O objetivo dos processos de fabrico à base de pó
Índice
- O objetivo dos processos de fabrico à base de pó
- O processo de prensagem isostática a frio (CIP)
- O processo de prensagem isostática a quente (HIP)
- A oportunidade de pré-processamento de construções numa única etapa através do fabrico aditivo multimaterial
- A utilização da tecnologia de deposição selectiva da kintek na prensagem isostática
- O potencial de uma abordagem semelhante para peças processadas com HIP
- Conclusão: A ponte da deposição selectiva de pós entre o novo fabrico aditivo e o fabrico tradicional
O objetivo da maioria dos processos de fabrico à base de pó
O objetivo da maioria dosprocessos de fabrico baseados em pócomo a metalurgia do pó (PM), é produzir peças densas com menos de 1% de porosidade sem derreter o material de base. O pó solto utilizado nestes processos tem normalmente uma baixa densidade de empilhamento, com uma densidade máxima teórica de apenas 64% para partículas perfeitamente esféricas empilhadas aleatoriamente. No entanto, utilizando distribuições de tamanho de partículas de pó adequadas ou pós deformáveis, podem ser alcançadas densidades de empacotamento superiores a 90%.
As limitações da prensagem uniaxial
Para obter resultados satisfatórios nos processos de fabrico baseados em pó, a aplicação de pressão é crucial. A prensagem uniaxial, em que a pressão é aplicada numa única direção, é normalmente utilizada. No entanto, este método tem limitações, particularmente para peças espessas. Tende a resultar em diferenças de densidade ao longo da direção de prensagem, o que pode afetar a qualidade da peça final.
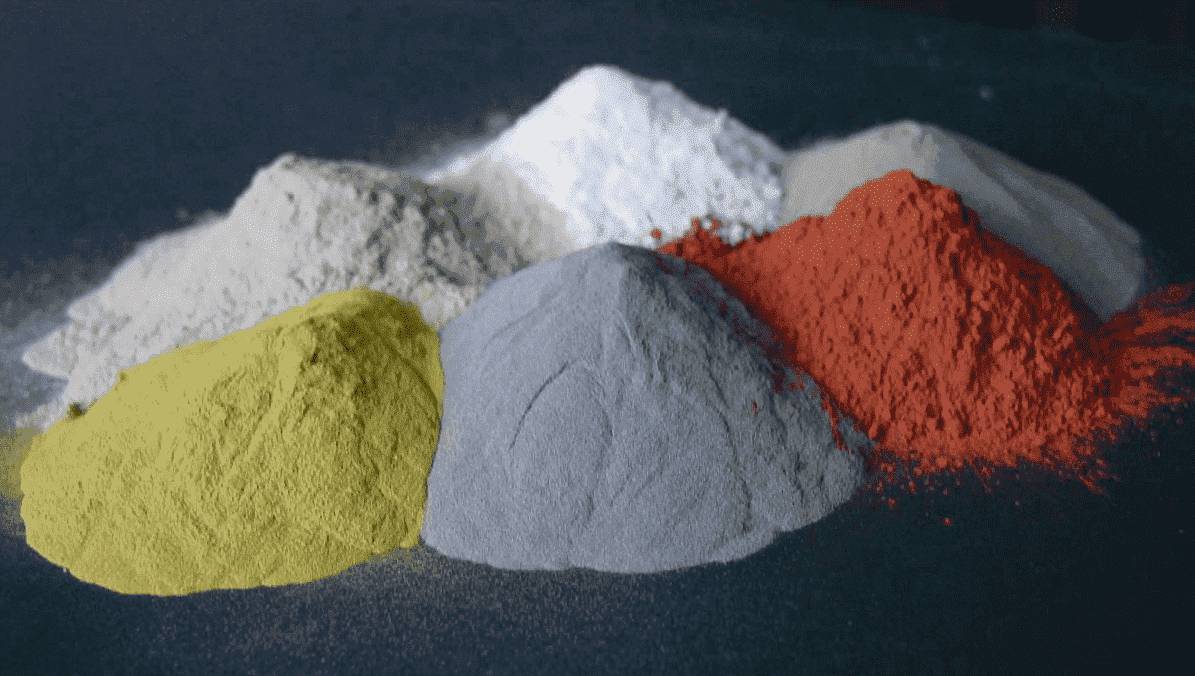
A solução: prensagem isostática
Para ultrapassar as limitações da prensagem uniaxial,prensagem isostática é frequentemente utilizada para peças a granel. A prensagem isostática é uma técnica de processamento de pó que utiliza a pressão do fluido para compactar a peça. Os pós metálicos são colocados num recipiente flexível, que serve de molde para a peça. A pressão do fluido é exercida sobre toda a superfície exterior do recipiente, fazendo com que este pressione e forme o pó na geometria desejada. Ao contrário da prensagem uniaxial, a prensagem isostática aplica pressão de todas as direcções, resultando numa distribuição de densidade mais uniforme.
