Definition and Function of Isostatic Pressing
Table of Contents
Explanation of isostatic pressing and how it applies uniform pressure to food products
Isostatic pressing is a process that involves applying equal pressure to a compacted powder in order to achieve optimal density and microstructure uniformity. This process is commonly used in various industries, including food processing.
Isostatic pressing applies a uniform, equal force over the entire product, regardless of its shape or size. This means that food products are compressed by uniform pressure from every direction. This uniform pressure helps to ensure that the food products are evenly processed and that the desired results are achieved.
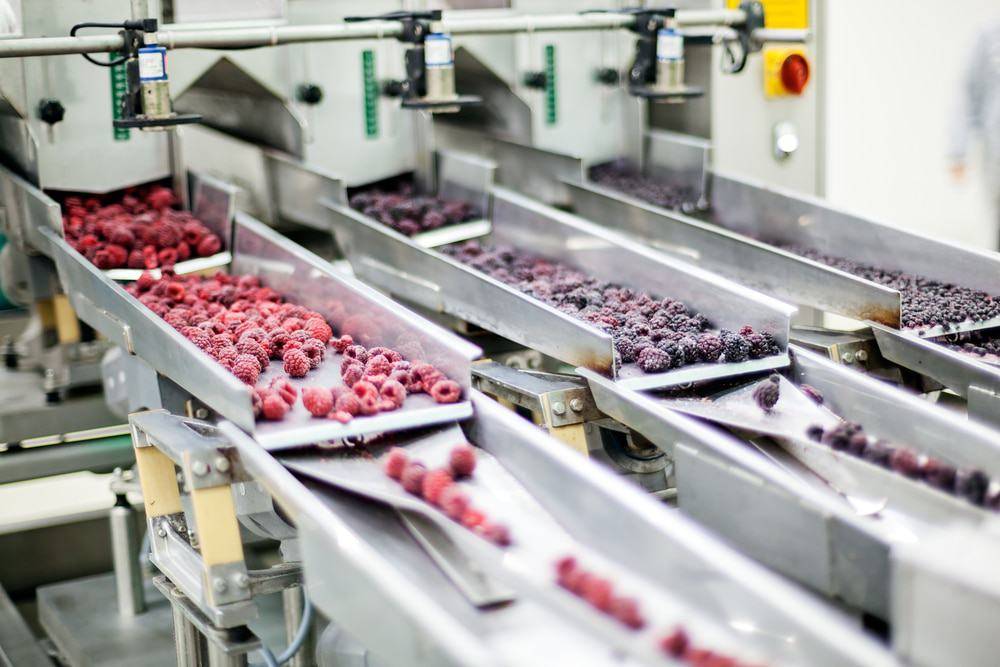
Role of isostatic pressing in food preservation through pasteurization and sterilization
In food processing, isostatic pressing plays a role in both pasteurization and sterilization processes. It is considered a mild preservation technology that helps to preserve vitamins, natural colorings, and flavorings in food products.
During the isostatic pressing process, the cell walls, cell membranes, and membranes surrounding the nucleus of microorganisms break down. This breakdown helps to deactivate microorganisms and enzymes present in the food products. Additionally, the process also helps to denature proteins and polysaccharides.
By applying uniform, simultaneous, and omnidirectional pressure, isostatic high-pressure presses facilitate the preservation of food products by breaking down unwanted substances and allowing desired substances to penetrate.
