Os revestimentos tipo diamante (DLC) são aplicados utilizando técnicas avançadas de deposição, principalmente a Deposição Física de Vapor (PVD) e a Deposição Química de Vapor (CVD).Estes métodos envolvem a criação de uma camada fina e durável de carbono tipo diamante (DLC) na superfície de ferramentas ou componentes.O PVD envolve a evaporação de um material de origem e permite que este se condense na ferramenta, formando uma monocamada de DLC com uma espessura típica de 0,5 a 2,5 microns.O CVD, por outro lado, utiliza gases de hidrogénio e metano numa câmara, onde fios de tungsténio aquecidos a mais de 2.300°C decompõem os gases, permitindo que os átomos de carbono se recombinem e formem uma película de diamante puro na superfície da ferramenta.Ambos os métodos requerem um controlo preciso da temperatura, da pressão e da composição do gás para obter os melhores resultados.
Pontos-chave explicados:
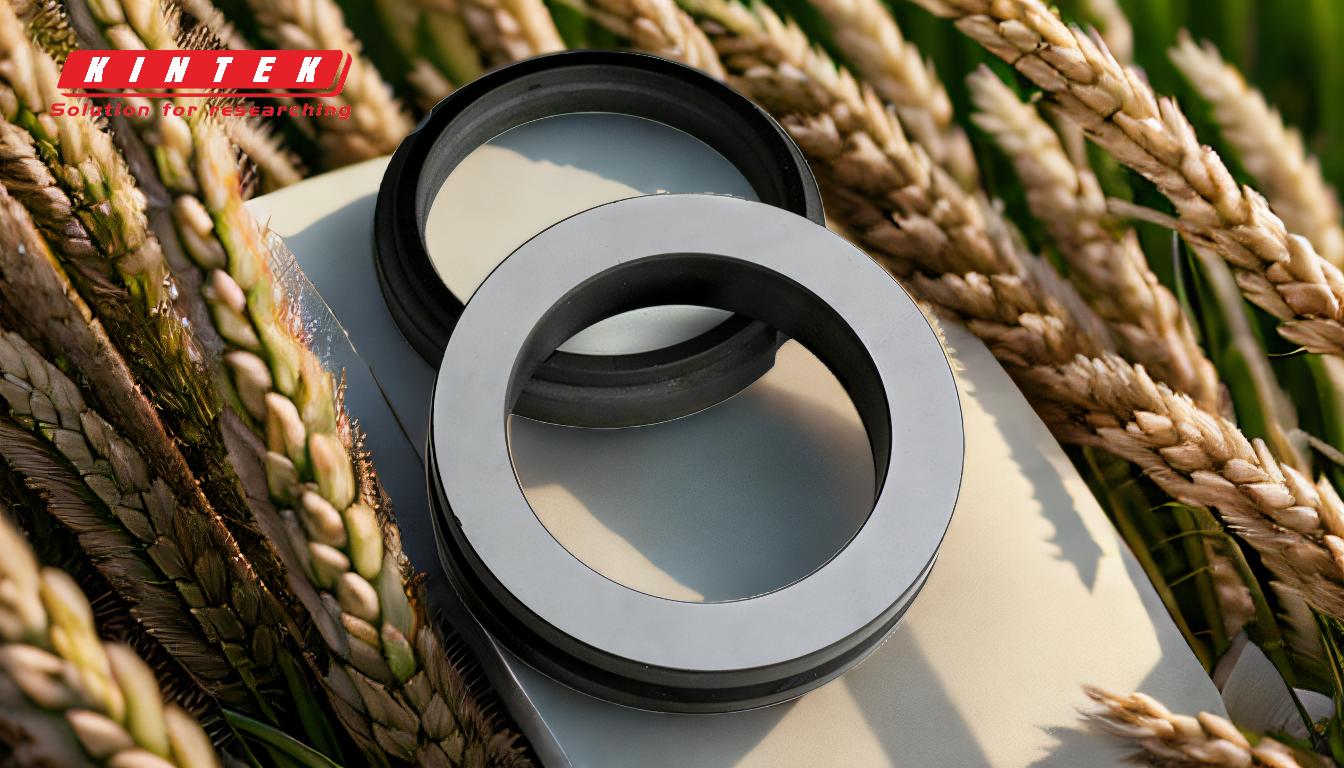
-
Visão geral dos revestimentos tipo diamante (DLC):
- Os revestimentos DLC são camadas finas, duras e resistentes ao desgaste aplicadas a ferramentas ou componentes para melhorar o seu desempenho e longevidade.
- Estes revestimentos são amorfos, o que significa que não têm uma estrutura cristalina, mas apresentam propriedades semelhantes às do diamante, tais como elevada dureza e baixa fricção.
-
Métodos de revestimento primário:
-
Deposição Física de Vapor (PVD):
- O PVD é um método amplamente utilizado para aplicar revestimentos DLC.
- O processo envolve a evaporação de um material de origem (frequentemente à base de carbono) numa câmara de vácuo.
- O material evaporado condensa-se então na superfície da ferramenta, formando uma camada fina e uniforme de DLC.
