A evaporação por feixe de electrões e os sistemas de pulverização iónica são ambas técnicas de deposição física de vapor (PVD) utilizadas para criar películas finas, mas diferem significativamente nos seus mecanismos, parâmetros operacionais e aplicações. A evaporação por feixe de electrões utiliza um feixe de electrões focalizado para aquecer e vaporizar materiais a alta temperatura, o que resulta numa elevada taxa de deposição e na adequação a aplicações como painéis solares e vidro. A pulverização catódica, por outro lado, envolve o bombardeamento de um material alvo com iões energéticos para ejetar átomos, que depois se depositam num substrato. A pulverização catódica funciona a temperaturas mais baixas, proporciona uma melhor adesão e homogeneidade da película e é ideal para substratos complexos e películas finas de elevada pureza. Cada método tem vantagens distintas, dependendo dos requisitos específicos do projeto.
Pontos-chave explicados:
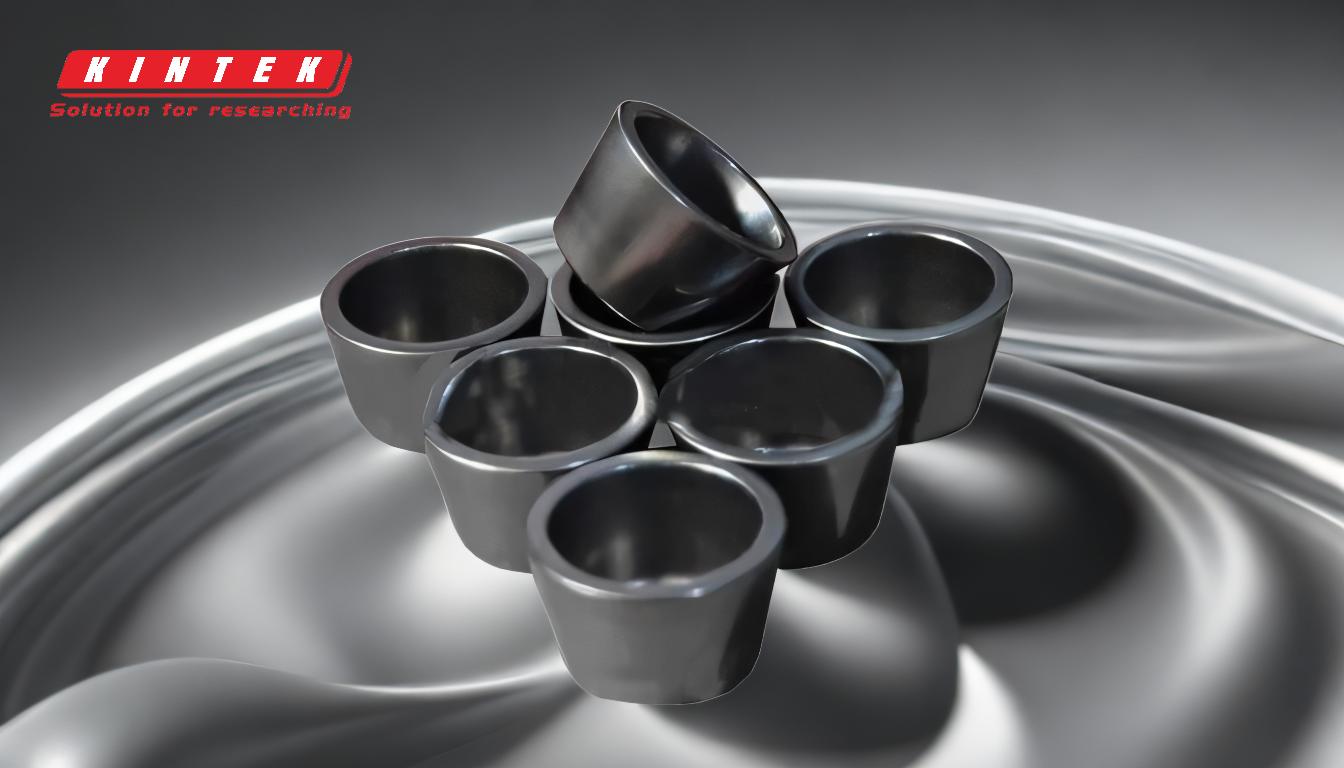
-
Mecanismo de deposição:
- Evaporação por feixe de electrões: Utiliza um feixe de electrões focalizado para aquecer e vaporizar o material de origem. O material vaporizado condensa-se no substrato para formar uma película fina.
- Sputtering de iões: Envolve o bombardeamento de um material alvo com iões energéticos (normalmente árgon) num ambiente de plasma. A colisão ejecta átomos do alvo, que depois se depositam no substrato.
-
Ambiente operacional:
- Evaporação por feixe de electrões: Requer um ambiente de alto vácuo para minimizar a contaminação e garantir uma vaporização eficiente.