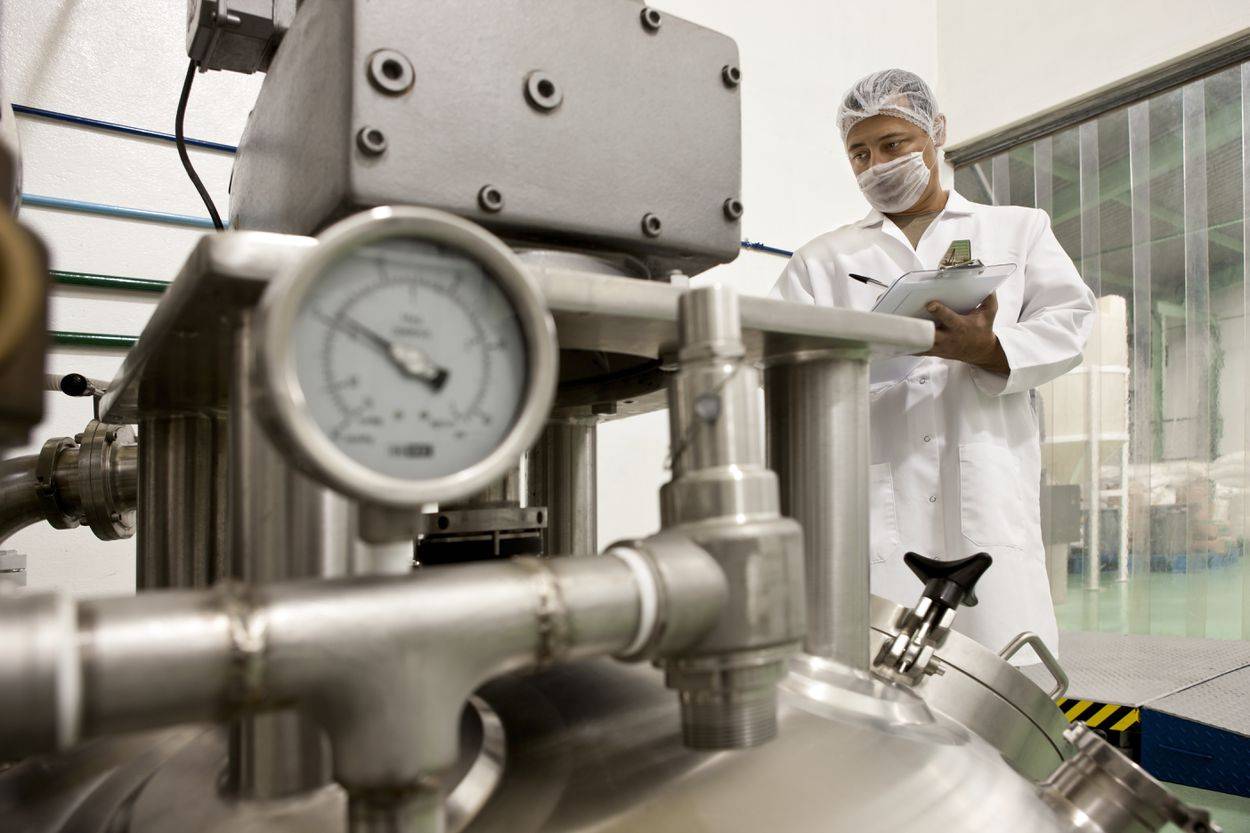
Mechanism of isostatic pressing in breaking down cell walls, membranes, and facilitating substance penetration
Isostatic pressing works by subjecting food products to uniform pressure from all directions. This pressure helps to break down the cell walls, cell membranes, and membranes surrounding the nucleus of microorganisms present in the food products.
The uniform pressure applied during isostatic pressing helps to deform the food products, allowing for the breakdown of unwanted substances and the penetration of desired substances. This process is particularly effective in altering the functional and sensory properties of various food components, especially proteins.
In addition to its preservation benefits, isostatic pressing also offers advantages such as uniform strength in all directions, uniform density, and shape flexibility. These benefits make it a valuable technique for food processing and preservation.
Effects of Isostatic High-Pressure Presses
Deactivation of Microorganisms and Enzymes, Denaturation of Proteins and Polysaccharides
Isostatic high-pressure presses have the ability to deactivate microorganisms and enzymes present in food products. The uniform and simultaneous pressure applied by these presses helps to break down the cell wall, cell membrane, and membrane surrounding the nucleus of microorganisms. This deactivation process ensures the preservation of food by preventing the growth of harmful bacteria and enzymes.
In addition, the high pressure applied by isostatic presses can also cause the denaturation of proteins and polysaccharides. Denaturation refers to the alteration of the structure and function of these macromolecules. The pressure treatment can lead to changes such as the crystallization of lipids, denaturation of proteins and enzymes, and gelatinization of starch.