Processos alternativos
Prensagem isostática
A prensagem isostática é um processo de fabrico à base de pó amplamente utilizado que aplica uma pressão uniforme para consolidar pós ou curar defeitos em peças fundidas. Pode ser usado para uma variedade de materiais, incluindo cerâmicas, metais, compósitos, plásticos e carbono. O processo envolve a colocação do pó num molde flexível, selando-o e sujeitando-o a pressão de todas as direcções. A prensagem isostática oferece vantagens únicas para aplicações cerâmicas e refractárias, uma vez que permite a formação de formas de produto com tolerâncias precisas, reduzindo a necessidade de maquinação dispendiosa.
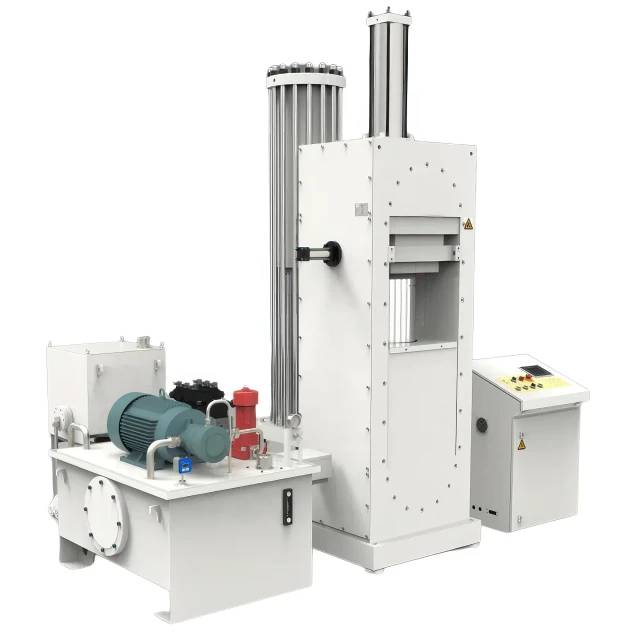
Processamento de metal em pó
O processamento de metal em pó é outra técnica de fabrico baseada em pó que permite a produção de produtos com propriedades que podem ultrapassar os materiais ligados. Neste processo, os pós metálicos ou cerâmicos, juntamente com um aglutinante, são misturados para formar uma mistura que pode ser prensada nas formas desejadas. Para peças maiores, a mistura é colocada em moldes. Este processo é habitualmente utilizado na produção de produtos como as brocas de diamante policristalino (PDC) para perfuração de poços profundos, em que a mistura é prensada e cozida para obter produtos com uma forma quase líquida.
Avanços na metalurgia do pó
Os processos à base de pó, como a compactação de pó, a prensagem isostática a quente de pó (P-HIP), a moldagem por injeção de metal (MIM) e a sinterização por plasma de faísca, são cada vez mais utilizados para fabricar componentes em forma de rede (NS) e quase em forma de rede (NNS) de ligas de alto desempenho. Estes processos têm como objetivo fabricar peças que se aproximam da geometria final exigida, reduzindo o custo, o tempo de execução e o desperdício de materiais através da minimização das etapas do processo, como a maquinagem e o acabamento. As tecnologias baseadas em pó têm a capacidade de produzir peças com propriedades de desempenho que podem igualar ou mesmo melhorar as dos processos de fabrico tradicionais, como a fundição. Isto deve-se a factores como a microestrutura uniforme associada aos materiais particulados e aos avanços na metalurgia do pó que permitem a produção de uma vasta gama de ligas de elevado desempenho em formato de pó.
Em conclusão, o objetivo dos processos de fabrico à base de pó é produzir peças densas com altas densidades de empacotamento e porosidade mínima. A prensagem isostática é uma técnica valiosa utilizada para ultrapassar as limitações da prensagem uniaxial, proporcionando uma distribuição mais uniforme da densidade em peças espessas. Além disso, processos alternativos como o processamento de metal em pó e os avanços na metalurgia do pó expandiram as capacidades do fabrico à base de pó, permitindo a produção de formas complexas e ligas de elevado desempenho.
