No processo de revestimento por Deposição Física de Vapor (PVD), são utilizados vários gases, dependendo das propriedades de revestimento pretendidas e da técnica específica de PVD utilizada.O árgon é o gás inerte mais utilizado devido à sua natureza não reactiva, garantindo a pureza do material de revestimento durante a vaporização.Os gases reactivos, como o oxigénio, o azoto, o metano e o acetileno, também são utilizados para formar revestimentos compostos, como óxidos, nitretos e carbonetos.A escolha do gás depende do material de revestimento, do substrato e da aplicação pretendida para o produto revestido.
Pontos-chave explicados:
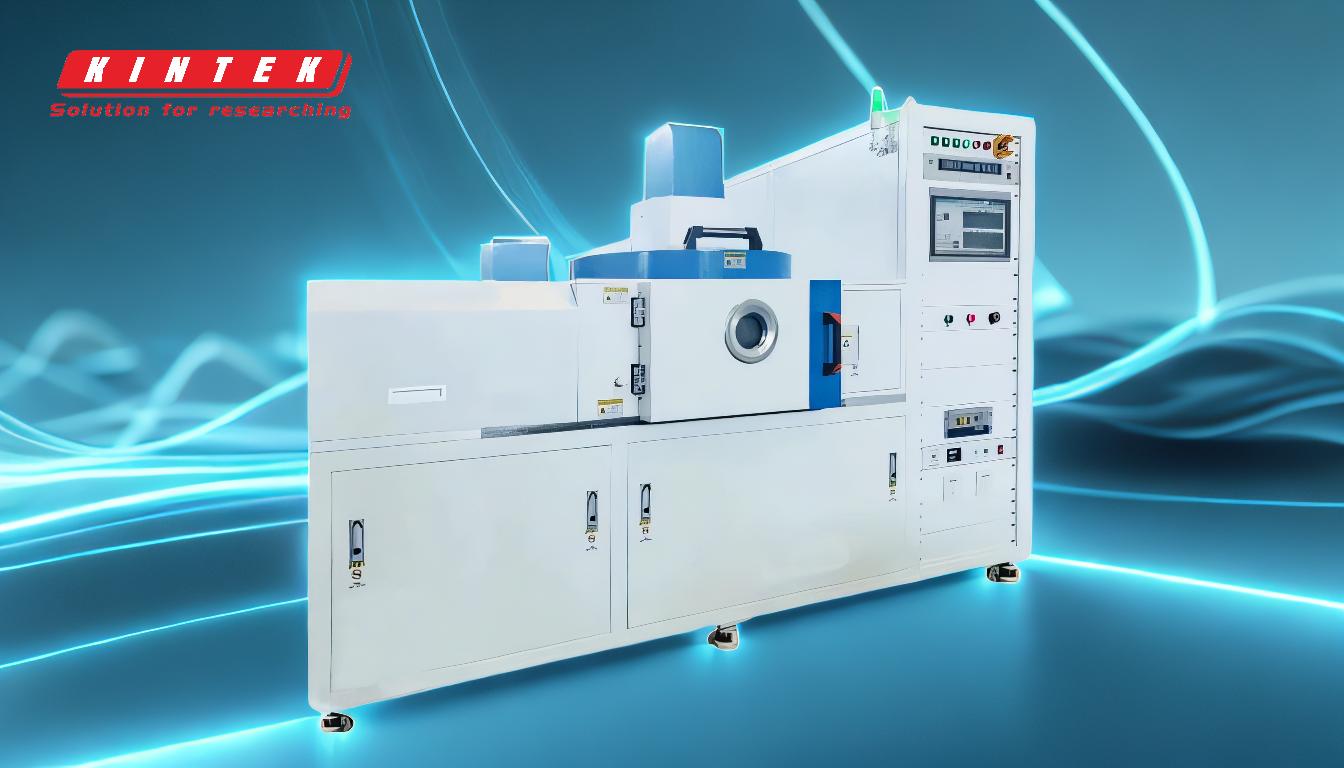
-
O árgon como principal gás inerte:
- Função:O árgon é amplamente utilizado em PVD porque é inerte, o que significa que não reage quimicamente com o material de revestimento ou com o substrato.Isto assegura que o material de revestimento permanece puro durante as fases de vaporização e deposição.
- Processo:Durante a pulverização catódica ou a evaporação por arco catódico, os iões de árgon são utilizados para bombardear o material alvo, provocando a sua vaporização e a formação de um plasma.O material vaporizado deposita-se então no substrato.
