O revestimento PVD (Deposição Física de Vapor) é um processo versátil utilizado para aplicar camadas finas, duradouras e funcionais a vários substratos.O processo envolve a vaporização de um material sólido no vácuo e a sua deposição num substrato, formando uma película fina.A escolha do produto químico utilizado no revestimento PVD depende das propriedades desejadas do produto final, como a dureza, a resistência ao desgaste, a resistência à corrosão ou a estética.Os materiais comuns utilizados nos revestimentos PVD incluem metais, ligas, cerâmicas e compostos especializados como nitretos, carbonetos e boretos.Estes materiais são selecionados com base na sua capacidade de melhorar o desempenho e o aspeto do produto revestido em indústrias como a aeroespacial, automóvel, eletrónica e aplicações decorativas.
Explicação dos pontos principais:
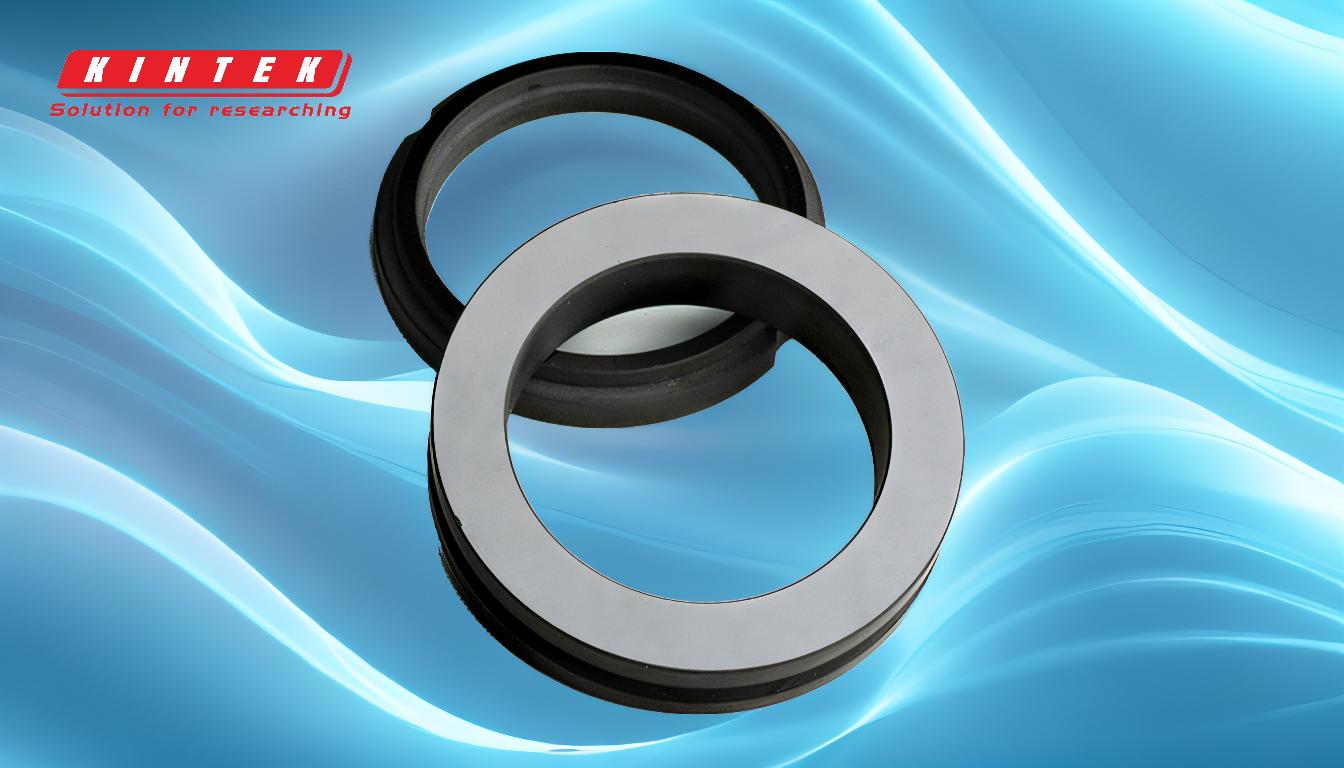
-
Materiais comuns de revestimento PVD:
- Metais:O titânio, o zircónio, o alumínio, o aço inoxidável e o cobre são frequentemente utilizados em revestimentos PVD.O ouro também é popular, especialmente na eletrónica aeroespacial, devido à sua condutividade e resistência à corrosão.
- Ligas:As combinações de metais como o titânio-alumínio (TiAl) são utilizadas para criar revestimentos com propriedades melhoradas.
