Compreender a prensagem a quente
Índice
- Compreender a prensagem a quente
- Tipos de aquecimento na prensagem a quente
- Introdução a três tipos de aquecimento: aquecimento por indução, aquecimento por resistência indireta e técnica de sinterização assistida por campo (FAST) / prensagem direta a quente
- Aquecimento indutivo
- Aquecimento por resistência indireta
- Técnica de sinterização assistida por campo (FAST) / Prensagem direta a quente
- Aquecimento indutivo
- Aquecimento por resistência indireta
- Técnica de sinterização assistida no terreno (FAST) / Prensagem direta a quente
- Aplicações da prensagem a quente
- Fabrico de artigos críticos como alvos de pulverização catódica e componentes cerâmicos de elevado desempenho
- Vantagens da utilização de pó metálico
- Adequação do processo para altas taxas de aquecimento
- Papel da prensagem direta a quente na indústria de materiais de fricção
- Aplicações de pastilhas de travão e discos de embraiagem sinterizados
Definição e processo de prensagem a quente
A prensagem a quenteé um processo de metalurgia do pó de alta pressão e baixa taxa de deformação utilizado para formar pó ou pó compacto a altas temperaturas para induzir processos de sinterização e de fluência. Envolve a aplicação simultânea de calor e pressão para fabricar materiais duros e quebradiços.
Utilização e aplicação principais
A prensagem a quente é utilizada principalmente na consolidação de ferramentas de corte compostas de diamante e metal, cerâmicas técnicas e outros materiais duros e quebradiços. Funciona através do rearranjo das partículas e do fluxo de plástico nos contactos das partículas. O pó solto ou a peça pré-compactada é colocada num molde de grafite, permitindo o aquecimento por indução ou resistência até temperaturas tipicamente de 2.400 °C (4.350 °F). Podem ser aplicadas pressões até 50 MPa (7.300 psi). A prensagem a quente também é utilizada na prensagem de diferentes tipos de polímeros.
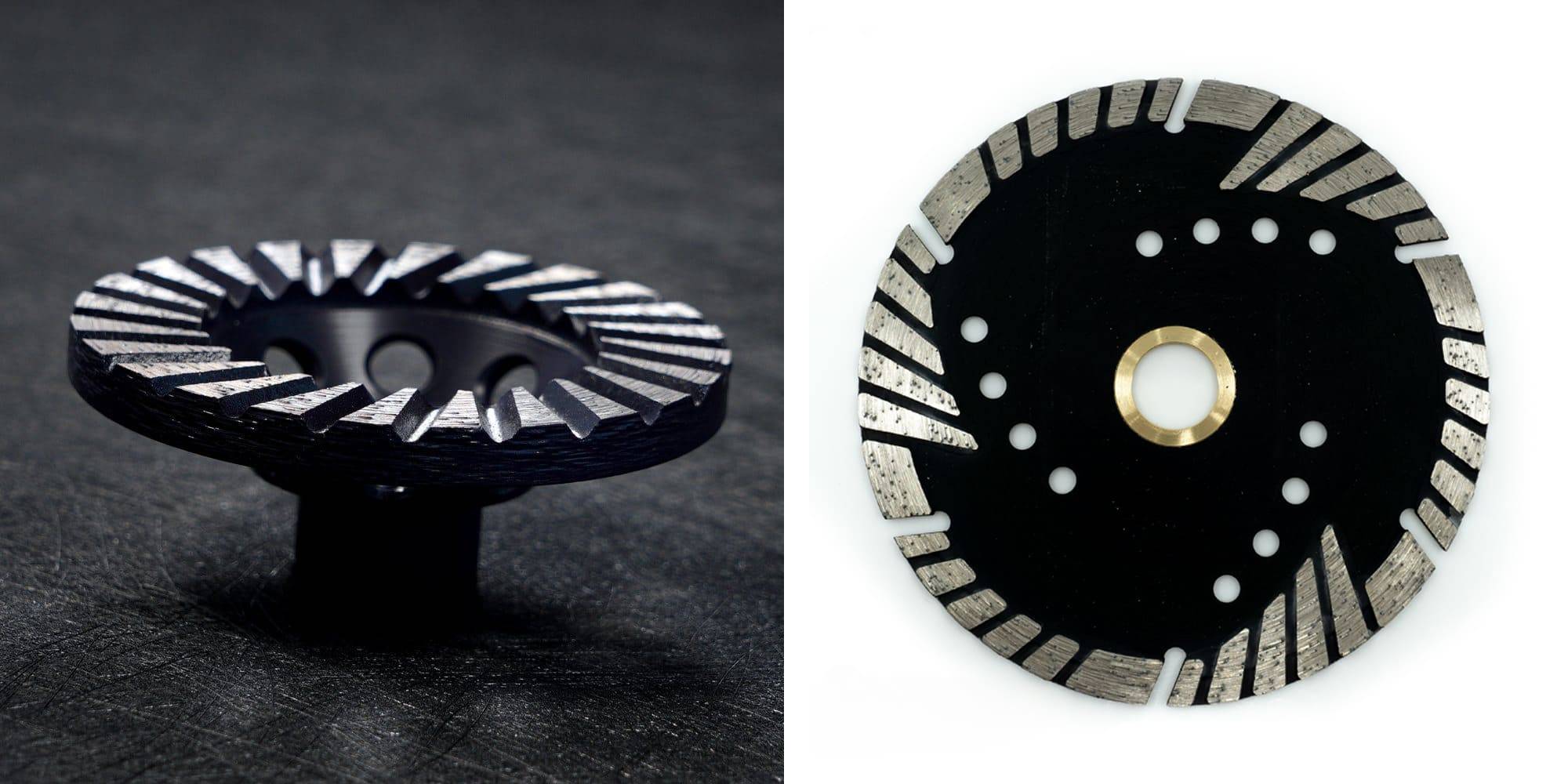
Diamantes prensados a quente
Densificação através de rearranjo de partículas e fluxo plástico
O processo de densificação na prensagem a quente ocorre através do rearranjo das partículas e do fluxo de plástico nos contactos das partículas. A pressão externa aplicada durante a prensagem a quente causa a destruição de defeitos e poros internos, resultando no contacto das superfícies internas entre si. O material sofre então uma fluência a alta temperatura, permitindo a penetração mútua e a ligação por difusão, eliminando completamente os defeitos e a porosidade.
Utilização do molde de grafite e temperaturas de aquecimento
