O endurecimento é um processo de tratamento térmico usado para aumentar a dureza e a resistência dos metais, normalmente por meio de aquecimento e resfriamento rápido (têmpera). Embora melhore significativamente as propriedades mecânicas, também pode afetar as dimensões do material. As alterações dimensionais durante o endurecimento são influenciadas por fatores como a composição do material, o meio de têmpera e a geometria da peça. Essas alterações podem resultar em empenamentos, distorções ou até mesmo rachaduras se não forem controladas adequadamente. Compreender a relação entre endurecimento e estabilidade dimensional é crucial para os fabricantes garantirem que o produto final atenda às especificações.
Pontos-chave explicados:
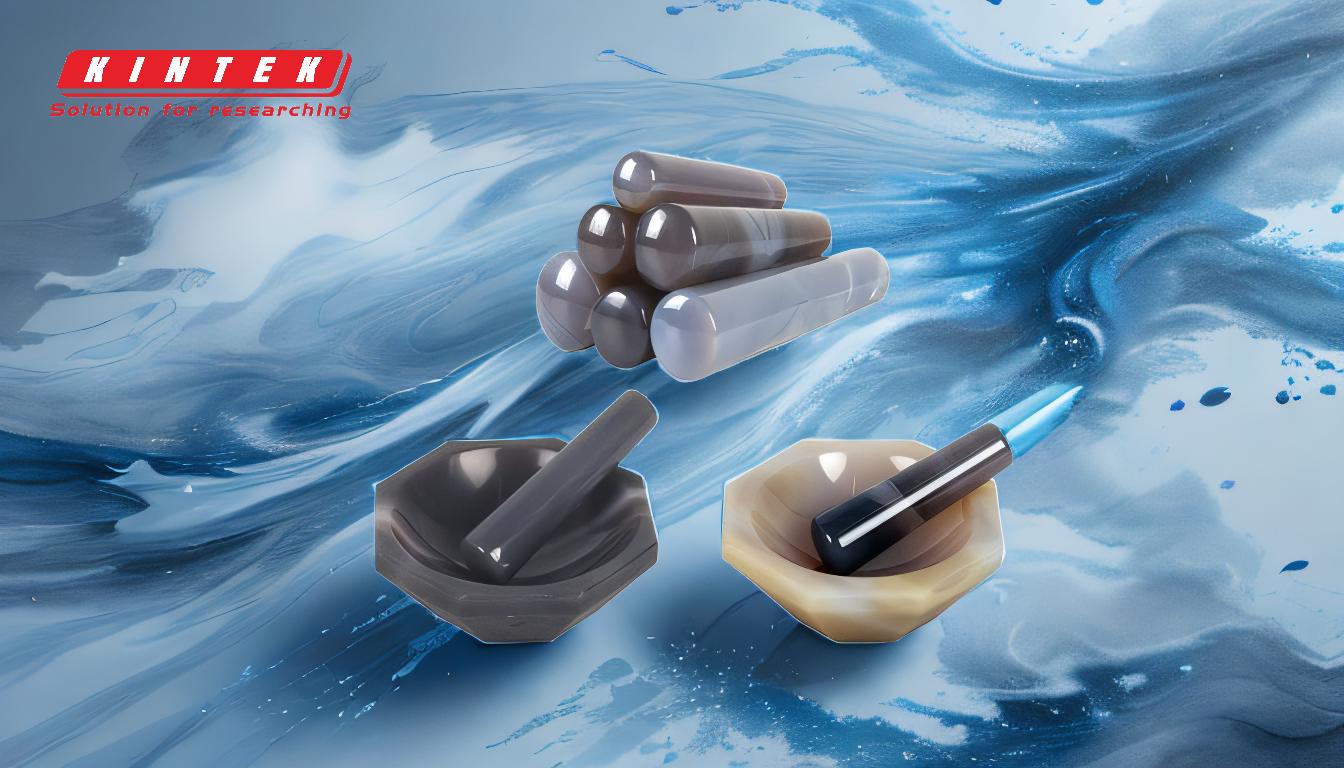
-
Mecanismo de Endurecimento e Mudanças Dimensionais:
- O endurecimento envolve aquecer o metal a uma alta temperatura e depois resfriá-lo rapidamente. Esse processo altera a microestrutura do metal, transformando-o em um estado mais duro, como a martensita do aço.
- O rápido resfriamento durante a têmpera introduz tensões internas, que podem causar alterações dimensionais. Essas tensões surgem devido a taxas de resfriamento desiguais no material, levando a empenamentos ou distorções.
- A magnitude das mudanças dimensionais depende do coeficiente de expansão térmica do material, das transformações de fase e da taxa de resfriamento.
-
Fatores que influenciam as mudanças dimensionais:
- Composição de materiais: Os elementos de liga no metal podem afetar sua resposta ao endurecimento. Por exemplo, os aços com alto teor de carbono são mais propensos à distorção devido ao seu maior potencial de dureza.
- Meio de têmpera: A escolha do meio de têmpera (óleo, água ou ar) impacta a taxa de resfriamento. Meios de resfriamento mais rápidos, como água, aumentam o risco de distorção e rachaduras.
- Geometria da peça: Formas complexas ou seções finas são mais suscetíveis a alterações dimensionais porque esfriam de forma desigual, levando a tensões internas mais altas.
-
Mitigando Mudanças Dimensionais:
- Controle de precisão de têmpera: O uso de técnicas de têmpera controlada, como têmpera interrompida ou martêmpera, pode reduzir as tensões internas e minimizar a distorção.
- Alívio do estresse: Tratamentos térmicos pós-endurecimento, como revenimento, ajudam a aliviar tensões residuais e estabilizar dimensões.
- Considerações de projeto: Os engenheiros podem projetar peças com seções transversais uniformes e evitar cantos vivos para reduzir as concentrações de tensão durante a têmpera.
-
Implicações práticas para compradores de equipamentos e consumíveis:
- Ao selecionar materiais para componentes que necessitam de endurecimento, os compradores devem considerar a suscetibilidade do material a alterações dimensionais e escolher ligas com melhor estabilidade dimensional.
- Para equipamentos como fornos e sistemas de têmpera, investir em sistemas de controle avançados pode garantir aquecimento e resfriamento uniformes, reduzindo o risco de distorção.
- A colaboração com especialistas em tratamento térmico pode ajudar a otimizar o processo de endurecimento para aplicações específicas, garantindo dureza e precisão dimensional.
Ao compreender a interação entre o endurecimento e as alterações dimensionais, os fabricantes podem tomar decisões informadas para alcançar as propriedades mecânicas desejadas, mantendo a integridade dimensional.
Tabela Resumo:
Fator-chave | Impacto nas mudanças dimensionais |
---|---|
Composição de materiais | Os elementos de liga influenciam a distorção; aços com alto teor de carbono são mais propensos a empenar. |
Meio de têmpera | O resfriamento mais rápido (por exemplo, água) aumenta os riscos de distorção e rachaduras. |
Geometria da peça | Formas complexas ou seções finas esfriam de maneira desigual, levando a tensões internas mais altas. |
Estratégias de Mitigação | A têmpera controlada, o revenido e o design uniforme das peças reduzem as alterações dimensionais. |
Otimize seu processo de endurecimento para obter precisão dimensional— entre em contato com nossos especialistas hoje !