O revestimento por Deposição Física de Vapor (PVD) é um processo sofisticado utilizado para depositar películas finas de material num substrato, melhorando as suas propriedades, como a resistência ao desgaste, a dureza e o aspeto estético.O processo envolve o aquecimento de um material alvo até à sua vaporização e, em seguida, a deposição do vapor na superfície do substrato.Os materiais comuns utilizados nos revestimentos PVD incluem metais como o titânio, o crómio, o tungsténio e o alumínio, que são frequentemente combinados com gases reactivos como o azoto ou os hidrocarbonetos para formar revestimentos como nitretos e carbonitretos.O processo PVD é versátil, capaz de incorporar uma vasta gama de materiais inorgânicos e alguns materiais orgânicos, tornando-o adequado para várias aplicações, desde revestimentos decorativos duradouros a componentes aeroespaciais de elevado desempenho.
Explicação dos pontos principais:
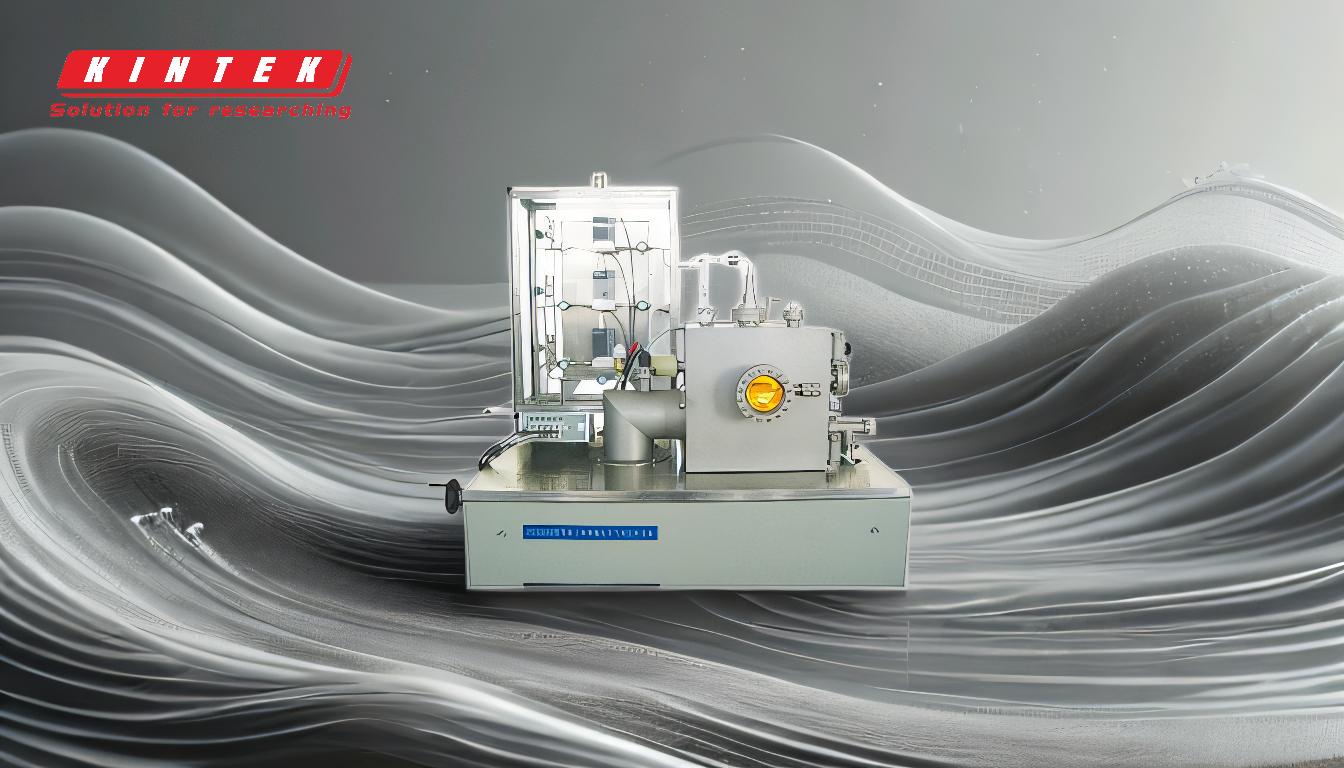
-
Materiais alvo no revestimento PVD:
- Metais e ligas metálicas:Os metais mais comuns utilizados nos revestimentos PVD incluem o titânio, o crómio, o tungsténio e o alumínio.Estes metais são escolhidos pelas suas propriedades específicas, como a dureza, a resistência ao desgaste e a capacidade de formar ligações fortes com gases reactivos.
