A sinterização é um processo crítico na indústria do aço, em que os materiais em pó, como o minério de ferro, são compactados e aquecidos abaixo do seu ponto de fusão para formar materiais densos, fortes e porosos.Este processo melhora as propriedades mecânicas dos materiais, reduz a porosidade e melhora a sua adequação para utilização em altos-fornos.A sinterização envolve a mistura de pó de minério de ferro com coque e cal, a ignição da mistura e a passagem de ar através dela para criar uma reação de combustão.O minério sinterizado resultante é utilizado como clínquer na produção de ferro, melhorando a eficiência do alto-forno e reduzindo os custos.A sinterização é também utilizada noutras indústrias, como a cerâmica e o fabrico de aditivos, para criar formas complexas e materiais de elevado desempenho.
Pontos-chave explicados:
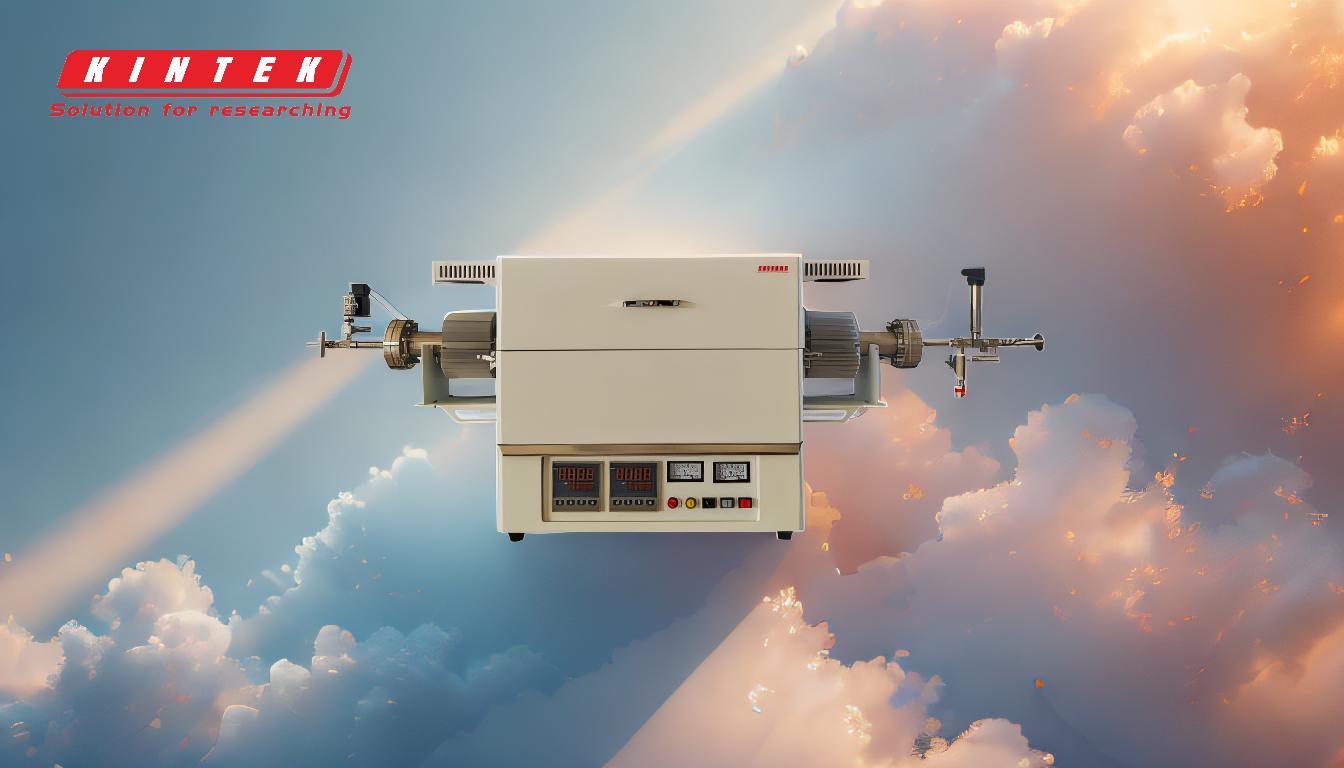
-
Definição e objetivo da sinterização:
- A sinterização é um processo que compacta e funde materiais em pó, como o minério de ferro, utilizando calor e pressão abaixo do ponto de fusão do material.
