O processo de sinterização é uma técnica de fabrico fundamental utilizada para criar materiais sólidos e duradouros a partir de substâncias em pó.Envolve várias fases, começando com a preparação do pó, seguida da compactação para formar a forma desejada e, finalmente, o aquecimento do material para unir as partículas sem as fundir completamente.Este processo é amplamente utilizado em indústrias como a metalurgia do pó e a cerâmica para produzir componentes com elevada resistência e durabilidade.Em seguida, vamos explorar em pormenor os principais passos envolvidos no processo de sinterização.
Pontos-chave explicados:
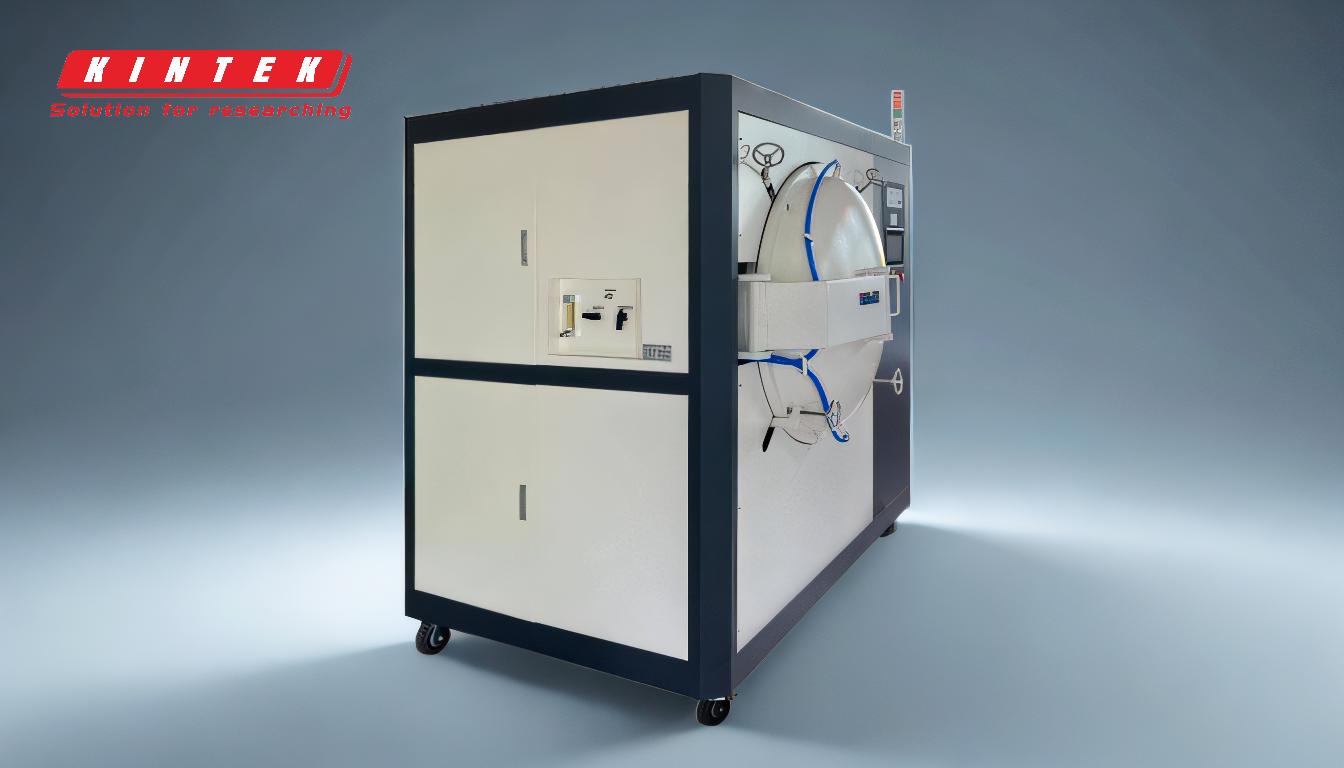
-
Preparação do pó de sinterização
- O primeiro passo envolve a seleção e preparação da matéria-prima em forma de pó.Isto inclui determinar a composição do pó metálico ou cerâmico e assegurar que é bem misturado para obter uniformidade.
- O pó pode ser pré-tratado para melhorar as suas propriedades, por exemplo, adicionando aglutinantes ou lubrificantes para facilitar a compactação.
-
Compactação do pó
- O pó preparado é então compactado na forma desejada utilizando alta pressão.Normalmente, isto é feito utilizando um molde ou matriz, o que garante que o pó é distribuído uniformemente e não tem espaços vazios.
- A compactação pode ser conseguida através de prensagem a frio, prensagem a quente ou outros métodos, dependendo do material e da aplicação.
-
Aquecimento num forno de sinterização
- O material compactado é colocado num forno de sinterização e aquecido a uma temperatura inferior ao seu ponto de fusão.Este aquecimento controlado permite que as partículas se liguem através da difusão, formando pescoços entre elas.
- A temperatura e a duração do aquecimento são cuidadosamente reguladas para atingir o nível desejado de densificação e resistência sem provocar a fusão do material.
-
Difusão e densificação de partículas
- Durante o processo de aquecimento, os átomos difundem-se através das fronteiras das partículas, levando à formação de uma estrutura coesa.Esta fase é crucial para reduzir a porosidade e aumentar a densidade do material.
- Em alguns casos, a sinterização em fase líquida (LPS) é utilizada para acelerar a densificação através da introdução de uma fase líquida que ajuda na fusão das partículas.
-
Arrefecimento e solidificação
- Após a fase de aquecimento, o material é arrefecido gradualmente para permitir a sua solidificação numa massa rígida e unificada.Este processo de arrefecimento é essencial para obter as propriedades mecânicas finais do produto sinterizado.
- A taxa de arrefecimento pode ser ajustada consoante o material e as caraterísticas pretendidas, como a dureza ou a tenacidade.
-
Tratamentos pós-sinterização (opcional)
- Nalguns casos, podem ser aplicados tratamentos adicionais, como maquinagem, acabamento de superfícies ou tratamento térmico, ao produto sinterizado para melhorar as suas propriedades ou cumprir requisitos de design específicos.
Ao seguir estes passos, o processo de sinterização transforma o pó solto num componente forte, durável e com uma forma precisa.Este método é particularmente valioso para materiais com pontos de fusão elevados ou para criar geometrias complexas que são difíceis de obter através de técnicas de fabrico tradicionais.
Tabela de resumo:
Passo | Descrição |
---|---|
1.Preparação do pó | Selecionar e misturar as matérias-primas; pré-tratar com aglutinantes ou lubrificantes para obter uniformidade. |
2.Compactação | Compactar o pó na forma desejada utilizando moldes ou matrizes sob alta pressão. |
3.Aquecimento no forno | Aquecer o material compactado abaixo do ponto de fusão para unir as partículas por difusão. |
4.Difusão de partículas | Os átomos difundem-se através das fronteiras, reduzindo a porosidade e aumentando a densidade. |
5.Arrefecimento e solidificação | Arrefecer o material gradualmente para solidificar numa massa rígida e unificada. |
6.Tratamentos pós-sinterização | Tratamentos opcionais como maquinagem ou tratamento térmico para melhorar as propriedades. |
Descubra como o processo de sinterização pode revolucionar o seu fabrico- contacte os nossos especialistas hoje !