Na prensagem a quente, é normalmente utilizado um molde de grafite para conter o pó solto ou a peça pré-compactada. O molde de grafite permite um aquecimento eficiente através de aquecimento por indução ou resistência. As temperaturas utilizadas na prensagem a quente podem atingir os 2.400 °C (4.350 °F), assegurando os processos de sinterização e de fluência necessários para a densificação.
Pressões envolvidas no processo
A prensagem a quente envolve a aplicação de pressões elevadas para obter a densificação. Podem ser aplicadas pressões de até 50 MPa (7.300 psi) durante o processo de prensagem a quente. A alta pressão ajuda no rearranjo das partículas e no fluxo de plástico, resultando num produto final compacto e denso.
Prensagem a quente na indústria de polímeros
A prensagem a quente também é amplamente utilizada na indústria de polímeros. Ao utilizar a técnica de prensagem a quente, os fabricantes podem eliminar a necessidade de aglutinantes no seu processo de fabrico e, em vez disso, utilizar a combinação de força e temperatura para unir completamente as suas peças. Isto permite a produção de produtos poliméricos de alta qualidade com propriedades mecânicas e precisão dimensional melhoradas.
Em resumo, a prensagem a quente é um processo de metalurgia do pó utilizado para fabricar materiais duros e frágeis. Envolve a aplicação de calor e pressão para induzir processos de sinterização e de fluência, resultando em densificação. A prensagem a quente é amplamente utilizada em várias indústrias, incluindo a aeroespacial, a cerâmica e o fabrico de polímeros. O processo utiliza um molde de grafite e pode atingir altas temperaturas e pressões para alcançar os resultados desejados.
Tipos de aquecimento na prensagem a quente
Introdução a três tipos de aquecimento: aquecimento por indução, aquecimento por resistência indireta e técnica de sinterização assistida por campo (FAST) / prensagem direta a quente
A prensagem a quente é uma técnica amplamente utilizada na indústria transformadora para criar ligações duráveis e apertadas entre materiais. Envolve a combinação de força adicional durante a sinterização de materiais a alta temperatura, quer no vácuo quer sob uma pressão positiva de gás inerte. Esta pressão ajuda a aumentar a densificação do material, resultando num lingote de material com densidades próximas da teórica.
Existem dois tipos principais de fornos de prensagem a quente: os que utilizam varetas quentes e frias para aplicar pressão e os que utilizam punções e matrizes de grafite ou placas de prensagem para exercer a força durante a ligação por difusão. Estes fornos eliminam a necessidade de aglutinantes no processo de fabrico, tornando-os altamente eficientes.
