Os revestimentos são essenciais para a resistência ao desgaste, uma vez que protegem os materiais e componentes de danos mecânicos, prolongando a sua vida útil e reduzindo os custos.Ao aplicar uma fina camada de revestimento, os materiais obtêm propriedades de superfície melhoradas, tais como maior dureza, melhor resistência ao desgaste e melhor desempenho em condições adversas.Isto é particularmente importante em indústrias como a automóvel e a aeroespacial, onde os componentes estão sujeitos a um desgaste extremo.Os revestimentos também permitem a reutilização de peças existentes, minimizando a necessidade de novo fabrico e resolvendo a escassez de material.Em geral, os revestimentos são uma solução económica e eficiente para melhorar a durabilidade e a eficiência operacional.
Explicação dos pontos principais:
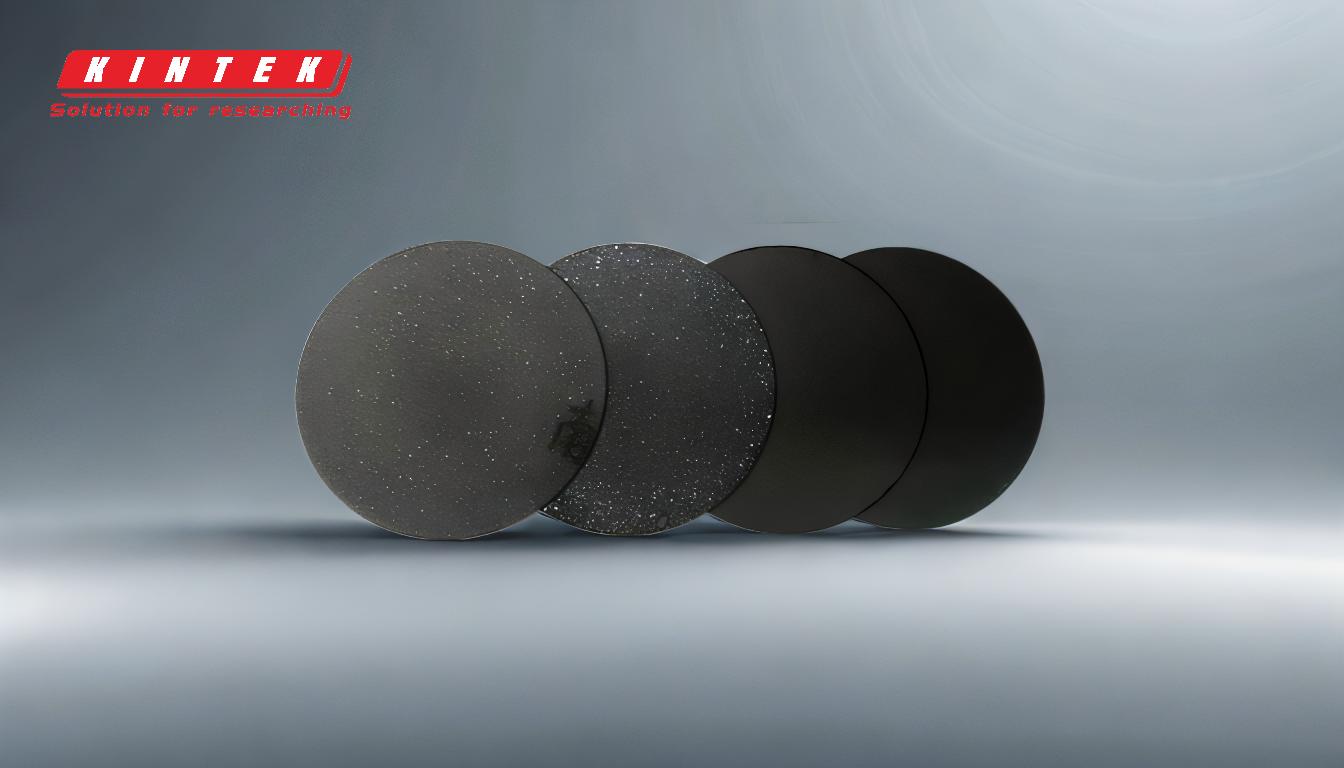
-
Proteção contra danos mecânicos:
- Os revestimentos actuam como uma barreira protetora, protegendo o material subjacente do desgaste causado pela fricção, abrasão e impacto.Isto é crucial para componentes expostos a condições de funcionamento difíceis, tais como ferramentas de corte, peças de motores e maquinaria industrial.
