Princípio da prensagem isostática a frio (CIP)
Índice
- Princípio da prensagem isostática a frio (CIP)
- Comparação entre a CIP e a prensagem de moldes metálicos
- Introdução à prensagem de moldes metálicos
- Processos automatizados em equipamentos industriais de prensagem de moldes metálicos
- Diferenças nos processos de pressurização de CIP e Prensagem de Moldes Metálicos
- Comparação da distribuição de densidade em produtos moldados por CIP e Prensagem de Moldes Metálicos
- Tipos de processamento CIP
- Segmentação do mercado
- Detalhes do processo de saco húmido
- Pormenores do processo de saco seco
Compreensão do princípio da CIP com base no conceito de pressão de Blaise Pascal
A prensagem isostática a frio (CIP) é um método de processamento de materiais que se baseia no princípio proposto por Blaise Pascal, conhecido como lei de Pascal. De acordo com este princípio, a pressão aplicada num fluido fechado é transmitida em todas as direcções ao longo do fluido sem qualquer alteração de magnitude.
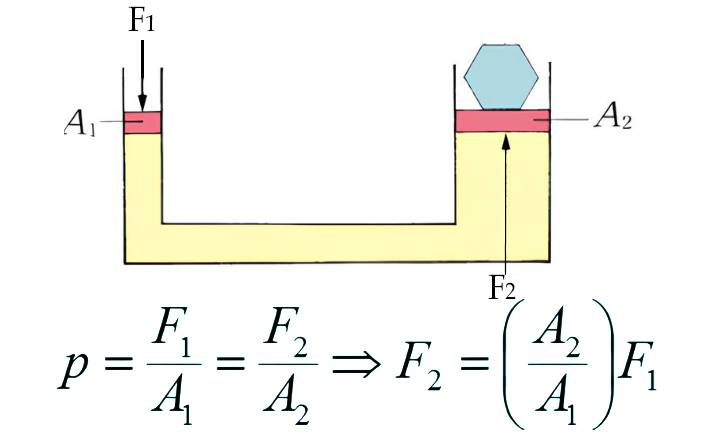
No CIP, os pós são compactados envolvendo-os num molde de elastómero, que tem baixa resistência à deformação. O molde é então submetido a uma pressão uniforme do líquido, que comprime os pós. Isto resulta na formação de um sólido altamente compacto.
A CIP pode ser utilizada para processar uma variedade de materiais, incluindo plásticos, grafite, metalurgia do pó, cerâmica e alvos de pulverização. É um método versátil para moldar e compactar pós em componentes de diferentes tamanhos e formas.
Processo de selagem de materiais em pó num molde de formação e aplicação de pressão líquida
No processo CIP, os materiais em pó são selados num molde de formação com baixa resistência à deformação, como um saco de borracha. A pressão do líquido é então aplicada uniformemente ao molde, comprimindo os pós. Esta pressão líquida é transmitida ao longo do molde, resultando na compressão uniforme do corpo moldado em toda a sua superfície.
O CIP é realizado à temperatura ambiente e utiliza um molde feito de um material elastómero, como o uretano, a borracha ou o cloreto de polivinilo. O fluido utilizado no CIP é normalmente óleo ou água, e a pressão aplicada durante a operação varia tipicamente entre 60.000 lbs/in2 (400 MPa) e 150.000 lbs/in2 (1000 MPa).
A vantagem do CIP é que ele ajuda a reduzir a distorção, melhorar a precisão e minimizar o risco de aprisionamento de ar e vazios. É amplamente utilizado em várias indústrias, incluindo a médica, aeroespacial e automóvel, para a produção de componentes.
A prensagem de moldes metálicos é um método semelhante ao CIP. Neste processo, os materiais em pó são colocados num espaço confinado pelo molde metálico e pelo punção inferior. Em seguida, são comprimidos através da redução da distância entre os punções superior e inferior.
Em geral, o CIP é um método eficaz para moldar e compactar materiais em pó em componentes sólidos, proporcionando um elevado nível de precisão e reduzindo o risco de defeitos.
Comparação entre a CIP e a prensagem de moldes metálicos
Introdução à prensagem de moldes metálicos
A prensagem de moldes metálicos é um método de processamento de materiais semelhante à prensagem isostática a frio (CIP). Neste método de prensagem, os materiais em pó são colocados num espaço delimitado pelo molde metálico e pelo punção inferior. Em seguida, são comprimidos através da redução da distância entre os punções superior e inferior.