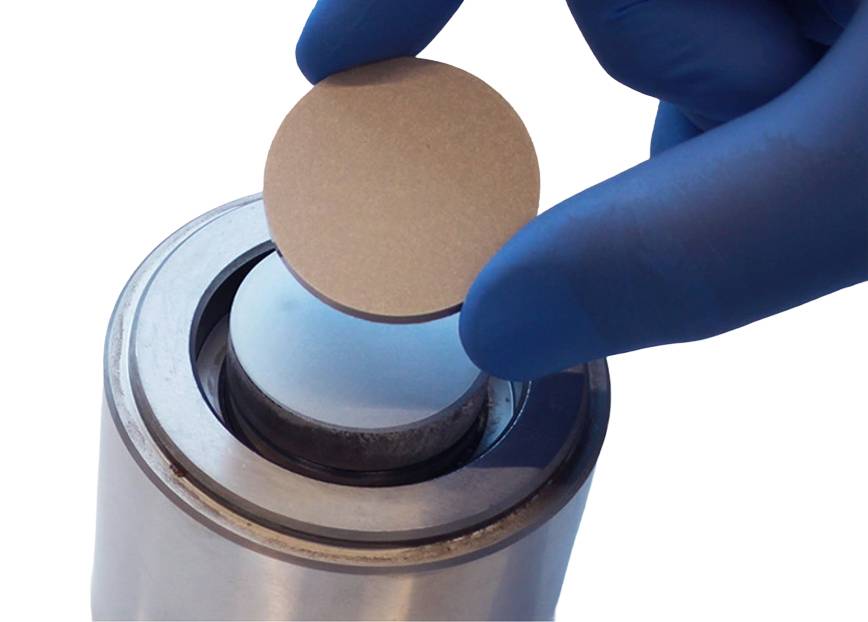
O processo de prensagem isostática a frio (CIP)
O processo de CIP
A Prensagem Isostática a Frio (CIP) é um método de processamento de materiais utilizado para moldar e compactar pós em componentes de diferentes tamanhos e formas. Envolve a colocação do pó ou de uma peça verde de baixa densidade num recipiente flexível selado e a sua imersão em líquido dentro de um recipiente sob pressão. É aplicada uma pressão de vários milhares de bar, comprimindo o compacto verde o mais próximo possível da sua densidade máxima de empacotamento. Esta densidade inicial mais elevada acelera a consolidação até à densidade final no ciclo térmico.
O CIP utiliza o princípio proposto pelo cientista francês Blaise Pascal, que afirma que uma mudança de pressão num fluido incompressível fechado é transmitida sem diminuição a todas as partes do fluido e à superfície do seu recipiente. Os materiais em pó são selados num molde com baixa resistência à deformação, como um saco de borracha, e é aplicada pressão líquida para comprimir uniformemente o corpo moldado em toda a sua superfície.
A prensagem em molde metálico é um método de prensagem semelhante ao CIP. Neste método, os materiais em pó são colocados num espaço delimitado por um molde metálico e um punção inferior. Em seguida, são comprimidos através da redução da distância entre os punções superior e inferior.
As vantagens de uma densidade inicial elevada na aceleração da consolidação até à densidade final no ciclo térmico
A alta densidade inicial obtida através do processo CIP oferece vários benefícios na consolidação de pós. Estes benefícios incluem:
-
Compressão previsível durante o processo de sinterização subsequente: A elevada compactação e a densidade uniforme proporcionam uma compressão previsível durante o processo de sinterização, resultando numa densidade final consistente e fiável.
-
Capacidade de processar formas grandes, complicadas e perfeitas: A CIP permite o processamento de formas grandes e complexas com elevada precisão. Isto poupa tempo e custos durante os processos de pós-tratamento.
-
Geração de peças de grande proporção com densidades uniformes: A CIP pode produzir peças com rácios de aspeto superiores a 2:1, mantendo densidades uniformes em todo o componente.
-
Resistência verde para manuseamento e tratamento durante o processo: O compacto verde formado através da CIP tem resistência suficiente para ser submetido a manuseamento e tratamento durante o processo, reduzindo os custos de produção.
Em geral, o processo CIP oferece uma moldagem e compactação eficientes e eficazes dos pós, resultando em componentes de alta qualidade com as densidades desejadas. A sua versatilidade e capacidade de processar vários materiais tornam-no um método valioso em indústrias como o fabrico de precisão, aeroespacial, defesa e automóvel.
De acordo com um relatório da DataIntelo, o mercado global de equipamentos de prensagem isostática a frio (CIP) deve crescer a um CAGR substancial durante o período de previsão, 2020-2026. A crescente demanda por produtos processados por CIP em setores como manufatura de precisão, aeroespacial, defesa e automotivo está impulsionando esse crescimento.