- Vantagens:A natureza inerte do árgon torna-o ideal para a criação de revestimentos metálicos puros sem a introdução de impurezas.
-
Gases reactivos para revestimentos compostos:
- Oxigénio (O2):Utilizado para formar revestimentos de óxidos metálicos (por exemplo, dióxido de titânio, óxido de alumínio).Estes revestimentos são frequentemente utilizados pela sua dureza, resistência ao desgaste e propriedades ópticas.
- Nitrogénio (N2):Reage com átomos de metal para formar nitretos (por exemplo, nitreto de titânio, nitreto de crómio), que são conhecidos pela sua dureza, resistência à corrosão e aparência decorativa semelhante ao ouro.
- Metano (CH4) e Acetileno (C2H2):Utilizado para criar revestimentos de carboneto (por exemplo, carboneto de titânio, carboneto de silício), que são extremamente duros e resistentes ao desgaste.O acetileno é particularmente utilizado para revestimentos de carbono tipo diamante (DLC).
- Hexa-Metil-Disiloxano (HMDSO):Utilizado na deposição de vapor químico assistida por plasma (PACVD) para criar revestimentos contendo silício, que são frequentemente utilizados pelas suas propriedades ópticas e de barreira.
-
Seleção de gás com base na técnica de PVD:
- Pulverização catódica por magnetrão:O árgon é o principal gás de pulverização catódica, mas podem ser introduzidos gases reactivos como o azoto ou o oxigénio para formar revestimentos compostos.
- Evaporação por arco catódico:O árgon é utilizado como gás primário, mas podem ser adicionados gases reactivos para modificar as propriedades do revestimento.
- Evaporação térmica ou por feixe de electrões:Normalmente, é utilizado árgon, mas podem ser introduzidos gases reactivos para formar revestimentos compostos.
-
Sistema de entrada de gás de processo:
- Fornecimento de gás:Os gases são fornecidos a partir de cilindros e controlados através de válvulas e medidores para garantir taxas de fluxo precisas.
- Câmara de vácuo:Os gases são introduzidos na câmara de vácuo, onde interagem com o material de revestimento vaporizado para formar o revestimento desejado.
-
Aplicações de diferentes gases:
- Revestimentos decorativos:O azoto é frequentemente utilizado para criar revestimentos semelhantes ao ouro para fins decorativos.
- Revestimentos funcionais:O oxigénio e o metano são utilizados para criar revestimentos duros e resistentes ao desgaste para aplicações industriais.
- Revestimentos ópticos:O HMDSO é utilizado para criar revestimentos com propriedades ópticas específicas.
-
Importância da pureza do gás:
- Os gases de alta pureza são essenciais para evitar a contaminação e garantir uma qualidade consistente do revestimento.As impurezas no gás podem levar a defeitos no revestimento, reduzindo o seu desempenho e durabilidade.
Ao selecionar cuidadosamente o gás ou a mistura de gases adequada, os fabricantes podem adaptar as propriedades do revestimento PVD para satisfazer requisitos de aplicação específicos, quer para fins decorativos, funcionais ou ópticos.
Tabela de resumo:
Tipo de gás | Papel no revestimento PVD | Aplicações comuns |
---|---|---|
Árgon (Ar) | Gás inerte para revestimentos metálicos puros, utilizado em processos de pulverização catódica e evaporação. | Revestimentos metálicos puros, garantindo a ausência de impurezas. |
Oxigénio (O2) | Forma revestimentos de óxidos metálicos (por exemplo, TiO2, Al2O3) para obter dureza e resistência ao desgaste. | Revestimentos duros e resistentes ao desgaste para aplicações industriais. |
Nitrogénio (N2) | Cria nitretos (por exemplo, TiN, CrN) para dureza, resistência à corrosão e decoração. | Revestimentos decorativos semelhantes ao ouro e camadas funcionais resistentes ao desgaste. |
Metano (CH4) | Forma revestimentos de carboneto (por exemplo, TiC, SiC) para extrema dureza e resistência ao desgaste. | Aplicações industriais que exigem elevada durabilidade. |
Acetileno (C2H2) | Utilizado para revestimentos de carbono tipo diamante (DLC). | Revestimentos de alto desempenho para ferramentas e maquinaria. |
HMDSO | Cria revestimentos contendo silício para propriedades ópticas e de barreira. | Revestimentos ópticos e camadas protectoras de barreira. |
Precisa de ajuda para selecionar os gases certos para o seu processo de revestimento PVD? Contacte hoje mesmo os nossos especialistas para soluções à medida!