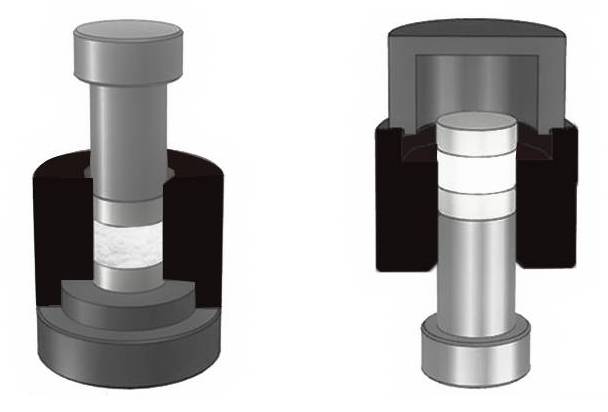
Processos automatizados em equipamento industrial de prensagem de moldes metálicos
O equipamento de prensagem de moldes metálicos utilizado em ambientes industriais consiste numa série de processos automatizados. Estes processos incluem o enchimento de pó, a compressão e a remoção do corpo moldado. A prensagem de ação simples, um método comum utilizado, comprime o pó até à forma com o punção inferior fixo.
Diferenças nos processos de pressurização da CIP e da prensagem de moldes metálicos
A principal diferença entre a CIP e a prensagem de moldes metálicos reside nos processos de pressurização que utilizam. A CIP aplica pressão isostática aos materiais utilizando pressão líquida, enquanto a prensagem de moldes metálicos aplica apenas pressão uniaxial. Esta diferença resulta na produção de produtos com diferentes distribuições de densidade.
Comparação da distribuição de densidade em produtos moldados por CIP e prensagem de molde metálico
A CIP produz produtos com uma densidade e homogeneidade uniformes devido à ausência de fricções com um molde metálico. Por outro lado, a prensagem de moldes metálicos pode resultar em variações na distribuição da densidade. A parte inferior de um corpo moldado produzido por prensagem de molde metálico tende a ter uma densidade mais baixa em comparação com a sua parte superior. Isto deve-se às fricções entre o pó e o molde metálico ou o punção, bem como entre as partículas de pó.
Em resumo, tanto a CIP como a prensagem de moldes metálicos são métodos de processamento de materiais utilizados em várias indústrias. Embora partilhem semelhanças, como a utilização de materiais em pó e a compressão, diferem nos seus processos de pressurização e na distribuição da densidade resultante nos produtos moldados. A CIP oferece uma densidade e homogeneidade uniformes, enquanto a prensagem de moldes metálicos pode resultar em variações de densidade.
Tipos de processamento CIP
Os métodos de moldagem CIP são classificados em dois tipos: o processo de saco húmido e o processo de saco seco, de acordo com a relação entre um molde de formação para encher o pó e um meio de pressão para transmitir a pressão.
Processo de saco húmido
No processo de saco húmido, como mostra a figura abaixo, o pó é enchido num molde de formação e selado hermeticamente no exterior do recipiente de alta pressão antes da imersão direta num meio de pressão. Em seguida, é aplicada uma pressão isostática nas superfícies exteriores do molde para comprimir o pó numa forma. Este método é adequado para vários tipos de produção de pequena qualidade para produtos de forma complicada ou em grande escala e investigação de produção experimental.
Limitações:
- Tempo de ciclo: 5-30 min para saco húmido
- Frio (temperatura ambiente)
- Densidade verde uniforme
- Mais lento do que a prensagem uniaxial
- Sem cera, formas complexas
- As peças podem necessitar de pós-maquinação
Processo de saco seco
No processo de saco seco, automatizado, uma peça de cada vez, o pó é preenchido num molde de formação e selado hermeticamente dentro do recipiente de alta pressão. Em seguida, o meio de pressão é introduzido no recipiente de pressão e a pressão isostática é aplicada às superfícies exteriores do molde para comprimir o pó numa forma. Este método é adequado para produzir peças com formas diferentes de uma forma económica.
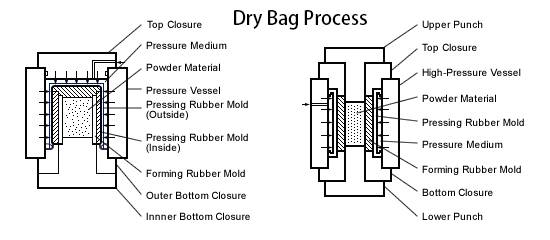
Limitações:
- Tempo de ciclo: 3-5 min
- Quente (100°C)
- Elimina a pós-sinterização
- Quente (2200°C)
- Melhora as propriedades mecânicas e físicas
- Os tempos de ciclo podem ser lentos: 10-15 h
- Forma quase líquida
- Densidade total
CIP com saco húmido
Dois tipos de métodos CIP evoluíram ao longo dos anos: saco húmido e saco seco. O chamado método de saco húmido é utilizado para produzir formas mistas. Estima-se que existam atualmente mais de 3000 prensas de sacos húmidos em todo o mundo, com tamanhos que variam entre 50 e 2000 mm de diâmetro.