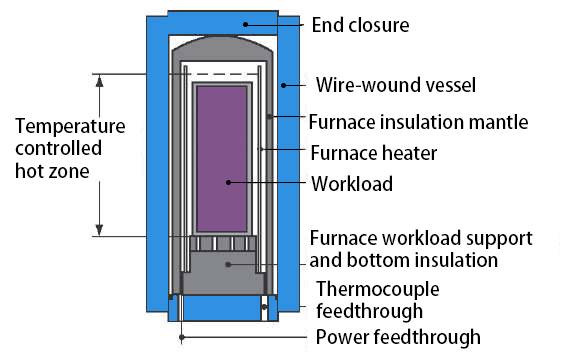
O processo de prensagem isostática a quente (HIP)
O efeito de alavanca da sinterização assistida por pressão uniaxial em HIP
A pressão também pode ser aplicada durante o ciclo térmico. Na sinterização assistida por pressão uniaxial, normalmente só podem ser produzidos produtos tipo placa. Para peças mais complexas, é utilizada a prensagem isostática a quente (HIP). A HIP é efectuada numa atmosfera gasosa, pelo que o principal requisito é que a superfície exterior das peças tratadas seja estanque ao gás. Como tal, este processo pode ser utilizado para produzir componentes através da selagem a vácuo de pó de peças num invólucro de aço macio. A aplicação uniforme de pressão assegura a manutenção da forma à medida que a peça e o invólucro encolhem. Os pós processados utilizando uma estratégia HIP não são normalmente compatíveis com os processos de fusão, exigindo temperaturas excessivas ou produzindo microestruturas desfavoráveis. No entanto, o esforço extra que é feito para processar estes materiais indica a sua utilização em aplicações exigentes em que mesmo um baixo nível de porosidade não é aceitável.
Os requisitos e resultados do processo HIP
A prensagem isostática a quente (HIP) consiste na aplicação simultânea de alta temperatura e pressão a metais e outros materiais durante um determinado período de tempo, com o objetivo de melhorar as suas propriedades mecânicas. Na unidade HIP, um forno de alta temperatura é encerrado num recipiente sob pressão. A temperatura, a pressão e o tempo de processo são controlados com precisão para obter as propriedades ideais do material. As peças são aquecidas num gás inerte, geralmente árgon, que aplica uma pressão "isostática" uniforme em todas as direcções. Isto faz com que o material se torne "plástico", permitindo que os vazios colapsem sob a pressão diferencial. As superfícies dos vazios unem-se por difusão para eliminar eficazmente os defeitos, atingindo uma densidade próxima da teórica e melhorando simultaneamente as propriedades mecânicas das peças, como as peças fundidas por cera perdida.
A incompatibilidade dos pós processados utilizando uma estratégia HIP com processos de fusão
A prensagem isostática a quente (HIP) é um processo de tratamento de materiais que envolve a utilização de calor e pressão para melhorar as propriedades físicas de um material. É normalmente efectuado em metais e cerâmicas. Quando qualquer um destes tipos de materiais é exposto ao calor e à pressão, as suas propriedades físicas alteram-se. A HIP é um processo eficaz para eliminar defeitos em peças fabricadas aditivamente à base de pó, gerando material 100% denso com propriedades de fadiga e ductilidade melhoradas.
Os sectores em que a HIP se desenvolveu são os seguintes: atingiu uma escala comparável à das peças fundidas e forjadas e tornou-se reconhecida como concorrente económica da forja e da fundição em aplicações com custos de matéria-prima mais elevados. Existem atualmente três sectores principais de HIP: Petróleo e gás, produção de eletricidade e indústria aeroespacial. A produção de um componente PM HIP é mais simples e mais curta do que os processos metalúrgicos convencionais habituais. O custo da HIP em relação aos custos de energia e materiais diminuiu 65% nas últimas duas décadas.
Introdução A prensagem isostática a quente (HIP) é um processo de densificação de pós ou peças fundidas e sinterizadas num forno a alta pressão (100-200 MPa) e a temperaturas de 900 a 1250°C, por exemplo, para aços e superligas. A pressão do gás actua uniformemente em todas as direcções para proporcionar propriedades isotrópicas e 100% de densificação. Proporciona muitas vantagens e tornou-se uma alternativa viável e de elevado desempenho aos processos convencionais, como o forjamento, a fundição e a maquinagem, em muitas aplicações.
Sinterização/Metalurgia do pó: Tecnologia de prensagem isostática a quente (HIP)
Nos últimos 50 anos, a prensagem isostática a quente passou do laboratório de investigação para a produção regular em grande escala. O futuro desta tecnologia parece promissor, à medida que se acelera a procura de melhores propriedades dos materiais, a utilização de materiais em pó e o desejo de produzir peças de forma líquida ou quase líquida.
Fonte de temperatura do forno aquecido por resistência no interior do recipiente
O processo HIP, originalmente conhecido como ligação gás-pressão, foi desenvolvido no laboratório do Battelle Memorial Institute em Columbus, Ohio, em 1955. A aplicação original era o revestimento por difusão de zircónio em ligas de zircónio-urânio para elementos de combustível nuclear. Mais ou menos na mesma altura, a ASEA-Suécia estava a utilizar a aplicação isostática de pressão para compactar os primeiros diamantes sintéticos. A prensagem isostática a quente (HIP) é um processo de fabrico utilizado para reduzir a porosidade dos metais e aumentar a densidade de muitos materiais cerâmicos. Isto melhora as propriedades mecânicas e a capacidade de trabalho do material.
O que é a prensagem isostática a quente (HIP)?