- Sputtering de iões: Funciona num ambiente de vácuo mais baixo e frequentemente num campo magnético fechado para melhorar a ionização e a eficiência da deposição.
-
Taxa de deposição:
- Evaporação por feixe de electrões: Oferece uma taxa de deposição mais elevada, tornando-a adequada para aplicações que requerem uma formação rápida de película.
- Sputtering de iões: Geralmente tem uma taxa de deposição mais baixa, especialmente para materiais dieléctricos, mas proporciona um melhor controlo das propriedades da película.
-
Adesão e qualidade da película:
- Evaporação por feixe de electrões: Produz películas com menor aderência e menos homogéneas, o que pode exigir tratamentos pós-deposição.
- Sputtering de iões: Proporciona melhor aderência, maior homogeneidade da película e tamanhos de grão mais pequenos, resultando em películas finas de maior qualidade.
-
Requisitos de temperatura:
- Evaporação por feixe de electrões: Requer temperaturas elevadas para vaporizar o material de origem, o que pode limitar a sua utilização com substratos sensíveis à temperatura.
- Sputtering de iões: Funciona a temperaturas mais baixas, tornando-o adequado para materiais sensíveis à temperatura e substratos complexos.
-
Escalabilidade e automação:
- Evaporação por feixe de electrões: Menos escalável e mais difícil de automatizar devido à sua dependência do alto vácuo e do controlo preciso do feixe de electrões.
- Sputtering de iões: Mais escalável e mais fácil de automatizar, o que a torna ideal para produção em grande escala e aplicações industriais.
-
Aplicações:
- Evaporação por feixe de electrões: Normalmente utilizado em aplicações como painéis solares, revestimentos de vidro e películas ópticas devido à sua elevada taxa de deposição.
- Sputtering de iões: Preferida para a produção eléctrica e ótica, películas finas de elevada pureza e revestimentos em substratos complexos, devido à sua qualidade superior de película e adesão.
-
Energia das espécies depositadas:
- Evaporação por feixe de electrões: Produz espécies de vapor de baixa energia, o que pode resultar em películas menos densas.
- Sputtering de iões: Ejecta átomos de energia mais elevada, dando origem a películas mais densas e mais aderentes.
-
Absorção de gás:
- Evaporação por feixe de electrões: Menos propensa à absorção de gás devido ao ambiente de alto vácuo.
- Sputtering de iões: Mais suscetível de absorver gases, o que pode afetar as propriedades da película, mas também permite a pulverização reactiva para criar películas compostas.
-
Direccionalidade das partículas atomizadas:
- Evaporação por feixe de electrões: Produz um fluxo de vapor mais disperso, o que pode levar a uma deposição menos direcional.
- Sputtering de iões: Ejecta partículas de uma forma mais direcional, melhorando a cobertura em geometrias complexas.
Em resumo, a escolha entre a evaporação por feixe de electrões e a pulverização iónica depende dos requisitos específicos do projeto, tais como a taxa de deposição, a qualidade da película, a complexidade do substrato e a escalabilidade. Cada método tem as suas vantagens e limitações únicas, tornando-os adequados para diferentes aplicações na deposição de películas finas.
Tabela de resumo:
Aspeto | Evaporação por feixe de electrões | Sputtering de iões |
---|---|---|
Mecanismo | Um feixe de electrões focalizado aquece e vaporiza os materiais. | Os iões energéticos bombardeiam o material alvo para ejetar átomos. |
Ambiente operacional | É necessário vácuo elevado. | Vácuo mais baixo, frequentemente com um campo magnético. |
Taxa de deposição | Maior taxa de deposição. | Menor taxa de deposição, melhor controlo das propriedades da película. |
Adesão e qualidade da película | Menor adesão, menor homogeneidade. | Melhor aderência, maior homogeneidade, tamanhos de grão mais pequenos. |
Temperatura | São necessárias temperaturas elevadas, menos adequadas para substratos sensíveis. | Temperaturas mais baixas, ideal para materiais sensíveis e substratos complexos. |
Escalabilidade | Menos escalável, mais difícil de automatizar. | Mais escalável, mais fácil de automatizar para produção em grande escala. |
Aplicações | Painéis solares, revestimentos de vidro, películas ópticas. | Produção eléctrica/ótica, películas de elevada pureza, substratos complexos. |
Energia dos átomos depositados | Espécies de vapor de menor energia, películas menos densas. | Átomos de energia mais elevada, películas mais densas e mais aderentes. |
Absorção de gases | Menos propensos à absorção de gases. | Mais suscetível de absorver gases, permitindo a pulverização reactiva. |
Direccionalidade | Fluxo de vapor disperso, menos direcional. | Mais direcional, melhor cobertura em geometrias complexas. |
Precisa de ajuda para escolher a técnica de PVD certa para o seu projeto? Contacte os nossos especialistas hoje para obter orientação personalizada!