A galvanoplastia e a deposição física em fase vapor (PVD) são duas técnicas distintas de revestimento de superfícies utilizadas para melhorar as propriedades dos materiais, como a resistência à corrosão, a dureza e o aspeto estético. A galvanoplastia envolve a deposição eletroquímica de uma camada metálica sobre um substrato utilizando uma solução electrolítica, enquanto a PVD utiliza processos físicos como a evaporação ou a pulverização catódica para depositar películas finas num ambiente de vácuo. A PVD oferece vantagens como maior resistência à corrosão, melhor aderência e segurança ambiental, uma vez que não depende de produtos químicos tóxicos. A galvanoplastia, por outro lado, é frequentemente mais económica e adequada para revestimentos mais espessos, mas pode envolver produtos químicos perigosos e produzir acabamentos menos duradouros.
Pontos-chave explicados:
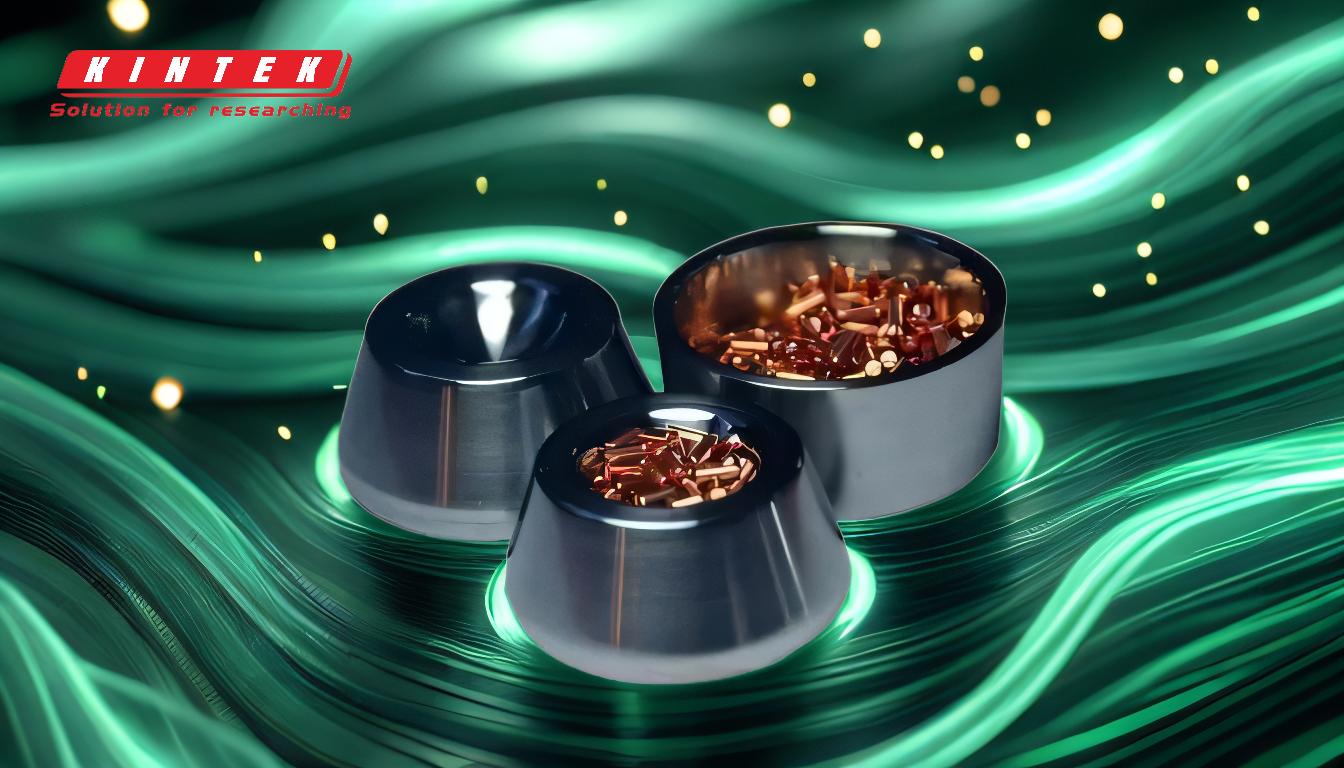
-
Mecanismo do processo:
- Eletrodeposição: Este é um processo eletroquímico em que uma solução de iões metálicos (eletrólito) é utilizada para depositar uma camada de metal num substrato. Uma corrente eléctrica reduz os iões metálicos no eletrólito, fazendo com que estes se liguem ao substrato.
- PVD: O PVD é um processo físico que envolve a vaporização de um material sólido (alvo) numa câmara de vácuo. Os átomos ou moléculas vaporizados condensam-se então no substrato para formar um revestimento fino e uniforme. Técnicas como a pulverização catódica e a evaporação são normalmente utilizadas.