A prensagem isostática a quente (HIP), ou "Hipp'ing", é a aplicação simultânea de calor e alta pressão aos materiais. Este processo é ideal para melhorar as características do seu produto fabricado com aditivos, removendo a porosidade até 100%.
Atualmente, este processo já é utilizado na melhoria de produtos fabricados por aditivos. Após o Hipp'ing, o resultado é a eliminação dos vazios internos (ou seja, a porosidade) e a melhoria da microestrutura, o que conduz a propriedades mecânicas extremamente melhoradas. A HIP pode ser aplicada a uma grande variedade de ligas, incluindo titânio, aços, alumínio, cobre e magnésio.
A oportunidade de pré-processamento de construções num único passo através do fabrico aditivo multimaterial
As potenciais vantagens do fabrico aditivo multimaterial nos processos CIP e HIP
O fabrico aditivo multimaterial oferece uma gama de potenciais benefícios nos processos de Consolidação por Prensagem Isostática (CIP) e Prensagem Isostática a Quente (HIP). Ao utilizar a deposição selectiva de pó, esta abordagem pode colmatar a lacuna entre a nova tecnologia de fabrico de aditivos e os métodos tradicionais de fabrico de componentes topo de gama. Ao consolidar peças utilizando tecnologia estabelecida, pode ajudar a aliviar as preocupações sobre a qualidade e fiabilidade dos artigos produzidos por AM.
Uma das principais vantagens do fabrico aditivo multimaterial é a diminuição dos custos de fabrico. Com o aumento da complexidade das peças, menos etapas de processamento e tempo reduzido, os fabricantes podem conseguir poupanças de custos. Isto é particularmente benéfico para a produção de pequenas séries ou protótipos, onde a eficiência e a relação custo-eficácia são cruciais.
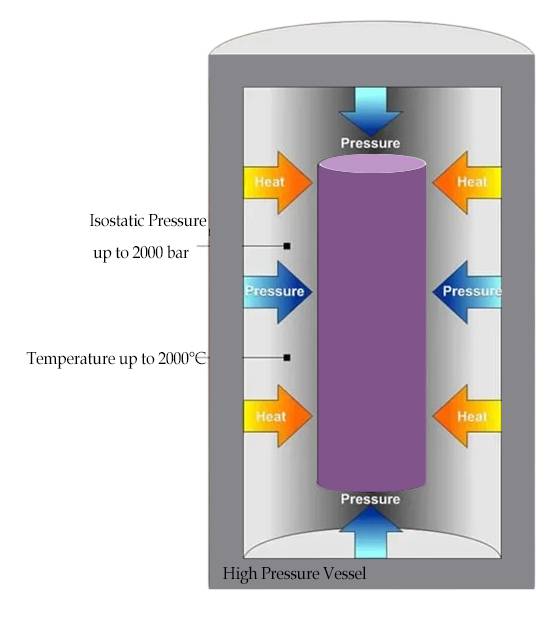
A potencial redução dos custos de fabrico com o aumento da complexidade das peças, menos etapas de processamento e tempo
A utilização do fabrico aditivo multimaterial pode levar a uma diminuição dos custos de fabrico. Os métodos tradicionais de fabrico subtrativo têm limites geométricos que já não se aplicam ao fabrico aditivo. Isto significa que podem ser criadas formas e desenhos complexos sem aumentar significativamente os custos de produção. Além disso, a capacidade de criar várias versões do mesmo produto sem variar o custo de produção pode reduzir ainda mais os custos.
Outra vantagem significativa da manufatura aditiva multimaterial é a drástica redução dos custos de produção.
é a redução drástica dos resíduos de processamento. Ao adicionar material passo a passo até obter o objeto desejado, o desperdício é mínimo em comparação com os métodos tradicionais de fabrico subtrativo. Isto não só reduz os custos, como também contribui para um processo de fabrico mais sustentável.
O mundo do fabrico aditivo de metal está a registar um aumento notável na utilização de métodos como a moldagem por injeção de metal (MIM), o jato de aglutinante (BJ) e a modelação por deposição fundida (FDM). Estes métodos oferecem vantagens únicas em termos de custos, flexibilidade de design e propriedades dos materiais.

No fabrico de aditivos metálicos, a remoção térmica de ligantes é um processo crucial após a impressão. Envolve a remoção de aglutinantes e outros aditivos para obter uma peça metálica totalmente densa. O desbobinamento correto das peças produzidas por fabrico aditivo de metal é essencial para obter as propriedades mecânicas e a precisão dimensional desejadas.
Tanto os processos CIP como HIP utilizam construções multimateriais. O CIP envolve a utilização de invólucros de polímero com pós cerâmicos, enquanto o HIP utiliza um invólucro de chapa de aço macio soldado com ligas de metalurgia do pó de alta qualidade. Estes métodos apresentam uma oportunidade para o pré-processamento de construções numa única etapa através do fabrico aditivo multimaterial.