Na tecnologia de prensagem a quente, são utilizados três tipos distintos de métodos de aquecimento: aquecimento por indução, aquecimento por resistência indireta e técnica de sinterização assistida por campo (FAST) / prensagem direta a quente.
Aquecimento indutivo
O aquecimento indutivo é um método comummente utilizado para a sinterização de pó metálico, cerâmico e de alguns compostos intermetálicos metálicos refractários. Envolve a utilização de indução electromagnética para gerar calor dentro do material.
Neste processo, uma corrente alternada é passada através de uma bobina, criando um campo magnético. Este campo magnético induz correntes de Foucault no material, que por sua vez geram calor. O calor é então utilizado para sinterizar o material e criar a ligação desejada.
O aquecimento indutivo é conhecido pela sua eficiência e precisão. Permite taxas de aquecimento rápidas e um controlo preciso da distribuição da temperatura, resultando em ligações de alta qualidade. É particularmente adequado para materiais com elevada condutividade eléctrica.
Aquecimento por resistência indireta
O aquecimento por resistência indireta é outro método habitualmente utilizado na prensagem a quente. Envolve a utilização de resistência eléctrica para gerar calor dentro do material.
Neste processo, é passada uma corrente eléctrica através do material, causando resistência e gerando calor. O calor é então utilizado para sinterizar o material e criar a ligação desejada.
O aquecimento por resistência indireta é conhecido pela sua simplicidade e versatilidade. Pode ser utilizado com uma vasta gama de materiais e é particularmente adequado para materiais com baixa condutividade eléctrica. Permite um controlo preciso da temperatura e pode atingir taxas de aquecimento elevadas.
Técnica de sinterização assistida por campo (FAST) / Prensagem direta a quente
A técnica de sinterização assistida por campo (FAST), também conhecida como prensagem direta a quente, é um método relativamente novo utilizado na prensagem a quente. Envolve a utilização de um campo elétrico para ajudar no processo de sinterização.
Neste processo, é passada uma corrente eléctrica através do material, criando um campo elétrico. Este campo elétrico aumenta a mobilidade dos átomos no interior do material, permitindo uma sinterização e densificação aceleradas.
A FAST / prensagem direta a quente é conhecida pela sua capacidade de produzir materiais altamente densos e uniformes. Permite taxas de sinterização rápidas e pode atingir densidades elevadas próximas da teórica. É particularmente adequada para materiais que têm baixa difusividade e alta condutividade eléctrica.
Em conclusão, a prensagem a quente é uma técnica valiosa na indústria transformadora para criar ligações duráveis e apertadas entre materiais. Na tecnologia de prensagem a quente, são normalmente utilizados três tipos de métodos de aquecimento: aquecimento por indução, aquecimento por resistência indireta e técnica de sinterização assistida por campo (FAST) / prensagem direta a quente. Cada método tem as suas próprias vantagens e é adequado para diferentes materiais e aplicações.
Aquecimento indutivo
Processo e funcionamento do aquecimento indutivo
O aquecimento indutivo é o processo de aquecimento de materiais condutores de eletricidade, tais como metais ou semicondutores, utilizando a indução electromagnética. Isto é conseguido através da passagem de uma corrente alternada de alta frequência através de um eletroíman, criando um campo magnético rapidamente alternado. Este campo magnético induz correntes de Foucault no interior do material, que fluem através da sua resistência e geram calor por aquecimento Joule. Nos materiais ferromagnéticos e ferrimagnéticos, o calor é também gerado por perdas por histerese magnética. A frequência da corrente eléctrica utilizada depende de factores como o tamanho e o material do objeto, o acoplamento entre a bobina de trabalho e o objeto e a profundidade de penetração.
Este método de aquecimento é normalmente utilizado para fundir metais e fazer ligas. A fusão por indução em vácuo, que combina uma atmosfera controlada e um controlo preciso do processo de fusão, é uma aplicação popular do aquecimento indutivo. Os fornos de indução podem atingir temperaturas de 1800ºC ou superiores, e consistem tipicamente num refrigerador, numa unidade de potência e numa unidade de vácuo.