- Cerâmica e Compostos:A PVD também pode depositar cerâmicas e compostos como carbonetos, nitretos, silicetos e boretos.Estes materiais são frequentemente utilizados em aplicações especializadas que exigem um elevado desempenho, tais como componentes aeroespaciais e automóveis.
- Elementos da Tabela Periódica:O processo pode utilizar uma vasta gama de elementos da tabela periódica, permitindo a criação de revestimentos únicos adaptados a necessidades específicas.
-
Gases reactivos:
- Azoto:Frequentemente utilizado para formar revestimentos de nitreto, que são conhecidos pela sua dureza e resistência ao desgaste.Por exemplo, o nitreto de titânio (TiN) é um revestimento PVD comum utilizado em ferramentas de corte.
- Gases à base de hidrocarbonetos:Estes gases são utilizados para criar revestimentos de carbonitreto, que combinam as propriedades dos carbonetos e dos nitretos.São particularmente úteis em aplicações que requerem dureza e baixa fricção.
-
Materiais de substrato:
- Materiais de base:O substrato, ou material de base, pode ser feito de vários materiais, incluindo metais, plásticos e cerâmicas.A escolha do substrato depende da aplicação pretendida e das propriedades desejadas do produto final.
- Preparação da superfície:Antes do processo de revestimento PVD, o substrato é frequentemente submetido a uma preparação da superfície, como a limpeza e o polimento, para garantir a aderência correta do revestimento.
-
Processo de revestimento PVD:
- Vaporização:O material alvo é aquecido até vaporizar.Isto pode ser conseguido através de métodos como a pulverização catódica ou a evaporação.
- Deposição:O material vaporizado é então depositado na superfície do substrato, formando uma película fina.A espessura da película pode variar entre alguns nanómetros e alguns micrómetros.
- Uniformidade:O processo PVD é conhecido por produzir revestimentos uniformes, que são essenciais para um desempenho e aparência consistentes.
-
Aplicações dos revestimentos PVD:
- Revestimentos decorativos duráveis:Utilizado em produtos em que tanto a durabilidade como o aspeto estético são importantes, tais como relógios, jóias e produtos electrónicos de consumo.
- Revestimentos de desempenho:Aplicado a componentes que requerem propriedades mecânicas melhoradas, tais como ferramentas de corte, moldes e peças de motor.
- Revestimentos de carbono tipo diamante (DLC):Estes revestimentos oferecem elevada dureza e baixa fricção, o que os torna ideais para aplicações nas indústrias automóvel e aeroespacial.
- Alternativas ao cromo PVD:Utilizado como uma alternativa ecológica à cromagem tradicional, oferecendo propriedades estéticas e de proteção semelhantes.
-
Vantagens do revestimento PVD:
- Propriedades melhoradas:Os revestimentos PVD melhoram a resistência ao desgaste, a dureza e a resistência à corrosão do substrato.
- Apelo estético:O processo pode produzir revestimentos com uma variedade de cores e acabamentos, melhorando a atração visual do produto.
- Impacto ambiental:O PVD é considerado um processo amigo do ambiente devido ao seu mínimo de resíduos e menor consumo de energia em comparação com os métodos de revestimento tradicionais.
Ao compreender estes componentes e processos fundamentais, é possível apreciar a versatilidade e a eficácia dos revestimentos PVD em várias aplicações industriais.
Tabela de resumo:
Componente | Descrição |
---|---|
Materiais alvo | Metais (por exemplo, titânio, crómio), cerâmicas e elementos da tabela periódica. |
Gases reactivos | Azoto, hidrocarbonetos (por exemplo, para revestimentos de nitreto e carbonitreto). |
Materiais de substrato | Metais, plásticos, cerâmicas; requer preparação da superfície para adesão. |
Processo | Métodos de vaporização e deposição (por exemplo, pulverização catódica, evaporação). |
Aplicações | Revestimentos decorativos duradouros, revestimentos de desempenho, DLC, alternativas ao crómio PVD. |
Vantagens | Maior resistência ao desgaste, dureza, resistência à corrosão e apelo estético. |
Liberte o potencial dos revestimentos PVD para as suas aplicações- contacte hoje os nossos especialistas !