A sinterização em fase líquida (LPS) é um processo amplamente utilizado na metalurgia do pó e na cerâmica, em que uma fase líquida facilita a densificação e a ligação de partículas sólidas.Embora ofereça vantagens como a densificação melhorada e a capacidade de produzir formas complexas, também apresenta vários inconvenientes.Estas incluem custos elevados devido ao equipamento dispendioso e ao consumo de energia, desafios na obtenção de propriedades uniformes e potenciais defeitos, tais como deformações ou flacidez.Além disso, o processo pode exigir materiais especializados e um controlo preciso dos parâmetros, tornando-o complexo e menos adequado para a produção em grande escala ou para aplicações que exijam uma elevada resistência mecânica.
Pontos-chave explicados:
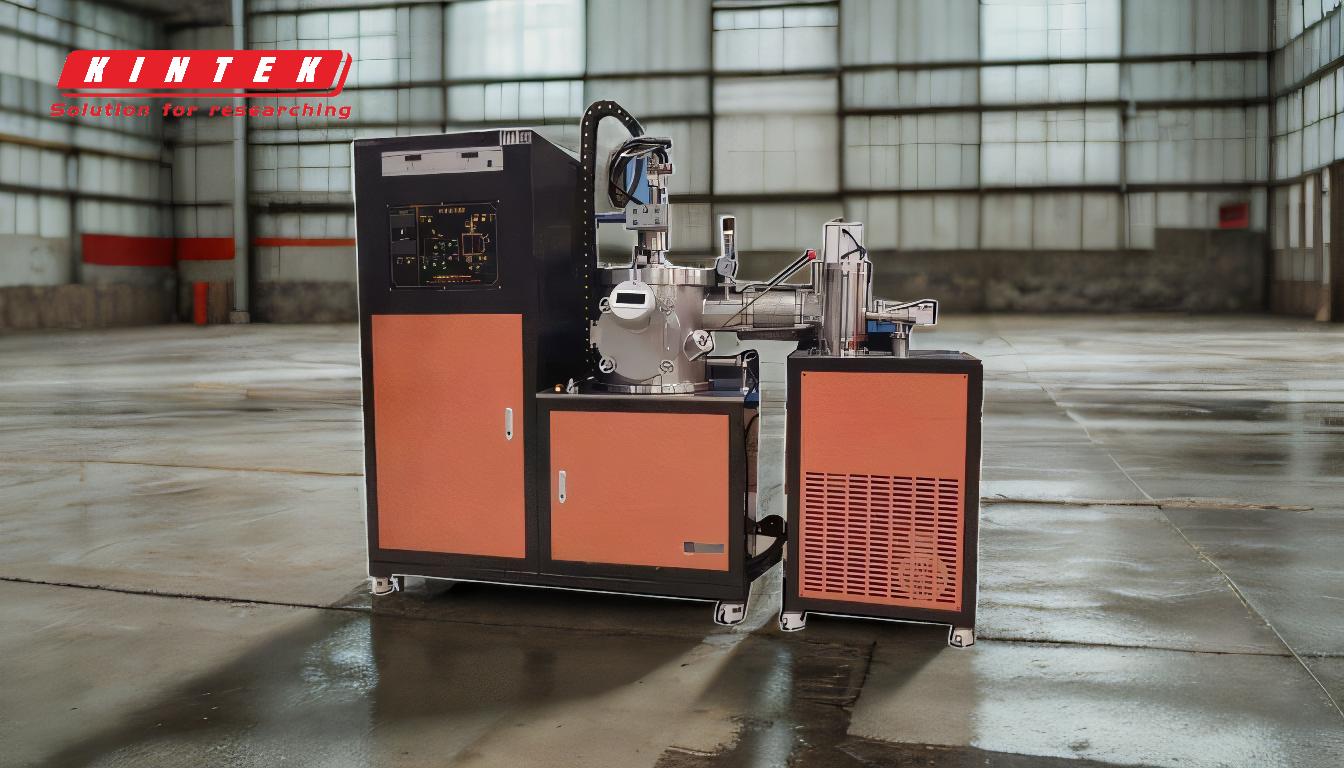
-
Elevados custos operacionais e de equipamento
- A sinterização em fase líquida requer frequentemente fornos especializados capazes de manter temperaturas e atmosferas exactas, cuja aquisição e manutenção são dispendiosas.
- O processo exige um consumo de energia significativo, particularmente para a sinterização a alta temperatura, levando a custos operacionais mais elevados.
- É necessária experiência profissional para operar e manter o equipamento, o que aumenta os custos de mão de obra.
-
Limitações do material e do processo
- O processo pode exigir materiais ou aditivos específicos para formar a fase líquida, o que pode aumentar os custos dos materiais.
- Conseguir uma distribuição uniforme da fase líquida é um desafio, podendo levar a propriedades inconsistentes no produto final.
- O processo pode não ser adequado para materiais sensíveis a temperaturas elevadas ou propensos a uma contração excessiva.
-
Potencial para defeitos
- O empeno e a flacidez são problemas comuns durante a sinterização em fase líquida devido à gravidade ou à fricção, o que pode levar a imprecisões dimensionais ou defeitos na peça final.
- A retração excessiva durante a sinterização pode complicar o processo de conceção e produção, exigindo uma compensação cuidadosa durante as fases iniciais.
-
Restrições de tamanho e complexidade
- A sinterização em fase líquida pode enfrentar limitações na produção de peças de grandes dimensões ou de formas complexas, à semelhança de outros processos de metalurgia do pó.
- O processo pode não atingir a mesma resistência mecânica ou ductilidade que os métodos tradicionais de fundição ou forjamento, limitando a sua utilização em aplicações de elevado desempenho.
-
Baixa produtividade e rendimento
- O processo de sinterização é muitas vezes moroso, com tempos de ciclo longos que reduzem a produtividade global.
- A produção por forno é tipicamente pequena, o que a torna menos eficiente para a produção em grande escala em comparação com outros métodos de fabrico.
-
Complexidade técnica
- O processo requer um controlo preciso de parâmetros como a temperatura, a pressão e a atmosfera, o que o torna tecnicamente exigente.
- Podem ser necessários ajustes para diferentes materiais, o que aumenta a complexidade da operação e o risco de erros.
Em resumo, embora a sinterização em fase líquida ofereça vantagens únicas, as suas desvantagens - tais como custos elevados, complexidade técnica e potenciais defeitos - tornam-na menos adequada para determinadas aplicações.A consideração cuidadosa destes factores é essencial quando se escolhe este processo para fabrico.
Tabela de resumo:
Desvantagens | Principais desafios |
---|---|
Elevados custos de equipamento | Fornos especializados dispendiosos, elevado consumo de energia e custos de mão de obra. |
Limitações do material | Requer aditivos específicos, distribuição desigual da fase líquida e problemas materiais. |
Defeitos potenciais | Deformação, flacidez e contração excessiva durante a sinterização. |
Limites de tamanho e complexidade | Capacidade limitada para produzir peças grandes ou complexas com elevada resistência mecânica. |
Baixa produtividade | Processo moroso com uma produção reduzida por forno. |
Complexidade técnica | É necessário um controlo preciso da temperatura, pressão e atmosfera. |
Precisa de ajuda para superar os desafios da sinterização em fase líquida? Contacte hoje os nossos especialistas para soluções à medida!