- Cerâmica:Materiais como o nitreto de titânio (TiN), o nitreto de crómio (CrN) e o carbonitreto de titânio (TiCN) são amplamente utilizados pela sua dureza e resistência ao desgaste.
-
Compostos especializados:
- Nitretos:O nitreto de titânio (TiN), o nitreto de crómio (CrN) e o nitreto de titânio e alumínio (TiAlN) são revestimentos de nitreto comuns utilizados pela sua dureza e resistência ao desgaste e à corrosão.
- Carbonetos:O carbonitreto de titânio (TiCN) é um material híbrido que combina as propriedades dos carbonetos e dos nitretos, oferecendo elevada dureza e baixa fricção.
- Boretos:O nitreto de titânio e boro (TiBN) é utilizado devido à sua excecional dureza e estabilidade térmica.
-
Gases reactivos em PVD:
-
A composição dos revestimentos PVD pode ser modificada através da introdução de gases reactivos durante o processo de vaporização.Por exemplo:
- A adição de azoto resulta na formação de nitretos metálicos (por exemplo, TiN, CrN).
- A adição de oxigénio pode criar óxidos metálicos, que são úteis para revestimentos ópticos.
- A adição de carbono pode produzir carbonetos metálicos (por exemplo, TiC), que são conhecidos pela sua dureza e resistência ao desgaste.
-
A composição dos revestimentos PVD pode ser modificada através da introdução de gases reactivos durante o processo de vaporização.Por exemplo:
-
Aplicações dos revestimentos PVD:
- Aplicações decorativas:O TiN é amplamente utilizado pelo seu aspeto dourado em relógios, jóias e peças de hardware.O Cr2N é utilizado para películas de prata em artigos decorativos.
- Aplicações funcionais:Os revestimentos de AlCr prolongam a vida útil de ferramentas e peças de máquinas, enquanto as películas finas de ITO (óxido de índio e estanho) são utilizadas em LCD, ecrãs de plasma e painéis tácteis devido à sua condutividade e dureza.
- Aplicações industriais:Os revestimentos TiAlN e TiBN são utilizados em componentes aeroespaciais e automóveis devido à sua estabilidade a altas temperaturas e resistência ao desgaste.
-
Processo de revestimento PVD:
- Vaporização:O material sólido é vaporizado utilizando técnicas como cadinhos aquecidos, feixes de electrões, bombardeamento de iões ou evaporação por arco catódico.
- Deposição:O material vaporizado é depositado átomo a átomo sobre o substrato numa câmara de vácuo, assegurando um revestimento limpo e uniforme.
- Modificação:Podem ser introduzidos gases reactivos para alterar a composição e as propriedades do revestimento.
-
Substratos para revestimentos PVD:
-
Os revestimentos PVD podem ser aplicados a uma vasta gama de substratos, incluindo
- Metais:Aço inoxidável, alumínio e titânio.
- Não-metais:Nylon, plásticos, vidro e cerâmica.
-
Os revestimentos PVD podem ser aplicados a uma vasta gama de substratos, incluindo
-
Vantagens dos revestimentos PVD:
- Durabilidade:Os revestimentos PVD são conhecidos pela sua dureza e resistência ao desgaste, à corrosão e às altas temperaturas.
- Apelo estético:Os revestimentos como TiN e Cr2N proporcionam acabamentos decorativos com um brilho metálico.
- Funcionalidade:Os revestimentos como o ITO e o AlCr melhoram o desempenho dos componentes electrónicos e das ferramentas industriais.
Ao compreender os materiais e os processos envolvidos no revestimento PVD, os compradores podem selecionar os produtos químicos e as técnicas adequadas para satisfazer os requisitos específicos das suas aplicações.
Tabela de resumo:
Categoria | Exemplos | Propriedades |
---|---|---|
Metais | Titânio, Zircónio, Alumínio, Ouro | Condutividade, Resistência à Corrosão |
Ligas | Titânio-alumínio (TiAl) | Força reforçada, resistência ao desgaste |
Cerâmica | Nitreto de titânio (TiN), nitreto de crómio (CrN), carbonitreto de titânio (TiCN) | Dureza, Resistência ao Desgaste, Resistência à Corrosão |
Compostos especializados | Nitreto de Alumínio e Titânio (TiAlN), Nitreto de Boro e Titânio (TiBN) | Estabilidade a altas temperaturas, dureza excecional |
Gases reactivos | Nitrogénio, Oxigénio, Carbono | Forma nitretos, óxidos e carbonetos para propriedades melhoradas |
Precisa do revestimento PVD perfeito para a sua aplicação? Contacte hoje os nossos especialistas para soluções à medida!