A sinterização de cerâmica é um processo crítico no fabrico de objectos cerâmicos, envolvendo a transformação de materiais em pó numa estrutura densa e coesa através da aplicação de calor e, por vezes, de forças adicionais como pressão ou correntes eléctricas. O processo inclui normalmente várias fases: preparação do pó compacto, aquecimento a altas temperaturas para induzir a ligação e a densificação das partículas e arrefecimento para solidificar o material. Este método reduz a porosidade, provoca a contração e melhora as propriedades mecânicas da cerâmica. O processo de sinterização pode variar consoante os materiais específicos e os resultados pretendidos, mas geralmente envolve passos como a prensagem, o aquecimento e, por vezes, a maquinagem ou montagem pós-sinterização.
Pontos-chave explicados:
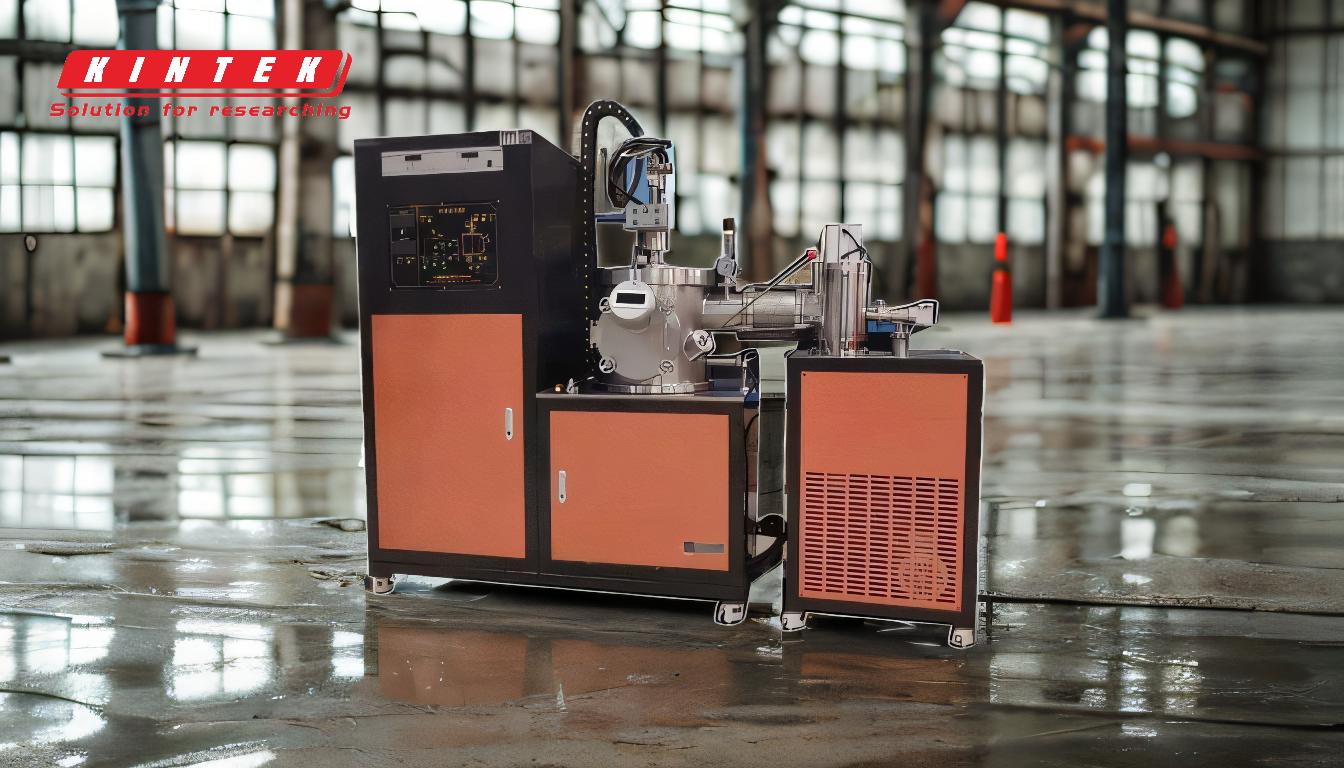
-
Preparação do pó compacto:
- Mistura e composição: O processo começa com a preparação de uma mistura em pó, que inclui materiais cerâmicos primários, agentes de acoplamento, aglutinantes e defloculantes. Esta mistura é frequentemente combinada com água para formar uma pasta.
- Secagem por pulverização: A lama é então seca por pulverização para produzir um pó fino e fluido que é mais fácil de manusear e prensar.