- Ao reduzir o contacto direto entre as superfícies, os revestimentos minimizam a perda de material e a deformação, garantindo uma vida útil mais longa.
-
Dureza de superfície melhorada:
- Os revestimentos aumentam frequentemente a dureza da superfície dos materiais, tornando-os mais resistentes a riscos, amolgadelas e outras formas de danos mecânicos.Isto é conseguido através de materiais como o carbono tipo diamante (DLC), nitreto de titânio (TiN) ou revestimentos cerâmicos.
- O aumento da dureza está diretamente relacionado com uma melhor resistência ao desgaste, uma vez que as superfícies mais duras são menos propensas à deformação sob tensão.
-
Eficiência de custos e sustentabilidade:
- A aplicação de revestimentos em peças existentes reduz a necessidade de substituições frequentes, diminuindo os custos de material e de produção.Isto é especialmente benéfico em indústrias onde os materiais de alto desempenho são caros ou escassos.
- Os revestimentos têm normalmente uma espessura de apenas micrómetros, o que significa que utilizam um mínimo de material, ao mesmo tempo que proporcionam benefícios funcionais significativos, contribuindo para os esforços de sustentabilidade.
-
Aumento da vida útil das ferramentas e dos componentes:
- Na indústria transformadora, os revestimentos das ferramentas de corte e dos componentes das máquinas prolongam significativamente a sua vida útil, reduzindo o desgaste.Isto leva a menos interrupções na produção e a menores custos de manutenção.
- Por exemplo, as ferramentas de corte revestidas podem funcionar a velocidades e temperaturas mais elevadas sem se degradarem, melhorando a eficiência e a qualidade da produção.
-
Aplicações específicas do sector:
- Indústria automóvel:Os revestimentos melhoram a resistência ao desgaste em componentes de motores, sistemas de travões e peças de transmissão, garantindo fiabilidade e desempenho em condições exigentes.
- Indústria aeroespacial:Os revestimentos reduzem o desgaste dos componentes das aeronaves, como as lâminas das turbinas e os trens de aterragem, ao mesmo tempo que proporcionam benefícios adicionais como a resistência à corrosão e a eficiência do combustível.
- Fabrico geral:Os revestimentos são utilizados em moldes, matrizes e outras ferramentas para resistir ao uso repetitivo e a ambientes agressivos.
-
Benefícios funcionais e estéticos:
- Para além da resistência ao desgaste, os revestimentos podem modificar a textura da superfície, melhorar o isolamento térmico ou elétrico e aumentar a molhabilidade ou a hidrofobicidade.Estas propriedades podem ser adaptadas a aplicações específicas, acrescentando valor funcional e estético.
- Por exemplo, os revestimentos decorativos na indústria automóvel não só protegem contra o desgaste como também melhoram o aspeto visual dos veículos.
-
Redução da escassez de materiais:
- Ao prolongar a vida útil dos componentes existentes, os revestimentos reduzem a procura de matérias-primas, abordando questões de escassez de materiais e promovendo a conservação de recursos.
- Isto é particularmente importante para as indústrias que dependem de materiais raros ou dispendiosos, como a indústria aeroespacial e a indústria transformadora de alta tecnologia.
Em resumo, os revestimentos são indispensáveis para a resistência ao desgaste devido à sua capacidade de proteger, endurecer e prolongar a vida útil de materiais e componentes.Oferecem uma solução económica, sustentável e versátil para combater o desgaste, tornando-os uma tecnologia crítica em várias indústrias.
Tabela de resumo:
Principais benefícios dos revestimentos | Detalhes |
---|---|
Proteção contra danos mecânicos | Protege os materiais contra a fricção, a abrasão e o impacto, garantindo uma vida útil mais longa. |
Dureza de superfície melhorada | Aumenta a resistência a riscos e amolgadelas utilizando materiais como DLC, TiN ou cerâmica. |
Eficiência de custos e sustentabilidade | Reduz as necessidades de substituição, diminui os custos e promove a sustentabilidade. |
Aumento da vida útil das ferramentas e dos componentes | Melhora a vida útil das ferramentas de corte e da maquinaria, reduzindo os custos de manutenção. |
Aplicações específicas do sector | Utilizado na indústria automóvel, aeroespacial e de fabrico para resistência ao desgaste e desempenho. |
Benefícios funcionais e estéticos | Adiciona textura à superfície, isolamento e atração visual. |
Redução da escassez de materiais | Prolonga a vida útil dos componentes, reduzindo a procura de matérias-primas. |
Saiba como os revestimentos podem aumentar a eficiência da sua indústria- contacte-nos hoje !