- A espessura do revestimento varia normalmente entre 0,5 e 2,5 microns.
- A PVD é conhecida pela sua capacidade de produzir revestimentos aderentes de alta qualidade com excelente resistência ao desgaste.
-
Deposição de vapor químico (CVD):
- O CVD é outro método comum de aplicação de revestimentos DLC.
- Neste processo, a ferramenta é colocada numa câmara cheia de gases de hidrogénio e metano.
- Os fios de tungsténio aquecidos a mais de 2.300°C fornecem a energia necessária para quebrar as moléculas de gás.
- Os átomos de carbono activados recombinam-se então na superfície da ferramenta, formando uma película de diamante puro.
- A CVD é particularmente eficaz para criar revestimentos mais espessos e duráveis.
-
Deposição Física de Vapor (PVD):
-
Etapas do processo de aplicação de revestimentos DLC:
-
Preparação:
- A ferramenta ou o componente a revestir deve ser cuidadosamente limpo e preparado para garantir a correta aderência do revestimento.
- Isto envolve frequentemente a remoção de quaisquer contaminantes da superfície, tais como óleos ou óxidos, através de meios químicos ou mecânicos.
-
Carregamento na câmara:
- As ferramentas preparadas são carregadas na câmara de deposição.
- Em PVD, a câmara é evacuada para criar vácuo, enquanto que em CVD, a câmara é enchida com os gases apropriados.
-
Deposição:
- Para PVD, o material de origem é evaporado e o vapor condensa-se na superfície da ferramenta.
- No caso do CVD, os gases são activados e os átomos de carbono depositam-se na ferramenta.
-
Arrefecimento e acabamento:
- Após a deposição, as ferramentas revestidas são deixadas arrefecer lentamente para evitar tensões térmicas.
- O revestimento final é inspeccionado quanto à qualidade, espessura e aderência.
-
Preparação:
-
Principais parâmetros e considerações:
-
Temperatura:
- Os processos PVD e CVD requerem temperaturas elevadas, que variam normalmente entre 750°C e mais de 2.300°C, consoante o método.
- O controlo adequado da temperatura é crucial para garantir a qualidade e a aderência do revestimento.
-
Composição do gás:
- Na CVD, a composição dos gases hidrogénio e metano deve ser cuidadosamente controlada para se conseguir a deposição de carbono desejada.
-
Espessura do revestimento:
- A espessura do revestimento DLC é um fator crítico para determinar o seu desempenho.
- Os revestimentos mais espessos podem oferecer uma melhor resistência ao desgaste, mas também podem ser mais propensos a fissuras ou delaminação.
-
Adesão:
- Assegurar uma forte aderência entre o revestimento e o substrato é essencial para a durabilidade do revestimento.
- Isto envolve frequentemente o pré-tratamento do substrato ou a utilização de camadas intermédias.
-
Temperatura:
-
Aplicações dos revestimentos DLC:
- Os revestimentos DLC são utilizados numa vasta gama de indústrias, incluindo a automóvel, aeroespacial, dispositivos médicos e ferramentas de corte.
- São particularmente apreciados pela sua capacidade de reduzir o atrito, resistir ao desgaste e prolongar a vida útil dos componentes sujeitos a condições adversas.
-
Vantagens e limitações:
-
Vantagens:
- Elevada dureza e resistência ao desgaste.
- Baixo coeficiente de fricção, reduzindo o consumo de energia e melhorando a eficiência.
- Excelente resistência à corrosão.
- Capacidade de revestir geometrias complexas.
-
Limitações:
- Elevado custo do equipamento e do processo.
- Espessura limitada devido ao potencial de tensão interna e fissuração.
- Requer um controlo preciso dos parâmetros do processo.
-
Vantagens:
-
Tendências futuras:
- A investigação em curso centra-se na melhoria da adesão, espessura e uniformidade dos revestimentos DLC.
- Espera-se que os avanços na nanotecnologia e nos métodos de revestimento híbrido melhorem ainda mais o desempenho e a aplicabilidade dos revestimentos DLC em vários sectores.
Ao compreender estes pontos-chave, os compradores de equipamentos e consumíveis podem tomar decisões informadas sobre a aplicação de revestimentos tipo diamante, assegurando que selecionam o método e os parâmetros mais adequados às suas necessidades específicas.
Tabela de resumo:
Aspeto | Detalhes |
---|---|
Métodos primários | PVD (Deposição Física de Vapor), CVD (Deposição Química de Vapor) |
Espessura do revestimento | 0,5 a 2,5 mícrons (PVD), mais espessa para CVD |
Parâmetros-chave | Temperatura (750°C a 2.300°C), composição do gás, aderência, espessura do revestimento |
Aplicações | Indústria automóvel, aeroespacial, dispositivos médicos, ferramentas de corte |
Vantagens | Elevada dureza, baixa fricção, resistência à corrosão, geometrias complexas |
Limitações | Custo elevado, espessura limitada, necessidade de um controlo preciso dos parâmetros |
Optimize as suas ferramentas com revestimentos DLC avançados- contacte hoje os nossos especialistas para obter soluções à medida!