Esta abordagem é particularmente vantajosa para a produção de pequenas séries ou protótipos, uma vez que permite aumentar a complexidade das peças com menos passos de processamento e menos tempo. Ao tirar partido das vantagens do fabrico aditivo multimaterial, os fabricantes podem alcançar uma maior eficiência e rentabilidade nos seus processos de produção.
A base industrial para o processo HIP está a expandir-se rapidamente devido à crescente procura de melhores propriedades dos materiais e à utilização de materiais em pó. Além disso, os avanços no equipamento HIP, os tempos de processamento mais curtos e a melhoria da economia tornam o processo HIP uma escolha viável para uma vasta gama de materiais. Isto reforça ainda mais o potencial para o pré-processamento de construções num único passo através do fabrico aditivo multimaterial.
Em conclusão, o fabrico de aditivos multimateriais oferece oportunidades significativas para melhorar a eficiência, reduzir os custos e obter designs complexos nos processos CIP e HIP. Ao tirar partido das vantagens desta tecnologia, os fabricantes podem manter-se na vanguarda da inovação e satisfazer as exigências do mercado competitivo atual.
A utilização da tecnologia de deposição selectiva da kintek na prensagem isostática
A deposição simultânea de diferentes materiais
A prensagem isostática é um método de compactação de pó num recipiente elastomérico submerso num fluido a alta pressão. Tradicionalmente, este processo tem sido utilizado principalmente para cerâmicas e metais. No entanto, os recentes avanços na tecnologia de deposição selectiva, como a abordagem inovadora da Kintek, abriram novas possibilidades para a prensagem isostática.
A tecnologia de deposição selectiva da KinTek permite a deposição simultânea de diferentes materiais. Isto significa que, em vez de utilizar um único material em pó, podem ser depositados vários materiais camada a camada. Isto abre uma gama de possibilidades para a criação de peças complexas, multi-materiais com propriedades únicas.
Criação de um invólucro de polímero moldado e estanque ao líquido que envolve o pó cerâmico não compactado
Uma das principais vantagens da tecnologia de deposição selectiva da KinTek na prensagem isostática é a capacidade de criar um invólucro de polímero moldado e estanque ao líquido que envolve o pó cerâmico não compactado. Esse invólucro atua como uma barreira, impedindo que o pó cerâmico se disperse durante o processo de prensagem isostática.
Ao utilizar a deposição selectiva para criar este invólucro, é possível obter uma densidade verde uniforme, mesmo para peças com uma grande relação altura/diâmetro. Isto é particularmente importante para aplicações em que o controlo dimensional é crucial, como nas indústrias aeroespacial ou automóvel.
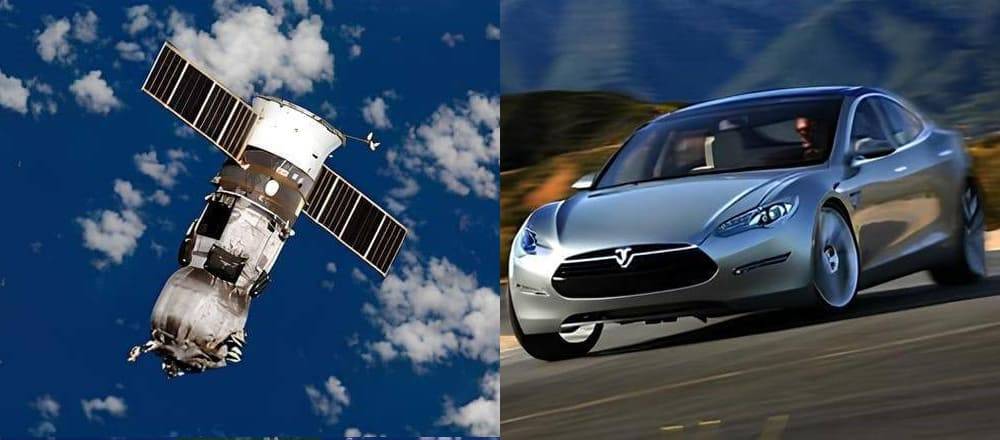
O fácil transporte e colocação da construção dentro de uma máquina CIP
Outra vantagem da tecnologia de deposição selectiva da 's é a facilidade de transporte e colocação da construção dentro de uma máquina de prensagem isostática a frio (CIP). A construção, que consiste no invólucro de polímero moldado preenchido com pó cerâmico não compactado, pode ser facilmente manuseada e posicionada dentro da máquina CIP.
Esta facilidade de transporte e colocação não só aumenta a eficiência como também reduz o risco de danos na construção durante o processo de carregamento. Permite um processo de prensagem isostática mais simples e fiável, garantindo resultados consistentes e peças de alta qualidade.
