O revestimento PVD (Deposição Física de Vapor) é um processo sofisticado utilizado para aplicar revestimentos finos, altamente aderentes e duradouros a vários substratos.O processo envolve várias etapas fundamentais, incluindo a limpeza e o pré-tratamento do substrato, a vaporização do material alvo, o transporte de átomos vaporizados, a reação com gases (se necessário) e a deposição no substrato.O resultado é uma camada de espessura micrónica que interpenetra com o material subjacente, proporcionando uma excelente aderência e resistência à descamação ou lascagem.O processo é realizado num ambiente de vácuo, utilizando gases inertes como o árgon, para garantir uma atmosfera quimicamente não reactiva, o que aumenta a qualidade e a durabilidade do revestimento.
Pontos-chave explicados:
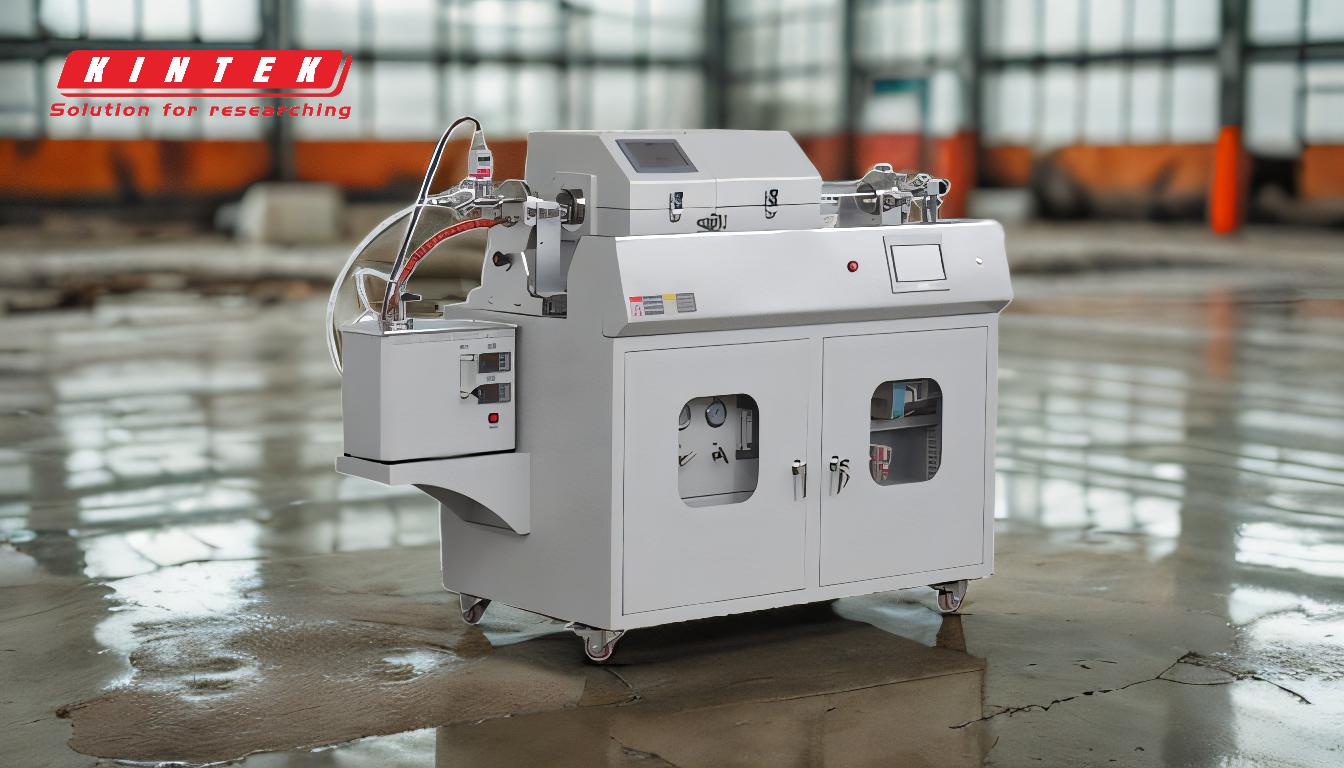
-
Limpeza e pré-tratamento do substrato:
- Limpeza: O substrato deve ser cuidadosamente limpo para remover quaisquer contaminantes, tais como óleos, poeiras ou óxidos.Isto é crucial porque quaisquer impurezas na superfície podem afetar negativamente a aderência e a qualidade do revestimento.Os métodos de limpeza podem incluir limpeza por ultra-sons, limpeza química ou limpeza por plasma.
- Pré-tratamento: Após a limpeza, o substrato é frequentemente submetido a processos de pré-tratamento para melhorar a aderência do revestimento.Este processo pode envolver o desbaste da superfície, o bombardeamento iónico ou a aplicação de uma camada de primário.O pré-tratamento assegura que a superfície está química e fisicamente preparada para receber o revestimento.
-
Vaporização do material alvo:
- Evaporação/Ablação: O material alvo, que é a fonte do revestimento, é colocado numa câmara de vácuo.São utilizadas fontes de alta energia, como electrões, iões ou lasers, para bombardear o material alvo, provocando a sua vaporização.Este processo converte o material alvo sólido numa fase de vapor.