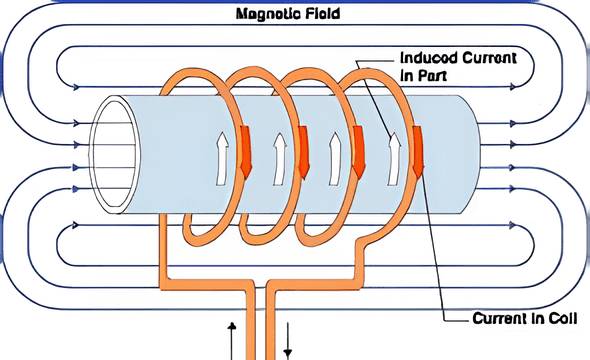
Vantagens e desvantagens do aquecimento indutivo
O aquecimento indutivo oferece várias vantagens em relação a outros métodos de aquecimento. É um processo mais rápido em comparação com o aquecimento elétrico ou a gás, graças ao seu princípio de indução. Os fornos de indução também têm um tempo de arranque rápido, uma vez que não requerem um ciclo de aquecimento ou arrefecimento. A fonte de alimentação de indução cria uma forte ação de agitação, resultando em misturas homogéneas de metal líquido. Além disso, os fornos de indução requerem menos materiais refractários em comparação com as unidades alimentadas a combustível. São mais eficientes em termos energéticos e capazes de reduzir o consumo de energia para a fusão de metais. Os fornos de indução são também compactos em tamanho, permitindo uma instalação mais fácil, e permitem taxas de produção mais elevadas devido a tempos de fusão mais curtos.
No entanto, existem também algumas desvantagens a considerar. A potência nominal dos fornos de indução pode nem sempre refletir a sua potência de trabalho real, levando a uma redução da eficiência de fusão. É importante garantir que o fornecedor possui tecnologia de placa de potência de indução auto-desenvolvida e pode fornecer soluções personalizadas flexíveis. Além disso, o aquecimento indutivo pode apresentar desafios na distribuição de calor e na taxa de aquecimento, exigindo uma análise cuidadosa da aplicação específica e do material a ser aquecido.
Problemas com a distribuição de calor e a taxa de aquecimento
O aquecimento indutivo pode produzir altas densidades de potência, permitindo tempos de interação curtos para atingir a temperatura necessária. Isto resulta num controlo rigoroso do padrão de aquecimento, seguindo de perto o campo magnético aplicado. Este controlo preciso ajuda a reduzir a distorção térmica e os danos no material a ser aquecido.
No entanto, a distribuição de calor e a taxa de aquecimento podem ser problemas potenciais no aquecimento indutivo. Pode ocorrer uma distribuição desigual do calor se a bobina de indução não tiver um contacto adequado com o material ou se o material tiver uma forma ou composição irregular. É importante assegurar um acoplamento adequado entre a bobina de trabalho e o objeto a aquecer para obter um aquecimento uniforme.
A taxa de aquecimento também pode ser influenciada por factores como o tamanho e o material do objeto, bem como a profundidade de penetração do campo eletromagnético. Compreender estes factores e o seu impacto no processo de aquecimento é crucial para alcançar os resultados desejados nas aplicações de aquecimento indutivo.
Em geral, o aquecimento indutivo é um método versátil e eficiente para aquecer materiais condutores de eletricidade. As suas vantagens em termos de velocidade, eficiência energética e capacidade de controlo fazem dele uma escolha popular em várias indústrias, incluindo a metalurgia, o fabrico de semicondutores e a fundição de ouro. Ao considerar os requisitos e desafios específicos de cada aplicação, as empresas podem tomar decisões informadas ao utilizar a tecnologia de aquecimento indutivo.
Aquecimento por resistência indireta
O aquecimento por resistência indireta é uma tecnologia utilizada em fornos eléctricos que envolve o aquecimento de um molde ou carga utilizando elementos de aquecimento de grafite. O calor é gerado pela passagem de uma corrente eléctrica através destes elementos, que depois transferem o calor para o molde por convecção. Este processo é conhecido como aquecimento por resistência indireta.