Em conclusão, a tecnologia de deposição selectiva da 's oferece possibilidades interessantes para a prensagem isostática. A deposição simultânea de diferentes materiais, a criação de um invólucro de polímero moldado e estanque ao líquido e a facilidade de transporte e colocação da construção dentro de uma máquina CIP contribuem para o avanço deste processo de fabrico. Com mais desenvolvimento e aperfeiçoamento, a tecnologia da 's tem o potencial de revolucionar a forma como produzimos peças complexas e multimateriais com melhor controlo dimensional e desempenho.
O potencial de uma abordagem semelhante para peças processadas com HIP
Co-deposição de um aço macio para ferramentas e de uma liga específica PM utilizando um sistema de deposição selectiva de pó
Para peças que têm de ser processadas com HIP, pode ser utilizada uma abordagem semelhante. Um aço macio para ferramentas e uma liga específica PM poderiam ser co-depositados utilizando um sistema de deposição selectiva de pó, e apenas o exterior do aço para ferramentas necessitaria de ser consolidado. Uma vez que a liga PM não necessita de ser fundida, é fácil imaginar a produção de um invólucro pré-preenchido com tubagem que permitiria a soldadura deste invólucro sob vácuo, tal como nas peças produzidas por HIP a partir de chapa metálica soldada. O resto do processamento HIP pode então seguir a rota tradicional.
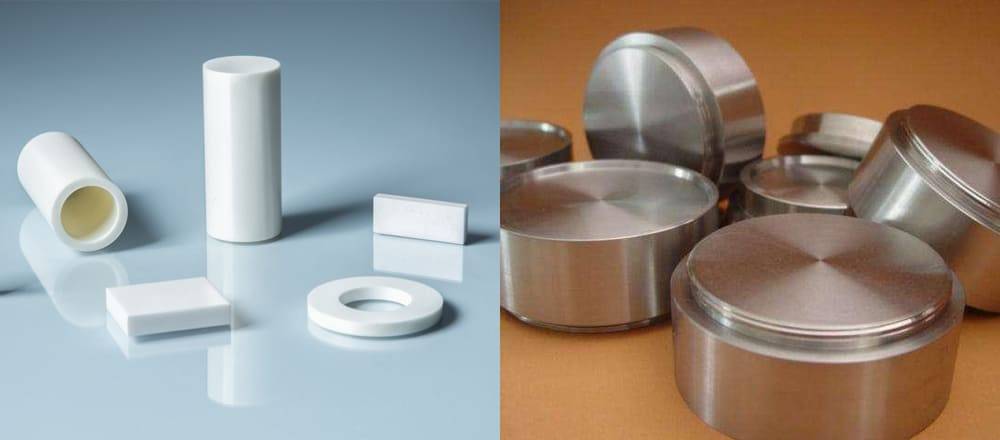
Produção de um invólucro pré-preenchido com tubagem para selagem por soldadura sob vácuo
Uma abordagem semelhante ao processamento HIP pode ser utilizada para peças que requerem tratamento HIP. Através da co-deposição de um aço macio para ferramentas e de uma liga específica PM utilizando um sistema de deposição selectiva de pó, é possível produzir um invólucro pré-preenchido com tubagem para selagem de soldaduras sob vácuo. Isto permite a consolidação do exterior do aço para ferramentas, preservando a integridade da liga PM. O restante processamento HIP pode então prosseguir como habitualmente.
O percurso tradicional do resto do processamento HIP
Após a co-deposição de um aço macio para ferramentas e de uma liga específica PM utilizando um sistema de deposição selectiva de pó e a consolidação do exterior do aço para ferramentas, o resto do processamento HIP pode seguir a rota tradicional. Isto inclui a utilização de tecnologia de arrefecimento avançada para aumentar a economia do processamento e melhorar as propriedades do material final. Com a capacidade de arrefecer mais rapidamente utilizando gás árgon e sistemas de arrefecimento interno, os ciclos de HIP podem ser significativamente reduzidos, conduzindo a poupanças de custos e a uma melhor qualidade das peças.
A utilização da HIP em várias indústrias provou ser altamente benéfica. A HIP pode ser utilizada para fabricar uma vasta gama de componentes, incluindo componentes metálicos grandes e maciços de forma quase líquida, tais como peças para petróleo e gás e impulsores de forma líquida. Também é adequado para a produção de pequenas ferramentas de corte PM HSS e peças minúsculas, como suportes dentários. O processo evoluiu ao longo dos anos para se tornar um método de alto desempenho, alta qualidade e económico para a produção de componentes metálicos e cerâmicos.
A HIPing oferece inúmeras vantagens, incluindo propriedades mecânicas melhoradas, redução de resíduos, minimização da maquinação e a capacidade de rejuvenescer peças antigas. Pode ser aplicado a uma variedade de materiais, incluindo alumínio, aço, aço inoxidável, superliga, titânio e cerâmica. Com os avanços no equipamento HIP e nos tempos de processamento, o processo HIP está a tornar-se cada vez mais popular para uma vasta gama de materiais e aplicações.
