Os revestimentos PVD (Physical Vapor Deposition) são conhecidos por sua excepcional dureza, durabilidade e versatilidade. Esses revestimentos são amplamente utilizados em indústrias que exigem materiais de alto desempenho, como microeletrônica, óptica e dispositivos médicos. A dureza de um revestimento PVD depende do material específico utilizado, com alguns revestimentos atingindo níveis extremos de dureza devido às suas propriedades e processos de deposição únicos. Entre os revestimentos PVD mais duros estão aqueles à base de carbono semelhante ao diamante (DLC) e nitreto de titânio (TiN), que são conhecidos por sua resistência superior ao desgaste, estabilidade em altas temperaturas e excelente adesão aos substratos. Isso os torna ideais para aplicações que exigem durabilidade e desempenho extremos.
Pontos-chave explicados:
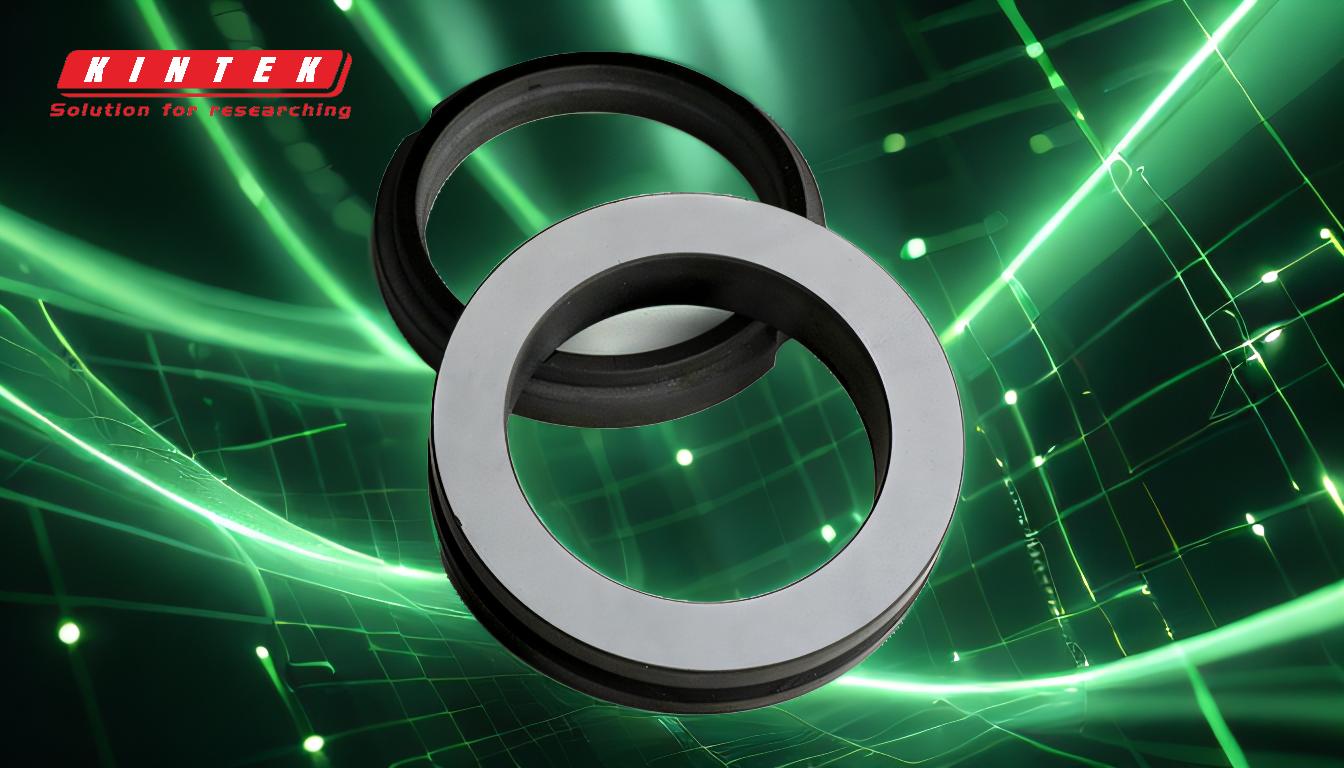
-
O que torna os revestimentos PVD duros?
- Os revestimentos PVD são criados através de um processo em que um material sólido é vaporizado no vácuo e depois depositado sobre um substrato. Este processo permite um controle preciso sobre as propriedades do revestimento, incluindo a dureza.
