A sinterização a laser, em particular a sinterização selectiva a laser (SLS), é uma técnica versátil de fabrico de aditivos que oferece vantagens e desvantagens únicas.É capaz de produzir formas altamente complexas e funcionais, que são difíceis de alcançar com os métodos de sinterização tradicionais.No entanto, tem custos significativos, tanto em termos de equipamento como de materiais, e requer operadores qualificados.Por outro lado, métodos alternativos como a metalurgia do pó são mais económicos para a produção em grande escala, mas podem resultar em componentes não uniformes.A sinterização a alta velocidade tem-se mostrado promissora na melhoria da densidade e da resistência, mas não é universalmente aceite, indicando potenciais limitações.
Pontos-chave explicados:
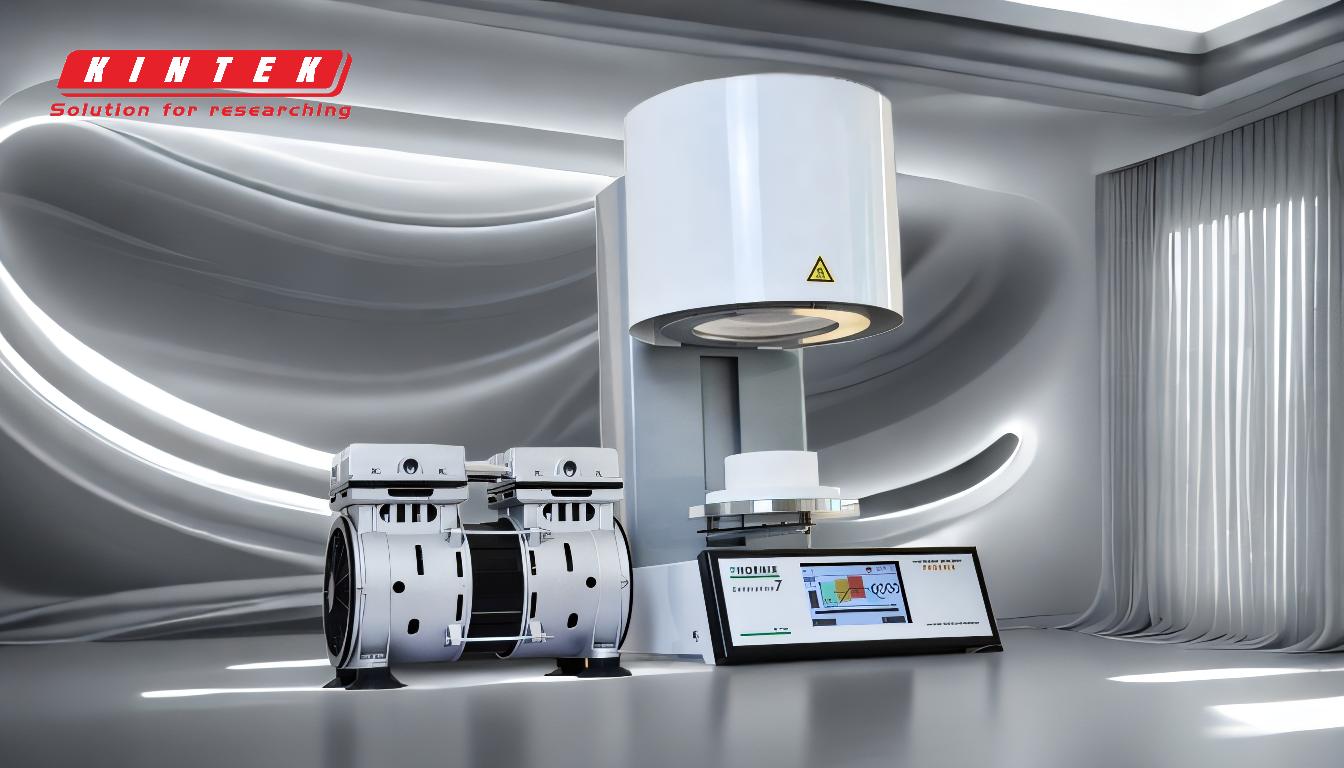
-
Vantagens da sinterização a laser:
- Formas complexas e funcionais: A sinterização a laser, especialmente a SLS, destaca-se na criação de geometrias complexas e funcionais que são difíceis ou impossíveis de alcançar com os métodos de sinterização tradicionais.Isto torna-a ideal para aplicações que requerem elevada precisão e complexidade, tais como dispositivos aeroespaciais ou médicos.
- Versatilidade de materiais: A SLS pode trabalhar com uma vasta gama de materiais, incluindo polímeros, metais e cerâmicas, permitindo diversas aplicações em todos os sectores.