Em conclusão, uma abordagem semelhante ao processamento HIP pode ser aplicada a peças que requerem tratamento HIP. Ao co-depositar um aço macio para ferramentas e uma liga específica PM utilizando um sistema de deposição selectiva de pó, é possível produzir invólucros pré-preenchidos com tubagem para selagem de soldaduras sob vácuo. Esta abordagem oferece inúmeras vantagens, incluindo a melhoria da qualidade das peças, a redução do tempo de processamento e a poupança de custos. Com os avanços contínuos na tecnologia HIP, o potencial de utilização desta abordagem em várias indústrias continua a expandir-se.
Conclusão: A ponte da deposição selectiva de pó entre o novo fabrico aditivo e o fabrico tradicional
O potencial da deposição selectiva de pó na criação de uma ponte entre a nova tecnologia de fabrico aditivo e o fabrico tradicional de componentes topo de gama
A deposição selectiva de pó tem o potencial de fazer a ponte entre a nova tecnologia de fabrico aditivo (AM) e o fabrico tradicional de componentes topo de gama. Esta abordagem tira partido dos processos bem conhecidos de tratamento por pressão e de ciclos térmicos que já estão disponíveis na indústria. Ao utilizar estes métodos estabelecidos para consolidar as peças criadas através da AM, pode ajudar a aliviar a ansiedade da indústria relativamente aos artigos produzidos através desta nova tecnologia.
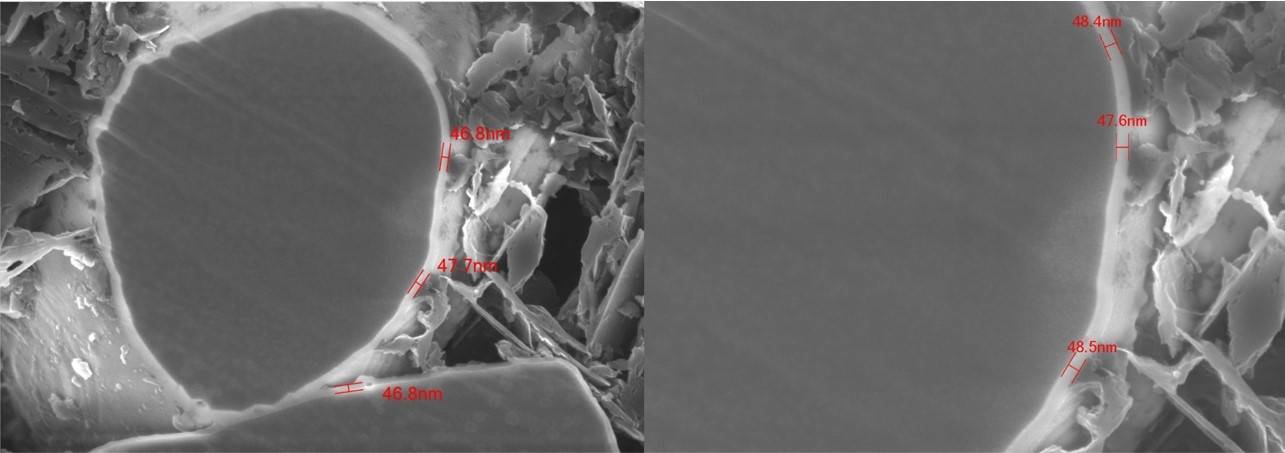
A possibilidade de aliviar a ansiedade da indústria relativamente aos artigos produzidos através da AM através desta abordagem
Uma das principais preocupações da indústria no que diz respeito ao fabrico aditivo é a qualidade e a fiabilidade dos produtos finais. Os métodos de fabrico tradicionais foram aperfeiçoados ao longo de décadas e existe um nível de confiança nos componentes produzidos através destes processos.
Ao utilizar a deposição selectiva de pó, as peças criadas através da AM podem ser moldadas utilizando a nova tecnologia, mas consolidadas utilizando os métodos há muito estabelecidos. Isto pode ajudar a aliviar alguma da ansiedade que rodeia a utilização da AM para componentes topo de gama.
Em conclusão, a deposição selectiva deposição selectiva de pós oferece uma solução promissora para colmatar o fosso entre a nova tecnologia de fabrico de aditivos e o fabrico tradicional. Ao aproveitar os processos e técnicas estabelecidos no fabrico tradicional, pode ajudar a criar confiança nos componentes produzidos através da AM.
CONTACTE-NOS PARA UMA CONSULTA GRATUITA
Os produtos e serviços da KINTEK LAB SOLUTION foram reconhecidos por clientes de todo o mundo. A nossa equipa terá todo o prazer em ajudar com qualquer questão que possa ter. Contacte-nos para uma consulta gratuita e fale com um especialista de produto para encontrar a solução mais adequada para as suas necessidades de aplicação!