- A dureza dos revestimentos PVD é influenciada pelo material utilizado, pelo processo de deposição e pela microestrutura resultante. Materiais como carbono semelhante ao diamante (DLC) e nitreto de titânio (TiN) são particularmente duros devido às suas fortes ligações atômicas e estruturas densas.
-
Revestimentos de carbono tipo diamante (DLC)
- Os revestimentos DLC estão entre os revestimentos PVD mais duros disponíveis. Eles consistem em uma mistura de ligações de carbono sp2 (semelhante ao grafite) e sp3 (semelhante ao diamante), o que lhes confere dureza e resistência ao desgaste excepcionais.
- Esses revestimentos são usados em aplicações que exigem extrema durabilidade, como ferramentas de corte, componentes automotivos e dispositivos médicos. Eles também exibem baixo atrito e alta inércia química.
-
Revestimentos de nitreto de titânio (TiN)
- Os revestimentos TiN são outro exemplo de revestimentos PVD extremamente duros. Eles são conhecidos por sua cor dourada e são amplamente utilizados em aplicações industriais, incluindo ferramentas de corte e componentes de máquinas.
- Os revestimentos TiN proporcionam excelente dureza, resistência ao desgaste e estabilidade térmica, tornando-os adequados para ambientes de alto estresse.
-
Outros revestimentos PVD duros
- Outros revestimentos PVD duros incluem nitreto de titânio e alumínio (TiAlN), nitreto de cromo (CrN) e nitreto de zircônio (ZrN). Esses revestimentos oferecem um equilíbrio entre dureza, resistência à corrosão e estabilidade térmica, tornando-os adequados para aplicações especializadas.
- A escolha do revestimento depende dos requisitos específicos da aplicação, como ambiente operacional, material do substrato e atributos de desempenho desejados.
-
Vantagens dos revestimentos PVD duros
- Durabilidade: Os revestimentos PVD duros são altamente resistentes ao desgaste, à abrasão e ao impacto, prolongando a vida útil dos componentes revestidos.
- Estabilidade em altas temperaturas: Esses revestimentos podem suportar temperaturas extremas, tornando-os adequados para aplicações em altas temperaturas.
- Versatilidade: Os revestimentos PVD podem ser aplicados a uma ampla variedade de substratos, incluindo metais, cerâmicas e polímeros.
- Precisão e Controle: O processo PVD permite controle preciso sobre a espessura, composição e propriedades do revestimento, garantindo desempenho ideal.
-
Aplicações de revestimentos PVD duros
- Ferramentas Industriais: Ferramentas de corte, brocas e moldes se beneficiam da dureza e da resistência ao desgaste dos revestimentos PVD.
- Aeroespacial e Automotivo: Componentes expostos a altas tensões e temperaturas, como peças de motores e pás de turbinas, são frequentemente revestidos com materiais PVD duros.
- Dispositivos Médicos: Os instrumentos cirúrgicos e implantes utilizam revestimentos PVD pela sua biocompatibilidade e durabilidade.
- Eletrônica e Óptica: Os revestimentos PVD são usados em microchips, lentes ópticas e painéis solares devido aos seus atributos de pureza e desempenho.
Em resumo, os revestimentos PVD mais duros, como DLC e TiN, são altamente valorizados pela sua excepcional dureza, durabilidade e versatilidade. Esses revestimentos são essenciais em indústrias que exigem materiais que possam suportar condições extremas e proporcionar desempenho duradouro. O controle preciso oferecido pelo processo PVD garante que esses revestimentos atendam às necessidades específicas de diversas aplicações, tornando-os um componente crítico na fabricação e na tecnologia modernas.
Tabela Resumo:
Tipo de revestimento | Propriedades principais | Aplicativos |
---|---|---|
Carbono semelhante a diamante (DLC) | Dureza extrema, baixo atrito, alta inércia química | Ferramentas de corte, componentes automotivos, dispositivos médicos |
Nitreto de Titânio (TiN) | Excelente dureza, resistência ao desgaste, estabilidade térmica | Ferramentas industriais, componentes de máquinas |
Nitreto de titânio e alumínio (TiAlN) | Dureza equilibrada, resistência à corrosão, estabilidade térmica | Aplicações industriais especializadas |
Nitreto de cromo (CrN) | Alta dureza, resistência à corrosão | Indústrias aeroespacial, automotiva e médica |
Nitreto de Zircônio (ZrN) | Dureza superior, estabilidade térmica | Eletrônica, óptica e ambientes de alto estresse |
Encontre o revestimento PVD perfeito para sua aplicação— entre em contato com nossos especialistas hoje para começar!