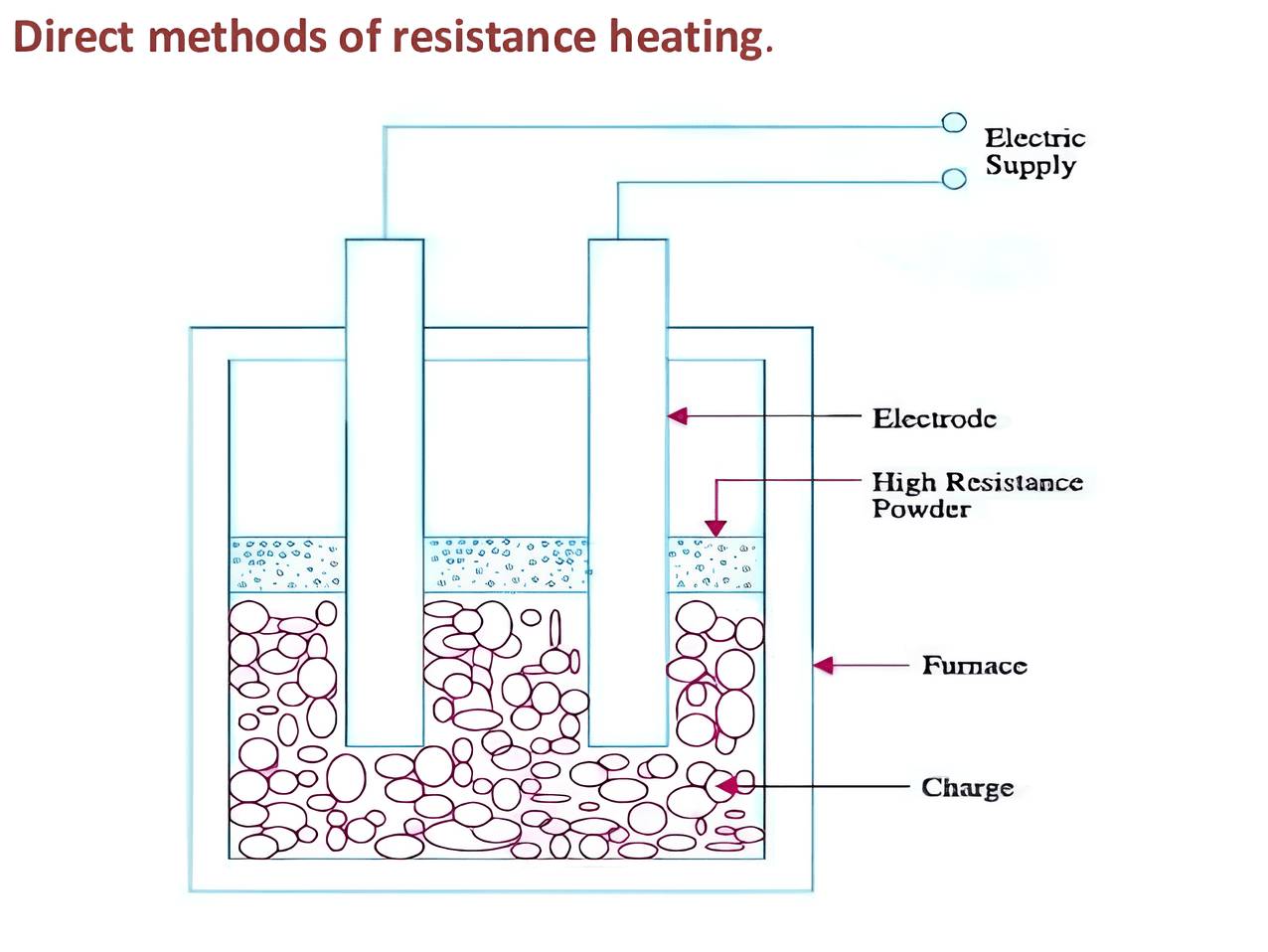
Processo e funcionamento do aquecimento por resistência indireta
No aquecimento por resistência indireta, o molde é colocado numa câmara de aquecimento onde se encontram elementos de aquecimento de grafite. Estes elementos são aquecidos pela corrente eléctrica que passa através deles. O calor gerado pelos elementos de aquecimento é então transferido para o molde por convecção, resultando no aquecimento do molde.
Vantagens e Desvantagens do Aquecimento por Resistência Indireta
Uma das vantagens do aquecimento por resistência indireta é a capacidade de atingir temperaturas elevadas. A temperatura atingida é independente da condutividade do molde e não é afetada pelo calor e pela pressão. No entanto, uma das principais desvantagens do aquecimento por resistência indireta é o tempo que demora a aquecer o molde. A transferência de calor da atmosfera do forno para a superfície do molde e ao longo da secção transversal do molde é relativamente lenta.
História e interesse atual no aquecimento por resistência
O aquecimento por resistência tem sido utilizado há muitos anos em várias aplicações. É normalmente utilizado em aparelhos domésticos, como fogões eléctricos e torradeiras. Nos últimos anos, tem havido um interesse crescente no aquecimento por resistência para aplicações industriais, como a tecnologia de prensagem a quente. O aquecimento por indução e a técnica de sinterização assistida por campo (FAST) / prensagem direta a quente são outros métodos de aquecimento utilizados em conjunto com o aquecimento por resistência.