- Pressionar: O pó é compactado numa forma desejada utilizando ferramentas de prensagem ou moldes. Esta etapa forma um "corpo verde", que é uma estrutura coerente mas frágil que mantém a forma do produto final.
-
Aquecimento e sinterização:
- Remoção de aglutinantes (desbobinagem): O corpo verde é aquecido a uma temperatura baixa para queimar quaisquer ligantes orgânicos ou agentes de acoplamento. Esta etapa é crucial para evitar defeitos durante o processo de sinterização a alta temperatura.
-
Sinterização a alta temperatura: O corpo verde é então aquecido a uma temperatura ligeiramente inferior ao ponto de fusão do material cerâmico. Durante esta fase, ocorrem vários processos-chave:
- Ligação de partículas: As partículas de pó começam a unir-se nos seus pontos de contacto, levando à formação de limites de grão.
- Migração de materiais: Os átomos migram através dos limites dos grãos, levando à densificação e à redução da porosidade.
- Retração: À medida que as partículas se unem e o material se densifica, a cerâmica sofre uma contração significativa, que deve ser cuidadosamente controlada para atingir as dimensões finais desejadas.
- Sinterização em fase líquida (opcional): Nalguns casos, é introduzida uma fase líquida para acelerar o processo de densificação. Isto envolve a adição de elementos como pó de cobre ou carbonetos cimentados, que derretem à temperatura de sinterização e fluem para os poros restantes, aumentando ainda mais a densidade do material.
-
Arrefecimento e solidificação:
- Após o processo de sinterização, a cerâmica é deixada arrefecer gradualmente. Esta fase de arrefecimento é fundamental para garantir que o material se solidifica numa massa unificada com as propriedades mecânicas desejadas, como a resistência e a dureza.
-
Processamento pós-sinterização:
- Maquinação: Dependendo da aplicação, a peça cerâmica sinterizada pode necessitar de maquinação adicional. Esta é frequentemente efectuada com ferramentas de diamante ou maquinagem ultra-sónica para obter dimensões e acabamentos de superfície precisos.
- Montagem: Em alguns casos, as peças cerâmicas são metalizadas e soldadas a outros componentes, especialmente em aplicações em que a cerâmica é utilizada em conjunto com metais.
-
Parâmetros de controlo:
- Temperatura e atmosfera: O processo de sinterização requer um controlo preciso da temperatura e da atmosfera. A temperatura deve ser suficientemente elevada para induzir a ligação das partículas, mas não tão elevada que provoque a fusão ou o crescimento excessivo dos grãos. A atmosfera (por exemplo, redutora, oxidante ou inerte) é também crucial para evitar reacções indesejadas ou oxidação.
- Espessura e velocidade da camada: Nos processos de sinterização contínua, parâmetros como a espessura da camada, a velocidade e o ponto final da sinterização devem ser cuidadosamente controlados para garantir uma densificação uniforme e minimizar os defeitos.
-
Aplicações e resultados:
- Redução da porosidade: Um dos principais resultados da sinterização é a redução da porosidade do material, o que aumenta a resistência mecânica e a durabilidade da cerâmica.
- Formação de um corpo de porcelana: Com o tempo, os materiais cerâmicos densificam-se gradualmente e formam um corpo de porcelana com uma certa resistência, adequado para várias aplicações, tais como cerâmica, componentes industriais e cerâmica avançada.
Em resumo, a sinterização de cerâmica é um processo de várias etapas que envolve uma preparação cuidadosa, aquecimento controlado e processamento preciso pós-sinterização para obter um produto cerâmico denso, forte e durável. O processo pode ser adaptado para satisfazer requisitos específicos, ajustando parâmetros como a temperatura, a atmosfera e a utilização de aditivos como aglutinantes ou fases líquidas.
Quadro de resumo:
Estágio | Principais etapas | Resultado |
---|---|---|
Preparação | Mistura, secagem por pulverização, prensagem | Formação de um corpo verde com a forma desejada |
Aquecimento e sinterização | Remoção de ligantes, sinterização a alta temperatura, sinterização em fase líquida opcional | Colagem, densificação e retração de partículas |
Arrefecimento | Arrefecimento gradual | Solidificação numa massa unificada com propriedades mecânicas melhoradas |
Pós-sinterização | Maquinação, montagem | Dimensões exactas, acabamentos de superfície e integração com outros componentes |
Parâmetros de controlo | Temperatura, atmosfera, espessura da camada, velocidade | Densificação uniforme e minimização de defeitos |
Aplicações | Cerâmica, componentes industriais, cerâmica avançada | Produtos cerâmicos fortes, duráveis e de baixa porosidade |
Pronto para otimizar o seu processo de fabrico de cerâmica? Contacte os nossos especialistas hoje mesmo para soluções à medida!