- O objetivo principal é melhorar as propriedades mecânicas do material, como a resistência, a dureza e a porosidade, tornando-o adequado para aplicações industriais como a produção de aço.
-
Materiais utilizados na sinterização:
- Na indústria siderúrgica, a sinterização envolve normalmente uma mistura de pó de minério de ferro, coque (uma forma de carvão) e cal.
- Estes materiais são combinados em rácios específicos para garantir que o produto sinterizado tem a resistência e a granularidade desejadas.
-
O processo de sinterização:
- A mistura é colocada numa grelha móvel e inflamada com um queimador de gás.
- O ar é aspirado através do leito para iniciar uma reação de combustão, gerando um calor elevado.
- Este calor faz com que as minúsculas partículas de metal se fundam, formando grumos ou clínquer.
- O produto sinterizado é então arrefecido e triturado até ao tamanho adequado para utilização em altos-fornos.
-
Papel na produção de aço:
- O minério sinterizado é uma matéria-prima essencial nos altos-fornos para a produção de ferro.
- Melhora o coeficiente de utilização dos altos-fornos, reduz o rácio de coqueificação e aumenta a permeabilidade do forno, assegurando um funcionamento suave e eficiente.
- Ao utilizar minério sinterizado, os produtores de aço podem obter poupanças de custos e um melhor controlo da qualidade do produto final.
-
Benefícios da sinterização:
- Propriedades melhoradas do material:A sinterização reduz a porosidade e melhora a resistência, a tenacidade e a condutividade térmica.
- Eficiência de custos:O processo permite a utilização de matérias-primas de baixo custo e reduz o consumo de energia em comparação com a fusão.
- Versatilidade:A sinterização pode ser utilizada para criar formas complexas e geometrias intrincadas que são difíceis de obter com os métodos de fabrico tradicionais.
- Benefícios ambientais:Ao melhorar a eficiência do alto-forno, a sinterização ajuda a reduzir as emissões de carbono e os resíduos.
-
Aplicações para além do aço:
- A sinterização é também utilizada na produção de cerâmica, vidro e metais refractários como o tungsténio e o molibdénio.
- No fabrico de aditivos (impressão 3D), a sinterização é utilizada para criar peças metálicas de elevado desempenho com dimensões precisas e desenhos complexos.
-
Comparação com outros processos:
- Ao contrário da fusão, a sinterização não requer que o material atinja o seu ponto de fusão, o que a torna adequada para materiais com temperaturas de fusão elevadas.
- É um processo mais eficiente em termos energéticos em comparação com a fusão e a fundição, uma vez que funciona a temperaturas mais baixas.
-
Desafios e considerações:
- O processo de sinterização requer um controlo preciso da temperatura, da pressão e da composição do material para garantir uma qualidade consistente.
- As poeiras e emissões geradas durante a sinterização têm de ser geridas para cumprir os regulamentos ambientais.
Ao compreender o processo de sinterização, os fabricantes de aço podem otimizar as suas operações, melhorar a qualidade do produto e reduzir os custos, tornando-o um componente vital da produção industrial moderna.
Tabela de resumo:
Aspeto | Detalhes |
---|---|
Definição | Compacta e funde materiais em pó utilizando calor e pressão abaixo da fusão. |
Materiais utilizados | Pó de minério de ferro, coque e cal. |
Processo | Mistura inflamada, ar aspirado, partículas que se fundem para formar clínquer. |
Papel na produção de aço | Melhora a eficiência do alto-forno e reduz os custos. |
Vantagens | Maior resistência, eficiência de custos, versatilidade e benefícios ambientais. |
Aplicações | Aço, cerâmica, vidro, metais refractários, fabrico aditivo. |
Desafios | Requer um controlo preciso da temperatura, pressão e gestão de poeiras. |
Optimize a sua produção de aço com a sinterização- contacte hoje os nossos especialistas para obter soluções à medida!