-
Espessura e uniformidade do revestimento:
- Eletrodeposição: Produz normalmente revestimentos mais espessos, que podem variar entre alguns micrómetros e vários milímetros. No entanto, conseguir uma espessura uniforme, especialmente em geometrias complexas, pode ser um desafio.
- PVD: Cria revestimentos muito mais finos, frequentemente na gama dos nanómetros a micrómetros. Os revestimentos PVD são altamente uniformes e podem adaptar-se a formas complexas devido ao processo de deposição em linha de visão.
-
Adesão e durabilidade:
- Eletrodeposição: A aderência dos revestimentos galvânicos depende da preparação da superfície e das condições electroquímicas. Embora duráveis, estes revestimentos podem ser susceptíveis de descascar ou descamar sob tensão.
- PVD: Oferece uma aderência superior devido à ligação a nível atómico entre o revestimento e o substrato. Os revestimentos PVD são altamente duráveis e resistentes ao desgaste, à corrosão e à oxidação.
-
Considerações ambientais e de segurança:
- Eletrodeposição: Envolve frequentemente a utilização de produtos químicos perigosos, tais como cianetos e ácidos, que requerem um manuseamento e eliminação cuidadosos. O processo pode gerar resíduos tóxicos e apresentar riscos ambientais.
- PVD: Geralmente considerado mais seguro e mais amigo do ambiente, uma vez que não envolve produtos químicos tóxicos. O processo é conduzido em vácuo, minimizando a exposição a substâncias perigosas.
-
Aplicações:
- Eletrodeposição: Normalmente utilizada em indústrias que requerem revestimentos espessos, decorativos ou funcionais, como a indústria automóvel (cromagem), a eletrónica (douramento) e a joalharia.
- PVD: Preferido para aplicações que requerem revestimentos de alto desempenho, tais como ferramentas de corte, dispositivos médicos e componentes aeroespaciais, onde a durabilidade, a resistência à corrosão e a precisão são fundamentais.
-
Custo e escalabilidade:
- Eletrodeposição: Geralmente mais rentável para a produção em grande escala e para revestimentos mais espessos. É amplamente utilizada na produção em massa devido ao seu custo relativamente baixo e ao seu elevado rendimento.
- PVD: Mais dispendioso devido à necessidade de equipamento de vácuo e de processos especializados. No entanto, é altamente escalável para aplicações de precisão e oferece benefícios de custo a longo prazo devido à durabilidade dos revestimentos.
-
Compatibilidade de materiais:
- Eletrodeposição: Limitada a metais que podem ser depositados electroquimicamente. Os substratos não condutores requerem um pré-tratamento condutor.
- PVD: Pode depositar uma vasta gama de materiais, incluindo metais, cerâmicas e compósitos, em substratos condutores e não condutores.
-
Acabamento e estética da superfície:
- Eletrodeposição: Proporciona um acabamento brilhante e refletor, tornando-a ideal para aplicações decorativas. No entanto, o acabamento pode degradar-se com o tempo devido à exposição ambiental.
- PVD: Oferece um acabamento mate ou acetinado, que pode ser adaptado a requisitos estéticos específicos. Os revestimentos PVD são mais resistentes ao desvanecimento e ao embaciamento.
Ao compreender estas diferenças fundamentais, os compradores podem tomar decisões informadas com base nos requisitos específicos da sua aplicação, tais como durabilidade, impacto ambiental e considerações de custo.
Tabela de resumo:
Aspeto | Eletrodeposição | PVD |
---|---|---|
Mecanismo do processo | Deposição eletroquímica utilizando uma solução de eletrólito. | Vaporização física num ambiente de vácuo. |
Espessura do revestimento | Revestimentos mais espessos (micrómetros a milímetros). | Revestimentos mais finos (nanómetros a micrómetros). |
Adesão e durabilidade | Durável, mas pode descascar ou descamar sob tensão. | Adesão superior, altamente durável e resistente ao desgaste e à corrosão. |
Impacto ambiental | Utiliza produtos químicos perigosos; gera resíduos tóxicos. | Amigo do ambiente; não são utilizados produtos químicos tóxicos. |
Aplicações | Automóvel, eletrónica, joalharia (revestimentos espessos e decorativos). | Ferramentas de corte, dispositivos médicos, indústria aeroespacial (revestimentos de alto desempenho). |
Custo | Económica para produção em grande escala. | Custo inicial mais elevado, mas benefícios de durabilidade a longo prazo. |
Compatibilidade de materiais | Limitada a metais; os substratos não condutores requerem pré-tratamento. | Compatível com metais, cerâmicas e compósitos. |
Acabamento da superfície | Acabamento brilhante e refletor; pode degradar-se com o tempo. | Acabamento mate ou acetinado; resistente ao desbotamento e às manchas. |
Ainda não tem a certeza de qual a técnica de revestimento mais adequada para o seu projeto? Contacte os nossos especialistas hoje mesmo para obter aconselhamento personalizado!