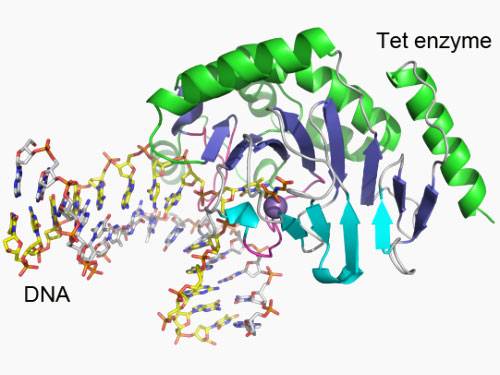
Alteration of Macromolecules like Lipids, Proteins, Enzymes, and Starch
Isostatic pressing can be used to alter the properties of various food components, particularly proteins. The tertiary and quaternary structures of molecules, which are maintained by hydrophobic and ionic interactions, can be beneficially altered by high pressure above 200 MPa. This alteration of macromolecules can result in improved functional and sensory properties of the food.
Beneficial Alteration of Tertiary and Quaternary Structures of Molecules using High Pressure
The application of high pressure in isostatic presses causes beneficial alterations in the tertiary and quaternary structures of molecules. These structures, which are crucial for the functioning of proteins and other macromolecules, can be altered in a positive way by the uniform and omnidirectional pressure exerted by isostatic presses.
Isostatic pressing offers several advantages over conventional processing techniques. It provides uniform strength in all directions, uniform density, and shape flexibility. The uniform pressure applied by isostatic presses ensures that the force is distributed equally throughout the entire product, regardless of its shape or size. This makes isostatic pressing suitable for producing parts with complex geometries.
Isostatic pressing finds applications in various industries such as pharmaceuticals, explosives, chemicals, and nuclear fuel Ferrites. It is particularly useful for materials that are difficult to compact using other methods, such as superalloys, titanium, tool steels, stainless steel, and beryllium.
Overall, isostatic high-pressure presses have significant effects on the deactivation of microorganisms and enzymes, denaturation of proteins and polysaccharides, and beneficial alteration of macromolecules. These presses offer advantages such as uniform strength, density, and shape flexibility, making them valuable tools in various industries.
Temperature and Pressure Conditions in Isostatic Pressing
Propagation of uniform pressure throughout the product
Isostatic pressing is a manufacturing process that applies uniform pressure to a product from all directions, resulting in a uniform internal organization of the material. This uniform pressure is isostatic, meaning it is propagated uniformly throughout the entire product. The pressure is exerted by a fluid, such as argon gas or a liquid medium, which ensures that the pressure is evenly distributed. This uniform compaction of the powder or material being processed leads to a uniform density within the final product.
Temperature increase in the treated foodstuff due to energy input via high pressure
During isostatic pressing, energy is inputted into the treated foodstuff via high pressure. This energy input leads to an increase in temperature in the foodstuff. The temperature can rise up to a maximum of 25°C due to this energy input. It is important to note that this temperature increase may not be desirable in certain cases, especially for heat-sensitive products or when precise temperature control is required.
Potential for cooling in the pressure chamber if temperature rise is undesirable
If the temperature rise in the pressure chamber during isostatic pressing is undesirable, there is potential for cooling. Cooling can be achieved by implementing cooling mechanisms in the pressure chamber. This allows for temperature control and ensures that the temperature remains within the desired range for the specific application or product being processed.
Isostatic pressing offers several advantages, including uniform strength in all directions, uniform density, and shape flexibility. These characteristics make it a versatile manufacturing process that is widely used in various industries, such as high-temperature refractory, ceramics, cemented carbide, and rare metal powder production.