Aplicações do processo CIP
Como uma tecnologia de processamento de formas quase líquidas, a CIP é normalmente utilizada nas seguintes aplicações:
- Aplicações em que o material é relativamente caro e, por conseguinte, a minimização dos resíduos (por exemplo, sob a forma de limalha de maquinagem) através da utilização de um processo quase em forma de rede ofereceria uma vantagem económica e ambiental significativa.
- Aplicações em que os materiais são difíceis de maquinar, sendo mais viável moldar a peça através do processamento de pós.
- Aplicações em que a complexidade geométrica da peça exige ferramentas dispendiosas (por exemplo, recipientes de sacrifício em HIP). A CIP utiliza ferramentas flexíveis reutilizáveis (ou potencialmente descartáveis) relativamente baratas que permitem a produção de formas complexas.
- Aplicações em que a uniformidade e a homogeneidade da microestrutura são necessárias para obter um desempenho mecânico específico. O processamento isostático de pós oferece uma vantagem relativa em relação a outros processos, como a prensagem uniaxial ou a fundição.
- Aplicações em que são necessários vários materiais ou estruturas graduadas. Nalgumas aplicações, as técnicas de união tradicionais não são adequadas, pelo que a CIP oferece um processo de união em estado sólido.
Embora o processo CIP tenha sido desenvolvido há muitos anos, as aplicações comerciais para metais têm sido relativamente limitadas. As aplicações tradicionais centravam-se em pré-formas e formas relativamente simples, tais como peças tubulares ou sólidas com rácios de aspeto elevados, como tubos, acessórios de pressão hidráulica e revestimentos de recipientes com paredes finas. Recentemente, o CIP tem sido considerado para aplicações relativamente avançadas em sectores de elevado valor. Por exemplo, as aplicações no sector automóvel incluem o forjamento de pré-formas para bielas e componentes de alumínio do sistema de cam phaser do veículo. As aplicações aeroespaciais incluem câmaras de impulso arrefecidas regenerativamente. As aplicações na produção de energia incluem peças para reactores de cisão, componentes estruturais de reactores nucleares e ligas ferríticas reforçadas por dispersão de óxido utilizadas para revestimento de combustível ou materiais estruturais em futuros sistemas nucleares. As aplicações de defesa incluem invólucros de ogivas de mísseis. O CIP+HIP foi implementado para fabricar invólucros de ogivas de mísseis Stinger (com volumes de produção até).
Segmentação do mercado
Com base no tipo de produto, o mercado de equipamentos de prensagem isostática a frio (CIP) é bifurcado em:
- Prensagem em saco húmido
No processo de saco húmido, o material em pó é encerrado num saco de molde flexível, que é submerso num líquido de alta pressão num recipiente de pressão. Em seguida, é aplicada uma pressão isostática nas superfícies exteriores do molde para comprimir o pó numa forma. Este processo é ideal para a produção de várias formas e de pequenas a grandes quantidades, bem como para a prensagem de produtos de grandes dimensões.
Tanto o processo CIP como o HIP utilizam construções multimateriais: invólucros de polímero com pós cerâmicos no CIP e invólucro de chapa de aço macio soldado com ligas de metalurgia do pó de alta qualidade no HIP. Assim, ambos os métodos apresentam uma oportunidade para o pré-processamento de construções numa única etapa através do fabrico aditivo multimaterial. Esta abordagem pode ser particularmente benéfica para a produção de pequenas séries ou protótipos, e pode mesmo diminuir os custos de fabrico ao permitir o aumento da complexidade das peças com menos passos e tempo de processamento.
Detalhes do processo Wet Bag
Explicação do processo de saco húmido
A tecnologia de saco húmido é um método utilizado para moldar pó, enchendo-o num molde e selando-o firmemente. O molde é então submerso num fluido sob pressão dentro de um recipiente sob pressão. A pressão isostática é aplicada à superfície externa do molde, comprimindo o pó numa massa sólida. Este processo é adequado para produção de várias formas e de pequenas a grandes quantidades.
