A sinterização de materiais argilosos é um processo de tratamento térmico que transforma a argila em pó num corpo cerâmico denso, forte e durável.Este processo envolve o aquecimento da argila abaixo do seu ponto de fusão, permitindo que as partículas se liguem através da difusão no estado sólido, resultando numa redução da porosidade, aumento da densidade e melhoria das propriedades mecânicas.A sinterização é fundamental para alcançar a microestrutura desejada, a estabilidade dimensional e as caraterísticas funcionais dos produtos cerâmicos.É amplamente utilizada nas indústrias para criar formas complexas, melhorar as propriedades dos materiais e permitir uma produção em massa económica.
Pontos-chave explicados:
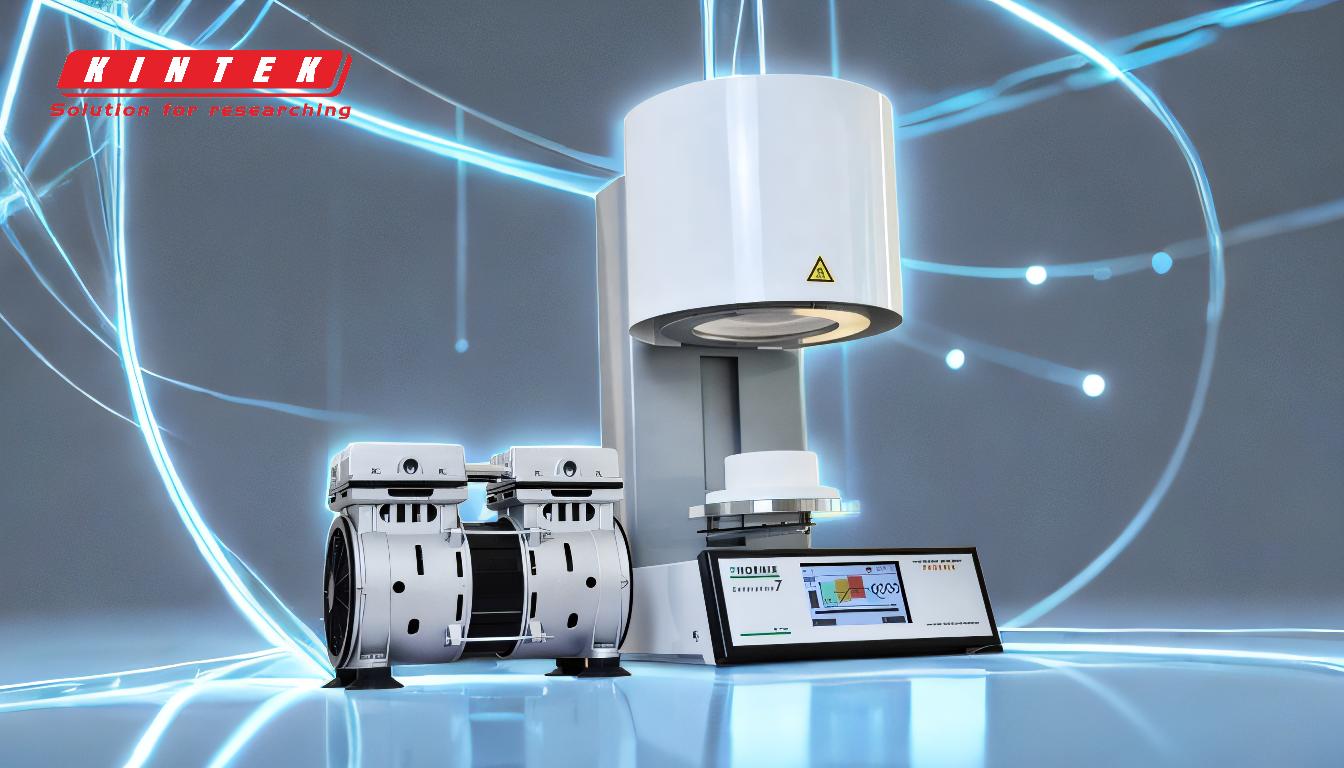
-
Definição de Sinterização:
- A sinterização é um processo térmico utilizado para densificar materiais em pó, como a argila, aquecendo-os abaixo do seu ponto de fusão.Este processo transforma as partículas soltas numa estrutura sólida e coesa através da ligação das partículas e da eliminação dos poros.
-
Objetivo da Sinterização:
- Densificação:Reduz a porosidade e aumenta a densidade do material.
- Aumento da resistência:Melhora as propriedades mecânicas como a dureza, a tenacidade e a durabilidade.
- Formação da microestrutura:Cria uma microestrutura uniforme e estável com propriedades específicas.