Os elementos de aquecimento por resistência, tais como fios ou fitas de resistência, são normalmente utilizados em vários dispositivos de aquecimento e fornos industriais. Estes elementos convertem energia eléctrica em calor através do aquecimento por efeito de Joule. A resistência encontrada pela corrente eléctrica que passa através do elemento resulta no aquecimento do elemento.
Em conclusão, o aquecimento por resistência indireta é uma tecnologia que utiliza elementos de aquecimento de grafite para aquecer um molde ou carga por convecção. Oferece vantagens como temperaturas elevadas que podem ser atingidas, independentemente da condutividade do molde e do calor/pressão. No entanto, tem o inconveniente de uma transferência de calor relativamente lenta. Os elementos de aquecimento por resistência, como os fios de resistência, são normalmente utilizados em vários dispositivos de aquecimento e fornos industriais.
Técnica de sinterização assistida no terreno (FAST) / Prensagem direta a quente
Conceito e execução de FAST
A tecnologia de sinterização assistida por campo/sinterização por plasma de faísca (FAST/SPS) utiliza uma corrente eléctrica DC para aquecer diretamente o molde e/ou a amostra através do aquecimento Joule. Este aquecimento direto permite atingir taxas de aquecimento elevadas e tempos de ciclo de processamento reduzidos. Permite também a consolidação de uma vasta gama de materiais metálicos, cerâmicos e funcionais. O FAST/SPS oferece novas possibilidades para o fabrico de materiais com características potencialmente extraordinárias. Também pode processar compósitos multi-materiais, materiais de grau funcional e de ligação por difusão.
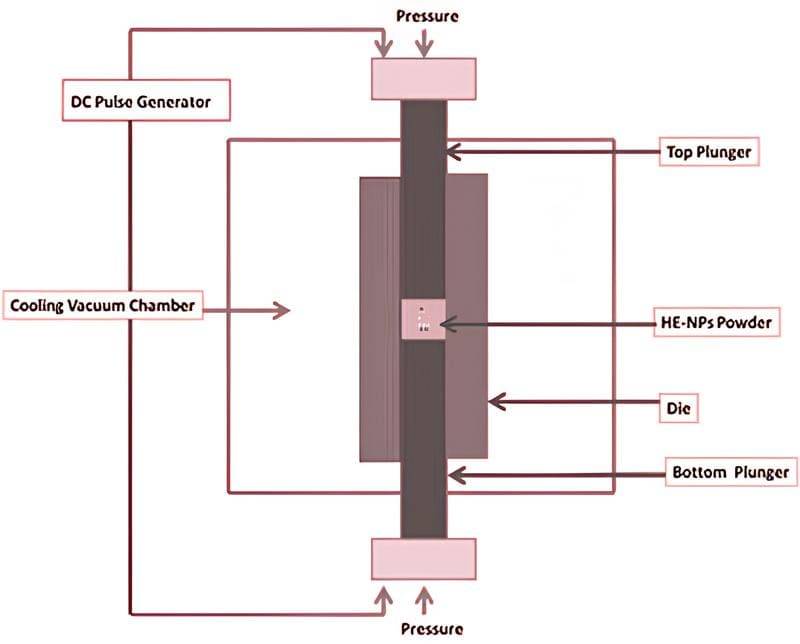
Razões para reduzir o tempo de ciclo
A razão principal para encurtar o tempo de ciclo na prensagem direta a quente é evitar o crescimento de grão e poupar energia. Na prensagem direta a quente, o molde está diretamente ligado à energia eléctrica, gerando calor no molde através da resistividade do molde e da peça em pó. Isto resulta em taxas de aquecimento muito elevadas e aumenta significativamente a atividade de sinterização dos agregados de pó metálico fino. Tornam-se possíveis tempos de ciclo curtos de alguns minutos e o processo reduz a temperatura e a pressão limite de sinterização em comparação com as técnicas de sinterização convencionais. O aquecimento por resistência direta garante que o calor é gerado onde é necessário.
Vantagens da prensagem direta a quente
A prensagem direta a quente oferece várias vantagens em comparação com as técnicas convencionais de sinterização por metalurgia do pó. Permite a produção de propriedades únicas através da utilização de temperaturas de processamento mais baixas e/ou tempos de processamento mais curtos. Permite a sinterização por prensagem a quente de pós metálicos e cerâmicos, a preparação de compósitos cerâmicos/metálicos e compostos intermetálicos e a investigação e desenvolvimento de processos de soldadura por difusão. Facilita também a sinterização por prensagem a quente de compostos de oxigénio/nitrogénio/borão/carbono e respectivas misturas.