- Pós-processamento mínimo: As peças produzidas através de SLS requerem frequentemente menos pós-processamento em comparação com outros métodos de fabrico de aditivos, uma vez que o processo produz inerentemente componentes de forma quase líquida.
-
Desvantagens da Sinterização a Laser:
- Custos elevados: O investimento inicial das máquinas SLS é substancial, excedendo frequentemente os $250.000.Além disso, os materiais utilizados na SLS são caros, aumentando ainda mais o custo total.
- Necessidade de um operador qualificado: O SLS requer operadores com competências e formação especializadas, aumentando os custos operacionais e a complexidade.
- Escalabilidade limitada: Embora a SLS seja excelente para a criação de protótipos e produção em pequena escala, é menos eficiente para o fabrico em grande escala em comparação com métodos como a metalurgia do pó.
-
Comparação com a metalurgia do pó:
- Custo-eficácia: A metalurgia do pó é geralmente mais económica, tanto em termos de equipamento como de materiais, o que a torna mais adequada para a produção em grande escala.
- Facilidade de operação: Ao contrário da SLS, a metalurgia do pó não requer operadores altamente qualificados, reduzindo os custos de mão de obra e os requisitos de formação.
- Problemas de uniformidade: Uma das desvantagens da metalurgia do pó é a possibilidade de os componentes não serem uniformes devido à fricção entre o pó e as ferramentas, o que pode afetar a qualidade e a consistência do produto final.
-
Sinterização a alta velocidade:
- Densidade e resistência melhoradas: Alguns estudos sugerem que a sinterização a alta velocidade pode produzir peças com densidade e resistência ligeiramente superiores em comparação com os métodos de sinterização tradicionais.
- Aprovação limitada: Apesar destes benefícios, nem todos os fornecedores de materiais, particularmente os que lidam com zircónia, apoiam a sinterização a alta velocidade.Isto pode dever-se a preocupações sobre a compatibilidade do material, estabilidade do processo ou outras limitações técnicas.
-
Considerações para os compradores de equipamentos e consumíveis:
- Requisitos da aplicação: Ao decidir entre SLS e outros métodos de sinterização, os compradores devem considerar os requisitos específicos da sua aplicação, tais como a necessidade de geometrias complexas, propriedades do material e volume de produção.
- Restrições orçamentais: Os elevados custos associados à SLS podem ser um fator limitativo para algumas organizações, especialmente as que têm orçamentos limitados ou que requerem uma produção em grande escala.
- Experiência do operador: A necessidade de operadores qualificados deve ser tida em conta no processo de tomada de decisão, uma vez que pode afetar tanto a configuração inicial como os custos operacionais contínuos.
- Compatibilidade de materiais: Para quem está a considerar a sinterização a alta velocidade, é essencial verificar a compatibilidade dos materiais e consultar os fornecedores para garantir que o método é adequado para a aplicação pretendida.
Em resumo, a sinterização a laser, em especial a SLS, oferece vantagens significativas em termos de flexibilidade de conceção e versatilidade de materiais, mas acarreta custos elevados e complexidades operacionais.Métodos alternativos, como a metalurgia do pó, são mais económicos para a produção em grande escala, mas podem comprometer a uniformidade dos componentes.A sinterização a alta velocidade mostra potencial para melhorar as propriedades dos materiais, mas não é universalmente aceite, o que indica a necessidade de uma análise cuidadosa das suas limitações.Os compradores devem ponderar estes factores em função das suas necessidades e restrições específicas para tomarem uma decisão informada.
Quadro de síntese:
Aspeto | Sinterização a laser (SLS) | Metalurgia do pó | Sinterização a alta velocidade |
---|---|---|---|
Formas complexas | Excelente na criação de geometrias complexas e funcionais | Capacidade limitada para produzir formas complexas | Dados limitados disponíveis |
Versatilidade de materiais | Funciona com polímeros, metais e cerâmica | Opções limitadas de materiais | Potenciais problemas de compatibilidade com materiais como a zircónia |
Custo | Investimento inicial elevado (>$250.000) e materiais caros | Mais económico para a produção em grande escala | Os custos variam; não são universalmente aceites |
Competência do operador | Requer operadores altamente qualificados | Mais fácil de operar; requer menos mão de obra especializada | Requer conhecimentos especializados |
Escalabilidade | Ideal para a criação de protótipos e produção em pequena escala | Adequado para produção em grande escala | Escalabilidade limitada devido a limitações técnicas |
Pós-processamento | Pós-processamento mínimo necessário | Pode exigir mais pós-processamento | Pós-processamento mínimo |
Uniformidade dos componentes | Elevada precisão e consistência | Potencial para componentes não uniformes | Densidade e resistência melhoradas, mas endosso limitado |
Precisa de ajuda para escolher o método de sinterização correto para a sua aplicação? Contacte os nossos especialistas hoje para um aconselhamento personalizado!