- Estabilidade dimensional:Tem em conta as pequenas contracções durante o processo para obter dimensões finais precisas.
-
Mecanismo de Sinterização:
- Difusão em estado sólido:Os átomos movem-se através das superfícies das partículas, pescoços e limites de grão, levando à ligação e densificação.
- Crescimento do grão:As partículas fundem-se e os grãos aumentam de tamanho, reduzindo os vazios e os limites dos grãos.
- Transferência de material:Os mecanismos de transferência de massa, como a difusão superficial e a evaporação-condensação, contribuem para a densificação.
-
Fases da Sinterização:
- Fase inicial:Rearranjo de partículas e formação de pescoço entre as partículas.
- Fase intermédia:Os poros ficam interligados e a densificação acelera-se.
- Fase final:Os poros ficam isolados e o material atinge uma densidade próxima da teórica.
-
Factores que influenciam a sinterização:
- Temperatura:As temperaturas mais elevadas favorecem a difusão e a ligação, mas devem manter-se abaixo do ponto de fusão.
- Tempo:Durações de sinterização mais longas permitem uma maior densificação e crescimento do grão.
- Atmosfera:Ambientes controlados (por exemplo, atmosferas inertes ou redutoras) evitam a oxidação e a contaminação.
- Tamanho das partículas:As partículas mais pequenas sinterizam mais eficazmente devido a uma maior energia de superfície.
- Aditivos:Os fluxos ou auxiliares de sinterização podem baixar a temperatura necessária e melhorar a densificação.
-
Aplicações da Sinterização em Materiais Argilosos:
- Cerâmica:Utilizado para produzir cerâmicas avançadas com propriedades adaptadas para aplicações electrónicas, aeroespaciais e médicas.
- Produtos estruturais:Cria tijolos, telhas e cerâmica com maior resistência e durabilidade.
- Formas complexas:Permite a produção de geometrias complexas que são difíceis de obter com outros métodos.
- Fabrico rentável:Reduz os custos de ferramentas e permite uma produção em massa rápida.
-
Vantagens da Sinterização:
- Versatilidade:Adequado para uma vasta gama de materiais, incluindo cerâmica, metais e compósitos.
- Precisão:Obtém-se uma elevada precisão dimensional e repetibilidade.
- Propriedades do material:Combina propriedades desejáveis como dureza, resistência à abrasão e estabilidade térmica.
- Sustentabilidade:Minimiza o desperdício de material e o consumo de energia em comparação com os processos de fusão.
-
Desafios da Sinterização:
- Retração:A redução de volume deve ser cuidadosamente controlada para evitar defeitos.
- Defeitos microestruturais:As não homogeneidades ou os poros residuais podem enfraquecer o produto final.
- Otimização do processo:O equilíbrio entre a temperatura, o tempo e a atmosfera exige um controlo preciso.
-
Comparação com outros processos:
- Sinterização vs. Fusão:A sinterização ocorre abaixo do ponto de fusão, preservando a composição e a forma originais do material.
- Sinterização vs. Compactação:A compactação forma o corpo verde, enquanto a sinterização o densifica e fortalece.
-
Tendências futuras na sinterização:
- Materiais avançados:Desenvolvimento de nanocompósitos e materiais funcionalmente graduados.
- Eficiência energética:Inovações na tecnologia dos fornos para reduzir o consumo de energia.
- Fabrico aditivo:Integração da sinterização com a impressão 3D para componentes complexos e de alto desempenho.
Em resumo, a sinterização é um processo transformador que desempenha um papel vital na produção de cerâmicas à base de argila e outros materiais.Ao compreender os seus mecanismos, fases e factores de influência, os fabricantes podem otimizar o processo para obter propriedades materiais superiores e satisfazer diversas necessidades industriais.
Tabela de resumo:
Aspeto | Detalhes |
---|---|
Definição | Processo de tratamento térmico para densificar a argila em pó abaixo do seu ponto de fusão. |
Objetivo | Densificação, aumento da resistência, formação de microestruturas, estabilidade. |
Mecanismo | Difusão em estado sólido, crescimento de grão, transferência de material. |
Etapas | Fases inicial, intermédia e final da eliminação dos poros. |
Factores de influência | Temperatura, tempo, atmosfera, tamanho das partículas, aditivos. |
Aplicações | Cerâmica, produtos estruturais, formas complexas, fabrico rentável. |
Vantagens | Versatilidade, precisão, propriedades melhoradas do material, sustentabilidade. |
Desafios | Contração, defeitos microestruturais, otimização do processo. |
Tendências futuras | Materiais avançados, eficiência energética, fabrico de aditivos. |
Optimize a sua produção cerâmica com sinterização- contacte hoje os nossos especialistas para saber mais!