Diferenças entre sinterização com corrente pulsada e não pulsada
A investigação mais recente sugere que não existe uma diferença básica entre a sinterização com corrente pulsada ou não pulsada (SPS ou FAST). Em princípio, todas as técnicas de prensagem direta a quente podem obter melhores resultados de sinterização em comparação com a prensagem a quente convencional se a melhoria se dever apenas ao aquecimento in situ do pó. No entanto, se estiverem presentes efeitos físicos adicionais associados à própria densidade da corrente eléctrica, uma corrente pulsada tem frequentemente efeitos benéficos adicionais. Isto deve-se ao facto de, durante cada impulso, a densidade da corrente eléctrica atingir um valor significativamente mais elevado do que uma corrente contínua com uma potência de aquecimento comparável.
Em resumo, a Técnica de Sinterização Assistida por Campo (FAST) ou a prensagem direta a quente utilizando uma corrente eléctrica direta oferece inúmeras vantagens em termos de tempos de ciclo de processamento mais curtos, temperaturas e pressões mais baixas e a capacidade de produzir propriedades únicas numa vasta gama de materiais. Quer utilize corrente pulsada ou não pulsada, a técnica de prensagem direta a quente pode alcançar melhores resultados de sinterização em comparação com os métodos convencionais.
Aplicações da prensagem a quente
Fabrico de artigos críticos como alvos de pulverização catódica e componentes cerâmicos de elevado desempenho
A tecnologia de prensagem a quente tem sido utilizada com sucesso no fabrico de artigos críticos, como alvos de pulverização catódica e componentes cerâmicos de elevado desempenho. Materiais como o carboneto de boro, o diboreto de titânio e o sialon foram obtidos através deste processo. Ao utilizar pó metálico, a condutividade do molde permite o aquecimento rápido da peça de trabalho. Este método é especialmente adequado para aplicações que requerem altas taxas de aquecimento, tornando-o ideal para materiais que só podem ser mantidos em altas temperaturas por pouco tempo ou para processos que requerem taxas de aquecimento rápidas para alta produtividade.
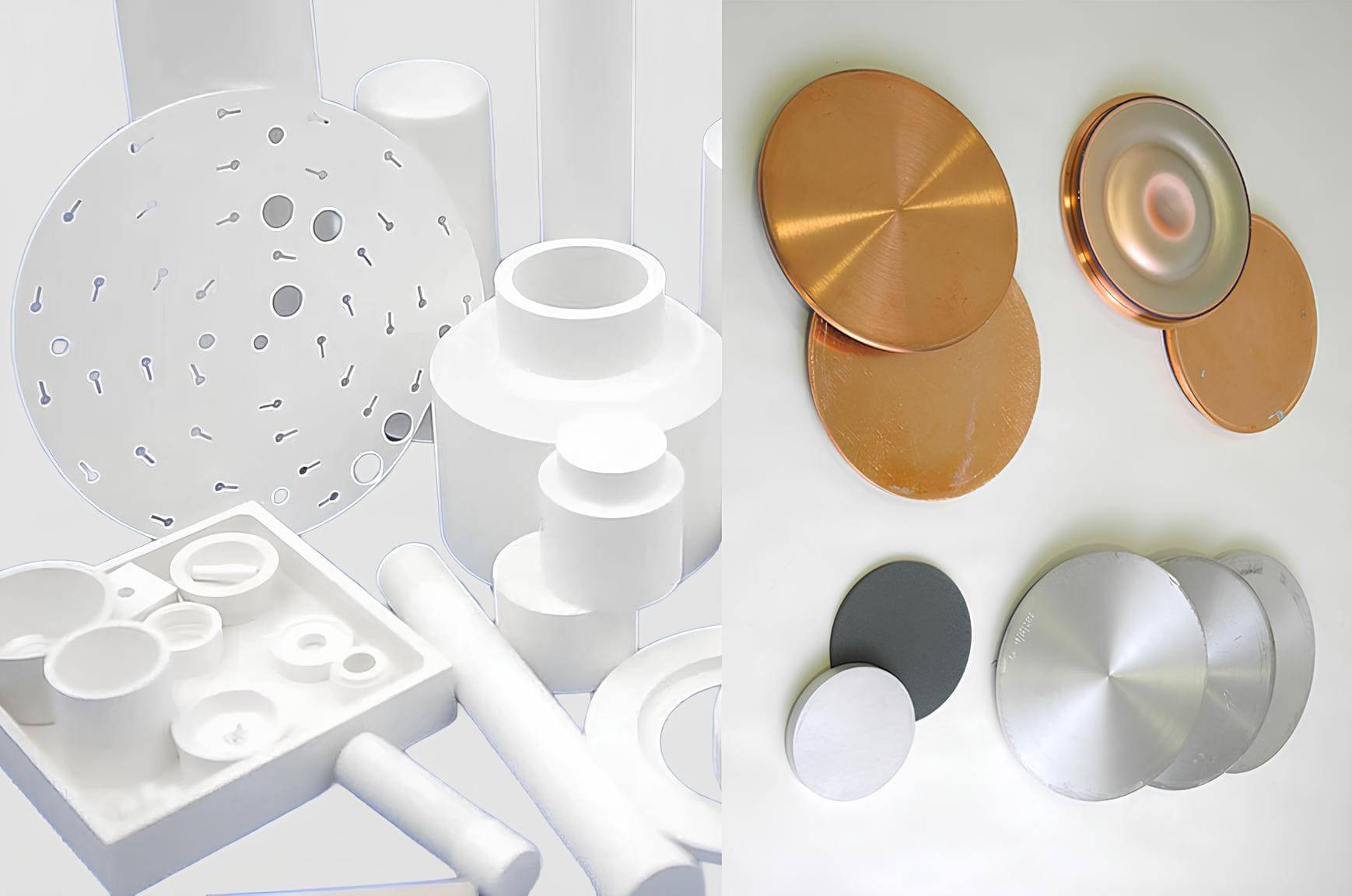
Benefícios do uso de pó metálico
Uma das vantagens do uso de pó metálico no processo de prensagem a quente é que ele permite o aquecimento rápido da peça de trabalho. Moldes com diâmetro grande e altura relativamente pequena podem ser aquecidos rapidamente, resultando em maior eficiência e produtividade. Além disso, a utilização de pó metálico elimina a necessidade de aglutinantes no processo de fabrico, permitindo uma ligação completa das peças através de uma combinação de força e temperatura.