- Transporte: Os átomos ou moléculas vaporizados são então transportados através da câmara de vácuo em direção ao substrato.O ambiente de vácuo assegura que as partículas vaporizadas viajam sem interferência das moléculas de ar, permitindo uma deposição mais controlada e uniforme.
-
Reação com Gases (se necessário):
- Reação: Em alguns casos, os átomos vaporizados reagem com gases selecionados (como o azoto, o oxigénio ou o metano) introduzidos na câmara.Esta reação forma compostos como óxidos metálicos, nitretos ou carbonetos, que determinam as propriedades finais do revestimento, como a dureza, a cor e a resistência química.
- Controlo das condições de reação: As condições de reação, incluindo a composição do gás, a pressão e a temperatura, são cuidadosamente controladas para obter as propriedades de revestimento desejadas.Por exemplo, a introdução de gás nitrogénio pode resultar na formação de nitretos metálicos, que são conhecidos pela sua dureza e resistência ao desgaste.
-
Deposição no substrato:
- Condensação: Os átomos ou moléculas vaporizados condensam-se na superfície do substrato, formando uma película fina.O processo de deposição é controlado para garantir uma cobertura e espessura uniformes.O revestimento acumula-se camada a camada, ligando-se fortemente ao substrato.
- Adesão: O revestimento interpenetra-se com o material subjacente, criando uma ligação forte que evita a descamação ou a lascagem.Esta é uma das principais vantagens dos revestimentos PVD, uma vez que proporcionam uma excelente aderência e durabilidade.
-
Controlo de qualidade e acabamento:
- Controlo de qualidade: Após a deposição, o substrato revestido é submetido a verificações de controlo de qualidade para garantir que o revestimento cumpre as especificações exigidas.Isto pode incluir medições de espessura, dureza, aderência e rugosidade da superfície.Quaisquer defeitos ou inconsistências são identificados e tratados.
- Acabamento: Dependendo da aplicação, o substrato revestido pode ser submetido a processos de acabamento adicionais para melhorar o seu aspeto ou desempenho.Isto pode incluir o polimento, o recozimento ou a aplicação de uma camada superior para melhorar a resistência à corrosão ou a estética.
-
Utilização de gases inertes:
- Atmosfera inerte: Ao longo do processo PVD, são utilizados gases inertes, como o árgon, para criar uma atmosfera quimicamente não reactiva.Isto evita reacções indesejadas entre o material de revestimento e o ambiente, garantindo a pureza e a qualidade do revestimento.O gás inerte também ajuda a remover os vapores residuais da câmara após a conclusão do processo de deposição.
-
Ambiente de vácuo:
-
Condições de alto vácuo:
Todo o processo PVD decorre num ambiente de alto vácuo.Isto é essencial por várias razões:
- Minimizar a contaminação: O vácuo reduz a presença de contaminantes que poderiam interferir no processo de revestimento.
- Deposição controlada: O vácuo permite um controlo preciso do processo de deposição, garantindo revestimentos uniformes e de alta qualidade.
- Eficiência energética: O ambiente de vácuo minimiza as perdas de energia, tornando o processo mais eficiente.
-
Condições de alto vácuo:
Todo o processo PVD decorre num ambiente de alto vácuo.Isto é essencial por várias razões:
-
Aplicações e benefícios:
- Vasta gama de aplicações: Os revestimentos PVD são utilizados em várias indústrias, incluindo automóvel, aeroespacial, dispositivos médicos e eletrónica de consumo.São valorizados pela sua capacidade de melhorar o desempenho, a durabilidade e a estética dos componentes.
- Vantagens: Os revestimentos PVD oferecem inúmeras vantagens, incluindo elevada dureza, resistência ao desgaste, resistência à corrosão e a capacidade de criar acabamentos decorativos.São também amigos do ambiente, uma vez que não envolvem produtos químicos nocivos nem produzem resíduos perigosos.
Em resumo, o processo de revestimento por PVD é um método altamente controlado e preciso para aplicar revestimentos finos, duradouros e aderentes a uma vasta gama de substratos.Ao compreender cada etapa do processo, desde a limpeza e o pré-tratamento até à deposição e ao controlo de qualidade, é possível apreciar a complexidade e a sofisticação envolvidas na criação de revestimentos PVD de elevado desempenho.
Tabela de resumo:
Passo | Descrição |
---|---|
Limpeza e pré-tratamento | Remove os contaminantes e prepara o substrato para uma melhor aderência. |
Vaporização | O material alvo é vaporizado utilizando fontes de alta energia numa câmara de vácuo. |
Reação com gases | Os átomos vaporizados reagem com gases para formar compostos como nitretos ou carbonetos. |
Deposição | Os átomos vaporizados condensam-se no substrato, formando um revestimento fino e duradouro. |
Controlo de qualidade | Assegura que o revestimento cumpre as especificações de espessura, dureza e aderência. |
Gases inertes | O árgon ou outros gases inertes criam uma atmosfera quimicamente não reactiva para revestimentos de alta qualidade. |
Ambiente de vácuo | As condições de alto vácuo minimizam a contaminação e garantem uma deposição precisa e uniforme. |
Aplicações | Utilizado na indústria automóvel, aeroespacial, dispositivos médicos e eletrónica de consumo para um melhor desempenho. |
Vantagens | Elevada dureza, resistência ao desgaste, resistência à corrosão e acabamentos decorativos. |
Pronto para melhorar os seus componentes com revestimentos PVD? Contacte-nos hoje para saber mais!