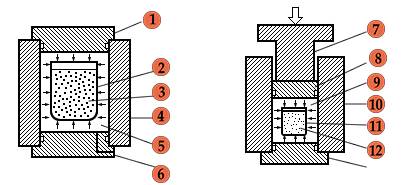
O processo de saco húmido não é tão comum como o processo de saco seco, mas continua a ser amplamente utilizado. Atualmente, são utilizadas mais de 3000 prensas de sacos húmidos em todo o mundo, com tamanhos que variam entre 50 mm e 2000 mm de diâmetro. Bombas de grande volume e mecanismos de carregamento melhorados podem ajudar a acelerar o processo, que normalmente demora entre 5 a 30 minutos a concluir.
Adequação do processo de saco húmido a vários tipos de produção
O processo de saco húmido é adequado para vários tipos de produção, especialmente para produtos de formato complicado ou de grande escala e investigação de produção experimental. Permite a produção de produtos com formas complexas que podem ser difíceis de obter através de outros métodos. Este processo também é adequado para a produção de pequenas quantidades e também pode ser utilizado para a produção em massa.
Tipos estruturais do processo de saco húmido: tipo de pressurização externa e tipo de pressurização direta por pistão
Existem dois tipos estruturais do processo de saco húmido: o tipo de pressurização externa e o tipo de pressurização direta por pistão.
O tipo de pressurização externa envolve a pressurização do meio de pressão para dentro do recipiente de pressão a partir do exterior. O meio de pressão é aplicado externamente ao molde, comprimindo o pó no seu interior.
O tipo de pressurização direta por pistão, por outro lado, pressuriza diretamente o meio de pressão selado no interior do recipiente de alta pressão com um pistão instalado em vez do fecho superior. Este tipo de processo de saco húmido elimina a necessidade de pressurização externa, tornando-o mais eficiente.
Em geral, o processo de saco húmido oferece um método único para moldar pó e é adequado para vários tipos de produção. Permite a produção de produtos com formas complexas e pode ser utilizado tanto para pequenas quantidades como para produção em massa. Os dois tipos estruturais do processo de saco húmido proporcionam flexibilidade e eficiência no processo de moldagem.
Detalhes do processo de saco seco
Explicação do processo de saco seco
O processo de saco seco é um método para moldar pó preenchido num molde de borracha de formação, transmitindo pressão através de um molde de borracha de prensagem no recipiente de alta pressão. Este método é adequado para a produção em massa de uma variedade simples e limitada de produtos, graças à sua operação automática que poupa trabalho.
Adequação do processo de saco seco para produção em massa
A prensagem de sacos secos é diferente dos sacos húmidos na medida em que uma membrana flexível é introduzida no recipiente de pressão e é utilizada durante todos os ciclos de prensagem. Esta membrana separa o fluido de pressão do molde, que se torna um "saco seco". Este processo é muito mais limpo, uma vez que o molde flexível não fica contaminado com pó húmido. Além disso, é necessária uma menor limpeza do recipiente. Este método tem ciclos rápidos e é muito ideal para a produção automatizada em massa de produtos em pó.
Classificação dos sistemas de processo Dry Bag: sistema de pressurização circunferencial + axial e sistema de pressurização circunferencial
O processo Dry Bag é classificado em dois sistemas: o sistema de pressurização circunferencial + axial e o sistema de pressurização circunferencial. O sistema de pressurização circunferencial + axial envolve a pressurização do meio de pressão para o recipiente sob pressão a partir do exterior, enquanto o sistema de pressurização circunferencial pressuriza diretamente o meio de pressão selado no interior do recipiente de alta pressão com um pistão instalado em vez do fecho superior.
A tecnologia Dry Bag é ideal para a produção em massa de materiais. Este processo demora normalmente apenas 1 minuto, o que o torna muito mais rápido do que a tecnologia de saco húmido.
Se estiver interessado nos nossos produtos, visite o sítio Web da nossa empresa:https://kindle-tech.com/product-categories/isostatic-pressA nossa empresa é uma empresa de investigação e desenvolvimento, onde a inovação foi sempre uma prioridade. A nossa equipa de I&D é constituída por engenheiros e cientistas experientes que seguem de perto as tendências da indústria e estão constantemente a ultrapassar os limites do que é possível. O nosso equipamento de laboratório incorpora a tecnologia mais recente para garantir a obtenção de resultados exactos e repetíveis durante as suas experiências. Desde instrumentos de alta precisão a sistemas de controlo inteligentes, os nossos produtos oferecem-lhe possibilidades ilimitadas para o seu trabalho experimental.
CONTACTE-NOS PARA UMA CONSULTA GRATUITA
Os produtos e serviços da KINTEK LAB SOLUTION foram reconhecidos por clientes de todo o mundo. A nossa equipa terá todo o prazer em ajudar com qualquer questão que possa ter. Contacte-nos para uma consulta gratuita e fale com um especialista de produto para encontrar a solução mais adequada para as suas necessidades de aplicação!