Adequação do processo para altas taxas de aquecimento
O processo de prensagem a quente é particularmente adequado para aplicações que requerem elevadas taxas de aquecimento. Isto é benéfico para materiais que só podem ser mantidos a altas temperaturas por um curto período de tempo ou para processos que requerem taxas de aquecimento rápidas para alcançar uma elevada produtividade. A combinação de força e temperatura na prensagem a quente permite uma ligação rápida e eficiente das peças.
Papel da prensagem direta a quente na indústria de materiais de fricção
A tecnologia de prensagem direta a quente desempenha um papel significativo na indústria de materiais de fricção. Permite que os materiais sejam sinterizados até à sua densidade final, alcançando um elevado nível de precisão de forma quase líquida. Esta precisão elimina frequentemente a necessidade de retrabalho mecânico de materiais que são difíceis de processar. A prensagem direta a quente é particularmente útil para materiais que requerem um elevado nível de densidade e precisão na sua forma final.
Aplicações de pastilhas de travão e discos de embraiagem sinterizados
A prensagem a quente é normalmente utilizada na produção de pastilhas de travão e discos de embraiagem sinterizados. O processo permite a criação de materiais densos e de elevado desempenho que oferecem capacidades superiores de travagem e de engate da embraiagem. As pastilhas de travão e os discos de embraiagem sinterizados são conhecidos pela sua durabilidade, resistência ao calor e desempenho consistente, o que os torna altamente valorizados na indústria automóvel.
Em conclusão, a prensagem a quente é um processo versátil e valioso que encontra aplicações em várias indústrias. É particularmente útil no fabrico de artigos críticos como alvos de pulverização catódica e componentes cerâmicos de alto desempenho. A utilização de pó metálico na prensagem a quente oferece vantagens como o aquecimento rápido e a eliminação de aglutinantes. O processo é adequado para altas taxas de aquecimento e desempenha um papel significativo na indústria de materiais de fricção. Além disso, a prensagem a quente é amplamente utilizada na produção de pastilhas de travão sinterizadas e discos de embraiagem, proporcionando um desempenho superior e durabilidade em aplicações automóveis.
CONTACTE-NOS PARA UMA CONSULTA GRATUITA
Os produtos e serviços da KINTEK LAB SOLUTION foram reconhecidos por clientes de todo o mundo. A nossa equipa terá todo o prazer em ajudar com qualquer questão que possa ter. Contacte-nos para uma consulta gratuita e fale com um especialista de produto para encontrar a solução mais adequada para as suas necessidades de aplicação!