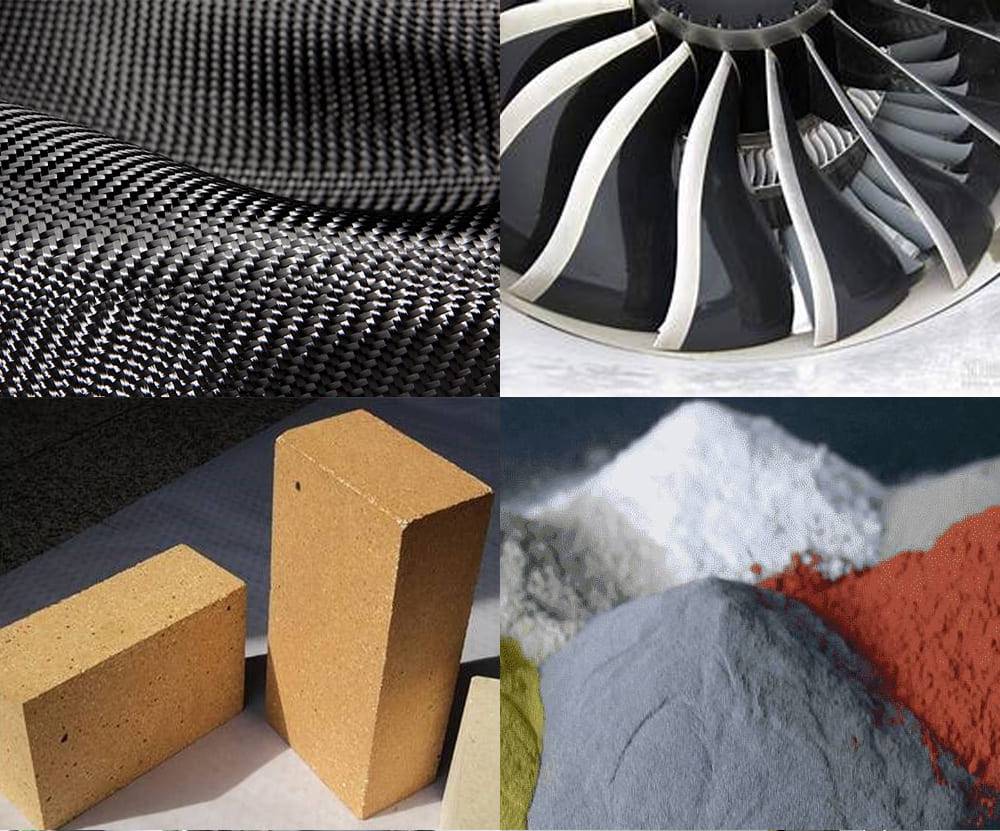
In addition to its applications in manufacturing, isostatic pressing is also used in food processing. It serves as a mild preservation technology for pasteurization and sterilization, preserving the vitamins, natural colorings, and flavorings in food products. Isostatic high-pressure presses deactivate microorganisms and enzymes, and denature proteins and polysaccharides. The application of uniform, simultaneous, and omnidirectional pressure to food products results in the breakdown of cell walls and membranes of micro-organisms, allowing for the penetration of unwanted substances.
Overall, temperature and pressure conditions play a crucial role in isostatic pressing. The propagation of uniform pressure ensures uniform compaction and density within the product, while the temperature increase due to energy input can be controlled through cooling mechanisms if necessary. Isostatic pressing offers numerous benefits in manufacturing and food processing, making it a valuable technique in various industries.
Advantages of Isostatic Pressing
Provision of uniform strength in all directions
Isostatic pressing enables the powder to be compacted with the same pressure in all directions. This results in a compacted piece that has uniform strength throughout, providing consistent performance and reliability. The uniform strength in all directions is achieved because no lubricant is needed during the process, allowing for high and uniform density to be achieved. This is especially beneficial for applications that require parts with consistent and reliable strength, such as in the aerospace and automotive industries.
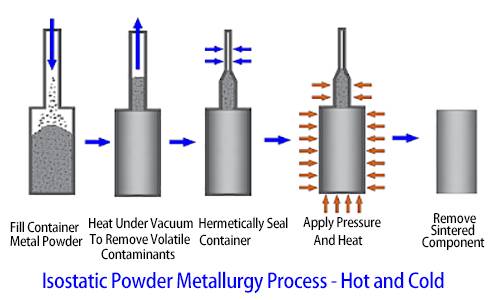
Achievement of uniform density
One of the key advantages of isostatic pressing is the ability to achieve high and uniform density. The process removes many of the constraints that limit the geometry of parts compacted unidirectionally in rigid dies. By applying pressure equally from all directions, the powder mixture is compacted and encapsulated, resulting in a product with uniform density. This is particularly important for applications that require high-density parts, such as in the manufacturing of medical implants or industrial components.
Flexibility in shaping the product
Isostatic pressing offers flexibility in shaping the product, allowing for the production of complex shapes and dimensions that may be difficult or impossible to produce using other methods. The process can accommodate a wide range of component sizes, from massive near net PM shapes to smaller MIM parts. The size of the isostatic pressure chamber determines the limits on part sizes, providing versatility in manufacturing. This flexibility in shaping the product makes isostatic pressing a preferred choice for industries that require unique and intricate designs, such as in the production of custom jewelry or specialized industrial components.
