para depositar materiais complexos.
Versatilidade
A tecnologia de deposição química em fase vapor (CVD) destaca-se pela sua excecional versatilidade, tornando-a uma pedra angular em várias indústrias. Esta versatilidade é atribuída principalmente à sua capacidade de depositar uma vasta gama de materiais, cada um adaptado a aplicações específicas. Quer se trate de criar películas de semicondutores de alta qualidade, de melhorar as tecnologias de visualização ou de desenvolver revestimentos protectores, a CVD prova a sua adaptabilidade a diferentes tipos de materiais e requisitos funcionais.
Diversidade de materiais
A capacidade da CVD de lidar com diversos materiais é uma vantagem significativa. Desde películas de silício e metal até compostos complexos como nitretos e óxidos, a gama de materiais que podem ser processados é extensa. Este amplo espetro garante que a CVD pode satisfazer as exigências rigorosas das aplicações tecnológicas modernas, desde a microeletrónica à ótica avançada.
Flexibilidade de aplicação
Para além da diversidade de materiais, a flexibilidade da CVD estende-se à sua aplicação em múltiplos campos. No fabrico de semicondutores, é indispensável para a criação de silicetos, películas de nitretos e camadas metálicas, desempenhando cada uma delas um papel crucial no desempenho dos dispositivos. Na tecnologia de ecrãs, a CVD é utilizada para depositar óxido de índio e estanho (ITO) e películas de cobre, melhorando a funcionalidade e a durabilidade dos ecrãs. Além disso, a CVD tem utilidade em áreas menos convencionais, como revestimentos ópticos e tratamentos anti-corrosão, ilustrando ainda mais a sua versatilidade.
Adaptabilidade do processo
A adaptabilidade dos processos de CVD é outra faceta da sua versatilidade. Técnicas como a CVD térmica, a CVD melhorada por plasma (PECVD) e a CVD orgânica metálica (MOCVD) oferecem vantagens únicas, permitindo um controlo preciso do processo de deposição. Esta adaptabilidade garante que a CVD pode ser optimizada para diferentes substratos e condições ambientais, tornando-a uma ferramenta versátil nas mãos de investigadores e engenheiros.
CONTACTE-NOS PARA UMA CONSULTA GRATUITA
Os produtos e serviços da KINTEK LAB SOLUTION foram reconhecidos por clientes de todo o mundo. A nossa equipa terá todo o prazer em ajudar com qualquer questão que possa ter. Contacte-nos para uma consulta gratuita e fale com um especialista de produto para encontrar a solução mais adequada para as suas necessidades de aplicação!