Isostatic pressing also offers additional advantages, such as low tooling cost for short production runs, the ability to enhance alloying possibilities without inducing segregation in the material, reduced lead times for complex shapes, and cost savings in material and machining. These advantages make isostatic pressing a highly efficient and cost-effective method for producing high-quality components.
In conclusion, the advantages of isostatic pressing, including the provision of uniform strength in all directions, the achievement of uniform density, and the flexibility in shaping the product, make it a preferred choice for industries that require reliable and high-density components with complex shapes and dimensions.
Application of Isostatic Pressing in Various Industries
Usage in pharmaceutical, explosives, chemicals, and nuclear fuel Ferrites industries
Isostatic pressing, a powerful technique in materials processing, finds applications in various industries. Some of the industries where isostatic pressing is commonly used include:
-
Pharmaceuticals: Isostatic pressing is used in the pharmaceutical industry for shaping and consolidating powdered materials. It allows for the creation of intricate shapes and achieves high green density.
-
Explosives: Isostatic pressing is employed in the explosives industry for compacting explosive powders into specific shapes and densities.
-
Chemicals: Isostatic pressing is utilized in the chemical industry for shaping and consolidating powdered materials, enabling the production of complex chemical products.
-
Nuclear fuel Ferrites: Isostatic pressing is applied in the nuclear fuel industry for the consolidation and shaping of nuclear fuel ferrites.
Other application industries of isostatic presses (pharmaceuticals, explosives, chemicals, nuclear fuel ferrite)
Distinction between cold isostatic presses (CIP) and hot isostatic presses (HIP) based on temperature conditions
There are two main types of isostatic presses: cold isostatic presses (CIP) and hot isostatic presses (HIP). The distinction between the two lies in the temperature conditions under which they operate.
Cold Isostatic Pressing (CIP):
Cold Isostatic Pressing, also known as cold isostatic compaction, involves subjecting a material to uniform pressure from all sides. This is achieved by immersing the material in a high-pressure fluid medium and applying hydraulic pressure. CIP is particularly effective for shaping and consolidating powdered materials, creating intricate shapes, and achieving high green density.
Advantages of Cold Isostatic Pressing:
-
Uniform density: Powder is compacted with the same pressure in all directions, resulting in high and uniform density.
-
No lubricant required: CIP does not require the use of lubricants, allowing for efficient material utilization.
-
Greater design flexibility: The process removes many constraints that limit the geometry of parts compacted unidirectionally in rigid dies, providing greater design flexibility.
Hot Isostatic Pressing (HIP):
Hot Isostatic Pressing involves subjecting a material to both high pressure and high temperature. This process is typically used for the consolidation and densification of materials, including metal powders, ceramics, and composites. HIP can improve the mechanical properties and reduce the presence of defects in the material.
In summary, Cold Isostatic Pressing and Hot Isostatic Pressing represent distinct approaches to materials processing, each with its own advantages. The decision between the two depends on the specific goals of your project and the characteristics of the materials involved.
Isostatic pressing has found significant applications in industries such as pharmaceuticals, explosives, chemicals, and nuclear fuel Ferrites. The ability to apply uniform pressure over the entire product, regardless of shape or size, offers unique benefits for shaping and consolidating materials. This technique has been instrumental in the development of precise product shapes, reducing the need for costly machining.
If you are interested in our products, please visit our company website:https://kindle-tech.com/product-categories/isostatic-press, where innovation has always been a priority. Our R&D team consists of experienced engineers and scientists who closely follow industry trends and are constantly pushing the boundaries of what is possible. Our laboratory equipment incorporates the latest technology to ensure that you can obtain accurate and repeatable results during your experiments. From high-precision instruments to intelligent control systems, our products will provide you with unlimited possibilities for your experimental work.
CONTACTE-NOS PARA UMA CONSULTA GRATUITA
Os produtos e serviços da KINTEK LAB SOLUTION foram reconhecidos por clientes de todo o mundo. A nossa equipa terá todo o prazer em ajudar com qualquer questão que possa ter. Contacte-nos para uma consulta gratuita e fale com um especialista de produto para encontrar a solução mais adequada para as suas necessidades de aplicação!